Injection Molding Machines
Injection molding machines are pivotal in modern manufacturing, enabling the efficient production of a wide array of plastic components and products. This versatile technology involves injecting molten plastic material into a mold cavity, where it cools and solidifies to take the desired shape. By exerting high pressure and temperature, these machines ensure precise molding of intricate designs and consistent product quality. Widely used across industries, from automotive to consumer goods, injection molding machines have revolutionized mass production by providing a cost-effective, rapid, and reliable method to shape plastics into functional and aesthetically pleasing end products.

Operations Carried Out on an Injection Molding Machine: A Step-by-Step Guide
Injection molding machines are a cornerstone of modern manufacturing, capable of producing a diverse range of plastic products with high precision. The following step-wise guide outlines the operations involved in the injection molding process –
Step 1: Clamping The process begins with the clamping unit securely closing the mold. This unit holds the two halves of the mold together, ensuring that the mold cavity remains in the correct position during the subsequent steps.
Step 2: Injection Once the mold is clamped, plastic pellets or resin are fed into the machine’s injection unit. The plastic is heated until it becomes a molten state. A screw mechanism within the injection unit then pushes the molten plastic into the mold cavity at high pressure.
Step 3: Dwelling After the mold cavity is filled with molten plastic, there is a brief pause known as the dwelling phase. During this time, the plastic continues to solidify and take on the desired shape within the mold.
Step 4: Cooling Once the dwelling phase is complete, the mold remains closed while the plastic inside begins to cool and harden. The cooling process is crucial for maintaining the integrity and dimensional accuracy of the final product.
Step 5: Mold Opening After the plastic has cooled and solidified, the clamping unit opens the mold. This exposes the newly formed plastic part, which remains attached to one side of the mold.
Step 6: Ejection The ejection system of the machine uses pins or ejector rods to push the plastic part out of the mold cavity. The mold is designed with features that allow the ejection system to remove the part without damaging it.
Step 7: Part Removal Once the part is ejected from the mold, it can be manually or automatically removed from the machine’s workspace. This step is important to ensure a clear workspace for the next molding cycle.
Step 8: Mold Closing With the mold cavity empty, the clamping unit closes the mold in preparation for the next injection cycle.
Step 9: Repeat The entire cycle is then repeated for the production of the next plastic part. Injection molding machines are capable of carrying out these operations continuously and with high precision, making them a cornerstone of efficient and cost-effective manufacturing.
Injection molding machines have revolutionized mass production across various industries, from automotive and electronics to consumer goods. Their ability to consistently create complex shapes with tight tolerances has positioned them as an indispensable tool for modern manufacturing processes.
Types of Injection Molding Machines
There are several types of injection molding machines, each designed for specific applications and production needs.
Hydraulic Injection Molding Machines
- Utilize hydraulic systems to power the machine.
- Suitable for a wide range of materials and applications.
- Known for their versatility and ability to handle high-tonnage operations.
- Slower compared to electric machines but offers strong clamp force.

Electric Injection Molding Machines
- Employ electric servo motors for powering the machine’s movements.
- Energy-efficient and provides precise control over the molding process.
- Ideal for high-precision, intricate, and repeatable molding tasks.
- Faster cycle times and reduced maintenance compared to hydraulic machines.

Hybrid Injection Molding Machines
- Combine elements of both hydraulic and electric machines.
- Benefit from energy efficiency and precision of electric systems while maintaining the power of hydraulic clamping.
- Offer a balance between performance, energy consumption, and cost.

Two-Shot Injection Molding Machines (Dual-Shot or Multi-Material Machines)
- Enable the injection of two different materials or colors into a single mold.
- Useful for producing complex parts with multiple components or over-molded parts.
- Reduces assembly steps and enhances product durability.

All-Electric Injection Molding Machines
- Utilize electric motors for all machine functions, including clamping, injection, and ejection.
- Deliver high precision, energy efficiency, and reduced noise levels.
- Suitable for cleanroom environments and medical applications.

