Introduction
Ejector pins may be small components in injection molding, but their role is crucial for ensuring the smooth release of molded parts from the mold cavity. A well-designed ejector pin system can significantly impact the efficiency, quality, and cost-effectiveness of the injection molding process. In this comprehensive guide, we will delve into the key aspects of ejector pin design and application, exploring their importance, types, best practices, and maintenance.
Understanding Ejector Pins
Ejector pins are fundamental components in the injection molding process, playing a critical role in ensuring the successful and efficient ejection of molded parts from the mold cavity. Their function might seem simple, but the design, placement, and operation of ejector pins have a significant impact on the overall quality of the final product, the production cycle, and the longevity of the mold. Let’s dive deeper into the intricacies of ejector pins to gain a comprehensive understanding of their importance.
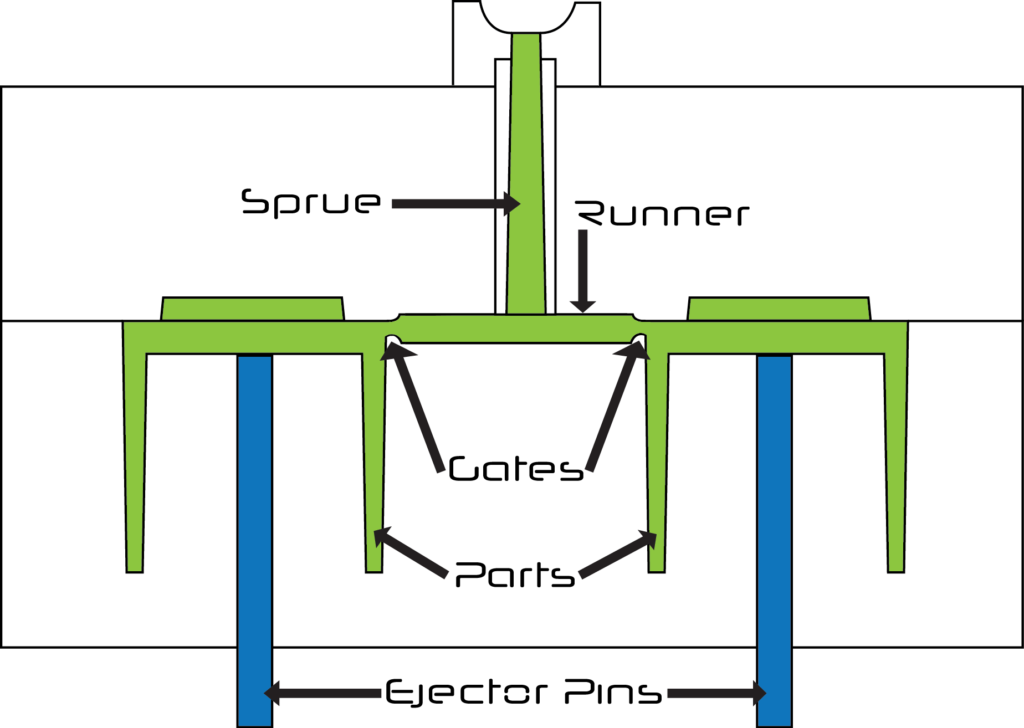
Role of Ejector Pins in Injection Molding
Ejector pins serve as the final step in the injection molding cycle. After the molten plastic material has been injected into the mold cavity, cooled, and solidified, the resulting plastic part needs to be carefully and efficiently removed from the mold. This is where ejector pins come into play. They apply force to the molded part, dislodging it from the mold’s intricate features, undercuts, and other complex shapes that might otherwise trap the part.
Importance of Proper Ejector Pin Design
While the concept of ejecting a part from a mold might seem straightforward, the design and application of ejector pins are anything but simple. A well-designed ejector pin system can lead to several crucial benefits –
Minimized Part Damage
Ejector pins must be carefully designed to apply force evenly across the part’s surface. Poorly designed pins or improper placement can lead to cosmetic defects, scratches, or even deformation of the part, rendering it unusable.
Optimized Cycle Time
Efficient ejection contributes to reducing the overall cycle time of the injection molding process. Properly designed ejector pins ensure a swift and smooth ejection process, allowing for faster mold opening and closing cycles.
