Introduction
In the dynamic world of manufacturing, where precision and efficiency are paramount, even the smallest details hold significant importance. Enter mold shot counters, unassuming yet vital components that play a crucial role in monitoring injection molding processes. Beyond mere numerical tracking, these counters provide insights that enhance maintenance schedules, optimize production, and elevate overall operational performance. This introduction delves into the fundamental role and hidden potential of mold shot counters, shedding light on their pivotal position in modern manufacturing processes.

Unveiling the Hidden Benefits of Mold Shot Counters
In the intricate dance of manufacturing, where every movement matters, it’s the seemingly minor players that often wield the most influence. Among these unsung heroes is the mold shot counter—a device that transcends its numeric function to reveal a treasure trove of concealed advantages that elevate the entire production process.
1. Proactive Maintenance Insights: Beyond mere shot tallies, modern mold shot counters provide a window into the health of molds. They help foresee maintenance needs by tracking shot numbers, reducing unplanned downtime, and ensuring molds are in peak condition.
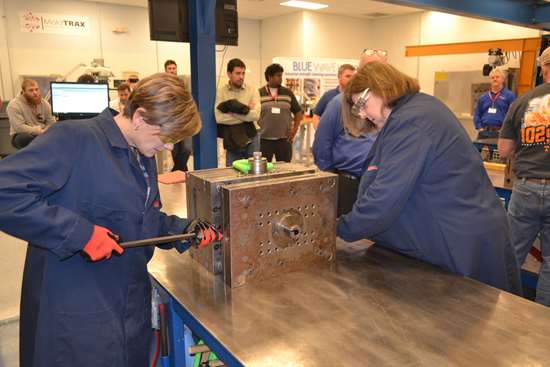
2. Informed Decision-Making: The data-rich capabilities of shot counters allow for informed decision-making. Analysis of production trends empowers manufacturers to optimize schedules, allocate resources effectively, and bolster the overall operational strategy.
3. Crystal Ball of Maintenance: Enter predictive algorithms. Some shot counters delve into historical data to predict maintenance requirements. This proactive approach minimizes disruptions, ensuring continuous operations.
4. Process Finesse: Accurate shot counting isn’t just a numbers game; it’s a key to fine-tuning production processes. By aligning shot count data with output, manufacturers can fine-tune cycle times, minimize material wastage, and enhance energy efficiency.
5. Quality in Every Count: Regular maintenance prompted by shot counters directly translates to consistent product quality. The interplay of optimized processes and well-maintained molds leads to fewer defects and greater uniformity in the final product.
6. Orchestrating the Workforce: Efficient production relies on an orchestra of skilled personnel. Shot counters offer a tangible metric for productivity. Incentivizing operators based on shot counts cultivates a culture of efficient performance.
7. Inventory IQ: Optimal inventory management hinges on predicting needs. With shot counters anticipating component replacements, manufacturers can ensure timely stock availability and keep operations flowing seamlessly.
8. Paving the Road to Savings: The symbiotic relationship between well-maintained molds and streamlined processes directly slashes waste and energy consumption. Cost savings emerge as a natural byproduct of this synergy.
9. Illuminating Process Trails: Shot counters bestow a cloak of traceability upon production. For industries with regulatory demands, like medical or automotive, this transparency is invaluable for compliance and quality control.
10. Compliance Chronicles: In a regulatory landscape, accurate shot counting isn’t just an advantage—it’s a necessity. Shot counters provide a credible record, attesting to adherence to predefined standards and specifications.
In summation, the mold shot counter transcends its numeric facade to reveal an arsenal of strategic advantages. From predictive maintenance to quality control, this unassuming device holds the key to operational finesse. Embracing the latent potential of mold shot counters transforms them from humble counters into strategic partners, driving the manufacturing journey toward precision, efficiency, and excellence.
Real-World Examples of Mold Shot Counters in Action
- Automotive Manufacturing: In an automotive plant, mold shot counters monitor the production of plastic components for vehicle interiors. By tracking shot counts, manufacturers predict maintenance needs, reducing downtime and ensuring consistent product quality in critical components like dashboards and door panels.
- Medical Device Production: In medical device manufacturing, precision is paramount. Mold shot counters ensure that injection-molded components for medical devices are produced with accuracy. Regular maintenance prompted by shot counts guarantees adherence to strict quality standards and regulations.
- Consumer Electronics: In the production of consumer electronics, mold shot counters optimize efficiency. For instance, in making smartphone casings, shot counters facilitate process adjustments, reducing cycle times and minimizing material waste to create sleek, consistent products.
