In this article, you will learn about lathe machine, lathe machine type, lathe machine parts & their work, and at the end, you can find some applications of lathe machines. Stay connected to this article to learn about lathe machines.
What is a Lathe Machine?
A lathe machine is a type of machine that rotates the workpiece on its axis so that cutting, drilling, and shaping operations can be performed with precision. It is commonly used in metal and woodworking to make cylindrical objects and symmetrical components.
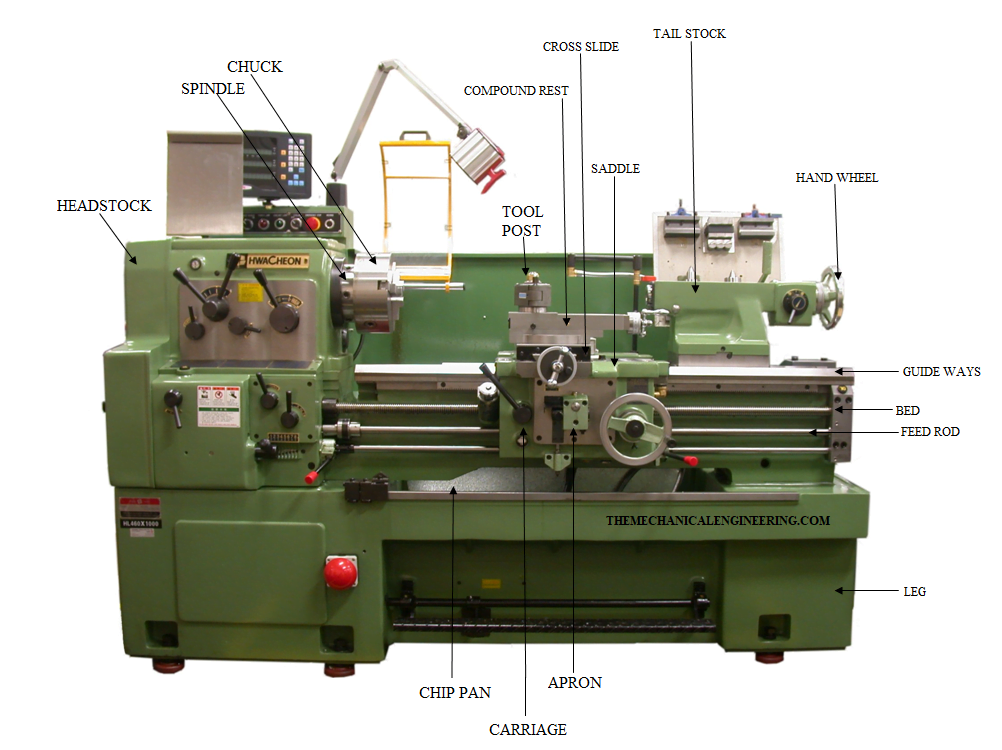
What Are The Types of Lathe Machines?
The main types of lathe machines are –
1. Speed Lathe Machine
It is a basic type of lathe with a high spindle speed, often used for light-duty tasks like metal spinning and polishing. It lacks advanced features but excels at producing small workpieces swiftly and efficiently, making it suitable for simple applications in various industries.
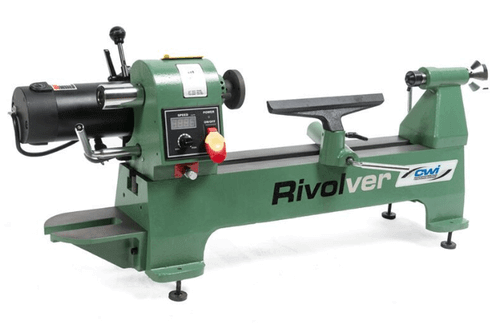
2. Center Lathe or Engine Lathe Machine
It is a versatile tool used for general-purpose machining tasks. It rotates the workpiece on its axis, allowing cutting, drilling, and shaping operations. With various attachments and accessories, it can handle both small and large workpieces, making it a fundamental tool in the metalworking and woodworking industries.
