In the world of manufacturing, molds are indispensable tools used for shaping various materials into precise parts and products. However, like any equipment, molds are subject to wear and tear, leading to occasional breakdowns. To minimize downtime and optimize mold performance, maintenance strategies are vital. In this article, we will delve into key maintenance metrics: MTBF, MTTR, MTTA, and MTTF, and explore their significance in the context of mold breakdown maintenance.
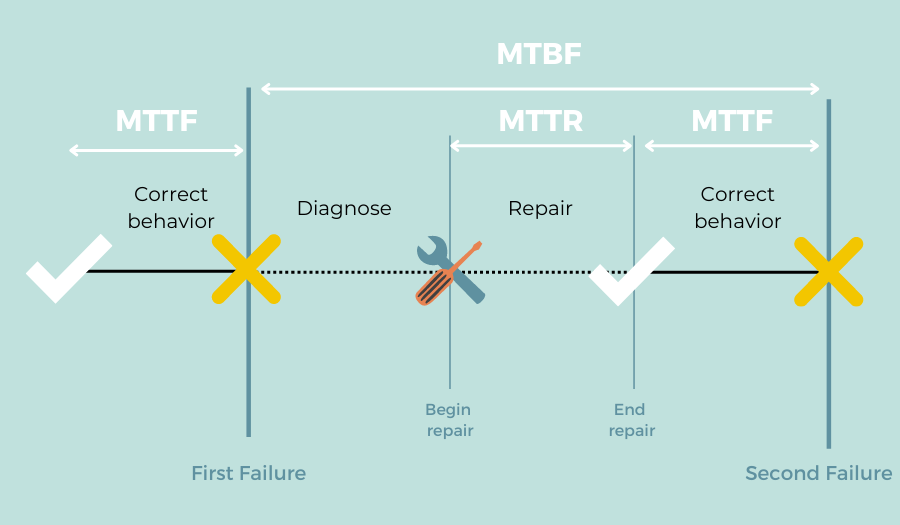
Understanding the Acronyms
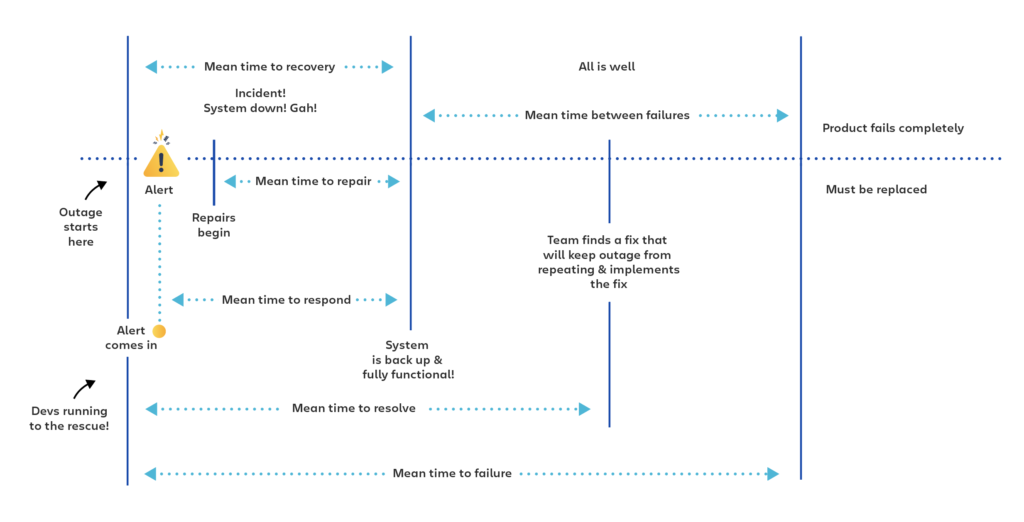
1. MTBF (Mean Time Between Failures)
MTBF is a metric that calculates the average time between one breakdown or failure of a mold and the next. It quantifies the reliability of the mold, indicating how often it typically requires maintenance.
2. MTTR (Mean Time To Repair)
MTTR measures the average time taken to repair a mold after a breakdown. It reflects the efficiency of maintenance and repair processes.
3. MTTA (Mean Time To Acknowledge)
MTTA represents the time taken to acknowledge the occurrence of a mold breakdown. It’s a crucial metric for identifying issues promptly and initiating repairs.
4. MTTF (Mean Time To Failure)
MTTF estimates the average time a mold operates before experiencing a failure. It is often used to predict the mold’s lifespan and plan maintenance activities.