Consistency and Quality
Consistent ejection prevents part sticking, warping, or distortion, resulting in consistently high-quality parts with precise dimensions and details.
Longevity of the Mold
The force exerted by ejector pins can impact the longevity of the mold itself. If ejector pins are improperly designed or applied, they can cause excessive wear and tear on the mold, leading to more frequent maintenance and mold replacement.
Reduced Production Costs
Efficient ejection and reduced part damage translate into lower scrap rates and higher yields, leading to cost savings in production.
Factors Influencing Ejector Pin Design
Several factors influence the design and application of ejector pins –
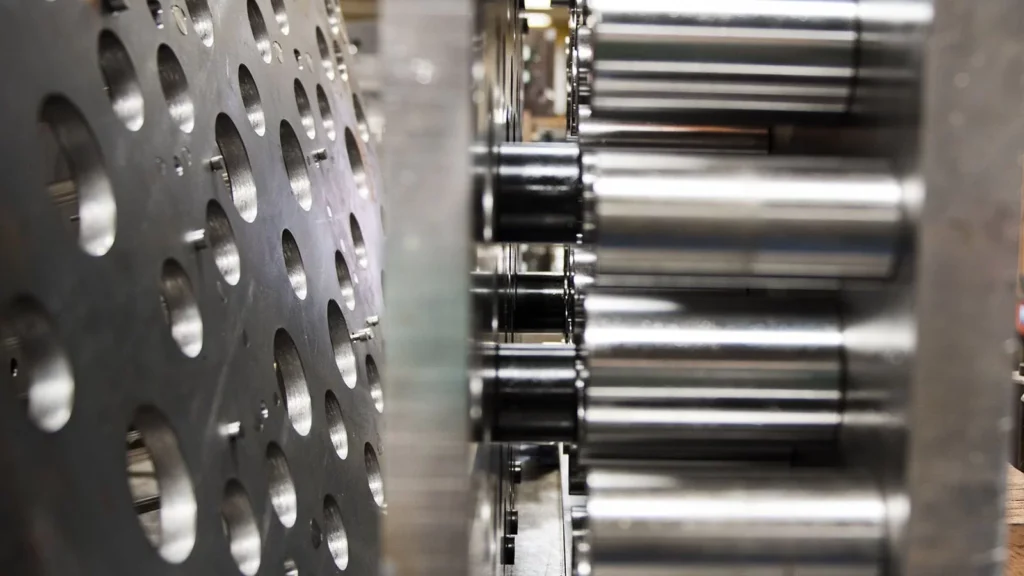
Part Geometry
The complexity of the part’s shape, including undercuts, protrusions, and surface details, affects the design of the ejector pin system.
Material and Wall Thickness
Different materials and wall thicknesses require varying amounts of force for ejection. This impacts pin size, quantity, and placement.
Draft Angles
Proper draft angles ensure smooth ejection by preventing the part from binding against the mold surfaces.
Ejection Area
The number and placement of ejector pins must be carefully determined to evenly distribute ejection force and avoid creating stress points on the part.
Ejector Plate Design
The layout and construction of the ejector plate, where the pins are mounted, are critical for achieving balanced ejection and avoiding misalignment issues.
Types of Ejector Pins: A Detailed Exploration
Ejector pins are indispensable components in injection molding, playing a vital role in the successful ejection of molded parts from the mold cavity. Different mold designs, part geometries, and material requirements necessitate various types of ejector pins. Let’s delve into the details of these types to better understand their characteristics, advantages, and applications.
Straight Ejector Pins
Straight ejector pins are the most common and straightforward type of ejector pins. They are cylindrical in shape and exert a direct, even force on the part for ejection. Straight pins are typically used for simple, flat-sided parts or in areas where minimal force is required. Their simplicity and versatility make them a staple in injection molding.