- Packaging Industry: In packaging facilities, mold shot counters contribute to efficient operations. They assist in producing consistent packaging materials by ensuring that injection-molded components, such as caps and containers, are accurately manufactured within specified shot counts.
- Appliance Manufacturing: Mold shot counters play a vital role in producing components for household appliances. They guide maintenance schedules for molds used in manufacturing items like refrigerator shelves, ensuring durability and uniformity in the final products.
- Toy Production: In the toy industry, mold shot counters to aid in the creation of safe and reliable products. By monitoring shot counts, manufacturers maintain the integrity of plastic components, like toy parts, and prevent potential defects.
- Industrial Equipment: In manufacturing heavy machinery, mold shot counters offer predictive maintenance insights. Manufacturers use shot count data to schedule maintenance for molds producing parts critical to industrial equipment, minimizing downtime and optimizing performance.
- Furniture Manufacturing: In the furniture industry, mold shot counters contribute to efficient production. Manufacturers use them to ensure consistent quality in components like chair seats or table legs, enhancing the overall appeal and durability of products.
- Beverage Industry: Mold shot counters are essential for producing accurate and uniform bottle caps or closures in the beverage industry. By tracking shot counts, manufacturers ensure proper sealing and prevent leakage issues in packaging.
- Building Materials Production: Mold shot counters are valuable in manufacturing construction materials. They help maintain precision in producing components such as plastic pipes or fittings, contributing to the durability and reliability of these materials.
These real-world examples showcase how mold shot counters silently but significantly impact various industries, ensuring quality, efficiency, and compliance across the production spectrum.
Maximizing Hidden Benefits
Maximizing the hidden benefits of mold shot counters involves a strategic approach that goes beyond basic shot counting. Here’s how to make the most of these valuable tools –
- Advanced Analytics: Embrace shot counters with data analysis capabilities. Leverage the insights they provide to identify trends, patterns, and correlations in production data. This information can guide decisions for process optimization and predictive maintenance.
- Predictive Maintenance Implementation: If your shot counters offer predictive algorithms, implement them effectively. Utilize historical data to create predictive models that forecast maintenance needs. Proactively schedule maintenance based on these predictions to minimize downtime.
- Integration with Maintenance Software: Integrate shot counters with your maintenance management software. This enables automated maintenance scheduling, work order generation, and real-time notifications for upcoming maintenance tasks.
- Cross-functional collaboration: Foster collaboration between production, maintenance, and data analysis teams. Sharing insights from shot counters ensures that decisions are data-driven and align with broader operational goals.
- Process Parameter Optimization: Correlate shot count data with other process parameters like cycle time, material usage, and energy consumption. Analyze how changes in one parameter affect shot counts and overall production efficiency.
- Performance Benchmarking: Establish shot count benchmarks for different molds and products. Regularly compare actual shot counts to these benchmarks to identify anomalies, optimize mold performance, and detect potential issues.
- Operator Training and Engagement: Educate operators about the significance of shot counting and how it impacts overall production. Incentivize operators to maintain accurate records and report deviations promptly.
- Root Cause Analysis: When shot counts deviate unexpectedly, conduct root cause analysis. Investigate whether process changes, material variations or other factors contribute to the deviation and take corrective actions.
- Continuous Improvement Initiatives: Incorporate shot count data into your continuous improvement initiatives. Regularly review production data and shot count trends to identify areas for enhancement in terms of efficiency, quality, and maintenance practices.
- Feedback Loop for Design Improvement: Utilize shot count data to provide feedback to design and engineering teams. Insights gained from shot counters can help refine mold designs and optimize mold longevity.
- Regular Training and Upgradation: Keep your team updated on the latest features and capabilities of your shot counters. Regular training ensures that the full potential of these devices is leveraged for continuous improvement.
By adopting these strategies, you can transform your mold shot counters from mere counters into strategic assets that drive efficiency, quality, and long-term success in your manufacturing operations.
Maker/Supplier of Shot Counters
10 Maker/Supplier of Shot Counters are –
- Omron India
- Autonics India
- B&R Industrial Automation
- Renu Electronics
- Multispan Instruments Company
- Shubh Instruments
- Sree Vasavi Traders
- Perceptive Engineering
- Vijay Systems Engineers Pvt Ltd
- Technotronics Control System
These companies specialize in industrial automation components and solutions, including shot counters. To ensure accurate and current information, I recommend contacting them directly or visiting their official websites.
