Introduction
When it comes to achieving impeccable quality in mold finishing, precision and expertise are paramount. Mold polishing is a crucial step in the manufacturing process, as it ensures that the final product meets the highest standards. While various methods and tools exist for mold polishing, one substance stands out as the ultimate partner in achieving unrivaled quality – diamond paste. In this article, we will delve into the world of diamond paste and explore how it has become an indispensable tool for mold polishing professionals.
What is Diamond Paste and how it works for Mold Polishing?
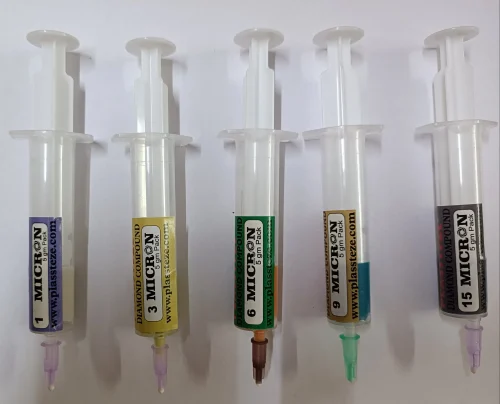
Diamond paste is a specialized abrasive compound that contains tiny diamond particles suspended within a paste-like carrier medium. This unique composition makes it an exceptionally effective tool for achieving high-precision and high-quality finishes in various industries, including mold polishing.
Here’s how diamond paste works for mold polishing –
- Composition: Diamond paste is composed of two main components: diamond particles and a carrier medium. The diamond particles are microscopically small, ranging in size from nanometers to micrometers, and they are typically industrial-grade diamonds. The carrier medium can be oil-based or water-based, and its purpose is to hold and evenly distribute the diamond particles.
- Hardness: Diamonds are renowned for their exceptional hardness. In fact, they are the hardest known natural material on Earth. This extreme hardness gives diamond paste its cutting ability. When applied to a surface, the diamond particles in the paste abrade the material, effectively removing imperfections, scratches, and other surface irregularities.
- Uniform Distribution: The key to diamond paste’s effectiveness is the uniform distribution of diamond particles throughout the carrier medium. This ensures consistent abrasion and prevents uneven wear on the polishing tool and the workpiece, resulting in a smoother finish.
- Selecting the Right Grit: Diamond paste is available in various grit sizes, which determine the coarseness of the abrasive action. Coarser grits are used for initial material removal, while finer grits are employed to refine the surface to a high degree of smoothness. The choice of grit depends on the level of finish required and the type of material being polished.
- Application Techniques: Diamond paste is typically applied to a polishing tool, such as a felt bob, a cloth pad, or a polishing wheel. The paste-coated tool is then used to work on the surface of the mold in a controlled and systematic manner. The pressure, speed, and duration of the polishing process can be adjusted to achieve the desired results.
- Gradual Progression: Mold polishing with diamond paste is usually done in multiple stages, progressing from coarser to finer grits. Each stage removes imperfections left by the previous one, gradually improving the surface quality.
- Inspection and Quality Control: Regular inspection and quality control checks are essential to ensure that the desired finish is achieved throughout the polishing process. Any remaining imperfections can be addressed with finer grits or additional polishing passes.
What is the composition of Diamond Paste?
Diamond paste is composed of two primary components diamond particles and a carrier medium. The composition may vary slightly depending on the specific brand or manufacturer, but the fundamental elements remain consistent –
- Diamond Particles: The key ingredient in diamond paste is, of course, diamond. However, these are not the large, gem-quality diamonds you might associate with jewelry. Instead, industrial-grade diamonds are used. These diamonds are typically synthetic and have been specially engineered for their abrasive properties. They are processed to produce extremely small, uniform particles ranging in size from nanometers to micrometers. These microscopic diamonds serve as the abrasive agents in the paste.
- Carrier Medium: The diamond particles are suspended within a carrier medium, which gives the paste its paste-like consistency. There are two main types of carrier mediums used in diamond paste:a. Oil-Based: In oil-based diamond paste, the carrier medium is typically a mineral oil or a synthetic oil. Oil-based diamond paste is suitable for applications where water might cause corrosion or is not compatible with the materials being polished.b. Water-Based: Water-based diamond paste uses water as the carrier medium. This type is often chosen when water is readily available, and it is compatible with the workpiece material. Water-based diamond paste is also easier to clean up after use compared to oil-based versions.