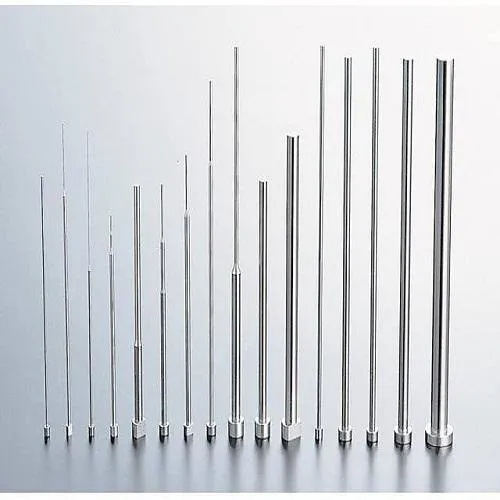
Blade Ejector Pins
Blade ejector pins, also known as ejector blades or ejector sleeves, are designed to eject parts from areas with complex shapes, undercuts, or tight spaces. They feature a flat, blade-like shape that allows them to slide along the mold’s surfaces, facilitating the ejection of intricate parts without causing damage. Blade ejector pins are ideal for molds with deep cavities or complex geometries.
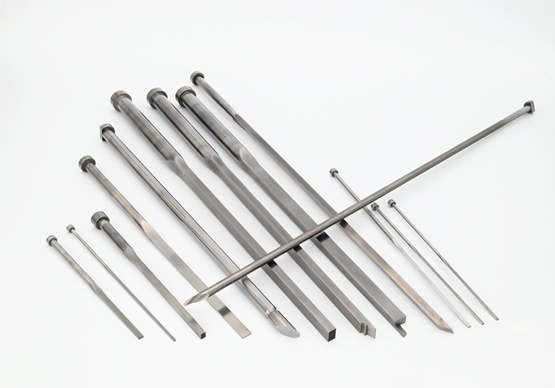
Sleeve Ejector Pins
Sleeve ejector pins are a variation of the blade ejector pins. They consist of a cylindrical sleeve that surrounds a smaller core pin. This design provides increased stability and control during ejection, making them suitable for parts with complex shapes and tight tolerances. Sleeve ejector pins are particularly useful for ejecting fragile or delicate parts without causing deformation.
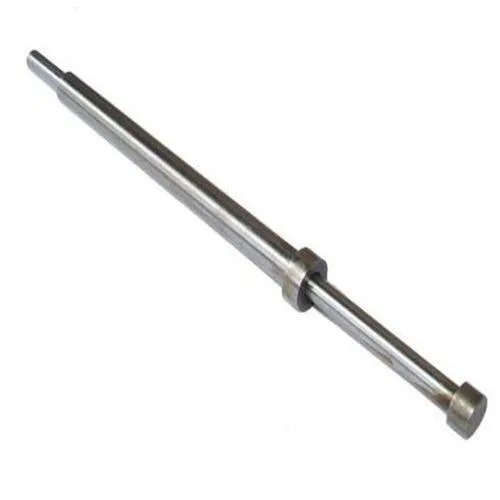
Through-Hardened Vs Nitrided Ejector Pins
Ejector pins can be made from different materials and undergo various heat treatment processes to enhance their durability and wear resistance –
Through-Hardened Ejector Pins
These pins are uniformly hardened throughout their entire cross-section, providing excellent strength and wear resistance. They are suitable for general-purpose applications and are often made from tool steels like H13.
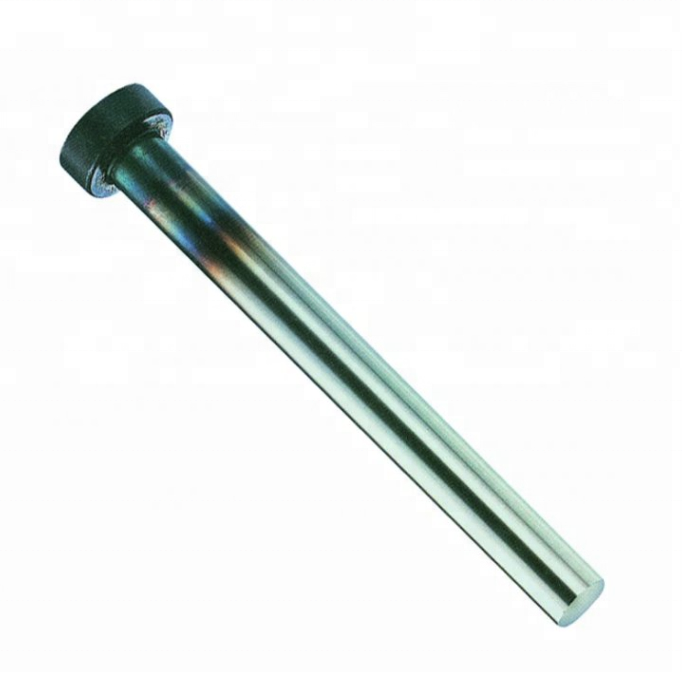
Nitrided Ejector Pins
Nitriding is a surface-hardening process that introduces nitrogen into the material’s surface, creating a hard and wear-resistant layer. Nitrided pins maintain a tough core while offering a tough and durable surface, making them well-suited for extended production runs and abrasive materials.
