What is Injection Molding Gate?
Injection molding gate is the entry point through which molten plastic or other materials are introduced into a mold cavity to form a desired product shape. It controls the flow of material, ensuring proper filling of the mold and uniform distribution. The gate location, size, and design impact the final part’s quality, minimizing defects like air pockets. Common gate types include edge, pin-point, and submarine gates. Selecting an appropriate gate is crucial for achieving consistent part dimensions, minimizing material waste, and optimizing production efficiency in the injection molding process.

Why do you need Injection Mold Gate Design?
Injection mold gate design is essential as it directly influences the quality and efficiency of the injection molding process. An appropriate gate design ensures controlled material flow into the mold cavity, preventing defects like air entrapment and incomplete filling. Proper gate placement and size enable uniform part cooling and reduced stress, minimizing warping and ensuring consistent dimensions. Effective gate design also optimizes cycle times and material usage, enhancing production efficiency and reducing costs. A well-designed gate facilitates easy part ejection, streamlining manufacturing processes and yielding high-quality final products in plastic injection molding.
Importance of Gate Location in Injection Molding
The gate location in injection molding plays a pivotal role in determining the overall quality, appearance, and manufacturability of the molded parts. The placement of the gate significantly impacts material flow, cooling, and the distribution of stresses within the product.
- Firstly, gate location affects material flow patterns. Placing the gate at the optimal location ensures that the molten material fills the mold cavity uniformly, minimizing the chances of air entrapment, voids, or inconsistent wall thicknesses. Improper gate positioning can result in flow imbalances, leading to defects like weld lines, sink marks, or short shots.
- Secondly, gate location influences part cooling. The gate acts as the initial entry point for the molten material, and its location determines how heat is dissipated during the solidification process. An ill-placed gate can lead to uneven cooling, causing internal stresses, warping, and dimensional inaccuracies in the final part.
- Additionally, gate location impacts the ease of part ejection from the mold. A well-positioned gate facilitates smooth ejection, reducing the likelihood of damage to both the part and the mold.
- Moreover, gate location affects the aesthetics of the final product. Gates often leave behind marks or scars on the part, which can be more or less noticeable depending on their location. Designing the gate to minimize its impact on the visible surfaces of the part is crucial for maintaining its visual appeal.
- Gate location is critical in injection molding because it directly affects material flow, cooling, part ejection, and aesthetics. Proper gate placement enhances product quality, reduces defects, and improves the overall efficiency of the manufacturing process. Careful consideration of gate location during the design phase leads to better end products and a more cost-effective production process.

Types of Gates used in Injection Mold
Injection molding gates include various types –
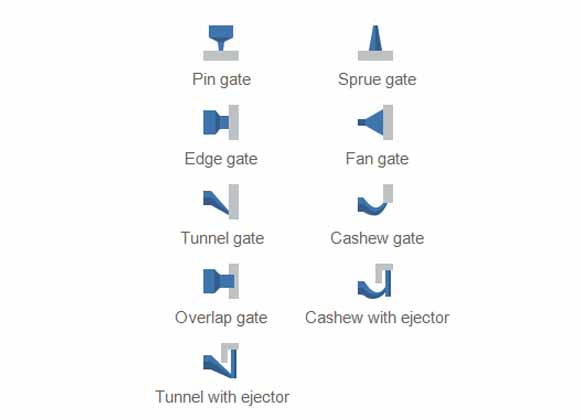
Direct or Sprue Gate
A sprue gate is the primary entry point for molten material into an injection mold. It connects the runner system to the mold cavity. While simple and cost-effective, it can leave noticeable gate marks on the part. Sprue gates are typically located at the thickest section of the part and are easy to remove after molding.
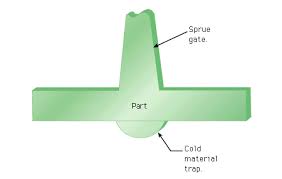
Edge or Side Gate
An edge or side gate is a type of injection molding gate located at the edge of a part. It offers simple and efficient material flow into the mold cavity, minimizing air entrapment. This gate leaves a visible mark on the part but is commonly used for its ease of manufacturing and ejection. It’s suitable for various part sizes and shapes, often chosen when appearance is not a primary concern.

