In the realm of mold manufacturing, precision and durability are paramount. As industries demand increasingly complex designs and higher efficiency, traditional welding methods can fall short. This is where laser welding techniques emerge as game-changers, offering unmatched precision, minimal distortion, and a level of control that reshapes the mold manufacturing landscape.
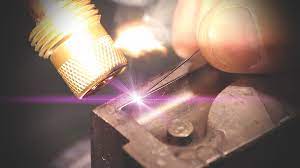
The Power of Laser Welding
Laser welding, a cutting-edge technology, utilizes concentrated beams of light to melt and fuse materials together. The focus keyword, “laser welding,” holds the key to a range of techniques that cater to the intricate demands of mold manufacturing.
Laser Beam Welding (LBW)
LBW involves focusing a high-energy laser beam onto the joint to melt and fuse the materials. It provides remarkable accuracy and minimal heat-affected zones, reducing distortion and preserving the mechanical properties of the mold components. This technique is particularly suitable for welding thin sections and delicate parts.
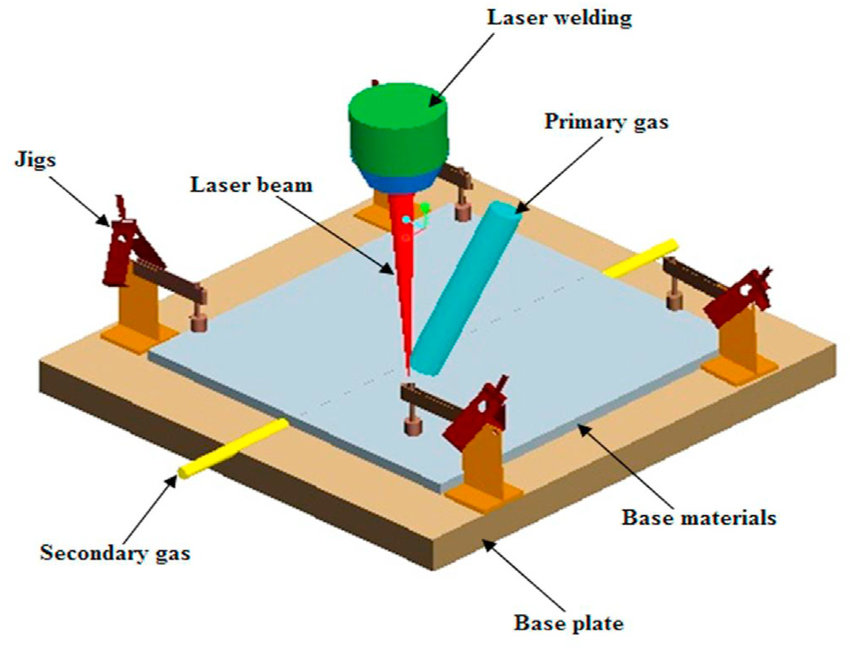
Laser Hybrid Welding
Combining laser welding with another technique like arc welding results in laser hybrid welding. It leverages the advantages of both methods, enhancing weld quality, deposition rate, and deep penetration. In mold manufacturing, this can mean improved joint integrity and reduced production times.
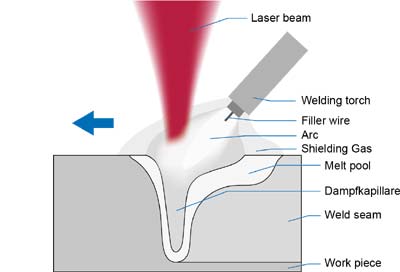
Fiber Laser Welding
Fiber lasers have revolutionized laser welding by offering high power and beam quality in a compact setup. This technique is ideal for welding highly reflective materials, a common requirement in mold manufacturing. Fiber laser welding excels in joining dissimilar materials and is particularly effective for molds with intricate details.