Vertical Injection Molding Machines
- Oriented vertically, with the mold clamping unit located above the injection unit.
- Ideal for insert molding, over-molding, and producing parts with complex geometries.
- Space-saving design and convenient for certain applications.
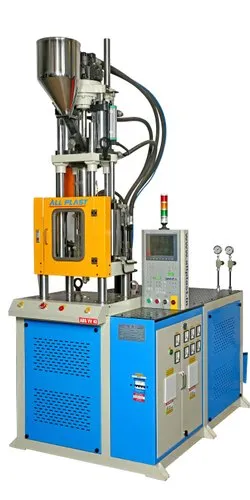
Liquid Silicone Rubber (LSR) Injection Molding Machines
- Specifically designed for processing liquid silicone rubber.
- Provide exceptional accuracy and consistency for producing medical and consumer goods.
- Offer precise control over material curing and temperature.
Multi-Material Injection Molding Machines
- Enable the molding of parts with multiple materials in a single cycle.
- Useful for creating products with distinct properties or appearances.
- Widely used in automotive and consumer electronics industries.
Gas-Assisted Injection Molding Machines
- Introduce inert gas into the mold during the molding process.
- Reduce material usage, decrease warpage, and enhance surface finish.
- Suitable for large and thin-walled parts.
Micro-Injection Molding Machines
- Each type of injection molding machine caters to different production requirements and material characteristics, allowing manufacturers to choose the most suitable option for their specific applications.
Components of Injection Molding Machines
Certainly, here’s a detailed explanation of the key components of injection molding machines, outlined in a point-wise format –

Clamping Unit
- Movable Platen: The part of the clamping unit that moves to open and close the mold.
- Fixed Platen: The stationary counterpart that supports the mold during clamping.
- Tie Bars: Strong metal rods that connect the movable and fixed platens, providing stability.
- Clamping Cylinder: Generates the force needed to hold the mold closed during injection.
Injection Unit
- Screw: Driven by a motor, the screw moves forward to melt and inject plastic material into the mold.
- Barrel: The heated chamber where plastic pellets are fed and melted by the rotating screw.
- Nozzle: Connects the end of the barrel to the mold, enabling the injection of molten plastic.
Hydraulic System
- Hydraulic Pump: Generates hydraulic pressure to power various machine movements.
- Valves: Control the flow of hydraulic fluid to different components.
- Accumulator: Stores hydraulic pressure for quick and powerful movements.
- Hydraulic Reservoir: Stores hydraulic fluid for the system.
Electric System
- Servo Motors: Drive various machine movements, providing precise control and energy efficiency.
- Controllers: Manage and regulate the machine’s operations, allowing operators to set parameters.
- Sensors: Monitor various parameters such as temperature, pressure, and position.
Ejector System
- Ejector Pins/Rods: Push the molded part out of the mold cavity after cooling.
- Ejector Plate: Mechanism that moves the ejector pins/rods to perform ejection.
Cooling System
- Water Circuits: Channels water to cool the mold and maintain proper temperatures.
- Cooling Lines: Passageways for coolant to flow within the mold.
Heating System
- Heating Bands: Wrapped around the barrel and other components to maintain precise temperatures for melting plastic.
Mold
- Cavity and Core: The two halves of the mold that shape the plastic into the desired product.
- Sprue, Runners, and Gates: Channels that guide molten plastic from the injection unit to the mold cavity.
- Ejector Pins: Push the finished part out of the mold after it’s cooled.
Safety Features
- Emergency Stop Buttons: Instantly halt machine operations.
- Safety Interlocks: Prevent certain actions if safety conditions aren’t met.
- Guards and Enclosures: Physical barriers to protect operators from moving parts.
Control Panel
- Touchscreen Interface: Allows operators to input settings and monitor the molding process.
- Control Buttons: Enable manual control over specific actions.
Material Hopper and Dryer
- Material Hopper: Stores plastic pellets that are fed into the injection unit.
- Dryer: Removes moisture from plastic pellets before they’re melted.
Robot and Automation Mounting Points
These components work in harmony to execute the injection molding process, transforming raw materials into finished plastic products with precision and efficiency.
Injection Molding Machine Tonnage
Injection molding machine tonnage refers to the clamping force that the machine can exert on the mold to keep it securely closed during the injection molding process. It is measured in tons or kilonewtons (kN) and indicates the machine’s capacity to hold the mold closed against the pressure generated by the molten plastic as it’s injected into the mold cavity.
Here’s how injection molding machine tonnage works and its significance –