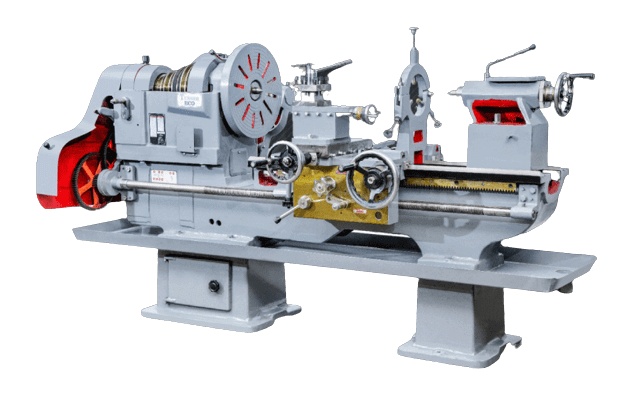
3. Turret Lathe Machine
This lathe machine is equipped with a turret tool post, enabling rapid and automatic tool changes. It is highly suitable for repetitive tasks, as it can hold multiple tools simultaneously. This feature enhances productivity and efficiency in manufacturing processes, particularly in mass production and turning operations.
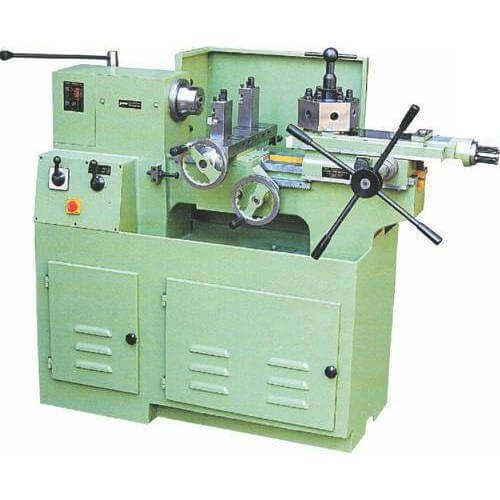
4. Toolroom Lathe Machine
This lathe machine is designed for precision machining and toolmaking in workshops or toolrooms. It offers higher accuracy, versatility, and customization options than standard lathes. With its robust construction and fine controls, it can handle complex tasks and produce high-quality components for various industries.
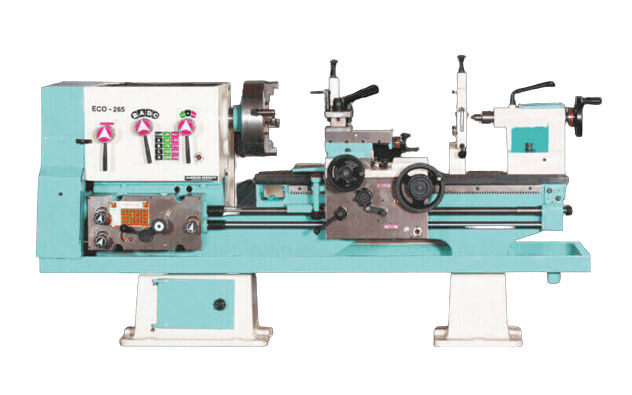
5. Bench Lathe Machine
It is a compact and lightweight version of the lathe, designed for small-scale projects and hobbyists. It is suitable for basic turning, facing, and drilling operations on small workpieces. Though limited in power and size, it serves as an affordable and portable option for light-duty tasks.