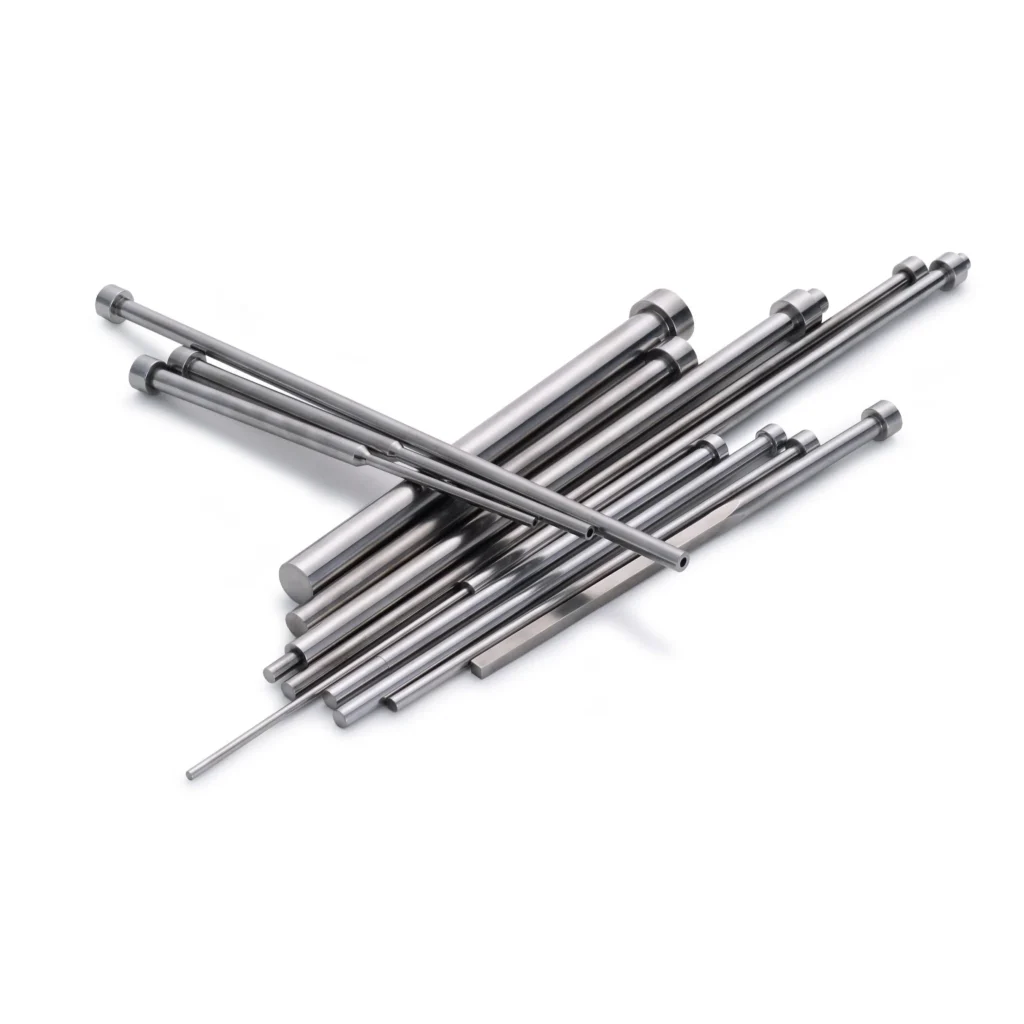
Selecting the Right Type
Choosing the appropriate type of ejector pin depends on factors such as –
Part Geometry
The complexity of the part’s shape, including undercuts and intricate features, will influence the type of ejector pin required.
