Introduction
CNC machining has redefined modern manufacturing, fusing advanced technology with precise craftsmanship. It’s the art of using computer-controlled machines to craft intricate parts with unmatched accuracy. In this article, we’ll demystify the world of CNC machining, exploring its processes, significance, and the harmony between efficiency and precision that drives its success. From the basics to the latest innovations, join us in uncovering how CNC machining shapes the things around us with unparalleled finesse.
Understanding the CNC Machining Process
CNC machining, short for Computer Numerical Control machining, represents a pivotal advancement in manufacturing technology. It involves using computer-controlled machines to shape and create intricate parts from various materials with exceptional precision. Unlike traditional manual machining, where human intervention is more prominent, CNC machining relies on programmed instructions to guide the machinery’s movements. This article delves into the core elements of the CNC machining process, shedding light on its inner workings, advantages, and the steps involved in transforming digital designs into tangible products.
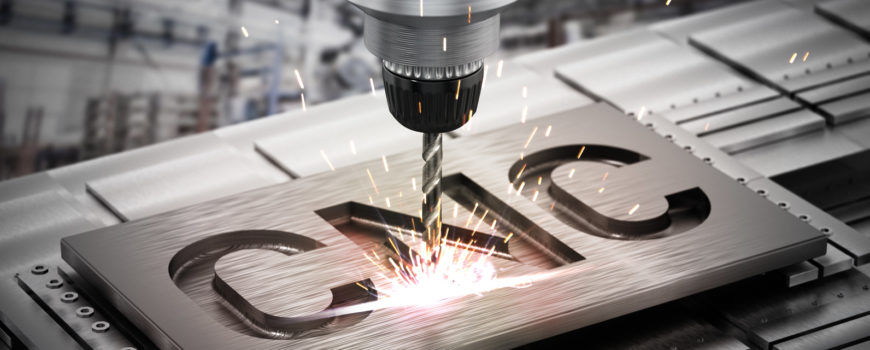
The Basics of CNC Machining
Concept
CNC machining, driven by computer-controlled machines and precise programming, is a cornerstone of modern manufacturing. It ensures unparalleled accuracy, faster production, and the creation of complex parts that were once challenging with manual methods. This technology revolutionizes industries by optimizing processes, reducing human errors, and enabling the production of intricate components crucial for sectors ranging from aerospace to medical devices.
A shift from Manual Machining to Automated Computer-Guided Processes
The transition from manual machining to automated, computer-guided processes marks a pivotal advancement in manufacturing. Traditional manual methods relied on human skill and physical labor, leading to variations in precision and time-consuming production. In contrast, automated CNC machining employs pre-programmed instructions to control machinery, ensuring consistent accuracy and enhanced efficiency. This shift eliminates human errors, accelerates production rates, and enables the creation of intricate designs that were once unattainable. The marriage of technology and machinery empowers industries to achieve higher productivity, reduce costs, and innovate faster, shaping a new era of precise and streamlined manufacturing processes.
Role of CAD (Computer-Aided Design) Software
CAD (Computer-Aided Design) software plays a crucial role in modern machining by enabling the creation of intricate digital models. Designers use CAD to craft detailed 3D representations of components, which are then translated into machine-readable instructions for CNC machining. This process ensures precision and consistency, allowing engineers to visualize, modify, and optimize designs before they are physically produced. CAD software bridges the gap between imagination and realization, facilitating efficient and accurate manufacturing while reducing errors and enhancing product development.
Components of CNC Machinery
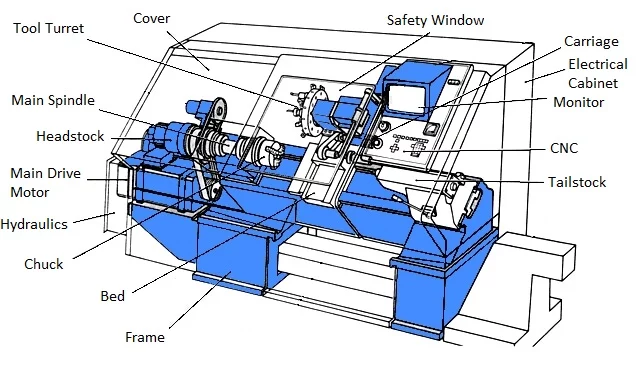
- Controller
- Function: Acts as the brain of the CNC machine, interpreting the programmed instructions and generating control signals for other components.