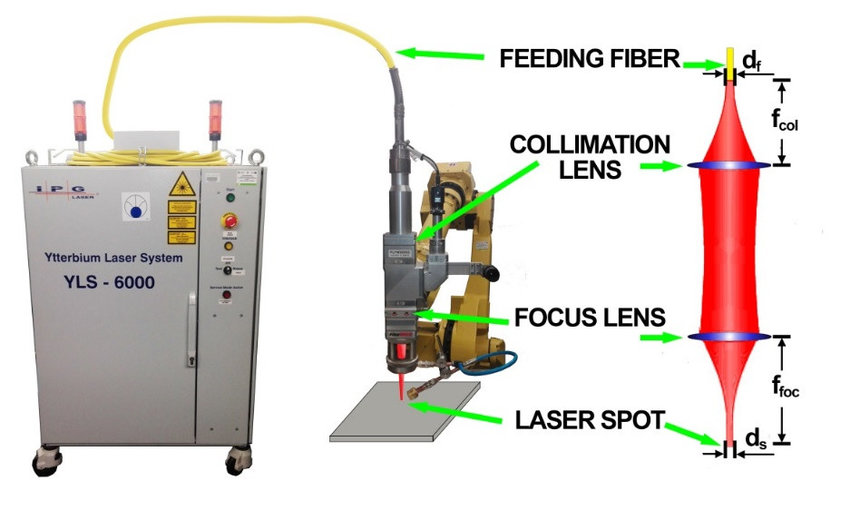
Continuous Wave and Pulsed Laser Welding
Continuous wave (CW) lasers provide a constant beam for consistent welds, while pulsed lasers emit periodic bursts of energy for controlled heating. In mold manufacturing, pulsed lasers are often preferred, as they minimize the heat-affected zone and prevent material distortion, which is essential for preserving the mold’s precision.
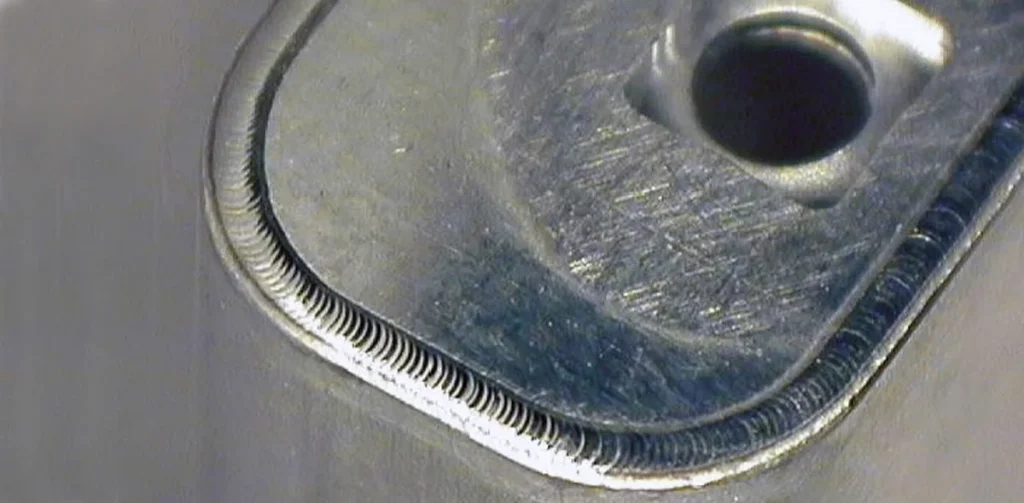
Laser Welding Machine
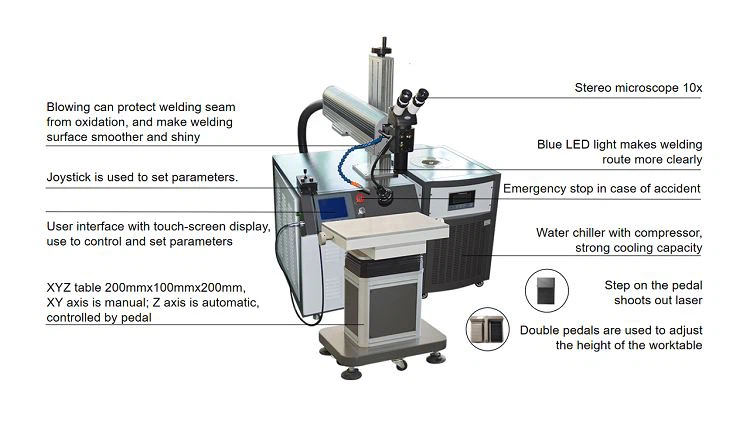
Laser welding machines have become invaluable tools in the mold manufacturing industry due to their exceptional precision and versatility. These machines utilize high-energy laser beams to fuse mold components together, offering several key applications –
- Intricate Mold Designs: It is ideal for creating molds with intricate designs and complex geometries. It can accurately join intricate components and features, ensuring the mold maintains its precision and desired dimensions.