The carrier medium’s role is to hold the diamond particles in suspension and evenly distribute them throughout the paste. This uniform distribution ensures consistent abrasive action during the polishing process.
Additionally, some variations of diamond paste may include additives or compounds to enhance specific properties, such as lubricity, flow, or stability. These additives are typically chosen to improve the paste’s performance in specific applications.
The choice between oil-based and water-based diamond paste depends on factors like the type of workpiece material, environmental considerations, and personal preferences. Both types are widely used in various industries for tasks like mold polishing, metal finishing, and fine abrasive applications, where precision and surface quality are essential.
Types of Diamond Paste Based on Diamond Particles
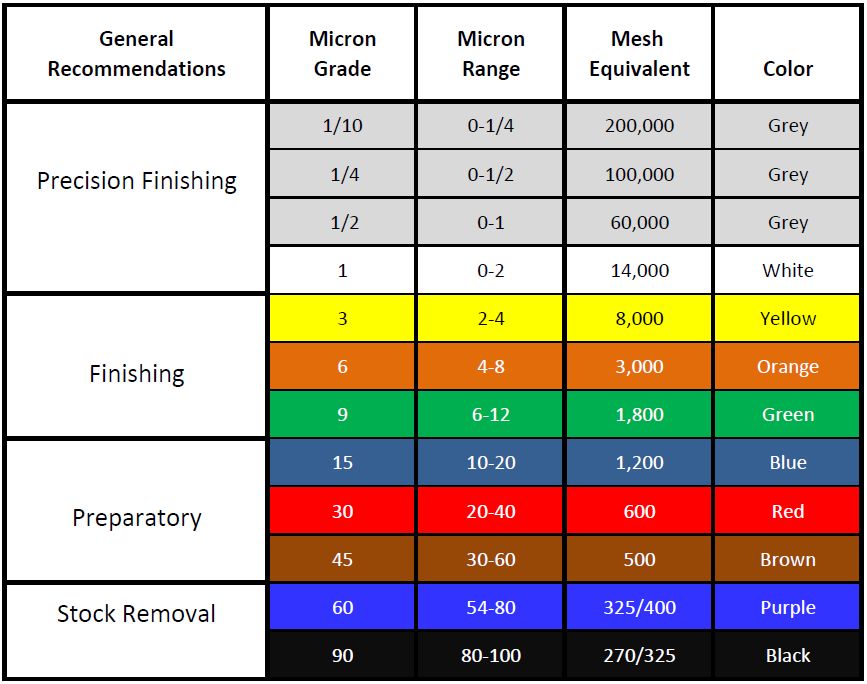
Diamond paste comes in various types based on the size of the diamond particles, which are typically measured in microns (μm) or mesh size. Different types of diamond paste are used for specific applications and surface finish requirements. Here’s an explanation of diamond paste types based on micron size –
- Coarse Diamond Paste (30-45 μm)
- Coarse paste contains larger diamond particles, typically ranging from 30 to 45 microns in size.
- It is used for initial lapping and stock removal processes when a relatively rough surface finish is acceptable.
- Applications include flattening or lapping surfaces, removing scratches, and preparing workpieces for finer polishing.
- Medium Diamond Paste (15-30 μm)
- Medium paste contains smaller diamond particles, typically ranging from 15 to 30 microns in size.
- It is used for intermediate polishing stages when a smoother surface is required after coarse lapping.
- Applications include achieving finer surface finishes on various materials, such as metals, ceramics, and optics.
- Fine Diamond Paste (6-15 μm)
- Fine paste consists of smaller diamond particles, usually ranging from 6 to 15 microns in size.
- It is used for achieving high-quality surface finishes, removing fine scratches, and preparing surfaces for final polishing.
- Applications include polishing precision components, optical lenses, and semiconductor substrates.
- Very Fine Diamond Paste (3-6 μm)
- Very fine paste contains even smaller diamond particles, typically ranging from 3 to 6 microns in size.
- It is used for fine polishing and achieving mirror-like finishes on a wide range of materials.
- Applications include polishing optical components, glass, and precision bearings.
- Ultra-Fine Diamond Paste (<3 μm)
- Ultra-fine paste consists of extremely small diamond particles, often less than 3 microns in size.