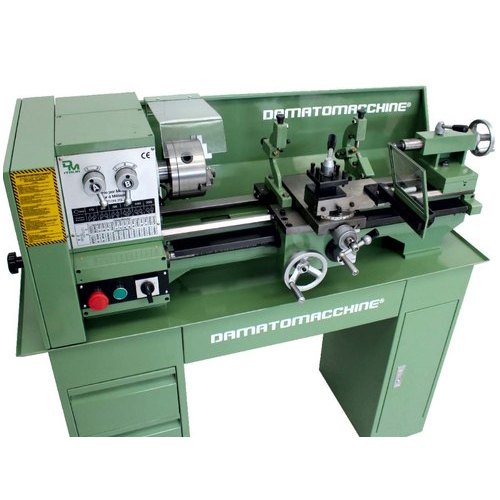
6. Automatic Lathe Machine
It is a highly automated tool that performs machining operations without constant manual intervention. It is capable of handling repetitive tasks efficiently, making it ideal for mass production. Equipped with automatic tool changers and control systems, it enhances productivity and precision in manufacturing processes.
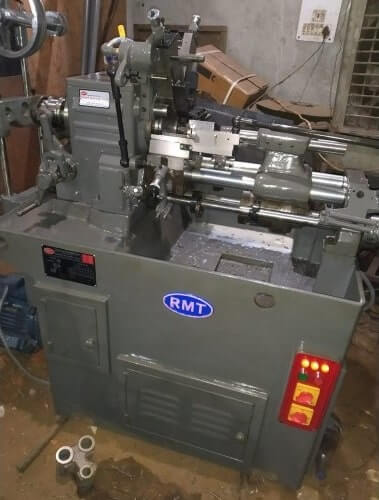
7. Special Purpose Lathe Machine
It is designed for specific and unique machining applications. It is customized with specialized attachments, tooling, and features to cater to specific production needs. These machines are highly efficient in producing specialized components, parts, or products for various industries with precise and tailored machining capabilities.
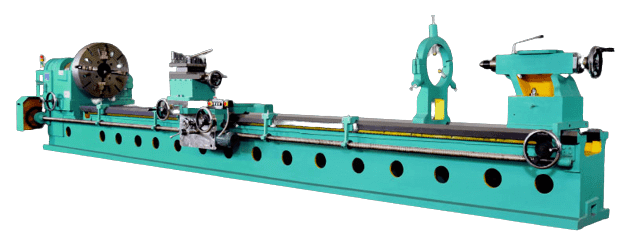
8. CNC Lathe Machine
The CNC lathe machine is a computer-controlled tool that offers high precision and automation in machining operations. It utilizes pre-programmed instructions to control the cutting tools’ movements, allowing for complex and intricate work on various materials. CNC lathes enhance productivity, consistency, and accuracy in modern manufacturing processes.
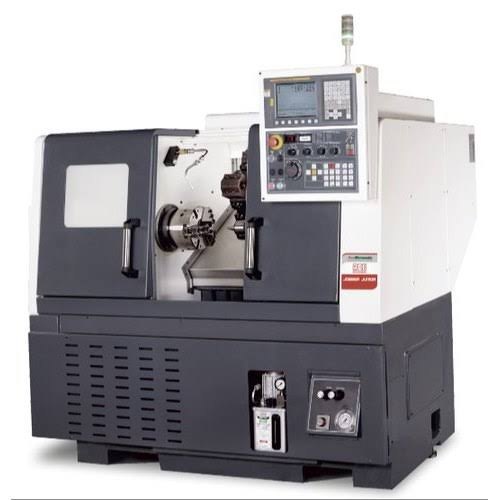
What Are The Parts of the Lathe Machine?
The main parts of a lathe machine include –
1. Carriage
The lathe machine carriage is a moving component that holds and controls the cutting tool. It moves along the lathe bed using handwheels or automated feeds.
- The carriage’s function is to facilitate the lateral movement of the cutting tool, allowing it to traverse the workpiece during turning and facing operations. It ensures the tool maintains a consistent depth of cut and produces the desired shape on the workpiece.