Clamping Force and Tonnage
- Clamping force is the force applied by the machine’s clamping unit to keep the mold halves together during injection, cooling, and ejection.
- Tonnage is the measure of this clamping force. One ton of clamping force is equivalent to applying a force of 2,000 pounds.
Selecting the Right Tonnage
- The appropriate machine tonnage depends on factors such as the size and complexity of the part being produced, the material being used, and the design of the mold.
- Larger and more complex parts typically require higher tonnage machines to withstand the pressure exerted by the molten plastic.
Tonnage and Mold Size
- The tonnage required is influenced by the projected area of the part being molded, the number of cavities in the mold, and the complexity of the mold design.
- Larger molds or molds with multiple cavities require more clamping force to ensure proper part formation.
Safety Margin
- It’s common practice to select a machine with slightly higher tonnage than is strictly necessary to accommodate unexpected factors like material variations, mold wear, and changes in process conditions.
- Having a safety margin helps prevent issues like flashes, short shots, and other molding defects.
Injection Molding Machine Range
- Injection molding machines are available across a wide tonnage range, from a few tons to thousands of tons.
- Smaller machines are suitable for producing small parts, while larger machines are used for producing bigger parts or multiple parts simultaneously.
Balancing Tonnage and Machine Size
- Properly matching the injection molding machine tonnage to the requirements of the specific production job is crucial for achieving consistent and high-quality results. Selecting the right tonnage ensures that the machine can exert the necessary clamping force to prevent defects like flash, sink marks, and warping, resulting in optimal part quality.
Makers of Injection Molding Machines
Here are 10 notable makers of injection molding machines –
- Haitian International Holdings Limited: A Chinese company known for its large range of injection molding machines and strong global presence.
- Chen Hsong Holdings Limited: Another prominent Chinese manufacturer, Chen Hsong is recognized for its quality machines and technological advancements.
- ENGEL Austria GmbH: An Austrian company with a global footprint, ENGEL is known for its high-performance and technologically advanced injection molding machines.
- ARBURG GmbH + Co KG: Based in Germany, ARBURG is a leading manufacturer with a wide range of machine types and innovative technologies.
- Sumitomo (SHI) Demag Plastics Machinery GmbH: This German-Japanese collaboration produces high-quality injection molding machines and offers innovative solutions.
- KraussMaffei Group: A German manufacturer that provides injection molding machines and other equipment for various industries.
- JSW Plastics Machinery Inc.: A Japanese company known for its advanced technologies and large-tonnage injection molding machines.
- Nissei Plastic Industrial Co., Ltd.: A Japanese manufacturer with a global presence, Nissei is recognized for its precision and high-speed injection molding machines.
- Milacron Holdings Corp.: A U.S.-based company offering a wide range of injection molding machinery, including advanced technologies for various industries.
- Toyo Machinery & Metal Co., Ltd.: A Japanese company with a strong focus on research and development, producing advanced injection molding machines.
Applications of Injection Molding Machines
Injection molding machines find a wide range of applications across various industries due to their versatility, efficiency, and ability to produce complex parts with precision. Here are some notable applications –
Automotive Industry
- Injection molding produces components such as dashboards, interior panels, door handles, and exterior trim.
- Critical safety components like airbags and sensor housings are also manufactured using injection molding.

Consumer Goods
- Common everyday items like bottles, containers, toys, and electronic device casings are made using injection molding.
- Cosmetic and personal care products, such as caps and packaging, are also produced this way.

Medical and Healthcare
- Injection molding creates medical devices, equipment, and consumables, including syringes, vials, IV connectors, and surgical tools.
- Components for diagnostic equipment, drug delivery systems, and medical packaging are also manufactured using this process.

Electronics
- Cases, housings, and components for electronic devices such as smartphones, laptops, and appliances are produced using injection molding.
- Connectors, cable management systems, and precision components also benefit from this process.

Packaging
- Thin-walled packaging items like containers, lids, caps, and closures are commonly manufactured using injection molding.
- The process is efficient for producing high volumes of uniform packaging products.

Aerospace and Defense
- Injection molding is used to create components for aerospace interiors, aircraft seating, and control panels.
- Military equipment, such as firearm parts and protective gear, can also be manufactured using this method.

Appliances
- Injection molding produces parts for appliances like washing machines, refrigerators, and air conditioners.
- Components such as knobs, handles, and control panels are commonly made using this process.

Toys and Games
- Plastic toys, puzzles, game pieces, and action figures are often manufactured using injection molding.
- The process allows for intricate designs and vibrant colors, appealing to children and collectors.
The versatility of injection molding machines, combined with their capability to create high-quality and cost-effective parts, makes them a staple in numerous industries, contributing to the production of an extensive array of products that shape our modern world.

