Introduction
In the fast-paced world of modern industries, where precision and efficiency are paramount, pneumatic torque wrenches have emerged as a game-changing tool. These sophisticated devices harness the power of compressed air to provide controlled torque for tightening or loosening bolts and nuts in a wide array of applications. As we delve deeper into this article, we will explore the working principles, advantages, and diverse applications of pneumatic torque wrenches that have made them essential tools in various sectors.
Understanding Pneumatic Torque Wrenches
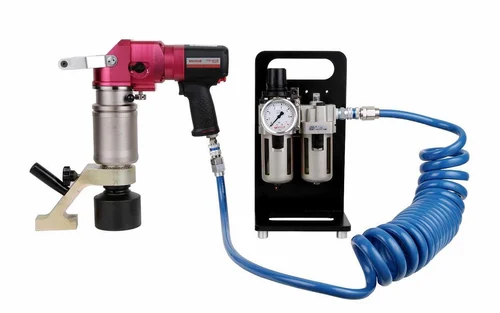
How Do Pneumatic Torque Wrenches Work?
Pneumatic torque wrenches operate on a simple yet powerful principle of converting compressed air energy into rotational force. The tool has a torque-controlled mechanism ensures the applied torque is consistent and within specified limits. When compressed air is directed into the air motor, it initiates rotation, and the energy is transferred through a gear train to the output square drive. The gear train is designed to regulate the torque applied, thereby preventing overtightening and reducing the risk of damage to bolts or nuts.
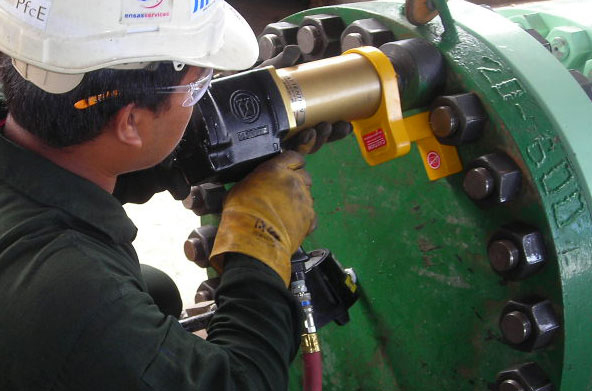
Components of a Pneumatic Torque Wrench
A typical pneumatic torque wrench comprises several key components. The body houses the air motor, gear train, and controls. The air motor serves as the heart of the wrench, converting the energy from compressed air into rotational motion. The gear train is responsible for multiplying the torque and ensuring precise application. To counteract the rotational force exerted by the tool, a reaction arm is employed, providing stability and support during the tightening or loosening process.
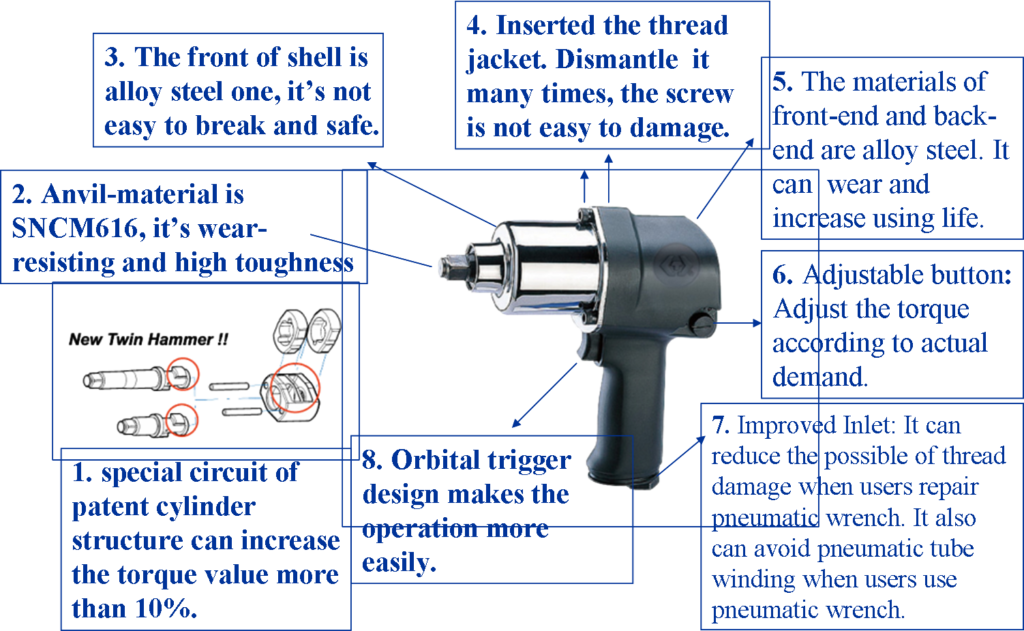
Pneumatic Torque Wrench Specification
A pneumatic torque wrench specification is a set of technical details and performance characteristics that define the capabilities and limitations of the tool. These specifications are essential for users, manufacturers, and industry professionals to understand the tool’s suitability for specific applications. The following are some key elements typically found in a pneumatic torque wrench specification –
- Torque Range: This specifies the minimum and maximum torque levels the wrench can apply. It is crucial to ensure that the tool can handle the required torque for the intended tasks.