Submarine/Tunnel Gate
A submarine or tunnel gate is a concealed type of injection molding gate located beneath the part’s surface. It minimizes visible gate marks on the finished part by allowing the gate to be hidden from view. This gate design is useful for parts requiring a high-quality appearance. However, it can be more complex to design and implement compared to other gate types, potentially affecting production efficiency.
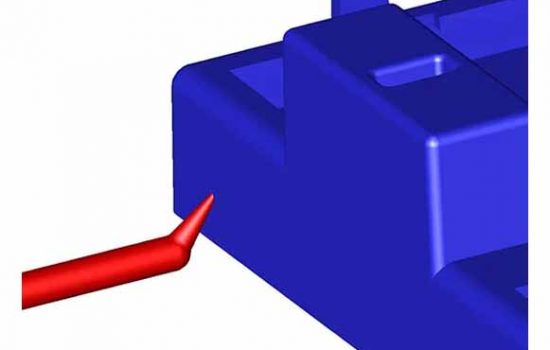
Cashew Gate
A cashew gate, also known as a banana gate, is a specialized injection molding gate resembling the shape of a cashew or banana. It’s often used for parts requiring minimal gate marks and aesthetics. This unique gate design helps reduce visible marks on the part’s surface while maintaining proper material flow. Its shape can complicate mold design, but it offers advantages in improving the final product’s appearance.

Diaphragm Gate
A diaphragm gate is a thin and subtle injection molding gate, designed to reduce visible gate marks on cosmetic or visible surfaces of a part. It minimizes the impact on the part’s appearance while ensuring proper material flow. This gate type requires precise control to prevent flow issues, making it suitable for parts where aesthetics are crucial, but careful design is essential for success.

Fan Gate
A fan gate is a wide and gradually tapering injection molding gate used for larger parts. It evenly distributes material flow, reducing the risk of flow-related defects. This type of gate is advantageous for parts with extended surface areas or complex geometries, ensuring uniform filling. Although it minimizes visible gate marks, it might require extra attention to prevent cosmetic imperfections on the part’s surface.
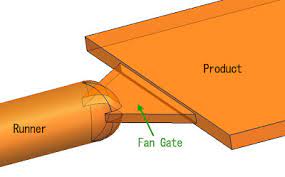
Rectangular Gate
A rectangular gate is a straightforward injection molding gate with a rectangular shape. It offers a controlled entry point for molten material into the mold cavity, ensuring uniform flow. This type of gate is commonly used for various part sizes and shapes, as well as when appearance is not a primary concern. It leaves visible gate marks but is cost-effective and easy to implement.

Pin Gate
A pin gate, also known as a pinpoint gate, is a small and precise injection molding gate. It’s ideal for delicate or intricate parts where gate marks need to be minimal. This gate type offers controlled material flow, reducing the risk of defects. Although it ensures fine detail, it might require careful design to prevent flow-related challenges and is typically chosen for parts where aesthetics are crucial.

Tab Gate
A tab gate is a specialized injection molding gate resembling a small tab. It’s often used for flat or thin parts where gate marks must be inconspicuous. This type of gate provides controlled material flow while minimizing the visual impact on the part’s appearance. It can be advantageous for parts requiring a clean surface finish, but careful design and positioning are essential for successful implementation.

Hot Runner Valve Gate
A hot runner valve gate is an advanced injection molding system that maintains molten material at elevated temperatures within the runner and gate channels. It employs a valve mechanism to precisely control material flow, minimizing gate vestiges on the part. This system enables faster production, reduced waste, and enhanced part quality, making it suitable for high-quality or complex parts where gate marks need to be minimized.
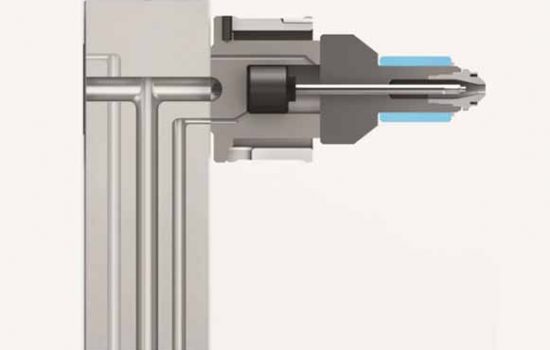
Hot Runner Thermal Gate
A hot runner thermal gate is a controlled injection molding gate system that maintains molten material’s temperature in the runner and gate channels. It ensures uniform material flow and reduces gate marks on the final part. This technology enhances part aesthetics and quality, making it valuable for high-end products. However, its implementation complexity requires careful design and maintenance.