Material and Strength
Different materials and part requirements may necessitate varying levels of ejection force and wear resistance.
Tight Tolerances
For parts with tight dimensional tolerances, sleeve or blade ejector pins might be preferred to ensure precision during ejection.
Production Volume
The expected production volume and mold longevity may impact the choice between through-hardened and nitrided ejector pins.
Design Considerations for Ejector Pins
Ejector pins are integral components in the injection molding process, responsible for efficiently and smoothly releasing molded parts from the mold cavity. Designing ejector pins requires careful consideration of various factors to ensure optimal performance, minimize part damage, and enhance the overall injection molding process. Let’s delve into the key design considerations that play a crucial role in achieving successful ejection.
Pin Size and Length
Determining the appropriate pin size and length is fundamental to effective ejection. Pins that are too small or short might not provide enough force for proper ejection, leading to part sticking or damage. Conversely, pins that are too large could cause excessive stress on the part or mold. The pin length should account for the depth of the mold and the required ejection stroke.
Placement and Quantity
Strategically positioning ejector pins is essential to ensure even and balanced ejection forces across the part’s surface. The number and placement of pins depend on factors such as part geometry, material properties, and ejection area. Properly distributed pins prevent warping, distortion, and cosmetic defects on the part.
Draft Angles and Surface Finish
Draft angles on the part’s features, combined with the surface finish of the mold cavity, play a significant role in smooth ejection. Adequate draft angles ensure that the part can be easily released without binding against the mold surfaces. A smooth surface finish reduces friction during ejection, minimizing the risk of part damage.
Material Selection
Choosing the right material for ejector pins is crucial for durability, wear resistance, and overall performance. Pins are often made from tool steels, with through-hardened and nitrided options available. Material selection should take into account factors such as the type of plastic being molded, expected production volume, and part complexity.
Ejection Area Design
The design of the ejector plate and the arrangement of pins on it contribute to efficient ejection. A well-designed ejector plate ensures that pins move smoothly and evenly, minimizing the risk of misalignment or binding. The plate’s design also impacts the distribution of ejection force and prevents concentrated stress points on the part.
Balanced Ejection
Balanced ejection involves distributing ejection forces evenly across the part’s surface to prevent distortion or damage. This is particularly important for parts with complex geometries or varying wall thicknesses. Achieving balanced ejection requires careful pin placement and a well-designed ejector plate system.
Preventing Part Damage
Ejector pins should be designed to apply a controlled force that releases the part without causing any deformation, scratches, or cosmetic defects. Careful consideration of pin size, shape, and placement helps prevent damage to the part during ejection.
Minimizing Flash and Mold Marks
Improperly designed ejector pins or inadequate ejection force can lead to flash (excess material) or mold marks on the part. These defects affect the part’s appearance and quality. Designing the ejector pin system to apply the right amount of force and ensuring proper pin placement can minimize these issues.
Ejector Pin Systems
Ejector pin systems are integral to the injection molding process, facilitating the smooth and efficient release of molded parts from the mold cavity. These systems encompass various components and mechanisms that work in coordination to ensure controlled and balanced ejection. In this detailed exploration, we’ll delve into the key elements of ejector pin systems, their design considerations, and their role in optimizing injection molding operations.

Ejector Plate Design
The ejector plate serves as the foundation for the ejector pin system. It provides the structure on which ejector pins are mounted and guides their movement during ejection. The design of the ejector plate influences the distribution of ejection forces and ensures even and consistent part release. Proper alignment and precision machining of the ejector plate is essential to avoid misalignment issues that can lead to part damage or deformation.