2. Servo Motors
- Function: Provide precise and controlled movement to the machine’s axes, ensuring accurate positioning of the tool or workpiece.
3. Spindle
- Function: Rotates the cutting tool at various speeds, facilitating the material removal process in machining operations like milling or drilling.
4. Tool Holder
- Function: Securely holds the cutting tool in place, allowing it to engage with the workpiece and perform machining operations.
5. Worktable or Bed
- Function: Provides a stable surface for holding the workpiece in position during machining, allowing for controlled movement and accurate cuts.
6. Guideways and Linear Bearings
- Function: Facilitate smooth and precise movement of machine components along different axes, ensuring minimal friction and high accuracy.
7. Coolant System
- Function: Supplies coolant (usually a mix of water and oil) to the cutting area to dissipate heat generated during machining, extending tool life and improving surface finish.
8. Control Panel
- Function: Offers a user interface for operators to input commands, set parameters, and monitor the machining process in real-time.
9. Tool Changer
- Function: Automatically swaps different tools based on the program’s requirements, reducing downtime and enabling multi-tool operations.
10. Encoders and Feedback Systems
- Function: Provide real-time position feedback to the controller, ensuring precise positioning and movement of the machine’s axes.
11. Power Supply and Electrical Components
- Function: Provide the necessary electrical power for the CNC machine’s operation, ensuring all components function as intended.
12. Computer System
- Function: Houses the software that generates and stores CNC programs, facilitating communication between the operator and the machine.
13. Emergency Stop System
- Function: Enables immediate cessation of machine operations in case of safety hazards or emergencies, ensuring operator well-being.
14. Dust and Chip Collection System
- Function: Removes chips, debris, and dust generated during machining, maintaining a clean work environment and preventing tool damage.
CNC Programming and Its Role in Guiding Machine Movements
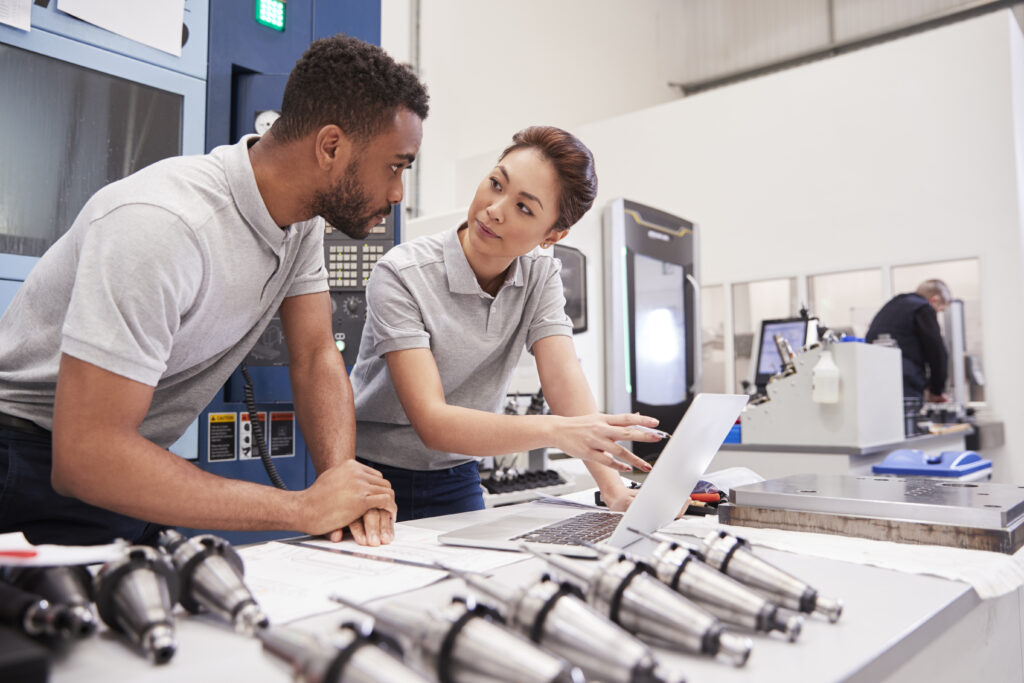
CNC programming is the vital process of creating a set of instructions that guide a CNC machine’s movements and actions during machining operations. These instructions are meticulously crafted to ensure precise tool paths, accurate dimensions, and desired surface finishes in the final product. The heart of CNC programming lies in translating a digital design into a language that the machine comprehends, allowing it to execute the intended operations flawlessly.