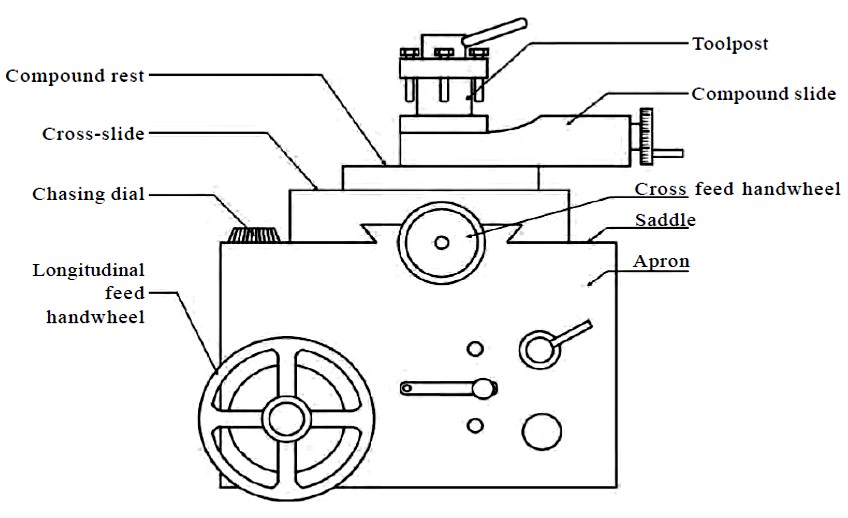
The carriage unit of the lathe machine also consists of some major parts and they are –
1.1. Saddle
The lathe machine saddle is a part mounted on the lathe bed that holds the cross slide and compound rest. It allows the cross slide and compound rest to move along its length.
- The saddle’s function is to provide lateral movement and support for the cutting tool, enabling it to make precise and controlled cuts across the workpiece during facing, turning, and tapering operations, enhancing machining accuracy.
1.2. Cross Slide
The lathe machine cross slide is a component mounted on the saddle that moves perpendicular to the lathe bed. It holds the cutting tool and enables precise lateral movement for facing and turning operations.
- The cross slide’s function is to control the tool’s horizontal position, allowing operators to achieve accurate cuts and smooth finishes on the workpiece, enhancing the overall precision of the machining process.
1.3. Compound Rest
The lathe machine compound rest is a part attached to the cross slide, allowing the cutting tool to be adjusted at various angles.
- Its function is to facilitate taper turning and other angular cuts on the workpiece. By providing controlled movement in two directions, the compound rest enables the operator to create intricate shapes and contours, enhancing the lathe’s versatility in machining operations.
1.4. Compound Slide
The lathe machine compound slide, also known as the compound rest, is a critical part mounted on the cross slide. It allows the cutting tool to be set at different angles to the workpiece.
- The compound slide’s function is to enable the operator to perform complex machining tasks like taper turning, thread cutting, and beveling, enhancing the lathe’s capability to produce diverse and precise components.
1.5. Tool Post
The lathe machine tool post is a component that holds and secures the cutting tool in place. It is mounted on the carriage and can be adjusted for height and angle.
- The tool post’s function is to provide a stable platform for the cutting tool, ensuring precise alignment with the workpiece and enabling efficient cutting, turning, and facing operations with accuracy and repeatability.
1.6 Apron
The lathe machine apron is a part located on the front of the carriage, containing gears, clutches, and mechanisms for automatic feed control.
- Its function is to engage and disengage the feed and threading mechanisms, allowing the operator to adjust the rate and direction of the cutting tool’s movement. The apron enables precise and automated feeding during turning and threading operations, enhancing efficiency and accuracy.
2. Tailstock
It is an essential component situated at the opposite end of the headstock. It can be adjusted to support the workpiece, allowing the machining process to occur accurately and efficiently.
- Its primary function is to provide alignment, stability, and counterforce to the cutting tool, ensuring precise and consistent turning, drilling, and boring operations on the workpiece.