- It is used for the final stages of polishing to attain exceptional surface smoothness and optical clarity.
- Applications include the polishing of optical lenses, semiconductors, and high-precision components where sub-micron surface finishes are required.
Selecting the appropriate diamond paste type depends on the specific finishing requirements of the workpiece and the desired surface quality. Manufacturers and technicians often use a series of diamond pastes with progressively finer grit sizes to achieve the desired level of precision and surface finish.
Advantages of Using Diamond Paste
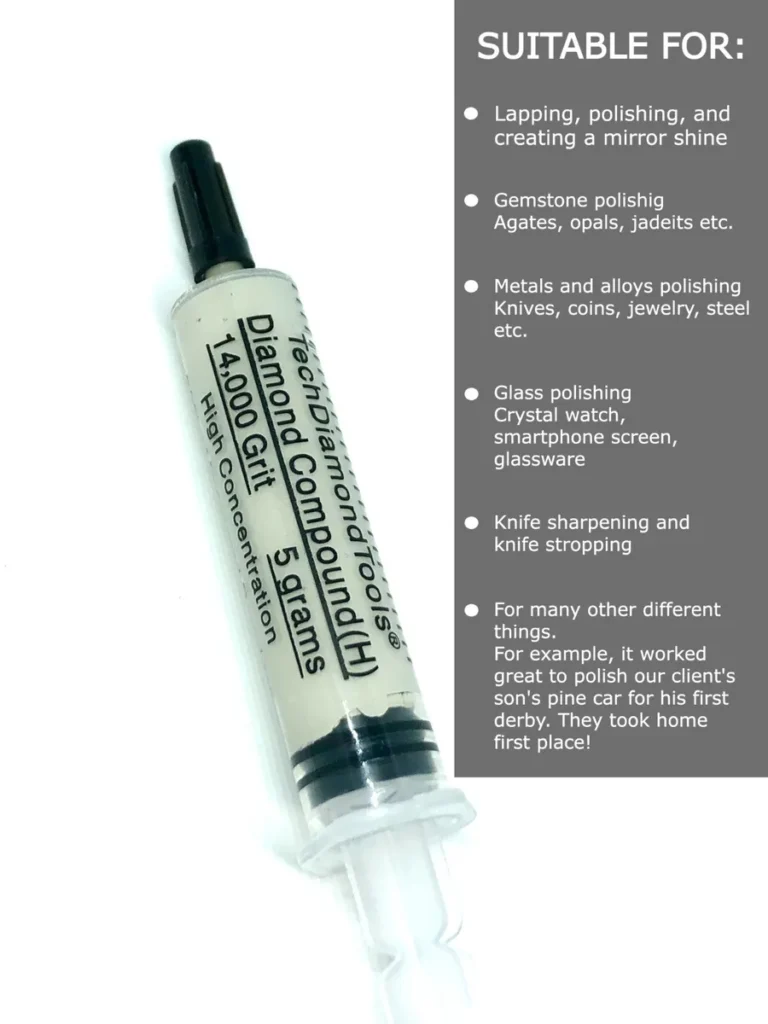
Using diamond paste for mold polishing offers several distinct advantages –
1. Superior Finish: Diamond paste consistently delivers a mirror-like finish with minimal defects, ensuring high-quality mold surfaces.
2. Time Efficiency: Compared to traditional methods, diamond paste significantly reduces polishing time, increasing overall production efficiency.
3. Cost-Effective: Although diamond paste is an investment, its longevity and effectiveness make it a cost-effective choice in the long run.
4. Versatility: Diamond paste can be used for various mold types and materials, making it a versatile tool in the manufacturing industry.
Manufacturers and Suppliers of Diamond Paste
Here are some well-known manufacturers and suppliers –
- Anand Gems
- Plassteze
- Abrasive Technology India
- Diamond International
- Mascot Tools
- Veer-O-Metals
- Techno Tools Corporation
- Super Abrasives
- Solar Diamond Tools
Conclusion
In the world of mold polishing, quality is non-negotiable. Diamond paste has emerged as the preferred partner for achieving the highest standards of finish and precision. Its exceptional hardness, consistency, and versatility make it an indispensable tool for mold polishing professionals. By understanding the polishing process and leveraging the advantages of diamond paste, manufacturers can ensure that their products meet unrivaled quality standards, setting them apart in their respective industries.