Molding Defects & Their Troubleshooting
Molding defects can occur during the injection molding process and can affect the quality and functionality of the final product. Troubleshooting these defects is essential to ensure consistent and high-quality production. Here’s an explanation of common molding defects and their troubleshooting steps in a point-wise format:
**1. Sink Marks:
- Defect: Indentations or depressions on the surface of the part due to shrinkage during cooling.
- Troubleshooting:
- Increase injection pressure to pack more material into the mold.
- Raise melt temperature to reduce material viscosity.
- Adjust cooling time or position to minimize differential cooling.

**2. Warping:
- Defect: The part distorts from its intended shape due to uneven cooling or material distribution.
- Troubleshooting:
- Optimize cooling system design to ensure even cooling.
- Adjust mold temperature and injection parameters for uniform material flow.
- Use proper mold release agents to prevent sticking.

**3. Flash:
- Defect: Excess plastic material that escapes from the mold cavity and forms thin edges or protrusions.
- Troubleshooting:
- Increase clamping force to prevent mold separation.
- Check for worn or damaged mold components causing leaks.
- Adjust injection speed and pressure for controlled material flow.

**4. Short Shots:
- Defect: The part is not completely filled, resulting in incomplete or short parts.
- Troubleshooting:
- Increase melt temperature to improve material flow.
- Raise injection pressure to pack the mold cavity fully.
- Check for blocked or insufficiently sized gates and runners.

**5. Jetting:
- Defect: Jet-like appearance on the surface of the part due to poor material flow and inadequate fusion.
- Troubleshooting:
- Increase injection speed to improve material flow and fusion.
- Adjust gate size and position for smoother material entry.
- Modify part design to ensure proper material distribution.

**6. Burn Marks:
- Defect: Dark or discolored areas on the part caused by excessive heat during molding.
- Troubleshooting:
- Reduce melt temperature to prevent material degradation.
- Optimize cycle time to avoid extended material exposure to heat.
- Vent the mold adequately to allow trapped air to escape.
**7. Voids/Bubbles:
- Defect: Air pockets or voids trapped within the part due to incomplete material filling or gas release.
- Troubleshooting:
- Increase injection pressure and speed to ensure complete material filling.
- Check for adequate venting to allow air to escape during molding.
- Adjust melt temperature to prevent gas entrainment.