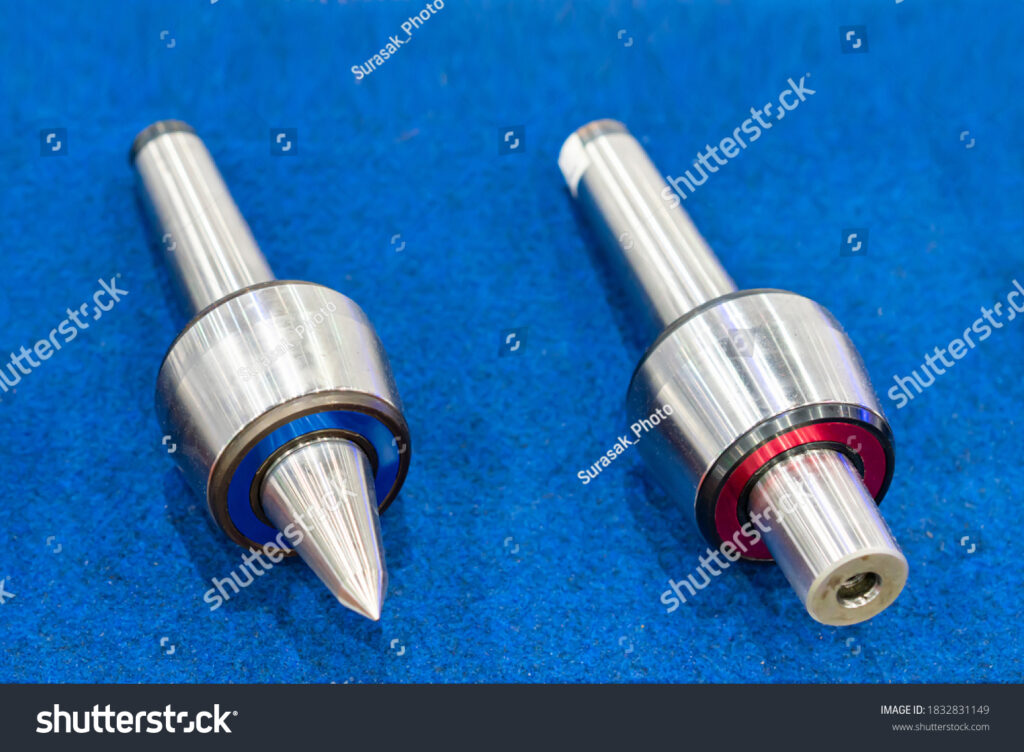
3. Sleeve
The lathe machine sleeve, also known as the tailstock sleeve or quill, is a cylindrical part within the tailstock. It moves in and out of the tailstock barrel and houses the center or drill to support the workpiece.
- The sleeve’s function is to provide fine adjustments for the center’s position, ensuring precise alignment with the headstock, and improving concentricity and accuracy in turning, drilling, and boring operations.
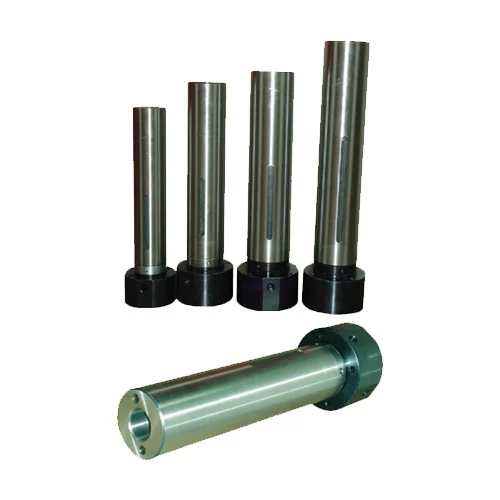
4. Headstock
It is a crucial part located at the left end of the lathe bed. It houses the spindle, which rotates the workpiece and provides various speed settings for different machining requirements.
- Its main function is to transmit power to the workpiece, allowing cutting tools to shape, turn, and drill materials with precision and accuracy during metalworking and woodworking processes.
