Introduction
Precision and control are paramount to achieving high-quality, defect-free plastic parts in the intricate world of injection molding. At the heart of this process lies the hot runner temperature controller, a sophisticated device that plays a critical role in maintaining optimal conditions within the hot runner system. In this article, we embark on a journey to understand the inner workings of a hot runner temperature controller, uncovering its mechanisms and exploring how it contributes to the seamless production of flawless plastic components.
To explore Hot Runner System with Auto Plastics World, read more
The Essence of Hot Runner Systems
Before delving into the specifics of a hot runner temperature controller, it’s essential to grasp the concept of a hot runner system. Imagine it as the lifeline between the injection molding machine and the mold itself. In essence, the hot runner system consists of a network of heated channels or nozzles that transport molten plastic from the injection unit to the mold cavities.

Maintaining an Optimal Flow: The Role of Temperature
Temperature control is paramount in injection molding. The viscosity of the molten plastic is heavily influenced by temperature, and maintaining the right viscosity is crucial for consistent flow, fill, and overall part quality. This is where the hot runner temperature controller steps in.
- Temperature Sensing: The process begins with temperature sensors strategically placed within the hot runner channels. These sensors continuously monitor the temperature of the molten plastic as it flows through the system. The real-time temperature data forms the foundation for precise control.
- Feedback Loop: The temperature data collected by the sensors is fed back to the hot runner temperature controller’s central control unit. This unit serves as the brain of the operation, processing the incoming data and making necessary adjustments to maintain the desired temperature setpoints.
- Heating Elements: Within the hot runner channels, embedded heating elements are responsible for regulating the temperature. When the temperature begins to deviate from the setpoint, the controller adjusts the power supplied to the heating elements. As a result, the elements generate heat to increase the temperature or reduce it to prevent overheating.
- Precision Control: The hot runner temperature controller’s advanced software employs complex algorithms to fine-tune the heating element’s output. This level of precision ensures that the molten plastic maintains its optimal viscosity throughout its journey, from the injection unit to the mold cavities.
Advancements and Innovation
In recent years, technology has propelled hot runner temperature controllers to new heights, offering unprecedented levels of control and efficiency –
- Multi-Zone Temperature Control: Modern controllers are equipped with multi-zone capabilities, enabling independent temperature control in different sections of the mold. This feature optimizes material flow and minimizes part variations.
- Smart Connectivity: Some controllers are integrated with smart technology, enabling remote monitoring and control. Manufacturers can oversee operations, analyze data, and make real-time adjustments from a distance, enhancing process control and efficiency.
- Adaptive Algorithms: Advanced controllers incorporate adaptive algorithms that anticipate and adjust to changing conditions. This ensures stable temperature control even in dynamic production environments, reducing downtime and optimizing productivity.
Uses and Applications
Hot runner temperature controllers find their primary use in the plastic injection molding process. They are designed to regulate and maintain precise temperature profiles within the hot runner system, which consists of heated channels that deliver molten plastic into mold cavities. These controllers ensure uniform temperature distribution, preventing premature cooling of the melt and avoiding defects such as flow imbalances, warping, and inconsistent part quality.

Applications of hot runner temperature controllers span a wide range of industries and products, including –
- Automotive: Precision parts like dashboards, interior panels, and automotive components.
- Consumer Goods: Manufacturing of items such as electronic casings, appliance parts, and packaging.
- Medical: Production of medical device components, laboratory equipment, and consumables.
- Electronics: Creation of connectors, housings, and enclosures for electronic devices.
- Industrial Equipment: Manufacturing of complex parts for machinery and industrial tools.
Troubleshooting of Hot Runner Temperature Controllers
Troubleshooting hot runner temperature controller breakdowns can help identify and address issues efficiently, ensuring minimal downtime and optimal production. Here’s a step-by-step guide to troubleshooting common problems with hot runner temperature controllers –
No Power or Display Issues
- Check the power source and ensure the controller is properly plugged in.
- Verify that circuit breakers or fuses are intact and not tripped.
- Inspect power cords and connections for damage or loose connections.
- Test the power outlet with another device to confirm it’s functioning.
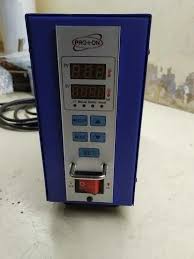
Temperature Fluctuations or Inaccuracies
- Ensure the thermocouples or RTDs (resistance temperature detectors) are securely attached and in proper contact with the mold or hot runner system.
- Calibrate or replace faulty temperature sensors.
- Check for loose or damaged wiring connections.
- Verify that the setpoint and actual temperature values match.
- Clean or replace contaminated or worn-out thermocouples or sensors.
Heating Element Issues
- Inspect the heating elements for physical damage or visible signs of wear.
- Test the heating elements for continuity using a multimeter.
- Replace faulty or burnt-out heating elements.
- Check for proper voltage supply to the heating elements.