- Air Pressure: Pneumatic torque wrenches operate using compressed air. The specification should indicate the required air pressure range for optimal performance.
- Air Consumption: This denotes the volume of compressed air the tool consumes during operation, which affects overall efficiency and air compressor requirements.
- Drive Size: The drive size refers to the square drive on the wrench, such as 1/4″, 3/8″, 1/2″, or 1″. This specification dictates the size of sockets and fasteners the tool can accommodate.
- Accuracy: The accuracy of a pneumatic torque wrench indicates how closely the applied torque aligns with the set value, often expressed as a percentage or within a certain tolerance range.
- Reaction Type: Some pneumatic torque wrenches come with different reaction types, such as direct drive or push-through. The specification should clarify the type of reaction mechanism employed.
- Weight and Dimensions: The weight and physical dimensions of the tool impact its portability and ease of use.
- Operating Speed: This refers to the rate at which the tool can achieve its maximum torque output. A higher operating speed may enhance productivity.
- Ergonomics and Handling: Information about the tool’s grip, handle design, and overall ergonomics help users assess its comfort and suitability for prolonged use.
- Certifications and Standards: The specification should mention any certifications or adherence to industry standards, ensuring the tool meets safety and quality requirements.
- Understanding these pneumatic torque wrench specifications enables users to make informed decisions when selecting the right tool for their specific applications, ensuring efficiency, accuracy, and safety in fastening tasks. Manufacturers and distributors use these specifications to provide appropriate guidance and support to users and establish clear benchmarks for quality and performance.
Working Principle of Pneumatic Torque Wrench
The working principle of a pneumatic torque wrench is based on converting compressed air energy into rotational force to tighten or loosen fasteners. The tool’s operation involves several key components that work together seamlessly –
- Air Motor: The heart of the pneumatic torque wrench is the air motor, which is powered by compressed air. When air flows through the motor, it initiates a rotary motion that drives the wrench’s output square drive.
- Gear Train: The air motor’s rotational force is transmitted through a gear train. The gear train multiplies the torque generated by the air motor, allowing the tool to exert higher levels of torque than a manual wrench.
- Torque-Controlled Mechanism: To ensure precise torque application, the pneumatic torque wrench incorporates a torque-controlled mechanism. This mechanism regulates the amount of air pressure allowed into the air motor, controlling the torque output. When the desired torque is reached, the mechanism restricts airflow, preventing further tightening and emitting a click sound or other indicator, depending on the wrench type.
- Reaction Arm: During operation, a reaction arm is used to counteract the rotational force applied by the wrench, providing stability and support for the operator.
- By combining these components, the pneumatic torque wrench achieves controlled and accurate torque application. When the operator activates the tool and applies the square drive to the fastener, the wrench applies rotational force until the desired torque level is reached. The torque-controlled mechanism then signals the operator to stop, ensuring that the fastener is tightened precisely to the required specifications. This working principle allows pneumatic torque wrenches to be used effectively in various industries where precise and consistent torque application is crucial for ensuring the integrity, safety, and performance of assembled components and structures.
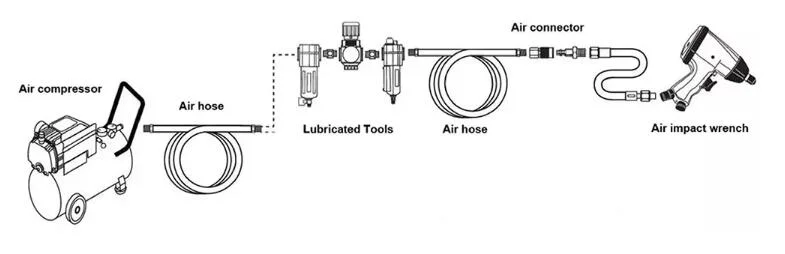
Heavy Duty Pneumatic Torque Wrench
A heavy-duty pneumatic wrench is a robust and powerful tool designed to handle demanding and high-torque applications in various industries. As a pneumatic tool, it operates using compressed air, providing the strength required to tackle tough fastening tasks effectively. Heavy-duty pneumatic wrenches typically feature larger air motors and gear trains to generate substantial torque output, making them suitable for tightening or loosening large and stubborn bolts and nuts.