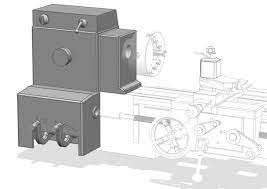
5. Bed
It is the foundation and main horizontal structure of the lathe. It supports and aligns all other components, providing stability and rigidity during machining operations.
- Its function is to ensure accurate and smooth movement of the carriage and tailstock along its length. The bed’s robust design and proper alignment are essential for achieving precision and repeatability in the turning process.
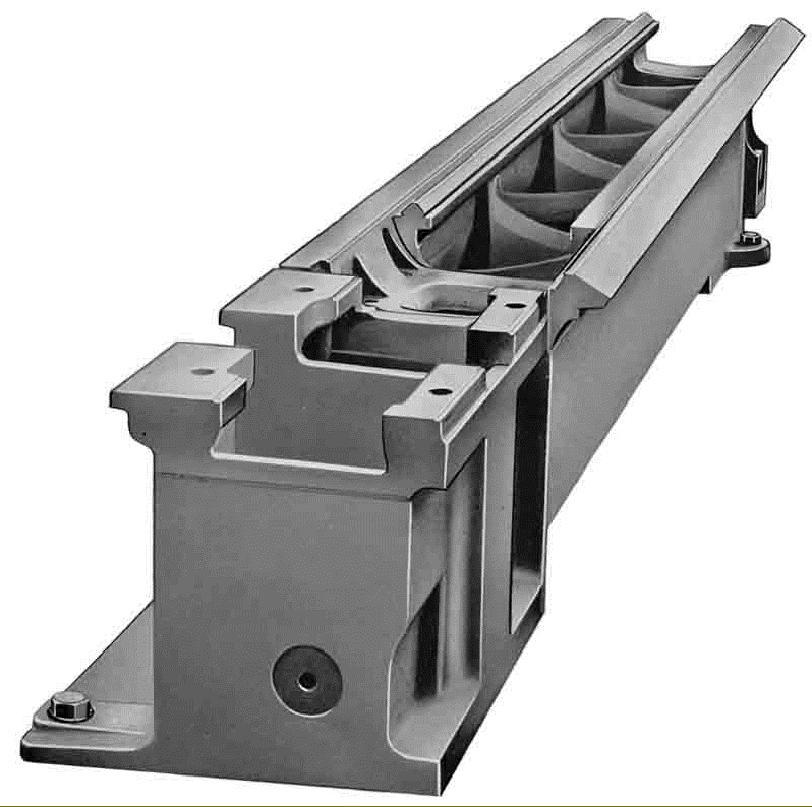
6. Lead Screw
It is a long, threaded rod located parallel to the lathe bed. It engages with the carriage to provide longitudinal movement during thread cutting and automatic feed operations.
- Its function is to transmit power and motion from the feed rod, allowing the carriage to move in a controlled manner, enabling accurate and uniform threads to be cut on the workpiece during the turning process.