Ejector Pins
Ejector pins are the core components of the ejector pin system. As discussed earlier, these pins exert controlled force on the molded part to release it from the mold cavity. The type, size, and placement of ejector pins are crucial design considerations that impact ejection efficiency, part quality, and mold longevity. Straight, blade, and sleeve ejector pins, as well as considerations like material selection and surface finish, all play a role in achieving successful ejection.
Return Systems
After ejection, the ejector pins need to return to their original positions for the next molding cycle. Return systems provide the means for this movement. Common types of return systems include –
Springs
Mechanical springs are often used to push the ejector pins back into their initial positions. The selection of spring type and strength should account for the force required for ejection and the pin’s stroke length.
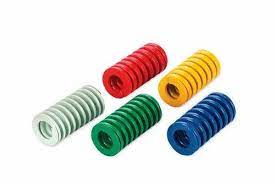
Hydraulic or Pneumatic Cylinders
These systems use fluid pressure to retract the ejector pins. They offer precise control over pin movement and can be particularly useful for molds with large or heavy parts.
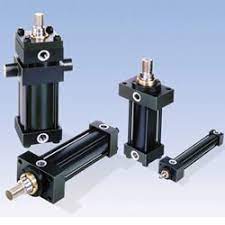
Wear Plates and Guide Components
Wear plates are installed on the mold to guide the movement of ejector pins and minimize friction. They help prevent direct contact between the pins and the mold, reducing wear and prolonging the mold’s lifespan. Guide components, such as leader pins and bushings, aid in maintaining the alignment and stability of the ejector pin system, preventing binding or misalignment during ejection.
Alignment and Synchronization
Proper alignment and synchronization of the ejector pin system are critical for achieving balanced ejection and preventing part damage. Misaligned or unsynchronized ejector pins can lead to uneven ejection forces, which may cause warping, deformation, or other cosmetic defects on the part. Maintaining precise alignment and synchronization requires careful mold design and precision machining.
Lubrication and Maintenance
Appropriate lubrication of the ejector pin system minimizes friction and wear during ejection and retraction. Regular maintenance, including cleaning and lubrication, is essential to ensure consistent and reliable performance over time. Neglecting maintenance can lead to increased wear on components, reduced part quality, and increased downtime for mold repairs.
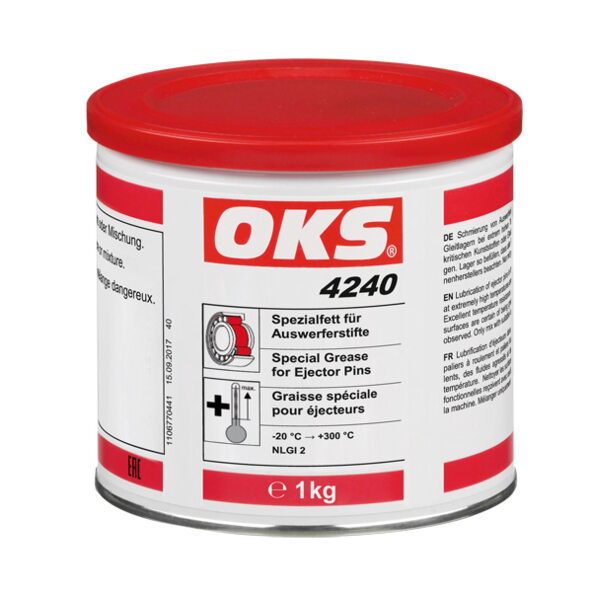
Best Practices for Ejector Pin Application
Effective ejector pin application is vital for achieving successful injection molding outcomes. Implementing best practices ensures efficient part release, minimizes damage, and enhances overall production quality. In this detailed guide, we will explore the key best practices for ejector pin application and their significance in optimizing the injection molding process.
Balanced Ejection
Balanced ejection involves distributing ejection forces evenly across the part’s surface to prevent warping, distortion, or cosmetic defects. Uneven ejection can lead to uneven stresses on the part, resulting in quality issues. To achieve balanced ejection, strategically position ejector pins, considering part geometry and material properties.
Proper Pin Size and Quantity
Selecting the appropriate pin size and quantity is crucial for achieving effective ejection. Too few pins may lead to insufficient force, causing part sticking or deformation. Too many pins can create excessive stress and damage. Calculate the required force for ejection based on part material, geometry, and wall thickness to determine the optimal pin size and quantity.
