This article is dedicated to Mold Maintenance Associates/Technicians/Engineers who are working on injection mold maintenance & its repair work and also for those who wish to work in this sector and for those who just want to learn about the term MOLD MAINTENANCE. So it’s our request to you please read the full article to know the types of mold maintenance carried out to make mold always ready for production & reduce production downtime due to mold breakdown. To know about the basics of mold & their types read more. You can also learn some basics of injection molding from our previous article.
What is Injection Mold Maintenance?
Mold maintenance is a process of rectification/repair work of mold from any issues or problems that occur in it that directly or indirectly affects production. So we start to work on preventive maintenance to track upcoming breakdowns and fix them in a timely without affecting the production line.
Mold maintenance refers to the regular and systematic upkeep and care of molds used in various industrial processes, particularly in production. Molds are precision tools or die that shape materials into specific forms, such as in plastic injection molding, metal casting, glass blowing, and other molding processes.
Injection Mold Maintenance Types
There are mainly two types of injection mold maintenance and they are discussed below in detail –
Mold Breakdown Maintenance
“Mold Breakdown Maintenance” refers to the failure or malfunction of a mold. Due to this mold is unable to produce quality products or quantity products within defined cycle time. When a mold experiences a breakdown, it means that it becomes inoperable or cannot perform its intended function correctly. For this type of maintenance, we use Breakdown Slip.
When a mold breaks down, it can result in production delays, increased scrap rates, and added costs for repair or replacement. To minimize the risk of mold breakdowns, organizations implement regular mold maintenance programs, conduct inspections, and address issues promptly when they arise.
Mold Preventive Maintenance
Mold preventive maintenance” refers to a proactive approach taken to keep molds used in various industrial processes, such as plastic injection molding, metal casting, glass blowing, and others, in optimal working condition. The primary objective of preventive maintenance is to prevent mold breakdowns, reduce downtime, maintain product quality, and extend the overall lifespan of the molds. By conducting regular maintenance tasks, potential issues are identified and addressed before they lead to significant problems or mold failures.
By implementing a well-structured preventive maintenance program, organizations can minimize unexpected mold breakdowns, increase production efficiency, and maintain consistent product quality. Preventive maintenance is a proactive strategy that saves time and resources by addressing potential issues before they become more significant problems, ultimately contributing to the overall success of the manufacturing process.
Mold Preventive Maintenance can also be categorized into 5 different types and they are –
Mold Readiness/Routine Maintenance
As per Process Planning Control (PPC) person make a plan for mold loading on the machine, mold setter/changer checks the mold status 1 -2 hours before mold loading to verify mold condition ok for production. During this time mold setter/changer checks and confirms the availability cooling connector, sprue bush, locating ring, limit switch, proper HRS connection(if applicable), hydraulic hose pipe(if applicable), mold lock plate, etc. If any issue is observed in a mold he(the mold setter) calls the concerned department team for its rectification before mold loading. By doing this type of maintenance production downtime reduce. For this type of maintenance, we use the Mold Loading-Unloading checksheet’s Mold Readiness page.
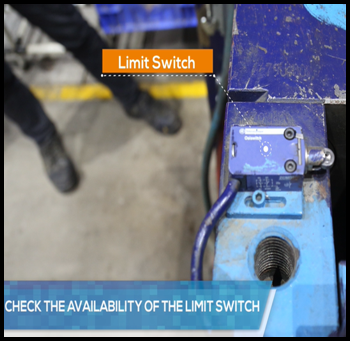
Simple Maintenance
In this type of injection mold maintenance, we clean the mold both half core and cavity before the machine starts production. As you know when mold was unloaded from the machine last time an antirust spray was used on the mold surface to prevent it from rust. Before starting the machine mold technician clean the core and cavity surface with tissue and degreaser spray and provide lubrication to the sliding parts. By doing this maintenance part rejection reduces during setup time.
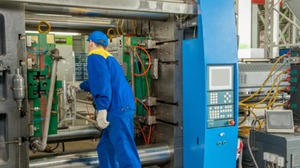
Daily Maintenance
This type of injection mold maintenance is taken to on-machine running mold. We do such maintenance to track any upcoming problems in running mold and rectify them before they occur to prevent running production from any delay/downtime. In this type of maintenance a mold supervisor checks the core & cavity surface should be free from the dent, scratches, any abnormal sound not coming from the mold, mold cooling lines working, and no material leakage from the machine nozzle & sprue bush, etc. For this type of maintenance, we use a Daily Maintenance checksheet.