- Repair and Maintenance: These machines are utilized to repair and refurbish damaged molds. They can mend cracks, pits, and other defects in molds, extending their lifespan and reducing the need for costly replacements.
- Component Assembly: It is employed to assemble various mold components, such as core inserts, cavity plates, and cooling channels. The high precision of laser welding ensures tight fits and robust joints, crucial for achieving quality molds.
- Material Compatibility: These machines can work with a wide range of mold materials, including metals and alloys commonly used in mold fabrication. This versatility allows for flexibility in material selection while maintaining weld quality.
- Surface Enhancement: It can be used to add or modify surface features of mold components, such as texture or engraving. This capability enhances the functionality and aesthetics of the mold.
- Reduced Post-Processing: Due to its focused energy input and minimal heat-affected zone, laser welding often reduces the need for extensive post-welding machining or finishing. This translates to time and cost savings in the production process.
Components of Laser Welding Machine
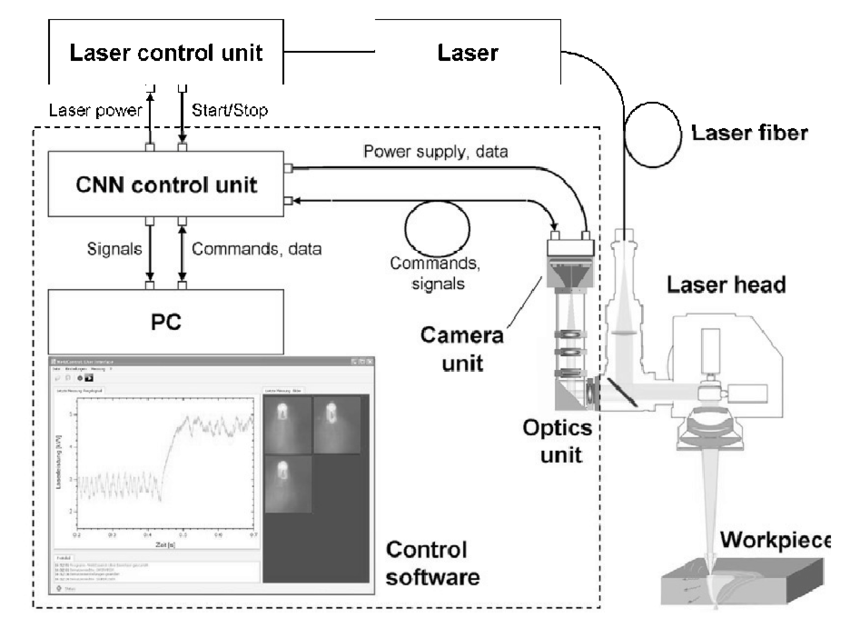
Laser welding machines consist of several essential components that work together to generate and focus a high-energy laser beam for precision welding applications. Here are the key components and their roles –
- Laser Source: The laser source generates the coherent light beam, typically using a laser resonator, which amplifies and focuses the light.
- Beam Delivery System: This system guides the laser beam from the source to the welding head. It includes mirrors, lenses, and fiber-optic cables to ensure precise alignment and focusing of the beam.