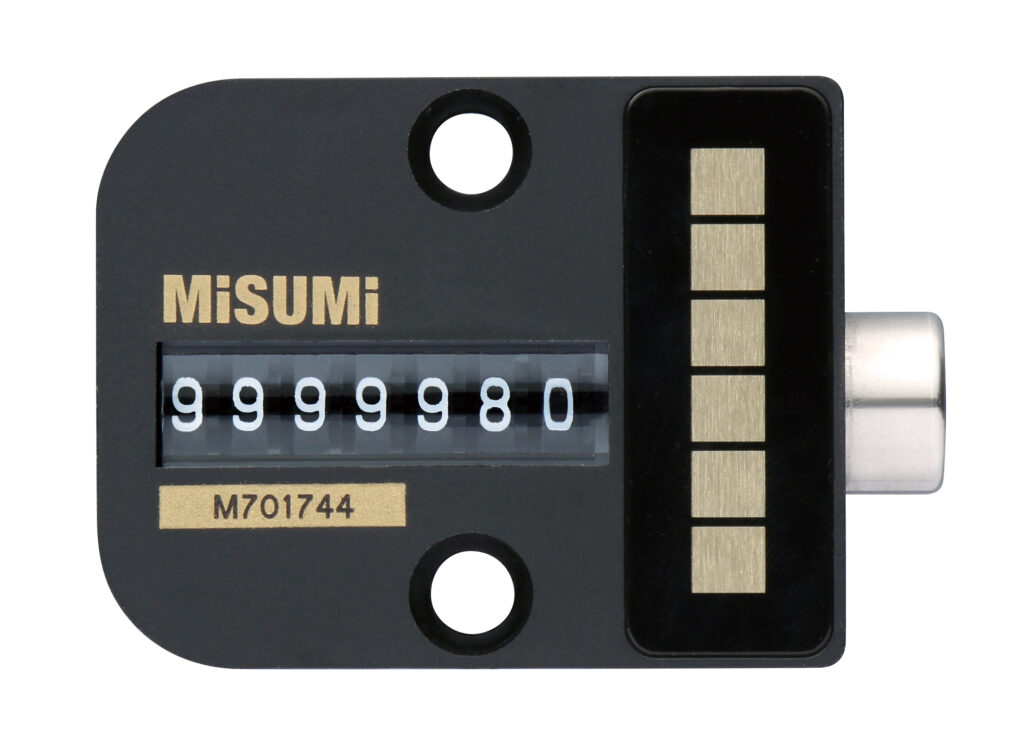
Future Possibilities of Mold Shot Counters: A Glimpse Ahead
Looking ahead, the future possibilities of mold shot counters are poised to revolutionize manufacturing processes, ushering in enhanced efficiency, precision, and data-driven decision-making. Here are some future scenarios to consider –
- Advanced Predictive Analytics: Mold shot counters will refine predictive analytics, foreseeing maintenance needs, and production bottlenecks for proactive solutions.
- AI and Machine Learning: Integration of AI and machine learning will enhance accuracy and adaptability, learning from data and adjusting to changing conditions.
- Real-time Monitoring: Shot counters will offer real-time alerts, notifying operators and maintenance teams instantly about issues or deviations.
- Industry 4.0 Integration: Mold shot counters will seamlessly connect within Industry 4.0, sharing data and collaborating with other equipment for comprehensive optimization.
- Remote Control: Remote monitoring and control will become feasible, facilitating prompt decisions and troubleshooting without physical presence.
- Enhanced Customization: Manufacturers will personalize shot counters to match their unique needs, setting maintenance thresholds and benchmarks.
- Digital Twin Integration: Shot counters will partner with digital twin simulations, refining processes through virtual replicas of molds and equipment.
- Supply Chain Efficiency: Predictive maintenance by shot counters will optimize supply chains, streamlining spare parts availability and reducing downtime.
- Energy Insights: Shot counters will correlate shot count data with energy consumption patterns, enabling cost-effective energy management.
- Continuous Learning: Shot counters will adapt and learn over time, gaining accuracy and insights from diverse scenarios for smarter predictions.
The future of mold shot counters holds a promise of smarter, more connected manufacturing processes, powered by predictive capabilities, digital integration, and data-driven decision-making.
Conclusion: Harnessing Precision and Insight with Mold Shot Counters
In the realm of modern manufacturing, precision, and efficiency reign supreme, and hidden beneath the surface of seemingly straightforward tools lies a powerhouse of benefits—enter the mold shot counters. These unassuming devices extend far beyond mere shot tallying, becoming conduits for predictive insights, informed decision-making, and enhanced production optimization.
As we’ve explored the diverse realms of maintenance, data analytics, process refinement, and beyond, it’s evident that mold shot counters play a pivotal role in shaping the future of manufacturing. They have evolved from basic counters to sophisticated instruments that not only streamline operations but also empower manufacturers to anticipate challenges and capitalize on opportunities.