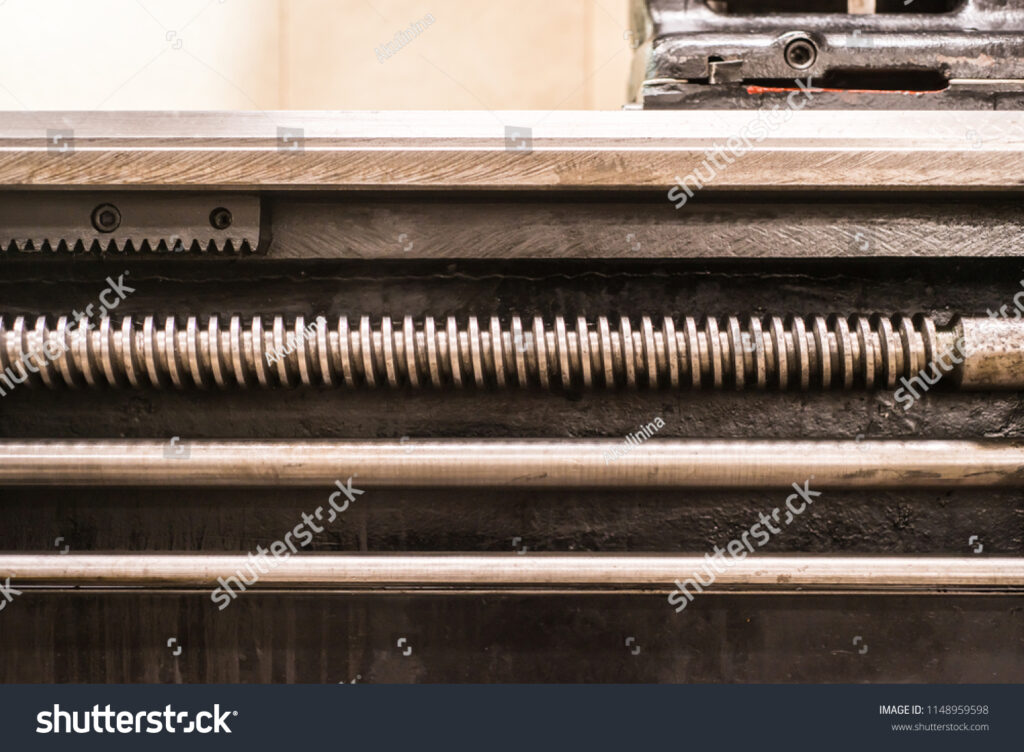
7. Spindle
The spindle is a key component located in the headstock. It rotates the workpiece, allowing cutting tools to shape, turn, and bore materials.
- Its function is to hold the workpiece securely in place and transmit rotational power from the headstock to achieve smooth and controlled cutting operations. The spindle’s precision and stability are crucial for achieving accurate and consistent results in machining.
8. Mandrel
The lathe machine mandrel is a cylindrical device used to support hollow workpieces during machining. It is inserted into the workpiece’s internal bore to prevent distortion and ensure concentricity.
- Its function is to provide additional rigidity and support, allowing for precise turning, drilling, and other operations on thin-walled or tubular workpieces, enhancing accuracy and quality in the machining process.
9. Faceplate
It is a flat, disc-shaped component attached to the lathe’s spindle. It provides a large flat surface to mount irregularly shaped workpieces that cannot be held by chucks.
- Its function is to securely hold and support the workpiece during machining, enabling operations like facing, turning, and drilling, ensuring stability and precision in working with non-cylindrical or asymmetric materials.
10. Bull Gear
The lathe machine bull gear is a large gear located in the headstock. It meshes with the gear on the spindle, transmitting power from the main motor to the spindle.
- The bull gear’s function is to provide different speed ranges for the lathe’s spindle, allowing operators to adjust the rotational speed to suit various materials and cutting requirements, enabling precise and efficient machining operations.
11. Chuck
The lathe machine chuck is a clamping device used to hold and secure the workpiece on the lathe spindle. It comes in various designs, including three-jaw, four-jaw, and collet chucks.
- The chuck’s function is to provide a strong and concentric grip on the workpiece, allowing for precise and stable rotation during turning, facing, and drilling operations, ensuring accurate and consistent machining results.
12. Guideway
The lathe machine guideway is a set of precisely machined tracks or surfaces on the lathe bed. It guides and supports the carriage and tailstock, providing smooth and accurate movement along the lathe’s length.
- Its function is to ensure precise and consistent positioning of the cutting tool and workpiece, allowing for high-quality and repeatable machining operations with minimal friction and wear.
13. Centre
A lathe machine center is a pointed tool or device attached to the tailstock, supporting the opposite end of the workpiece. It ensures proper alignment and concentricity of the workpiece during turning operations.
- The center’s function is to prevent deflection and enable accurate machining by supporting and stabilizing the workpiece’s non-rotating end, facilitating the production of symmetrical and well-centered components.