Draft Angles and Surface Finish
Draft angles on the part’s features and a smooth mold cavity surface finish facilitate smooth ejection. Draft angles prevent the part from binding against the mold, while a polished surface reduces friction during ejection. Adequate draft angles and a proper surface finish contribute to seamless part release and minimize the risk of cosmetic defects.
Pin Placement and Design
Carefully consider pin placement to ensure even ejection. Position pins strategically, taking into account areas with complex geometries, undercuts, and thin walls. A well-designed ejector plate system should allow for smooth and synchronized movement of all pins, preventing misalignment issues.
Preventing Part Damage
Ejector pins should exert controlled force to release the part without causing damage. Avoid excessive force that could lead to part deformation or cosmetic defects. Implement proper pin design and placement to minimize the risk of scratches, dents, or other damage during ejection.
Regular Maintenance and Lubrication
Maintain the ejector pin system through regular cleaning and lubrication. Lubrication reduces friction and wear, prolonging the life of the components. Neglecting maintenance can lead to increased downtime for mold repairs and decreased production efficiency.
Maintenance and Troubleshooting of Ejector Pin Systems
Maintaining and troubleshooting ejector pin systems is essential for ensuring the efficient and reliable operation of injection molding processes. Regular maintenance and prompt resolution of issues contribute to consistent part quality, extended mold life, and minimized downtime. In this detailed guide, we will delve into the key aspects of maintenance and troubleshooting for ejector pin systems.
Maintenance
Regular maintenance routines help prevent premature wear, ensure smooth operation, and extend the lifespan of ejector pin systems –
Cleaning
Regularly clean the ejector pins, plates, and associated components to remove debris, dust, and residues that can accumulate over time. Use appropriate cleaning agents and techniques that do not damage the pins or mold surfaces.
Lubrication
Apply suitable lubricants to reduce friction and wear between moving components, such as ejector pins and sleeves. Proper lubrication enhances the efficiency of the ejection process and prolongs the life of the ejector pin system.
Inspect Wear Components
Regularly inspect wear plates, guide components, and springs for signs of wear, damage, or misalignment. Replace worn or damaged components promptly to prevent issues during operation.
Spring Inspection
If springs are part of the return system, inspect them for fatigue, corrosion, or deformation. Replace worn or damaged springs to maintain consistent ejection force.
Alignment Check
Periodically verify the alignment of the ejector pin system, ensuring that pins move smoothly and evenly during ejection and retraction. Misaligned pins can cause uneven ejection and part damage.
Pin Surface Inspection
Examine the surfaces of ejector pins for signs of wear, chipping, or damage. Replace pins that show significant wear to maintain consistent ejection quality.
Troubleshooting
Promptly addressing issues with the ejector pin system is crucial to preventing production delays and maintaining part quality.
Sticking or Binding
If parts are sticking in the mold or pins are binding during ejection, check for misalignment, insufficient lubrication, or debris. Address these issues to ensure smooth part release.
Part Damage
If parts exhibit damage or cosmetic defects during ejection, review pin size, placement, and force. Adjust these parameters to prevent excessive force that could cause damage.
Uneven Ejection
Uneven ejection can result from misaligned pins, worn components, or inadequate force distribution. Ensure proper alignment, replace worn parts, and adjust pin placement if needed.
Excessive Flash
If excess material (flash) forms around the part during ejection, evaluate the ejection force, pin size, and mold design. Adjust these factors to prevent overexertion of force.
Unusual Noises
Unusual noises during ejection may indicate misalignment, interference, or worn components. Investigate and rectify the source of the noise to prevent further damage.
Inconsistent Part Release
If parts are released inconsistently, assess pin placement, alignment, and wear. Make necessary adjustments to ensure consistent and controlled ejection.
Conclusion: Optimizing Ejector Pin Systems for Injection Molding Success
Ejector pin systems play a pivotal role in the injection molding process, enabling the efficient release of molded parts from the mold cavity. From design considerations to application best practices and maintenance strategies, a comprehensive understanding of ejector pin systems is crucial for achieving successful and high-quality injection molding outcomes.