- Welding Head: The welding head contains the focusing optics, nozzle, and shielding gas supply. It focuses the laser beam onto the welding point, enabling precise control and energy concentration.
- Workholding System: A fixture or clamp secures the mold components in place during welding. The proper fixation ensures accurate alignment and stability during the welding process.
- Control System: The control system manages various parameters such as laser power, pulse duration, frequency, and welding speed. These settings determine the welding characteristics, influencing the weld quality and joint integrity.
- Cooling System: The laser source generates heat, necessitating a cooling system to prevent overheating. This system maintains the optimal operating temperature of the laser components.
- Safety Measures: Laser welding machines include safety features such as enclosures, interlocks, and protective eyewear to shield operators and bystanders from intense laser light.
- Gas Supply: Shielding gases like argon or helium are often used to protect the weld area from atmospheric contaminants, ensuring clean and strong welds.
- Power Supply: The power supply provides the necessary electrical energy to the laser source, enabling it to generate a high-energy laser beam.
- Fume Extraction System: During welding, fumes, and gases are produced. A fume extraction system removes these byproducts to maintain a clean and safe working environment.
These machines combine these components to create a controlled and precise welding process. This technology’s ability to focus energy accurately onto mold components enables intricate and durable welds, making it a valuable asset in modern manufacturing industries.
Advantages of Laser Welding in Mold Manufacturing
- Precision and Detail: Its pinpoint accuracy suits the intricate designs required for molds. It can mend tiny imperfections with minimal damage to the overall structure.
- Minimal Distortion: Traditional welding methods can introduce distortion due to excessive heat. Laser welding’s localized and controlled heat application reduces this concern, preserving the mold’s shape and dimensions.
- Reduced Post-Processing: The minimal heat-affected zone and precise welds of these often reduce the need for extensive post-weld machining or finishing, saving time and resources.
- Versatility: It is applicable to a wide range of mold materials, including metals and alloys, and can be used for various mold types, from injection to blow molds.
- Automation Integration: It can be easily integrated into automated manufacturing processes, enhancing overall production efficiency.
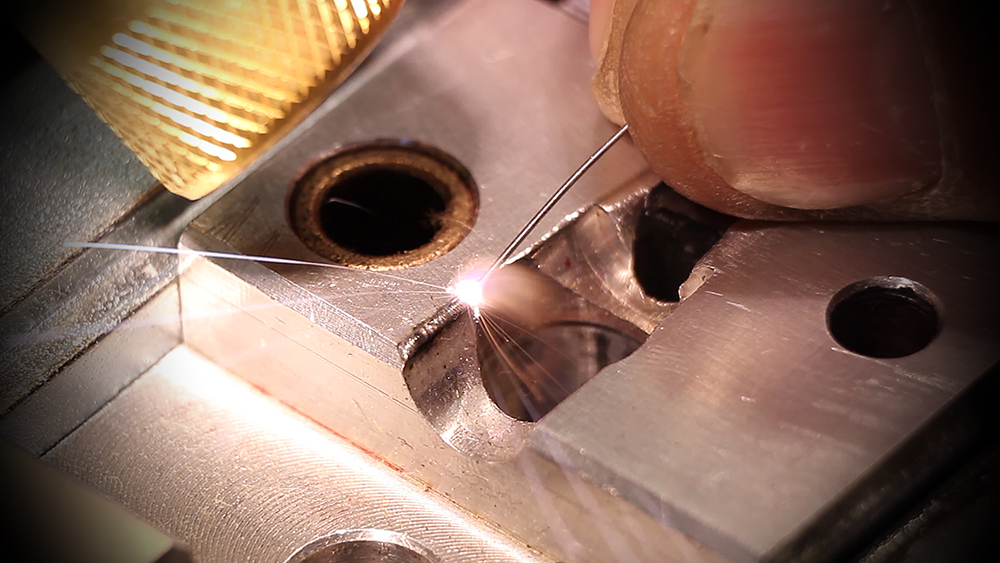
Challenges and Considerations
While these offer numerous advantages in mold manufacturing, it is essential to acknowledge the challenges and considerations associated with this advanced welding technique. These factors can impact the effectiveness and feasibility of using laser welding for mold fabrication.