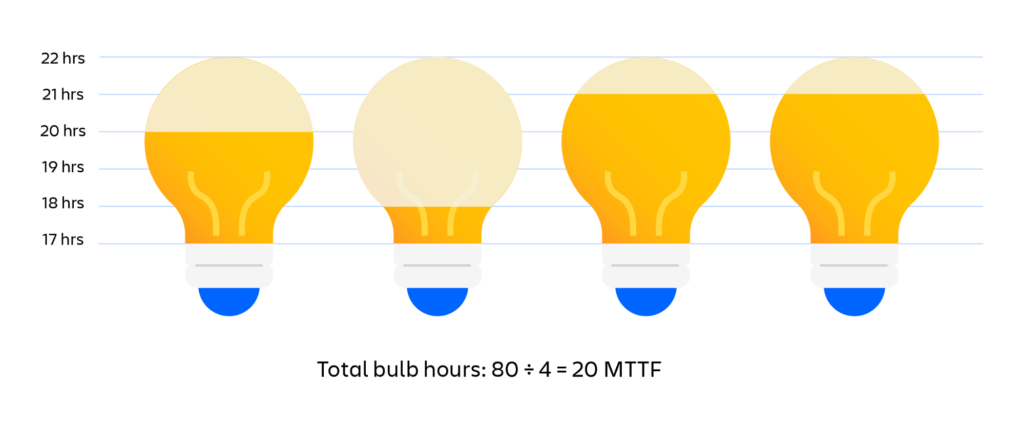
Significance of MTBF
MTBF is a pivotal metric for assessing mold reliability. A high MTBF value suggests that a mold has a long operational life between failures, translating to reduced production interruptions. To maximize MTBF for molds, regular preventive maintenance, quality material inputs, and optimal operating conditions are essential. By extending the time between breakdowns, manufacturers can increase productivity and reduce overall maintenance costs.
Streamlining MTTR
Efficient mold maintenance is the key to minimizing downtime. A lower MTTR indicates that molds can be repaired quickly, ensuring a swift return to production. To streamline MTTR, manufacturers can invest in well-organized maintenance teams, easy access to spare parts, and well-documented maintenance procedures. Reducing the time needed for repairs is critical in fast-paced manufacturing environments.
Rapid Response with MTTA
The MTTA metric emphasizes the importance of a quick response to mold breakdowns. A shorter MTTA ensures that issues are acknowledged promptly, enabling faster repair actions. Implementing effective communication channels, automated monitoring systems, and a well-trained workforce can contribute to reducing MTTA, thus minimizing production disruptions.
Predicting Mold Lifespan with MTTF
MTTF provides insights into a mold’s expected lifespan. By analyzing MTTF data, manufacturers can plan for mold replacement or major maintenance activities, preventing unexpected breakdowns. Accurate predictions based on MTTF enable proactive maintenance strategies, reducing unplanned downtime and production losses.
Integration for Enhanced Maintenance
Integrating these metrics into a comprehensive maintenance strategy is essential for maintaining mold reliability. A well-rounded approach involves –
- Preventive Maintenance: Regularly scheduled maintenance tasks can extend the MTBF by addressing potential issues before they cause breakdowns.
- Predictive Maintenance: Utilizing data and technology, manufacturers can predict mold failures with greater accuracy, enhancing MTTF estimations.
- Quick Response: Efficient maintenance teams and processes are key to minimizing MTTR and MTTA, ensuring rapid mold repair.
- Continuous Improvement: Regularly reviewing these metrics and refining maintenance strategies based on historical data can lead to ongoing efficiency gains.
Limitation & Implication of MTTR, MTBF, MTTA & MTTF
While MTBF, MTTR, MTTA, and MTTF are valuable metrics for evaluating equipment reliability and maintenance efficiency, they also have certain limitations. It’s important to be aware of these limitations to use the metrics effectively and to complement them with additional information when necessary –
1. Lack of Context
- Limitation: MTBF, MTTR, MTTA, and MTTF do not provide context about the specific nature of failures or repairs.
- Implication: These metrics do not distinguish between minor, non-critical failures and catastrophic ones. It’s essential to combine these metrics with qualitative data to assess the severity of failures.
2. Sensitivity to Data Quality
- Limitation: These metrics are sensitive to the quality and accuracy of data. Inaccurate or incomplete data can lead to misleading results.
- Implication: Organizations must maintain accurate records of failures, repairs, and acknowledgment times to ensure the reliability of these metrics.
3. Ignores Repair Time Variability
- Limitation: MTTR considers the average repair time but does not account for the variability in repair times.
- Implication: Variability can lead to significant disruptions, so organizations should analyze the distribution of repair times to better understand maintenance efficiency.
4. Fails to Consider Human Factors
- Limitation: These metrics do not consider the impact of human factors in maintenance and acknowledgment times.
- Implication: Human factors, such as technician experience and training, can significantly influence maintenance efficiency. These factors should be considered alongside the metrics.
5. Limited Predictive Power
- Limitation: MTTF provides an estimate of equipment lifespan but does not account for unpredictable or abrupt failures.