The concept of CNC programming involves using a programming language known as G-code. G-code comprises a series of alphanumeric codes that represent various commands, such as tool movement, spindle speed, feed rate, and tool changes. Each code corresponds to a specific action that the CNC machine must perform. For instance, G01 indicates a linear interpolation for controlled movement along a straight line, while M03 commands the spindle to start rotating clockwise.
CNC programming’s role is pivotal in manufacturing precision components. The programmer defines the sequence of operations, tool changes, and the exact path the tool must follow to shape the workpiece. The accuracy and intricacy of the final product are heavily reliant on the programmer’s expertise in crafting the correct G-code instructions. CNC programming bridges the gap between a designer’s vision and the machine’s execution, enabling the transformation of digital designs into tangible, precisely machined parts.
Types of CNC Machining Processes
Types of CNC Machining Processes:
- Milling:
- Rotate cutting tools to shape workpieces, creating complex profiles.
- Turning:
- Rotate the workpiece while cutting the tool shapes cylindrical parts.
- Drilling:
- Create holes using rotating cutting tools.
- Grinding:
- Achieve precise surface finishes with abrasive wheels.
- EDM (Electrical Discharge Machining):
- Use controlled electrical discharges to shape conductive materials.
- Laser Cutting:
- Employ lasers to cut intricate shapes in various materials.
- Waterjet Cutting:
- Use high-pressure water mixed with abrasives to cut materials.
- Plasma Cutting:
- Employ ionized gas and electrical arc to cut conductive materials.
- Wire EDM:
- Use thin electrically conductive wire to cut complex shapes.
- 5-Axis Machining:
- Simultaneously move tools along multiple axes for intricate geometries.
These processes encompass a range of techniques, each tailored to specific needs, enabling versatile and precise manufacturing across industries.
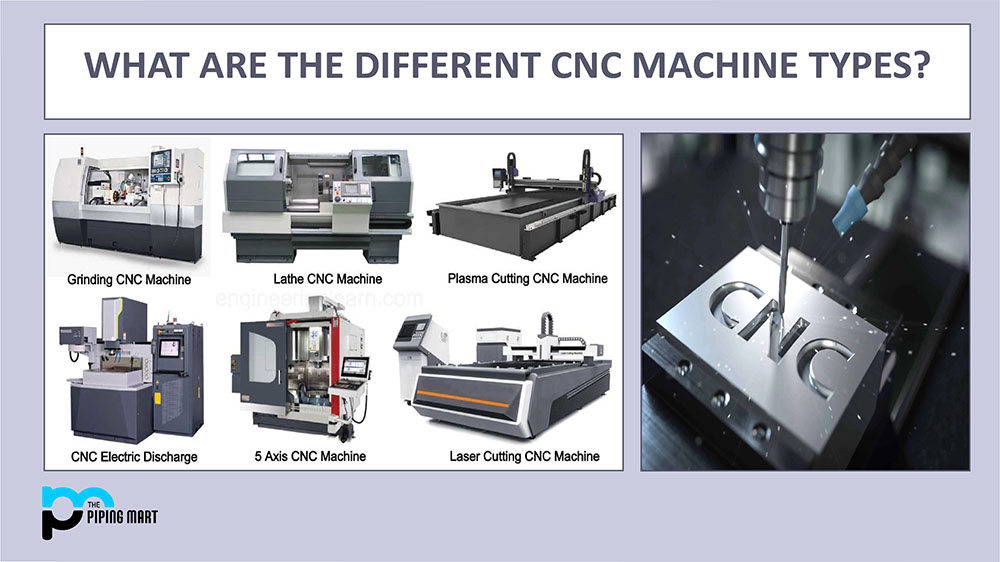
Workflow of CNC Machining
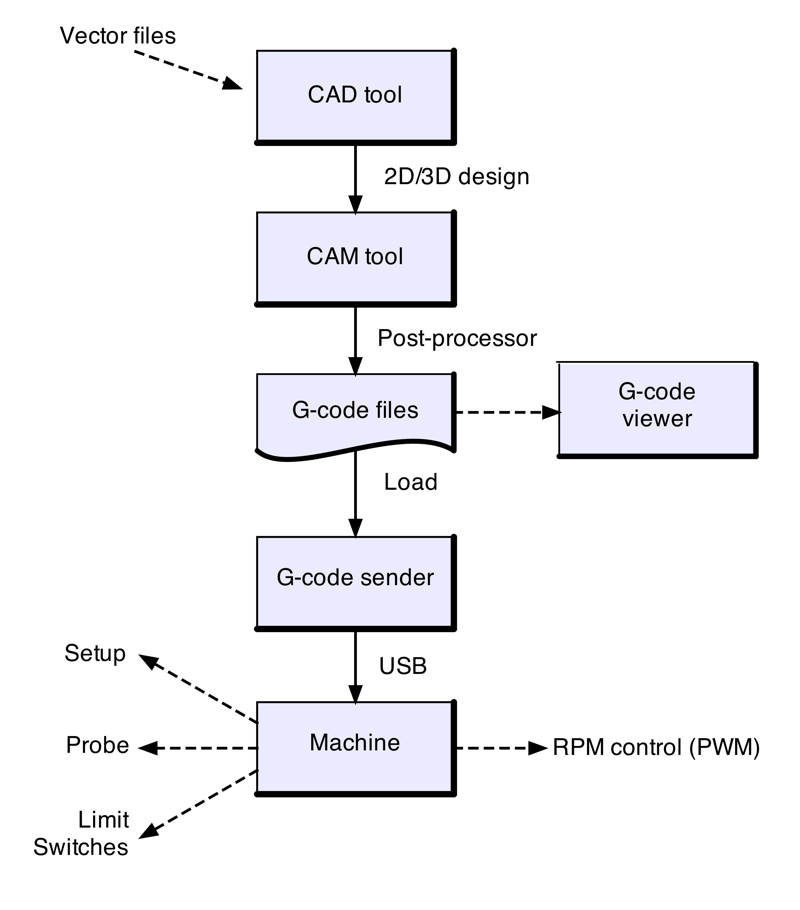
Workflow of CNC Machining –
- Design Creation:
- Develop digital design using CAD software.
- CAD to CAM Conversion:
- Transform CAD design into machine-readable CAM instructions.
- Programming:
- Generate G-code commands for tool paths, speeds, and operations.
- Machine Setup:
- Secure the workpiece on the machine’s worktable, and load tools.
- Loading G-code:
- Transfer the G-code program to the machine’s controller.
- Tool Calibration:
- Set reference points, and calibrate tools for accuracy.
- Machining Operations:
- Execute programmed tool paths and shape workpieces.
- Quality Control:
- Inspect and measure workpieces for accuracy.
- Tool Changes (if needed):
- Swap tools for different machining steps.
- Finishing Operations:
- Deburring, polishing for the final touch.
- Completion and Unloading:
- Remove the finished workpiece from the machine.
- Post-Processing:
- Clean, inspect, and apply treatments if necessary.
CNC machining’s systematic workflow ensures precision and efficiency in translating digital designs into tangible components.
Role of Precision in CNC Machining
Precision in CNC machining is paramount as it ensures consistent, accurate, and repeatable results. High precision guarantees that manufactured components meet exact specifications, fit together seamlessly, and perform optimally. It reduces material waste, enhances product quality, and minimizes the need for manual adjustments. Precision in tool paths, measurements, and tolerances results in parts that function flawlessly, enabling industries to meet demanding standards, achieve tight tolerances, and produce intricate designs that were once unattainable.
Factors Influencing CNC Machining
Factors Influencing CNC Machining –
- Tool Selection:
- Choose appropriate tools for the material and operation to ensure efficient cutting and prolong tool life.
- Cutting Speed:
- Optimize cutting speed based on material properties to balance efficiency and tool wear.
- Feed Rates:
- Adjust feed rates to control material removal rates and prevent excessive tool wear.
- Depth of Cut:
- Select the depth of cut to balance material removal and tool stability, avoiding tool breakage.
- Coolant Usage:
- Use coolant to dissipate heat, prolong tool life, and improve surface finish.
- Material Properties:
- Consider material hardness, brittleness, and thermal conductivity when selecting cutting parameters.
- Machine Rigidity:
- Ensure machine stability to prevent vibrations and maintain accurate cuts.
- Tool Wear Monitoring:
- Implement systems to monitor tool wear and replace tools at optimal times.
- Fixture Design:
- Design proper workpiece fixtures to secure components for accurate machining.
- Operator Skill:
- Trained operators ensure proper setup, programming, and monitoring for successful machining.
Balancing these factors leads to efficient, precise, and cost-effective CNC machining processes.