The journey of mold shot counters transcends their numerical essence, leading us into an era where every shot count carries the potential for innovation. With technology advancing at an unprecedented pace, these counters promise to unlock new dimensions of efficiency, quality, and predictive capabilities. By embracing their hidden potential and harnessing the insights they offer, manufacturers can journey confidently into a future of manufacturing excellence, where precision and productivity intertwine seamlessly.
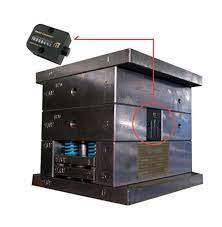
FAQ’s
What is the Use of Shot Counters in Mold?
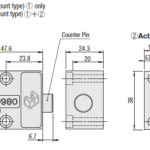
Shot counters in molds serve a crucial role in injection molding processes by accurately tracking the number of shots or cycles completed. This numerical tracking offers several important uses and benefits –
Maintenance Scheduling: Shot counters help manufacturers predict when molds will require maintenance. By monitoring the number of shots produced, manufacturers can proactively schedule maintenance to prevent unexpected breakdowns and production stoppages.
Optimized Mold Life: Regular maintenance based on shot counts prolongs the life of molds. This ensures that molds remain in good condition, producing consistent and high-quality parts over an extended period.
Quality Control: Shot counters contribute to maintaining consistent product quality. Regular maintenance prevents degradation of molds, reducing the likelihood of defects and variations in the final product.
Efficiency and Downtime Reduction: Proactive maintenance based on shot counts minimizes unplanned downtime. Manufacturers can schedule maintenance during planned downtimes, optimizing overall production efficiency.
Process Optimization: By correlating shot count data with production parameters, manufacturers can optimize cycle times, material usage, and energy consumption, resulting in more efficient and cost-effective production.
Preventing Catastrophic Failures: Early detection of potential issues through shot counts can prevent catastrophic mold failures that could lead to extensive downtime and costly repairs.
Inventory Management: Accurate shot counting aids in managing spare parts inventory. Manufacturers can anticipate when specific components might require replacement and ensure the availability of necessary parts.
Data-Driven Decisions: Shot count data provides insights into mold performance and wear. Manufacturers can make data-driven decisions regarding maintenance, replacement, and process adjustments.
Regulatory Compliance: In industries with regulatory standards, shot counters offer a documented history of mold usage, maintenance, and adherence to production requirements.
Cost Savings: Regular maintenance prompted by shot counters reduces the need for emergency repairs and replacements. This leads to cost savings over the long term and improves return on investment for molds.
In essence, shot counters are essential tools that help manufacturers maintain molds, optimize production processes, and ensure consistent product quality, contributing to overall operational efficiency and success.
What are Digital Shot Counters?
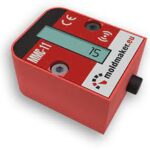
Digital shot counters are modern electronic devices designed to accurately track and display the number of shots or cycles completed in manufacturing processes, particularly in injection molding. These counters use digital technology to provide real-time monitoring and data recording, offering several advantages over traditional mechanical shot counters –
Precision and Accuracy: Digital shot counters provide highly accurate counting, minimizing the potential for errors associated with manual counting or mechanical counters.
Real-time Monitoring: These counters offer real-time tracking of shot counts, enabling operators and maintenance teams to have up-to-date information about production progress and maintenance requirements.
Data Recording: Digital shot counters often come equipped with data logging capabilities. This allows manufacturers to record shot count data over time and analyze trends for optimization purposes.
Remote Access: Some digital shot counters can be accessed remotely through connected devices. This enables operators and supervisors to monitor shot counts and production progress from a distance.
Integration with Automation: Digital shot counters can be seamlessly integrated with automation systems and manufacturing software, enabling data sharing, process optimization, and predictive maintenance.
Alerts and Notifications: Many digital shot counters can send alerts and notifications when predefined shot count thresholds are reached. This helps operators and maintenance teams stay proactive in scheduling maintenance.
Data Analysis: With data logging capabilities, manufacturers can analyze shot count data to identify patterns, production trends, and areas for improvement.
User-Friendly Interface: Digital shot counters often feature user-friendly interfaces with clear displays and easy-to-read digital readouts, making it simpler for operators to monitor shot counts.
Predictive Maintenance: Some advanced digital shot counters utilize predictive algorithms to forecast when maintenance will be needed based on historical data. This helps prevent unplanned downtime.
Reporting and Documentation: Digital shot counters provide accurate and detailed records of shot counts, making it easier to comply with regulatory requirements and quality control standards.
Digital shot counters are an integral part of modern manufacturing, offering greater accuracy, real-time monitoring, and data-driven insights that contribute to efficient production processes, quality assurance, and optimized maintenance schedules.