Key Takeaways
- Critical Role: Ejector pins are not mere afterthoughts; they are essential components that impact part quality, cycle time, and mold longevity. Properly designed and implemented ejector pin systems contribute to efficient, consistent, and cost-effective injection molding operations.
- Design Precision: Thoroughly analyzing factors such as part geometry, material properties, draft angles, and pin placement is fundamental to effective ejector pin system design. The proper design prevents issues like part damage, cosmetic defects, and uneven ejection.
- Balanced Ejection: Achieving a balanced ejection ensures an even distribution of forces, preventing warping, distortion, and other defects. This requires meticulous consideration of pin size, quantity, and placement.
- Maintenance Excellence: Regular maintenance routines, including cleaning, lubrication, and component inspection, are essential to prolonging the life of ejector pin systems and maintaining consistent performance.
- Troubleshooting Proficiency: Rapidly identifying and addressing issues such as sticking, part damage, or uneven ejection is crucial to minimizing production disruptions and ensuring continuous part quality.
- Collaborative Efforts: Successful ejector pin application involves collaboration among mold designers, toolmakers, and operators. Clear communication and a shared understanding of requirements lead to optimized ejector pin system performance.
Achieving Injection Molding Excellence
Ejector pin systems exemplify the intricate interplay between design, engineering, and operational execution within the injection molding process. By embracing the knowledge presented in this guide, manufacturers can establish a strong foundation for achieving injection molding excellence –
- Efficient part release, minimizing cycle times, and optimizing production efficiency.
- Consistent part quality, free from defects, damage, and cosmetic imperfections.
- Prolonged mold life and reduced maintenance requirements.
- Enhanced production predictability and minimized downtime.
In essence, the proper design, implementation, maintenance, and troubleshooting of ejector pin systems are integral to the success of injection molding operations. As the manufacturing industry continues to evolve, a strong grasp of these principles empowers manufacturers to deliver high-quality products, meet customer demands, and maintain a competitive edge. By embracing the comprehensive understanding provided in this guide, manufacturers are better equipped to navigate the intricate world of ejector pin systems and drive injection molding processes toward optimal outcomes.
FAQ
What is an Ejector Pin Mark?
An ejector pin mark is a shallow indentation or blemish on a molded plastic part’s surface, resulting from the contact between the ejector pins and the mold during the ejection process. These marks are often circular or linear and can vary in size and depth. Ejector pin marks are cosmetic defects that can mar the appearance of the final product. Proper design considerations, such as pin placement, size, and ejection force, along with appropriate part geometry and surface finish, are essential to minimize the occurrence of ejector pin marks and maintain the aesthetic quality of molded parts.
How do you remove Ejector Pin Mark from the part?
To remove an ejector pin mark from a part, several methods can be employed. One common approach is post-processing, involving sanding, polishing, or buffing the affected area to blend the mark with the surrounding surface. Alternatively, adjusting the ejection force, optimizing pin placement, or using special pin coatings can help minimize or eliminate marks during molding. Proper design, controlled ejection, and careful finishing techniques are key to effectively removing ejector pin marks while preserving the part’s aesthetic integrity.
What is an Ejector Pin?
An ejector pin is a mechanical component used in injection molding. It aids in releasing a molded part from the mold cavity once it has cooled and solidified. These pins apply controlled force to the part’s surface, facilitating its smooth and efficient removal. Ejector pins come in various types, including straight, blade, and sleeve pins, each designed for specific molding scenarios. Proper design and placement of ejector pins are crucial to ensure balanced ejection forces, prevent part damage, and maintain high-quality production in injection molding processes.
Why are Ejector Pins Important?
Ejector pins are essential in injection molding as they enable the proper release of molded parts from the mold cavity. By exerting controlled force, they prevent parts from sticking, warping, or getting trapped in complex geometries. Ejector pins ensure efficient production by minimizing cycle times, maintaining part quality, and preventing damage. Their proper design and application contribute to smooth ejection, consistent output, and cost-effective manufacturing. In essence, ejector pins play a critical role in achieving successful injection molding processes and ensuring the production of high-quality plastic parts.