Introduction
Milling operations are fundamental processes in machining that involve the use of rotary cutters to remove material from a workpiece. It’s a versatile technique used across various industries for precision shaping, cutting, and creating complex geometries. In this blog, we will delve into the different types of milling operations, understand their applications, and explore their significance in modern manufacturing.
Milling Machine
A milling machine is a versatile and essential tool in manufacturing and machining processes. It operates by removing material from a workpiece using rotary cutters to create intricate shapes and precise finishes. The workpiece is securely held on a bed or worktable, while the cutting tool rotates and moves in multiple directions, including up-down, side-to-side, and back-forth. This allows the machine to perform various milling operations, such as face milling, peripheral milling, and slot milling. Milling machines are crucial in industries like metalworking, woodworking, and plastics, providing the capability to produce complex components and parts with high accuracy and efficiency.

Types of Milling Operations
Milling operations are cutting processes used to shape and finish materials. Types include face milling for flat surfaces, peripheral milling for cutting edges, and slot milling for creating slots. Plunge milling enables deep cuts, while end milling produces profiles, and ball nose milling forms contoured shapes. Gang milling involves multiple cutters, and CNC milling utilizes computer controls. Each method offers unique advantages in material removal and precision, making milling vital in various industries for efficient and precise manufacturing. Let us know about them in detail –
Face Milling
Face milling is a common milling operation where the cutter’s axis is parallel to the workpiece surface. The cutting tool, known as a face mill, removes material from the face of the workpiece to create a flat surface. This process is often used for finishing large, flat areas or for creating precisely perpendicular surfaces.
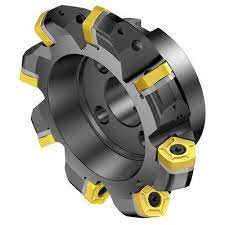
- Face milling is widely used in machining to create flat surfaces on a workpiece. It is highly efficient for removing large amounts of material quickly and achieving smooth finishes. Common applications include the milling of engine blocks, metal plates, and large casting surfaces. Face milling is essential for manufacturing components with precise flatness requirements and is an integral part of various industries, such as automotive, aerospace, and general engineering.

Peripheral Milling
In peripheral milling, the cutter’s axis is parallel to the workpiece surface, but the cutting occurs around the periphery of the cutter. This type of milling is ideal for removing large amounts of material quickly and efficiently. It is also known as roughing operations.

- Peripheral milling finds extensive application in various industries, such as automotive, aerospace, and electronics. It is commonly used for machining slots, keyways, and contours on workpieces. The process is ideal for creating precise edge profiles and grooves on materials like metal, plastic, and wood. Whether it’s producing gears, cutting threads, or shaping components, peripheral milling provides excellent versatility and accuracy for a wide range of manufacturing tasks.

End Milling
End milling involves using an end mill, which has cutting edges on the bottom and the sides, to remove material from the workpiece. It’s often used to create slots, pockets, and contours. End milling can be done in both conventional and climb milling directions, impacting the cutting forces and surface finish.

- End milling is widely applied in manufacturing processes to create profiles and features on the end of a workpiece. It is commonly used for producing flat surfaces, pockets, and contours. End mills are versatile tools used in various industries, including metalworking, woodworking, and mold-making. They provide excellent precision and efficiency for tasks like cutting, drilling, and slotting operations on different materials.

Slot Milling
Slot milling is a type of end-milling operation focused on creating slots, grooves, or keyways on the workpiece. The cutter moves radially into the workpiece, cutting along the sides to form the desired slot shape.

- Slot milling is a crucial machining operation used to create slots and grooves in workpieces. It finds application in manufacturing parts like keyways, T-slots, and internal slots on components such as shafts and machine tables. This process is widely used in industries like automotive, aerospace, and tool-making. Slot milling enables efficient material removal, precise slot dimensions, and improved overall component functionality in various engineering applications.