14. Feed Shaft
The feed shaft is a component connected to the carriage, allowing for the automatic feeding of the cutting tool along the workpiece. It controls the depth and rate of the tool’s movement during machining operations.
- The feed shaft’s function is to enable uniform and controlled cuts, increasing productivity and accuracy by automating the tool’s feeding process, especially in repetitive tasks and long-turning operations.
15. Legs
The lathe machine legs are sturdy supports that hold the lathe bed at a suitable working height. They are usually made of cast iron or steel for stability and strength.
- The legs’ function is to provide a robust and secure base for the lathe, ensuring it remains steady during machining operations. Properly designed legs enhance the lathe’s overall stability and reduce vibrations, leading to better machining precision.
16. Chips Pan
It is a tray or container located beneath the lathe’s work area. It collects and stores the chips and swarf generated during machining operations.
- Its function is to keep the working environment clean and organized by containing metal shavings and coolant, preventing them from scattering and causing workplace hazards. It facilitates easy cleaning and maintenance of the lathe machine.
17. Hand Wheel
It is a manual control located on the carriage or cross slide. It allows operators to move the tool or workpiece by hand during setup or fine adjustments.
- The handwheel’s function is to provide precise and controlled movement, enabling operators to position the cutting tool accurately and achieve the desired dimensions on the workpiece, enhancing the overall precision of the machining process.
18. Speed Controller
The speed controller is a component that regulates the rotational speed of the lathe spindle. It allows operators to adjust the spindle speed based on the material type, cutting tool, and machining requirements.
- The speed controller’s function is to provide variable speed options, enhancing versatility and enabling optimal cutting conditions, resulting in efficient and accurate machining for different workpieces and materials.
What Are The Applications of Lathe Machine?
Lathe machines have widespread applications in various industries, including –
- Metalworking: Turning, facing, and drilling operations for components like shafts, bolts, and bushings.
- Woodworking: Shaping and cutting wood to create furniture, tools, and decorative items.
- Automotive: Manufacturing engine components, axles, and gears.
- Aerospace: Producing precise parts for aircraft and spacecraft.
- Electronics: Machining components for electronic devices and connectors.
- Medical: Fabricating medical instruments and implants.
- Jewelry: Crafting intricate designs on metal for ornaments and accessories.
- Prototyping: Rapid prototyping for product development.
- Repair and Maintenance: Restoring worn-out parts and components.
- Art and Crafts: Creating sculptures and artistic works from various materials.
Here are some frequently asked questions on Google and I’m trying to give them answers here –
What is the Turning Process?
The turning process on a lathe machine involves rotating the workpiece on its axis while a cutting tool removes material to create a cylindrical shape or other profiles. It is widely used for shaping, finishing, and sizing operations, providing high precision and versatility in metalworking and woodworking industries.
What is the Facing Process?
The facing process on a lathe machine involves cutting the end of the workpiece to create a smooth, flat, and perpendicular surface. It is typically used to achieve a precise and square end on the workpiece, ensuring accurate fitting and assembly of components, and enhancing the overall appearance and functionality of the machined part.
What is the difference between Turning & Facing?
Turning is the process of removing material from the external surface of a workpiece to create a cylindrical shape or other profiles. Facing is the process of cutting the end of the workpiece to produce a flat and perpendicular surface. Turning shapes the outer diameter, while facing ensures a smooth and square end.
What is Taper Turning?
Using a lathe, the process of “taper turning” involves progressively changing the workpiece’s diameter along its length to produce a tapered shape. This is achieved by offsetting the tailstock or adjusting the compound rest angle. Taper turning is essential for producing components like conical shapes, machine tool parts, and various fittings.
What type of operation can be performed on the lathe machine?
Lathe machines can perform various operations, including turning, facing, drilling, boring, threading, tapering, and knurling. They are used to shape, cut, and finish workpieces made of metal, wood, or other materials, allowing for precise and versatile machining in industries like manufacturing, automotive, aerospace, and more.