Design Consideration for Injection Molding Gate
When designing an injection molding gate, several key considerations must be taken into account. First, gate location impacts material flow and part cooling, affecting part quality and appearance. Gate type influences gate marks and material distribution.
Size affects flow rate and potential defects. Balancing gate size with part size is crucial for uniform filling. Gate design should prevent air entrapment and minimize pressure drop. Gate positioning should facilitate easy ejection. Material properties and mold temperature impact gate design. Finally, the gate’s visual impact on the part’s surface should align with the desired aesthetics. Overall, gate design demands a balance between functionality, aesthetics, and manufacturability.
Gate Placement
Gate placement in injection molding design is critical for optimal part quality. It determines material flow, cooling, and appearance. Placing the gate at thicker sections reduces warping and enhances filling. Correct placement minimizes visible gate marks and ensures uniform distribution of molten material. Strategic gate positioning also influences efficient part ejection and overall production effectiveness.
Gate Size
Gate size is a vital design consideration in injection molding. It affects material flow rate, pressure, and potential defects. An appropriately sized gate allows proper filling while avoiding flow-related issues like air entrapment. A larger gate might speed up filling but can lead to visible marks. A smaller gate minimizes marks but requires careful control to avoid flow problems. Balancing gate size with part geometry and appearance is crucial for successful molding.
Part Shape & Finish
When considering gate design for injection molding, part shape and finish play pivotal roles. Part geometry influences gate placement, ensuring even filling and minimal material waste. Complex shapes might necessitate specific gate types for optimal material flow. Additionally, gate location should minimize visible marks on visible surfaces, preserving the part’s aesthetics.
The gate’s impact on the surface finish must align with the desired appearance. A well-designed gate ensures uniform cooling, reducing part warping and stress. Thus, harmonizing gate selection with part shape and finish guarantees both functional and visually appealing molded products.
Conclusion
The selection of the appropriate gate type in injection molding holds significant implications for the quality, efficiency, and aesthetics of the final product. The diverse array of gate types, such as edge gates for simplicity, submarine gates for minimal marks, and fan gates for larger parts, enables manufacturers to tailor their approach to specific design and production needs. Pin gates serve delicate parts, while diaphragm gates prioritize cosmetic surfaces.
Each gate type demands careful consideration of factors like material flow, cooling, and visible marks. Achieving a balance between functional requirements and desired appearance is crucial. By understanding and leveraging the nuances of gate types, manufacturers can optimize their injection molding processes to yield superior outcomes, whether it be enhanced part quality, minimized defects, or improved overall production efficiency.
FAQ’S
Where do you put the gate on injection molding?
In injection molding, gates are strategically placed on the part to facilitate proper material flow and minimize defects. Gates are typically located at thicker sections, geometrically balanced areas, or where appearance is less critical. Proper gate positioning ensures uniform filling, minimal visible marks, and efficient ejection, contributing to the overall quality of the molded part.
What are the common problems that occur in injection molding?
Common problems in injection molding include –
Warping: Parts deform due to uneven cooling, affecting dimensions.
Sink Marks: Indentations occur when thick sections cool unevenly.
Flash: Excess material escapes between mold halves, leading to excess protrusions.
Short Shots: Incomplete filling creates underfilled parts.
Burn Marks: Material overheats, causing surface discoloration.
Flow Lines: Material cools at different rates, leaving visible lines.
Voids and Bubbles: Air trapped creates internal defects.
Jetting: Fast material entry leaves marks and poor surface finish.
Weld Lines: Material flow fronts meet, resulting in weak lines.
Ejector Marks: Ejection pins cause impressions during part removal.
What are the basic steps to injection molding?
Injection molding involves –
1. Material Preparation.
2. Injection.
3. Cooling.
4. Ejection & Repeat the same
How many types of gates are used in injection molding?
Some common gates types include –
01. Edge Gates
02. Submarine Gates
03. Pin Gates
04. Tab Gates
05. Fan Gates
06. Diaphragm Gates
07. Cashew Gates
08. Hot Runner Valve Gates
09. Sprue Gate (Primary Gates)
10. Tunnel Gates
Each gates type has its advantages and is suited to different molding scenarios and part requirements.
What are types of runner in mold?
In injection molding, runners are channels that connect the sprue to individual cavities in the mold. Different types of runners are employed based on production needs.
Cold Runners are conventional and cost-effective, but result in material wastage during purging.
Hot Runners maintain molten material, reducing waste and cycle time.
Subtypes include Open Sprue, where molten material directly enters the runner system, and Valve Gate, which controls material flow. Hot Sprue allows for easier mold design changes. Insulated Runners use insulation to manage material temperature. Selecting the appropriate runner type depends on factors like material, part geometry, production volume, and desired quality.
Awesome post.