Benefits of CNC Machining
Benefits of CNC Machining –
- Precision:
- Achieve consistent and accurate results, meeting tight tolerances.
- Efficiency:
- Reduce manual intervention, increase production speed, and minimize waste.
- Complex Geometries:
- Craft intricate designs and shapes that manual methods can’t replicate.
- Repeatability:
- Reproduce identical parts with high consistency for large-scale production.
- Automation:
- Minimize human error and enhance operator safety through automated processes.
- Versatility:
- Handle various materials and operations with appropriate tooling and programming.
- Cost-Effectiveness:
- Lower production costs through reduced labor, material waste, and rework.
- Customization:
- Tailor designs and outputs to specific requirements for diverse applications.
- Shorter Lead Times:
- Accelerate time-to-market by streamlining design-to-production cycles.
- Innovation:
- Embrace advanced techniques and technologies for continuous improvement.
The benefits of CNC machining revolutionize manufacturing across industries, delivering accuracy, efficiency, and versatility.
Limitations and Challenges of CNC Machining
- Initial Setup Time:
- Time-consuming setup involving tool changes, workpiece fixturing, and programming.
- Programming Complexity:
- Requires skilled programmers to generate precise and optimized G-code instructions.
- High Initial Investment:
- CNC machines and training demand substantial upfront costs.
- Material Restrictions:
- Limited to machinable materials; certain materials can pose challenges.
- Tool Wear and Maintenance:
- Tools degrade over time, requiring replacements and maintenance.
- Operator Skill:
- Skilled operators are needed for proper setup, programming, and monitoring.
- Limited Accessibility:
- Difficulty in reaching tight spaces or complex geometries.
- Surface Finish:
- Achieving desired surface finishes can be challenging, requiring additional processes.
- Complexity of Parts:
- Extremely intricate designs might be challenging or time-consuming to machine.
- Risk of Error:
- Human errors in programming or setup can lead to flawed parts.
Understanding these limitations helps industries make informed decisions regarding CNC machining for optimal outcomes.
Future Trends and Innovations of CNC Machining
- Hybrid Machining:
- Integration of additive manufacturing with CNC for complex, multi-material parts.
- IoT Integration:
- Connecting CNC machines for real-time monitoring, predictive maintenance, and data analysis.
- 5G Connectivity:
- High-speed connectivity enables remote control, monitoring, and collaboration.
- AI-Assisted Machining:
- AI algorithms optimize tool paths, predict tool wear, and enhance efficiency.
- Smart Factories:
- Fully automated, interconnected production facilities for seamless manufacturing.
- Nanotechnology Applications:
- Micro-scale machining for electronics, medical devices, and high-precision components.
- Green Machining:
- Energy-efficient processes and sustainable materials for reduced environmental impact.
- Advanced Materials:
- Machining high-performance materials like composites, ceramics, and superalloys.
- Miniaturization:
- Precision machining for miniaturized components in electronics and medical fields.
- Customization on Demand:
- Rapid production of bespoke parts with quick design-to-production cycles.
Embracing these trends will redefine CNC machining, enhancing efficiency, precision, and adaptability across industries.
Conclusion
In conclusion, CNC machining stands as an indispensable cornerstone of modern manufacturing. Its precision, efficiency, and ability to realize intricate designs have propelled industries to new heights. As technology evolves, embracing advancements like AI, hybrid processes, and IoT integration, CNC machining’s potential only expands. It continues to shape the landscape of innovation, pushing boundaries and ensuring that the future of manufacturing remains precise, efficient, and at the forefront of technological progress.
FAQ’s
What is CNC full form?
Computer Numerical Control.
Why is CNC used?
CNC (Computer Numerical Control) is used for its precision and automation. It ensures accurate, consistent, and complex manufacturing by using programmed instructions to control machinery, reducing human error, increasing efficiency, and enabling the production of intricate components across various industries.
What is the CNC Machining Process?
CNC machining is a precise manufacturing process where computer-controlled machines remove material from a workpiece to create intricate parts. It involves programming tools to follow specific paths, resulting in accurate and consistent results. This automated process revolutionizes manufacturing by enabling complex shapes, high precision, and efficient production across diverse industries.
What are the types of CNC machines?
There are several types of CNC machines, each specialized for specific tasks –
CNC Milling Machines:
Use rotating cutting tools to remove material from a workpiece to make complex shapes.
CNC Turning Machines:
Rotate workpieces while cutting tools shape cylindrical parts like shafts or bolts.