- Material Compatibility: Different mold materials have varying thermal properties and reflectivity levels, which can affect the efficiency of this type of welding. Some materials might be challenging to weld due to their high reflectivity, making it difficult for the laser to penetrate and create a strong bond. Compatibility assessments are necessary to determine the suitability of laser welding for specific mold materials.
- Precise Setup and Alignment: This type of welding requires precise alignment of the workpieces to ensure accurate welds. The slightest misalignment can lead to compromised joint integrity or inadequate weld quality. Setting up the welding process demands meticulous attention to detail and skilled operators to achieve optimal results.
- Joint Accessibility: Mold designs can involve intricate geometries and hard-to-reach areas, making it challenging for the laser beam to access and weld effectively. Adequate access to the weld joint is essential for ensuring consistent and reliable welds throughout the mold components.
- Thermal Stress and Distortion: This type of welding involves localized heating, which can introduce thermal stress and distortion to the mold components. Minimizing these effects requires careful control of energy input and heat dissipation strategies to prevent warping or dimensional inaccuracies in the finished mold.
- Surface Finish and Aesthetic Concerns: Molds often require precise surface finishes to achieve the desired part quality. This welding can impact the surface appearance of the welded areas, potentially leading to cosmetic issues. Addressing this challenge may involve post-weld machining or finishing to restore the desired surface texture.
- Operator Skill and Training: Operating this welding equipment requires a high level of skill and expertise. Operators must understand the intricacies of the equipment, process parameters, and material interactions to ensure successful welds and avoid defects.
- Equipment Cost and Maintenance: Laser welding equipment can be expensive to acquire and maintain. Regular calibration, maintenance, and occasional repairs are necessary to keep the equipment in optimal working condition. The initial investment and ongoing operational costs should be factored into the decision to adopt laser welding.
- Safety Measures: This welding involves the use of high-intensity light beams that can be harmful to human eyes and skin. Proper safety measures, including protective eyewear and adherence to safety guidelines, are imperative to safeguard operators and other personnel.
- Production Volume and Cost Efficiency: It can be highly efficient for intricate welds and small production runs. However, for high-volume production, the speed and cost-effectiveness of laser welding compared to other welding methods must be evaluated to ensure economic viability.
Pros and Cons
Laser welding has emerged as a promising technology for mold manufacturing, offering distinct advantages and facing certain limitations. Here’s a breakdown of the pros and cons associated with using laser welding for molds.
Pros
- Precision and Accuracy: It provides exceptional precision, enabling the fabrication of intricate mold designs with minimal distortion. This accuracy is vital for molds used in industries demanding complex geometries and high-quality parts.
- Minimal Heat Affected Zone (HAZ): It focused energy input results in a small heat-affected zone, reducing the risk of material distortion, warping, and undesirable changes in material properties. This is crucial for maintaining the exact mold dimensions and mechanical properties.
- Reduced Post-Processing: The minimal HAZ often translates to reduced post-welding machining or finishing requirements, saving time and resources in the production process.
- Versatility: It is applicable to a wide range of mold materials, including metals and alloys, making it suitable for diverse mold manufacturing needs.
- Suitable for Complex Geometries: This type of welding’s pinpoint accuracy allows for welding intricate and hard-to-reach areas in mold components, enabling the production of molds with complex features.
- Joint Integrity: It creates strong and durable bonds, enhancing overall joint integrity and mold longevity.
Cons
- Material Compatibility: These welding may not be suitable for all materials due to variations in reflectivity and thermal properties. Compatibility assessments are crucial to ensure successful welds.
- Setup Precision: Achieving precise alignment of mold components is essential for successful laser welding. Meticulous setup and operator expertise are necessary to ensure accurate welds.