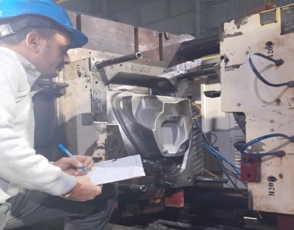
Regular Preventive Maintenance
This type of maintenance is known as regular preventive maintenance because mold is taken for preventive maintenance on a regular basis based on the plastic material used in the mold for production purposes. In this preventive maintenance, we check the entire mold, do ultrasonic cleaning, descaling of cooling lines, check the hot runner system, check mold matching & take corrective action if parts have any issues due to mold. For this type of maintenance, we use a Preventive Maintenance checksheet.
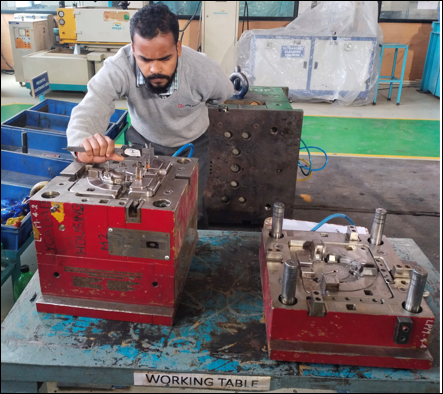
Injection Mold Preventive Maintenance Frequency
Toolroom takes mold under their possession for regular preventive maintenance if anyone one of them comes first, either (no. of shots run) or (no. of the month). Mold preventive maintenance frequency can be easily understood with the help of below table, please have a look
S. No. | Plastic Material | No. of Month | No. of Shots from last PM(Regular) |
1 | PP | 06 | 35000-40000 |
2 | HDPE | 06 | 35000-40000 |
3 | LDPE | 06 | 35000-40000 |
4 | ABS | 03 | 25000-30000 |
5 | PC | 03 | 25000-30000 |
6 | PC + ABS | 03 | 25000-30000 |
7 | AES | 03 | 25000-30000 |
8 | ASA | 03 | 25000-30000 |
9 | NYLON | 02 | 25000-30000 |
10 | PBT | 02 | 20000-25000 |
11 | PET | 02 | 20000-25000 |
12 | HIPS | 02 | 20000-25000 |
13 | SAN | 02 | 20000-25000 |
14 | POM | 02 | 20000-25000 |
15 | PVC | 02 | 20000-25000 |
16 | PC + PBT | 02 | 20000-25000 |
17 | PBT + PET | 02 | 15000-20000 |
18 | PPS | 02 | 15000-20000 |
19 | GLASS FILLED | 02 | GLASS-FILLED |
20 | BMS | 02 | 5000-10000 |
Mold Preventive Maintenance Time
If we are going for mold preventive maintenance, the first question comes to our mind that how much time & manpower requires for mold preventive maintenance. Here I am sharing a chart that will give you an idea about it –
S. No. | Machine Tonnage (Mold Running) | No. Of Manpower Require | Working Hour | Total Manhour Require |
1 | Upto 120T | 01 | 08 | 01*08 = 08 Hours |
2 | 120T-400T | 02 | 08 | 02*08 =16 Hours |
3 | 400T-900T | 02 | 16 | 02*16 = 32 Hours |
4 | 900T-1600T | 03 | 16 | 03*16 = 48 Hours |
5 | Above 1600T | 03 | 24 | 03*24 = 72 Hours |
Mold Preventive Maintenance Preparation
Before starting mold preventive maintenance we need to collect the following data –
S. No. | Document/Item Require | Purpose |
1 | Mold Preventive Maintenance Plan | To don’t miss any mold PM |
2 | Mold History Card | To enter rectification detail & check the total shot data |
3 | Mold PM Checksheet | To do preventive maintenance of mold in an effective way without missing any checkpoint |
4 | Spare Part Recording Sheet | To check & update available spare parts, if we have to use during maintenance |
5 | Daily Maintenance Checksheet | To take action on pending points which were observed in mold during running time |
6 | Last Part Approval Checksheet | To verify, is there any issues observed in part during mold running/unloading time and not close yet |
7 | Last Sample Part | Take a reference of actual problem in mold |
8 | Molding Loading – Unloading Checkpoint | To take corrective action on the problems as per machine operator feedback. |
Pro-Active/ Health Checkup
A mold health checkup, also known as a mold inspection or mold assessment, is a process conducted to evaluate the condition and health of molds used in industrial processes, such as plastic injection molding, metal casting, glass blowing, and others. The primary purpose of a mold health checkup is to identify potential issues, assess the mold’s performance, and determine if any maintenance or corrective actions are necessary to ensure optimal production and product quality.
For this type of maintenance, we use Mold Health Monitoring & Mold Assessment check sheet. Overall, conducting regular mold health checkups is an essential aspect of mold maintenance and contributes significantly to the overall success of industrial processes that rely on mold for production. It helps organizations maintain product quality, meet production targets, and ensure the safe and efficient operation of molding equipment.