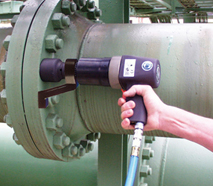
- These wrenches are commonly used in heavy industries such as construction, mining, shipbuilding, and oil and gas. They are indispensable for assembly, disassembly, and maintenance of heavy machinery, equipment, and structures where manual wrenches would be insufficient.
- Due to their durability and sturdy construction, heavy-duty pneumatic wrenches can withstand harsh working environments and prolonged use without compromising performance. Additionally, they often come with adjustable torque settings, allowing operators to apply precise torque according to specific requirements.
- Safety is a paramount concern when using heavy-duty pneumatic wrenches, as the high torque output can lead to potential hazards if not handled properly. Proper training and adherence to safety guidelines are essential for operators to ensure secure and efficient use of these powerful tools.
**Heavy-duty pneumatic wrenches are reliable workhorses for tackling challenging applications that demand substantial torque. Their robustness, efficiency, and versatility make them valuable assets in heavy industries where reliable and accurate fastening is crucial to ensuring the longevity and safety of machinery and structures.
Use of Pneumatic Torque Wrench in Mold Maintenance
In mold maintenance, pneumatic torque wrenches play a crucial role in ensuring precision and efficiency during disassembly and reassembly processes. Molds used in manufacturing processes require regular maintenance to ensure optimal performance and longevity. Pneumatic torque wrenches are ideal for this task due to their ability to provide controlled and consistent torque application.
- During mold disassembly, pneumatic torque wrenches allow technicians to remove tightly fastened bolts and nuts without damaging the mold components. The torque-controlled mechanism prevents overtightening and ensures that the bolts are removed safely.
- When reassembling the mold, pneumatic torque wrenches enable technicians to apply the correct torque to secure bolts and nuts precisely. This is vital to maintain the alignment and integrity of the mold, ensuring that it functions flawlessly during the manufacturing process.
- Using pneumatic torque wrenches in mold maintenance reduces the risk of human error and increases the overall efficiency of the maintenance process. By providing accurate torque application, these tools contribute to the safety and reliability of the molds, minimizing downtime and enhancing production output
Advantages of Pneumatic Torque Wrenches
Speed and Efficiency
In industries where time is of the essence, pneumatic torque wrenches shine. Their ability to operate at high speeds significantly reduces the time needed for tightening or loosening multiple bolts. This increased speed translates to enhanced productivity on assembly lines and construction sites, ultimately leading to cost savings and faster project completion.
Precision and Accuracy
Precision is paramount, especially in critical applications such as aerospace, automotive, and manufacturing. Pneumatic torque wrenches offer unbeatable accuracy in torque application, ensuring that every bolt is tightened to the precise specifications required by the manufacturer. This level of precision is essential to maintain the integrity and safety of machinery, equipment, and structures.
Reduced Operator Fatigue
In manual fastening methods, operators may experience fatigue, leading to inconsistent torque application. Pneumatic torque wrenches mitigate this issue by minimizing the physical effort required from the operator. The wrench’s air-powered mechanism does the hard work, resulting in more reliable and consistent tightening, ultimately reducing the likelihood of assembly errors.
Versatility
Pneumatic torque wrenches come in a wide range of sizes and torque capacities, making them suitable for various applications. From delicate tasks in electronics assembly to heavy-duty jobs in shipbuilding, there is a pneumatic torque wrench tailored for every need. This versatility makes them an indispensable tool in a diverse range of industries.
Applications of Pneumatic Torque Wrenches
Automotive Industry
In the automotive sector, pneumatic torque wrenches play a pivotal role in assembling engines, transmissions, suspensions, and various components. Precise torque application is vital to ensure the longevity and optimal performance of vehicles.
Aerospace Sector
The aerospace industry demands unparalleled precision and reliability due to the critical nature of its components. Pneumatic torque wrenches are extensively used to assemble aircraft engines, fuselage components, and landing gears, ensuring the safety and performance of aircraft in flight.