**8. Flow Lines:
- Defect: Visible lines or streaks on the part surface caused by material flow variations.
- Troubleshooting:
- Increase melt temperature for better material flow and fusion.
- Optimize gate placement to ensure uniform material distribution.
- Adjust injection speed and pressure for consistent flow.
Addressing these molding defects requires a systematic approach, involving adjustments to process parameters, mold design, material selection, and even the equipment itself. Regular monitoring and process optimization are essential to maintaining consistent and defect-free production.
Conclusion
Injection molding machines stand as the backbone of modern manufacturing, revolutionizing the way we produce plastic parts and products across various industries. These machines, through their intricate processes and precision engineering, enable the transformation of raw materials into complex, functional, and aesthetically appealing components that shape our world. Their ability to create parts ranging from the smallest intricate details to large, robust structures showcases their adaptability and versatility.
The injection molding process, driven by clamping force, temperature control, and material manipulation, embodies the synergy of technology, innovation, and engineering expertise. It has enabled advancements in sectors as diverse as automotive, healthcare, consumer goods, electronics, and beyond, touching every aspect of our daily lives.
As industries continue to evolve, injection molding machines are poised to evolve with them. Advancements in materials, automation, and process optimization continue to refine the injection molding process, enhancing efficiency, minimizing waste, and improving product quality. In an era of sustainability and rapid innovation, injection molding machines will remain pivotal in propelling us toward a future where manufacturing is efficient, eco-friendly, and attuned to the ever-changing demands of the global market.
FAQ’s
What is an Injection Molding Machine?
An Injection Molding Machine is a manufacturing device used in the process of injection molding, which is a widely used method for producing plastic parts and products. It is a process where molten plastic material is injected into a mold cavity, where it cools and solidifies to take on the shape of the mold. Injection molding is commonly used for producing a wide range of products, from small components to large automotive parts and everything in between.
The common components of an injection molding machine –
Hopper: This is where plastic pellets (or granules) are loaded into the machine. The plastic material is melted down into a liquid state before being injected into the mold.
Heating Unit: The plastic pellets are heated using heating elements until they melt and become a viscous liquid. This molten plastic is then ready for injection.
Injection Unit: The melted plastic is pushed or injected into a mold under high pressure. The injection unit consists of a screw or a reciprocating plunger that helps move the molten plastic material into the mold.
Mold: The mold is a carefully crafted tool that defines the shape and features of the final product. It consists of two halves: the stationary side and the moving side. The melted plastic is injected into the mold cavity, and when it cools and solidifies, the mold is opened to eject the finished part.
Clamping Unit: This unit holds the mold halves together with sufficient force to withstand the high pressure of the molten plastic being injected. It ensures that the mold remains closed during injection and cooling.
Cooling System: After the plastic is injected into the mold and takes on its intended shape, a cooling system helps to rapidly cool down the plastic, allowing it to solidify and retain its shape.
Ejection System: Once the plastic part has solidified within the mold, the mold is opened, and an ejection system helps remove the finished part from the mold cavity.
Modern injection molding machines are often automated and equipped with sophisticated control systems that regulate the temperature, pressure, and other variables to ensure consistent quality and precise manufacturing. The machines can handle various types of plastic materials, including thermoplastics and some thermosetting plastics.
Injection molding is a highly efficient and versatile manufacturing process, enabling the production of intricate and complex parts with high precision and repeatability. It finds applications in various industries, such as automotive, consumer goods, electronics, medical devices, and more.
How to select Injection Molding Machine?
Selecting the right injection molding machine involves considering several key factors to ensure that the machine meets your production requirements and produces high-quality parts. Here are the steps you should follow when selecting an injection molding machine:
Part Design and Size: Understand the design and size of the parts you intend to produce. Consider factors such as part geometry, wall thickness, and any intricate features. The size of the parts will help determine the appropriate clamping force and mold size needed.
Material Compatibility: Different plastics have varying properties, including melting points, viscosity, and flow characteristics. Choose a machine that is compatible with the specific type of plastic material you’ll be using. Make sure the machine’s barrel, screw, and heating system are suitable for the chosen material.
Production Volume: Determine the expected production volume. High-volume production might require a more robust and efficient machine. Low-volume production might allow for a smaller machine with lower operational costs.
Clamping Force: Clamping force is the pressure applied to hold the mold closed during injection and cooling. It is determined by the size and complexity of the parts. A machine with the right clamping force ensures proper part formation and minimizes defects.
Shot Size: The shot size refers to the maximum amount of plastic the machine can inject into the mold in one cycle. It should be sufficient to fill the mold cavities adequately without overfilling or underfilling.
Injection Rate and Pressure: Consider the required injection rate and pressure for your specific parts. These parameters influence the flow of plastic material into the mold and affect part quality.
Mold Compatibility: Ensure that the machine can accommodate the size and configuration of the mold you plan to use. This includes the mold’s dimensions and any special features it may have.
Automation and Control: Modern injection molding machines offer various levels of automation and control. Consider the level of automation needed for your production process, including features like robotics, real-time monitoring, and data collection.
Energy Efficiency: Look for machines with energy-efficient features, as they can significantly impact operating costs over the long term. Efficient heating, cooling, and motor systems can save energy and reduce operational expenses.
Manufacturer Reputation and Support: Choose a reputable manufacturer known for producing reliable and high-quality machines. Good customer support, maintenance services, and readily available spare parts are essential considerations.
Budget: Determine your budget for acquiring the injection molding machine. Consider not only the upfront cost but also the ongoing operational and maintenance expenses.
Future Expansion: Factor in the possibility of expanding your production in the future. Choosing a machine with some room for scalability can save you from needing to invest in a new machine as your production needs grow.
Consult Experts: If you’re new to injection molding, consider consulting with experts or professionals who have experience in the field. They can provide valuable insights and guidance in selecting the right machine for your needs.
By carefully considering these factors and conducting thorough research, you can select an injection molding machine that aligns with your production goals and ensures the quality and efficiency of your manufacturing process.
How does an Injection Molding Machine work?
An Injection Molding Machine works by melting plastic pellets and injecting the molten material into a mold to create a desired shape.
Material Loading: Plastic pellets are loaded into a hopper on the machine.
Melting: The pellets are fed into a heated barrel, where they are gradually melted by heating elements.
Injection: Once the plastic is molten, a screw or plunger pushes it into a mold under high pressure. The mold is made up of two halves: a stationary half and a moving half.
Cooling: The molten plastic takes the shape of the mold’s cavities. Cooling systems help solidify the plastic within the mold.
Ejection: After cooling and solidification, the mold is opened, and the finished part is ejected from the mold using ejector pins or other mechanisms.
Repeat: The mold closes again, and the process repeats for the next cycle.
Key components like the clamping unit, injection unit, and control systems work together to ensure precise temperature, pressure, and timing controls, resulting in consistent and accurate production of plastic parts.