CNC Drilling Machines:
Create holes in workpieces using rotating cutting tools.
CNC Grinding Machines:
Achieve precise surface finishes using abrasive wheels.
CNC EDM Machines (Electrical Discharge Machining):
Use controlled electrical discharges to shape conductive materials.
CNC Laser Cutting Machines:
Employ high-energy lasers to cut intricate shapes in various materials.
CNC Waterjet Cutting Machines:
Use high-pressure water mixed with abrasives to cut materials.
CNC Plasma Cutting Machines:
Employ ionized gas and an electrical arc to cut conductive materials.
Wire EDM Machines:
Use a thin electrically conductive wire to cut complex shapes.
5-Axis CNC Machines:
Simultaneously move tools along multiple axes, enabling intricate geometries.
Each type serves specific manufacturing needs, offering versatility and precision in creating a wide range of components.
Explain the working principle of the CNC Machine.
The working principle of a CNC (Computer Numerical Control) machine involves precise automation –
A computer generates a program with instructions (G-code) for tool paths, speeds, and operations.
These instructions are fed into the machine’s controller.
Servo motors move machine components along different axes according to the G-code.
Cutting tools remove material from the workpiece based on programmed paths.
The result is accurate, repeatable, and automated manufacturing, revolutionizing precision production.
CNC Machine Basic Knowledge
A CNC (Computer Numerical Control) machine is an automated manufacturing tool that follows programmed instructions to create precise parts. It uses G-code, a programming language, to guide the machine’s movements and tool actions. CNC machines come in various types, like mills, lathes, and routers, each tailored to specific tasks. They offer accuracy, efficiency, and versatility, enabling complex shapes and consistent production. CNC technology revolutionizes manufacturing by minimizing human error, increasing speed, and producing intricate components across industries.
What is the CNC Machining rate per hour in India?
The hourly rates for CNC machining services in India can vary widely based on several factors. Here’s a rough range to provide you with a general idea –
Basic CNC machining: ₹300 to ₹800 per hour.
Intermediate CNC machining: ₹800 to ₹1500 per hour.
Advanced CNC machining (complex parts, precision work): ₹1500 to ₹3000+ per hour.
Please note that these rates are approximate and can vary based on location, machine type, material, complexity, provider expertise, and market conditions.
It’s advisable to obtain quotes from local machining services for the most accurate and up-to-date pricing information.
CNC Machining Vs Injection Molding
CNC Machining vs Injection Molding –
CNC Machining:
Process:
Material is removed from a solid block using rotating cutting tools to create the desired shape.
Material:
Works well with various materials, including metals, plastics, and composites.
Complexity:
Ideal for complex geometries, prototypes, and low-volume production.
Tooling:
Minimal tooling is required, making it cost-effective for small quantities.
Setup Time:
Setup can be time-consuming, affecting production speed for intricate parts.
Lead Time:
Generally shorter lead times due to minimal tooling and setup requirements.
Precision:
Offers high precision and accuracy, suitable for tight tolerances.
Injection Molding:
Process:
The molten material is injected into a mold, cooled, and solidified to produce the final shape.
Material:
Primarily used with thermoplastic and thermosetting polymers.
Complexity:
Suited for high-volume production of complex parts with consistent quality.
Tooling:
Initial tooling costs can be high but cost-effective for large production runs.
Setup Time:
Longer setup time due to mold preparation and material melting.
Lead Time:
Longer lead times for tooling design, fabrication, and adjustments.
Precision:
Offers good precision, but tight tolerances may require more advanced techniques.
Both CNC machining and injection molding have their advantages and are chosen based on factors like production volume, part complexity, material, and cost considerations.
Platform of CNC Machine for Sale
CNC Machine Sales Platforms
Online platforms provide a convenient way to buy and sell CNC machines. Popular platforms include –
Machinery Marketplaces:
Websites like “Machinio,” “MachineTools.com” list a variety of CNC machines for sale.
Auction Sites:
“eBay” and “EquipNet” offer auctions for new and used CNC machines.
Manufacturer Websites:
CNC manufacturers often have dedicated sales sections on their websites.
Specialized Forums:
Industry-specific forums like “CNCZone” have classified sections for machine sales.
Local Classifieds:
Websites like “Craigslist” or “OLX” may have listings for used CNC machines.
Buyers should thoroughly research the machine’s condition, specifications, and the credibility of the seller before making a purchase.