Construction and Infrastructure
In the construction industry, where safety and stability are paramount, pneumatic torque wrenches are used to securely fasten structural elements such as beams, columns, and bridges. These tools are instrumental in ensuring the longevity and integrity of constructed infrastructure.
Manufacturing and Machinery
Pneumatic torque wrenches find extensive use in manufacturing plants for assembling machinery and equipment. Whether it’s assembling engines or securing parts in precision equipment, pneumatic torque wrenches contribute to increased productivity and reduced downtime.
Energy Sector
Power generation and distribution facilities rely on pneumatic torque wrenches to maintain turbines, generators, and other critical equipment. Properly tightened bolts are essential for the efficient and safe operation of these facilities.
Choosing the Right Pneumatic Torque Wrench
Selecting the appropriate pneumatic torque wrench for a specific application requires careful consideration of factors such as torque range, accuracy, size, and ergonomics. Consulting with manufacturers or industry experts can help ensure the right choice for the job at hand.
Conclusion
Pneumatic torque wrenches have revolutionized precision fastening across a broad spectrum of industries, thanks to their unparalleled speed, accuracy, and versatility. From the automotive and aerospace sectors to construction and manufacturing, these tools are essential for ensuring the safety, performance, and reliability of critical components. As technological advancements continue, pneumatic torque wrenches are likely to evolve further, reinforcing their position as indispensable tools for precision fastening in various applications.
What is a Pneumatic Torque Wrench?
A pneumatic torque wrench is a powerful tool that utilizes compressed air to deliver controlled rotational force for tightening or loosening bolts and nuts. It consists of an air motor, gear train, and torque-controlled mechanism to ensure precise torque application. This versatile tool finds widespread use in various industries, offering high speed, accuracy, and reduced operator fatigue during assembly and construction processes.
What are the 4 types of torque wrenches?
4 Types of torque wrenches are –
Click-Type Torque Wrench: Click-type torque wrenches emit an audible click sound when the preset torque value is reached, providing a simple and effective way to ensure precise tightening.
Beam-Type Torque Wrench: These wrenches use a calibrated bending beam to indicate applied torque. They are straightforward and do not require regular calibration.
Digital Torque Wrench: Digital torque wrenches display the applied torque value digitally, offering easy-to-read readings and sometimes allowing for data storage and transfer.
Dial Torque Wrench: Dial torque wrenches use a dial indicator to show the applied torque, making them suitable for applications with tight space constraints.
What is a Pneumatic Torque Driver?
A pneumatic torque driver is a specialized tool that utilizes compressed air to apply precise torque to fasteners, such as bolts and screws. It is designed to provide consistent torque output for repetitive tasks, ensuring uniform tightening. Pneumatic torque drivers are commonly used in manufacturing and assembly processes, where accuracy, speed, and repeatability are essential for achieving consistent and reliable results.
What is a Pneumatic Torque Multiplier?
A pneumatic torque multiplier is a powerful tool that utilizes compressed air to generate high torque output, exceeding what a person can manually achieve. It is designed to amplify the applied torque, making it suitable for heavy-duty applications where a significant amount of torque is required. Pneumatic torque multipliers are commonly used in industries such as construction, oil and gas, and heavy machinery maintenance, where large bolts or fasteners need to be tightened or loosened with precision and efficiency.
What is a Hydraulic Torque Wrench?
A hydraulic torque wrench is a specialized tool used for precision tightening or loosening of bolts and nuts in various applications. It operates on the principle of hydraulics, utilizing pressurized hydraulic fluid to generate rotational force. The tool consists of a hydraulic pump, hose, and hydraulic cylinder with a reaction arm. When pressure is applied to the hydraulic fluid, it creates a torque on the output square drive, allowing the wrench to tighten or loosen fasteners with controlled and accurate force. Hydraulic torque wrenches are commonly used in industries like construction, oil and gas, and heavy machinery maintenance, where high torque applications are required.
What is an Electric Torque Wrench?
An electric torque wrench is a specialized tool used for precise tightening or loosening of bolts and nuts. Unlike pneumatic or hydraulic wrenches, it operates using electricity. The tool typically includes an electric motor that generates rotational force, allowing for controlled torque application. Electric torque wrenches come with various features, such as digital displays for real-time torque readings and adjustable torque settings. They find applications in industries where accuracy and repeatability are critical, such as automotive assembly lines, electronics manufacturing, and maintenance of sensitive equipment. Electric torque wrenches offer convenience, reliability, and reduced operator fatigue compared to manual wrenches.