Plunge Milling
Plunge milling involves the axial movement of the cutting tool into the workpiece, rather than along the periphery. This process is used for creating pockets or cavities and can be an efficient way to remove material in deep cuts.

- Plunge milling is valuable for creating deep pockets, holes, and channels in workpieces. It finds application in industries like aerospace and mold making, where the need for efficient material removal is crucial. Plunge milling allows for faster machining of deep features without pre-drilling, reducing setup time and improving accuracy. This operation is instrumental in manufacturing turbine blades, cavities, and complex molds with precision and productivity.
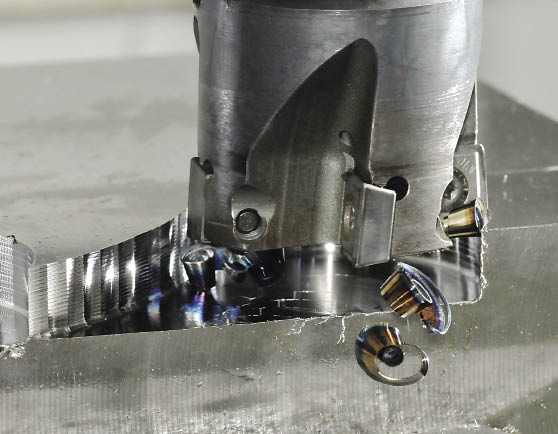
Pocket Milling
Pocket milling is similar to slot milling but involves creating open-ended cavities or pockets in the workpiece. The cutter moves in an enclosed path to remove material and create the desired pocket shape.
- Pocket milling is commonly used in machining to create open-ended cavities or pockets in a workpiece. This operation is ideal for manufacturing parts with recessed features, such as pockets, slots, or complex shapes. Pocket milling allows for efficient material removal and precise control, making it a versatile process in various industries like automotive, aerospace, and electronics manufacturing.
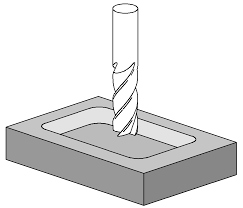
CNC Milling
Computer Numerical Control (CNC) milling is a modern automated milling process. It utilizes computer programming to control the movements of the milling machine and achieve high precision and repeatability. CNC milling is widely used in industries like aerospace, automotive, and electronics for complex and intricate machining tasks.
- CNC milling is a versatile machining operation that uses computer numerical control to precisely remove material from a workpiece. It finds widespread applications in manufacturing industries, producing complex parts for aerospace, automotive, electronics, and medical sectors. CNC milling ensures high accuracy, repeatability, and efficiency, making it an essential process for modern industrial production.

5-Axis Milling
Five-axis milling is an advanced machining technique that allows simultaneous movement of the cutting tool along five different axes. This capability enables the machining of complex and intricate geometries on all sides of a workpiece, reducing setup time and increasing precision. It is widely used in aerospace, automotive, and medical industries for manufacturing highly sophisticated components, prototypes, and molds, providing greater flexibility and efficiency in the production process.
- 5-axis milling is an advanced CNC machining technique capable of moving a workpiece in five directions simultaneously. This versatile operation is ideal for complex and contoured parts, such as aerospace components, turbine blades, and medical implants. Its ability to reach difficult angles and reduce setup times makes 5-axis milling essential for industries requiring high precision and intricate geometries.

Face Milling vs. Peripheral Milling
Face milling is preferred for flat surfaces, while peripheral milling is more suitable for removing large amounts of material quickly. The choice between the two depends on the specific machining requirements and the workpiece’s material properties.