- Implication: Relying solely on MTTF may not be sufficient to predict all failures, so organizations should use predictive maintenance methods that consider various failure modes.
6. Difficulty with Complex Systems
- Limitation: These metrics are less applicable to complex systems with multiple components and interdependencies.
- Implication: Complex systems often require more sophisticated reliability analysis methods, such as Fault Tree Analysis or Failure Modes and Effects Analysis (FMEA).
7. Does Not Consider Aging Effects
- Limitation: MTTF and MTBF may not accurately represent equipment aging effects over time.
- Implication: Organizations may need to incorporate aging and wear-and-tear considerations when planning maintenance for aging equipment.
8. Limited Scope
- Limitation: These metrics primarily focus on equipment reliability and maintenance and do not account for broader operational factors.
- Implication: Organizations should consider a wider range of operational, environmental, and business-related factors when making strategic decisions.
Conclusion
In the competitive manufacturing landscape, molds are essential assets. Understanding and optimizing maintenance metrics such as MTBF, MTTR, MTTA, and MTTF can significantly impact production efficiency and reduce costs associated with mold breakdowns. By implementing a well-rounded maintenance strategy that combines preventive, predictive, and responsive approaches, manufacturers can achieve higher mold reliability, increased production uptime, and ultimately, a competitive edge in the industry.
Frequently Asked Questions
What is MTBF, and why is it important in maintenance?
MTBF stands for Mean Time Between Failures. It is a measure of equipment reliability, indicating the average time between one failure or breakdown and the next. MTBF is crucial in maintenance because it helps organizations assess the reliability of their equipment and plan maintenance activities to minimize downtime.
How is MTBF calculated?
MTBF is calculated by dividing the total operational time by the number of failures that occurred during that period. The formula is: MTBF = Total Operational Time / Number of Failures.
What is MTTR, and why is it essential in maintenance?
MTTR stands for Mean Time To Repair. It measures the average time it takes to repair equipment or a system after a failure. MTTR is essential in maintenance to evaluate the efficiency of the repair process and minimize downtime.
How is MTTR calculated?
MTTR is calculated by dividing the total time spent on repairs by the number of repair incidents. The formula is: MTTR = Total Repair Time / Number of Repairs.
What is MTTA, and why does it matter in maintenance?
MTTA stands for Mean Time To Acknowledge. It measures the average time it takes to acknowledge the occurrence of a failure or issue. MTTA is vital in maintenance to ensure prompt identification of problems and initiate repair actions swiftly, reducing downtime.
How is MTTA calculated?
MTTA is calculated by dividing the total time it takes to acknowledge failures by the number of failure incidents. The formula is: MTTA = Total Acknowledgment Time / Number of Failures.
What is MTTF, and how does it contribute to maintenance planning?
MTTF stands for Mean Time To Failure. It estimates the average time a piece of equipment operates before experiencing a failure. MTTF is valuable in maintenance planning as it aids in predicting equipment lifespan and scheduling maintenance activities.
How is MTTF calculated?
MTTF is calculated by dividing the total operational time by the number of failures that occurred during that period. The formula is: MTTF = Total Operational Time / Number of Failures.
Thank you for explaining to us that MTBF refers to the metric that calculates the average time between one failure and the next since it quantifies the reliability of the product to determine how often it requires maintenance. My brother invested in an electronics company recently, so he needs an MTBF analysis for the new lineup of products they plan to release next year. I’ll keep this in mind while I help him find consulting services to hire for MTBF prediction and calculations soon.
Good
I used to be suggested this website through my cousin. I am no longer certain whether
this put up is written through him as nobody else know such targeted about
my trouble. You’re incredible! Thank you!
I am here to assist you as always
Hey people!!!!!
Good mood and good luck to everyone!!!!!
I am truly thankful to the owner of this web site who has shared
this great paragraph at at this time.
It is not my first time to visit this website, i am browsing
this web site dailly and get fastidious facts from here everyday.
Hello, Neat post. There is a problem together with your web
site in web explorer, may check this? IE nonetheless is the marketplace leader
and a large portion of other people will pass over your wonderful writing
because of this problem.
Hey people!!!!!
Good mood and good luck to everyone!!!!!
I dugg some of you post as I cerebrated they were extremely helpful very helpful
It’s hard to find well-informed people for this
topic, but you sound like you know what you’re talking about!
Thanks
informative post
Wow news for all us
hi
Hej, jeg ønskede at kende din pris.
our articles are free of cost for all users
Thanks for the article. Here’s more on the topic https://up-top.ru/
This is a very interesting and important topic, and I am glad that the participants are so actively sharing their opinions and experiences. The discussion turned out to be really diverse, because many issues become relevant with the development of modern technologies.
You made some decent points there. I did a search on the topic and found most individuals will consent with your blog.
Sure