Mold Health check-up carried out, when particular mold had already complete certain no. of shots run. This certain no. of shot depend upon which plastic material is use for part production. Here I am giving some data through this, you can take some idea about mold health check-up –
S. No. | Plastic Material | Health Check-up Shot (1st Time) |
1 | PP Grade | 4 Lakh Shots |
2 | TPO | 4 Lakh Shots |
3 | Nylon | 3 Lakh Shots |
4 | POM | 3 Lakh Shots |
5 | ABS | 2.5 Lakh Shots |
6 | PC | 2.5 Lakh Shots |
7 | ABS | 2.5 Lakh Shots |
8 | PC + ABS | 2.5 Lakh Shots |
9 | Hypolyene | 2.5 Lakh Shots |
Note:
- When mold reach 70% of above mention shot respectively to their running material category, mold should be taken into Health Checkup Plan for their health check-up.
- After mold health check-up done and corrective action taken against the defects in mold, mold next health check-up should be carried out before 1 lakh new shot run.

What is CAPA?
For effective injection mold maintenance, we should work on the concept of CAPA to reduce/stop the occurrence of the same problem in mold in repetition mode. In the corrective action stage, we take effective corrective action for its repair work. When corrective action is taken out mold trial is done to verify & validate the taken action.
After trial success, a good mold maintenance person starts to work on the second stage known as preventive action. Generally in this stage, we work for taking action against the previous breakdown so that it cant repeat in the future.
Benefits of Injection Mold Maintenance
Injection mold maintenance offers numerous benefits to manufacturers and organizations that rely on molds for their production processes. Here are some of the key advantages of implementing regular and effective injection mold maintenance –
- Enhanced Product Quality: Properly maintained molds produce consistent and high-quality products. Regular maintenance ensures that the mold remains in optimal condition, minimizing defects and variations in the final output.
- Increased Mold Lifespan: Regular maintenance helps to extend the life of the mold. By addressing wear and tear, preventing damage, and conducting timely repairs, the mold’s longevity is significantly enhanced, reducing the need for frequent replacements.
- Reduced Downtime: Unplanned mold breakdowns can lead to costly production downtime. Scheduled maintenance and preventive measures help avoid unexpected failures, reducing downtime and maximizing production efficiency.
- Cost Savings: Long-lasting molds and minimized downtime result in cost savings. Organizations can avoid the expense of frequent mold replacements and prevent production losses due to extended downtime.
- Improved Production Efficiency: A well-maintained mold operates more efficiently, leading to increased productivity and optimized production cycles. This results in higher output levels and better utilization of resources.
- Preventing Production Interruptions: Mold maintenance helps identify potential issues before they lead to significant problems. By addressing problems early on, manufacturers can prevent interruptions in the production process.
- Safety Assurance: Well-maintained molds are safer to operate. Regular inspections and maintenance help ensure that the mold is in good working condition, reducing the risk of accidents and injuries to workers.
- Compliance with Quality Standards: Many industries have strict quality standards and regulations. Regular mold maintenance helps organizations comply with these standards, ensuring that products meet the required specifications.
- Efficient Material Usage: A properly maintained mold minimizes material waste by producing fewer defective or rejected parts. This leads to improved material utilization and cost-effectiveness.
- Predictable Maintenance Costs: Planned maintenance allows organizations to budget for maintenance costs effectively. Regular upkeep helps avoid sudden, unexpected expenses associated with mold breakdowns.
- Better Customer Satisfaction: Consistently producing high-quality products leads to increased customer satisfaction and loyalty. Satisfied customers are more likely to return and recommend products, contributing to business growth.
- Continuous Improvement: Through regular mold maintenance, organizations can collect data and feedback on mold performance. This information can be used to identify patterns, trends, and areas for improvement in the production process.
Overall, injection mold maintenance is a proactive and essential practice for any organization using molds in their manufacturing processes. By investing in regular maintenance, companies can enjoy improved product quality, increased efficiency, cost savings, and a competitive advantage in the marketplace.
Here I am trying to give answers to some frequently asked questions related to injection mold maintenance, have a look –
What problems does injection mold neglect cause?
Neglecting injection mold maintenance can lead to several problems and challenges in the manufacturing process. Some of the key issues caused by neglecting injection mold maintenance include –
1. Reduced Product Quality.
2. Increased Scrap and Rework.
3. Unplanned Downtime.
4. Production Delays.
5. Higher Production Costs.
6. Safety Risks.
7. Customer Complaints.
8. Loss of Competitive Edge.
What is mold maintenance?
Mold maintenance is the regular and systematic upkeep of molds used in industrial processes, such as plastic injection molding, metal casting, and glass blowing. It involves cleaning, inspecting, and repairing molds to ensure consistent product quality, prevent breakdowns, and extend their lifespan.