Up Milling vs. Down Milling
In up-milling (conventional milling), the cutting tool rotates against the direction of the feed, resulting in higher tool wear but a better surface finish. In down milling (climb milling), the cutting tool rotates in the same direction as the feed, reducing tool wear but potentially leading to a rougher surface finish. Selecting the appropriate milling direction depends on factors such as workpiece material, cutter geometry, and machine stability.
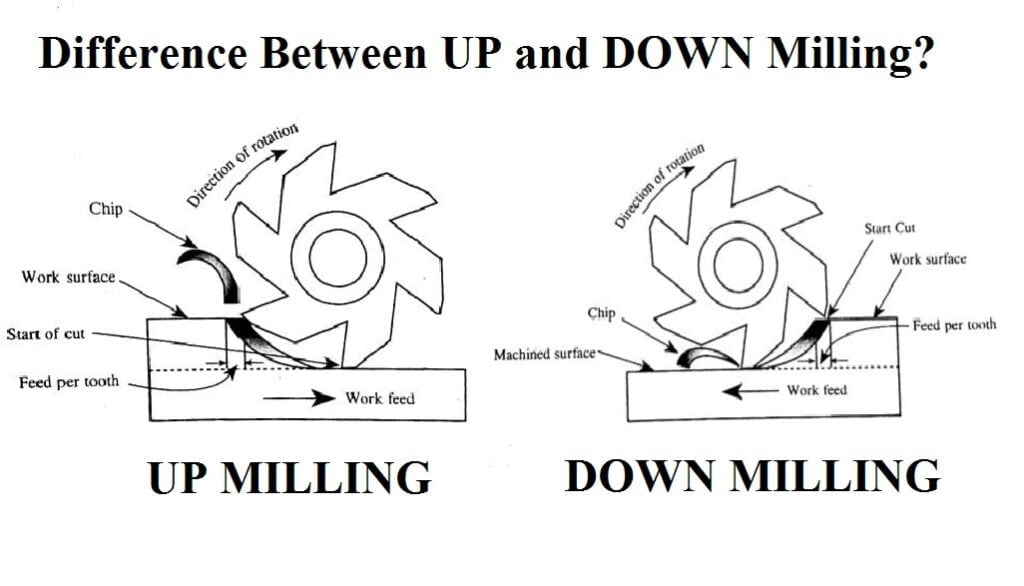
To know about the injection mold manufacturing process…read more
Also, check out the frequently asked questions on the net about milling operations –
Which type of milling cutter is used in straddle milling operations?
In straddle milling operations, a side milling cutter is used. This type of milling cutter has teeth on both sides and is mounted on an arbor, enabling it to machine two parallel surfaces on the workpiece simultaneously. Straddle milling is commonly used for machining slots, keyways, and other features that require a wider cut than what a single cutter can achieve, improving efficiency and reducing production time.
How is the order of operations generally selected for manual milling?
In manual milling, the order of operations is generally selected based on a combination of factors such as the workpiece material, part geometry, and machining requirements. The process typically begins with roughing operations to remove excess material efficiently, followed by semi-finishing to get closer to the final dimensions. Finishing operations are then performed to achieve the desired surface quality and accuracy. It’s essential to consider the tooling and setup constraints, ensuring optimal tool life and minimal tool changes. Machinists often prioritize safety, minimizing workpiece handling, and maintaining a logical sequence to prevent errors and achieve the best possible result.
How do I show milling operations on part drawing?
A milling machine can perform a wide range of operations, including facing, end milling, slotting, drilling, boring, chamfering, profiling, and more. Its versatility allows for complex part production and precision machining across various materials, making it a fundamental tool in modern manufacturing processes.
To show milling operations on a part drawing, you should use specific machining symbols and annotations to communicate the required features accurately to machinists and manufacturers. Commonly used symbols include –
Machining operation symbols: Use standard symbols for operations like facing, pocketing, contouring, drilling, and more.
Dimensioning and tolerancing: Clearly indicate dimensions, tolerances, and surface finishes for milled features.
Section views: If needed, include sectional views to display internal milling operations.
Material specifications: Specify the material type and its required hardness or other properties.
Notes: Add any additional instructions, tooling requirements, or process details relevant to the milling operations.
Using these elements, the part drawing provides a comprehensive and precise representation of the milling operations required to produce the final component.