- Joint Accessibility: Welding in tight or hidden spaces can be challenging for laser beams to access, potentially limiting its effectiveness in certain mold designs.
- Thermal Stress and Distortion: Despite minimal HAZ, laser welding can still introduce thermal stress and distortion, especially in larger mold components or those with uneven heat distribution.
- Surface Finish Concerns: These may alter the surface finish of the welded areas, requiring additional post-welding finishing processes to restore the desired texture.
- Operator Skill: Operating this welding equipment demands skilled operators who understand the process parameters, equipment intricacies, and material interactions.
- Equipment Costs: This type of welding equipment can be expensive to acquire and maintain, making it a significant upfront investment. Ongoing maintenance and calibration are necessary for consistent performance.
- Production Volume: While effective for intricate designs and low to medium production volumes, laser welding might not be as efficient for high-volume production due to its cycle time and cost considerations.
Conclusion
These welding techniques have ushered in a new era of precision and efficiency in mold manufacturing. As industries strive for intricate designs, rapid production, and top-tier quality, laser welding stands as a powerful solution that addresses these demands head-on.
With its ability to deliver pinpoint accuracy, minimal distortion, and reduced post-processing requirements, laser welding has redefined the standards of mold fabrication. Whether through Laser Beam Welding (LBW), Fiber Lazer Welding, or hybrid approaches, these techniques offer a level of control and detail that traditional welding methods struggle to achieve.
While challenges such as setup precision and material compatibility exist, advancements in technology and operator expertise continue to mitigate these concerns. The integration of laser welding into automated manufacturing processes further underscores its pivotal role in reshaping the landscape of mold manufacturing.
As industries push the boundaries of design complexity and production speed, the focus keyword, “laser welding,” remains at the forefront of innovative solutions. Its potential to optimize mold manufacturing processes, enhance end-product quality, and drive efficiency ensures that laser welding will continue to play an indispensable role in shaping the future of mold manufacturing across diverse industries.
FAQ’s
What is the process of Laser Welding?
Laser welding is a precision joining process that utilizes a high-energy laser beam to fuse materials together. The process involves focusing the laser beam onto the workpiece’s surface, generating intense heat that melts and welds the materials. As the laser energy is absorbed by the material, it creates a localized molten zone. Once the laser beam is moved or the material solidifies, a solid weld joint forms, bonding the materials together.
The key advantage of laser welding lies in its ability to provide pinpoint accuracy and minimal heat-affected zones. This precision is crucial for applications requiring intricate designs and minimal distortion. The process can be controlled to produce strong, high-quality welds with reduced post-processing requirements. Laser welding is used in various industries, including automotive, aerospace, electronics, and mold manufacturing, where precision, speed, and weld quality are paramount.
What is a Laser Weld?
A laser weld is a fusion of materials created by directing a high-energy laser beam onto its surface. The intense heat generated by the laser melts the materials, which then solidify to form a strong and precise joint. Laser welding is known for its accuracy and minimal heat-affected zones.
What are Laser Welders used for?
Laser welders are used to join materials by directing a high-energy laser beam onto their surfaces. They find applications in industries such as manufacturing, electronics, automotive, and medical devices. Laser welders offer pinpoint accuracy, minimal heat impact, and the ability to weld intricate components, making them ideal for tasks that demand precision, durability, and minimal distortion in the joined materials.
What are the applications of the Laser Welding Process?
The laser welding process finds versatile applications across various industries. It is extensively used in manufacturing precision components for the aerospace, automotive, and electronics sectors. Jewelry-making benefits from its ability to join intricate designs. Medical devices, such as implants and surgical instruments, rely on their precision. Mold fabrication, sensor production, and electronics assembly benefit from clean and precise welds. Moreover, it aids in the repair and refurbishment of worn-out components. The process’s accuracy, minimal heat-affected zones, and suitability for diverse materials make it indispensable for industries requiring intricate, durable, and high-quality welds.
What is the price range of the Laser Welding Machine?
The price range of the machine varies between 750000.00 – 1350000.00 INR (Approx.)