Communication or Control Problems
- Ensure communication cables (if applicable) are properly connected and not damaged.
- Test the controller’s communication functions using appropriate tools or software.
- Update or reset the controller’s software as per the manufacturer’s guidelines.
Error Messages or Alarms
- Refer to the controller’s manual to interpret error messages or alarms.
- Address the underlying issues causing the alarms, such as temperature deviations, sensor failures, or communication errors.
- Reset the controller after addressing the root cause of the alarm.
Overheating or Malfunctioning Components
- Inspect the internal components for signs of overheating, burnt traces, or damaged relays.
- Ensure proper ventilation and cooling mechanisms are in place to prevent overheating.
- Replace damaged components or relays as needed.
Calibration Issues
- Follow the manufacturer’s guidelines to calibrate the controller accurately.
- Check and adjust the controller’s calibration settings as required.
External Factors
- Consider any environmental factors that could impact the controller’s performance, such as ambient temperature fluctuations, humidity, or electrical interference.
Professional Assistance
- If troubleshooting doesn’t resolve the issue, consult the manufacturer’s technical support or a qualified technician for expert assistance.
- In some cases, it may be necessary to send the controller to an authorized repair center.
**Regular preventive maintenance, routine inspections, and proper usage can also help minimize the occurrence of breakdowns. Keep a log of any issues, repairs, and maintenance performed on the hot runner temperature controller for future reference.
Pros of Hot Runner Temperature Controllers
- Enhanced Part Quality: Precise temperature control leads to improved surface finish, dimensional accuracy, and structural integrity in molded parts.
- Reduced Material Waste: Optimal temperature management reduces material degradation, minimizing waste and costs.
- Faster Cycle Times: Controlled temperature ensures efficient filling and cooling, reducing production cycle times.
- Design Flexibility: Improved flow control enables the molding of intricate designs and thin-walled parts.
- Energy Efficiency: Advanced controllers optimize energy consumption by regulating heating elements.
Cons of Hot Runner Temperature Controllers
- Initial Cost: High-quality hot runner temperature controllers can represent a significant initial investment.
- Maintenance: Regular maintenance and calibration are essential to ensure consistent performance.
- Complex Setup: Proper installation and calibration require expertise and training.
Best Supplier of Hot Runner Temperature Controllers
- Yudo Hot Runner Systems
- Mold Masters
- Synventive Molding Solutions
- HRSflow
- Mold Hotrunner Solutions (MHS)
- Mastip Technology
- Athena Controls
Conclusion
The hot runner temperature controller stands as a testament to the marriage of precision engineering and cutting-edge technology in the field of injection molding. Through the synergy of temperature sensing, feedback loops, heating elements, and sophisticated algorithms, this device ensures that the molten plastic flows smoothly, fills mold cavities flawlessly, and produces high-quality plastic parts with unmatched accuracy. As innovation continues to propel the manufacturing landscape forward, the hot runner temperature controller remains an essential tool in the quest for perfection in plastic part production.
FAQs
Explain Hot Runner Vs Cold Runner Mold.
Hot Runner Mold :-
Channels: Hot runner molds use heated channels to deliver molten plastic directly to the mold cavities.
Material Savings: Eliminates the need for a solid “runner” system, reducing material waste and costs.
Cycle Time: Faster production due to reduced cooling time for runners.
Gate Vestige: Minimal or no gate marks on finished parts.
Complex Designs: Ideal for intricate or multi-cavity molds, offering uniform filling and quality.
Initial Cost: Higher initial investment due to complex design and components.
Cold Runner Mold :-
Channels: Cold runner molds have unheated channels (runners) that solidify and are later discarded.
Material Waste: Generates more waste from solidified runners, impacting cost efficiency.
Cycle Time: Slightly longer cycle time due to cooling of runners.
Gate Vestige: Potential gate marks on parts where runners are attached.
Simplicity: Simpler design, suitable for basic part geometries and lower production volumes.
Initial Cost: Lower initial investment due to simpler design and reduced complexity.
What is Hot Runner Controller?
A hot runner controller is a crucial component in the plastic injection molding process, specifically in systems that utilize hot runner molds. The hot runner controller is responsible for precisely regulating and maintaining the temperature of the hot runner system within the mold. The hot runner system consists of heated channels or nozzles that distribute molten plastic to the mold cavities, ensuring efficient and consistent filling.
The key functions of a hot runner controller include:
Temperature Control: The controller monitors and adjusts the temperature of the hot runner system to ensure the molten plastic remains at the optimal temperature for injection into the mold cavities.
Uniform Flow: By maintaining consistent temperatures throughout the hot runner channels, the controller ensures uniform flow and distribution of the molten plastic, preventing imbalances and defects in the final molded parts.
Preventing Cold Flows: The controller prevents premature cooling of the plastic material in the hot runner system, preventing material solidification and potential blockages.
Energy Efficiency: Advanced controllers optimize the use of heating elements, minimizing energy consumption while maintaining accurate temperature control.
Cycle Time Optimization: By controlling the temperature precisely, the hot runner controller contributes to faster cycle times by promoting efficient filling and cooling of the mold.
Quality Improvement: The controller’s role in maintaining consistent temperature profiles leads to improved part quality, reduced defects, and enhanced surface finish.
Hot runner controllers are equipped with temperature sensors that monitor the temperature within the hot runner channels. These sensors send real-time data to the controller, which uses this information to regulate the power supplied to the heating elements. The controller’s software employs algorithms to adjust the heating element output as needed to maintain the desired temperature setpoints.
What is Hot Runner Manifold?
A hot runner manifold is a vital component within a plastic injection molding system. It refers to a network of heated channels or passages that distribute molten plastic from the injection molding machine’s nozzle to multiple cavities in the mold without the need for a traditional, solid runner system.
The manifold is designed to maintain a consistent temperature in each channel, ensuring the plastic remains in its molten state as it flows into the mold cavities. This precise temperature control eliminates material wastage, reduces cycle times, and enhances part quality by preventing premature cooling or solidification of the plastic material.
Hot runner manifolds come in various configurations, such as single-tip, multi-tip, and valve-gate systems, catering to different molding requirements. They play a crucial role in optimizing the injection molding process by promoting uniform material distribution, faster production, and cost efficiency, making them a preferred choice for high-quality, high-volume manufacturing.