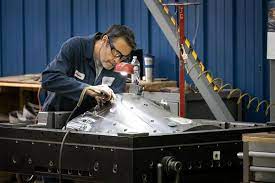
FAQ’s
What is Diamond Lapping and Polishing Paste?
Diamond lapping and polishing paste is an abrasive compound used in the final stages of precision machining and finishing processes. It consists of tiny diamond particles suspended in a lubricating liquid or paste. This compound is applied to a workpiece’s surface, such as metal, glass, ceramics, or semiconductors, and is used with polishing pads or cloth.
Here’s a brief explanation of diamond lapping and polishing paste –
Abrasive Particles: Diamond particles are tough and have sharp edges. They are graded for size, with finer particles used for polishing and coarser ones for lapping.
Lubricating Medium: The diamond particles are suspended in a lubricating medium, often a water-based or oil-based paste. This medium helps carry away debris and prevents overheating during the polishing process.
Application: The paste is applied to the workpiece’s surface, and the workpiece is pressed against a rotating polishing pad or cloth. The abrasive action of the diamond particles gradually removes material from the workpiece, smoothing out imperfections and creating a polished finish.
Precision Finishing: Diamond lapping and polishing paste are commonly used in industries requiring high precision, such as optics, electronics, and semiconductor manufacturing. They are used to achieve tight tolerances and mirror-like surface finishes.
Versatility: Diamond paste is available in various grit sizes, allowing users to select the appropriate paste for their specific finishing needs. Coarser grits are used for lapping, while finer grits are used for polishing.
Final Touch: Diamond lapping and polishing paste are often the last steps in the manufacturing process, ensuring that the workpiece meets stringent quality and surface finish requirements.
Write the list of items required for Diamond Polishing.
Diamond polishing, particularly for achieving high-precision finishes on various materials, requires specific tools and equipment. Here is a list of items typically required for diamond polishing:
Diamond Polishing Paste: Diamond paste containing diamond particles of various sizes, depending on the desired surface finish and the specific application.
Polishing Laps or Wheels: These are rotating discs or wheels made of various materials, such as metal or composite materials, used to hold the workpiece and apply the diamond paste.
Polishing Pads or Cloths: Flexible pads or cloths made of materials like felt, cloth, or resin, which hold the diamond paste and are used for hand polishing or in conjunction with polishing laps or wheels.
Lapping Machine or Polishing Equipment: Precision machinery designed for holding and rotating the workpiece while applying diamond paste. These machines provide controlled pressure, speed, and motion for consistent polishing.
Workpiece Holders: Fixtures or clamps that securely hold the workpiece in place during polishing, ensuring stability and precision.
Polishing Compound Dispensers: Containers or dispensers for storing and applying diamond paste to the polishing laps, pads, or wheels.
Cleaning Equipment: Solvents, ultrasonic cleaners, or other cleaning solutions to remove residual diamond paste and contaminants from the workpiece after polishing.
Microscopes or Inspection Equipment: High-resolution microscopes or inspection tools for examining the polished surface to assess the quality and surface finish.
Safety Equipment: Safety glasses, gloves, and appropriate protective gear to ensure operator safety when handling diamond paste and using polishing equipment.
Ventilation System: Adequate ventilation to minimize exposure to fine dust particles generated during the polishing process.
Workspace: A clean and well-organized workspace with sufficient lighting to facilitate the polishing process and inspection of the workpiece.
Polishing Compound Storage: Proper storage containers or cabinets for diamond paste to prevent contamination and ensure longevity.
Measurement Tools: Precision measuring instruments, such as calipers or surface profilometers, for evaluating the surface finish and ensuring it meets specified requirements.
Cleaning and Maintenance Supplies: Cleaning brushes, lint-free cloths, and maintenance tools for keeping the polishing equipment and workspace clean and well-maintained.
Personal Protective Equipment (PPE): In addition to safety gear, it’s essential to have PPE, including lab coats or aprons, to protect against splatters and contaminants.
The specific items required may vary depending on the nature of the workpiece, the material being polished, and the level of precision needed. Additionally, it’s important to follow safety guidelines and best practices when working with diamond polishing materials and equipment to ensure both the quality of the finished product and the safety of operators.
What are the techniques of diamond polishing?
Diamond polishing is a precision finishing technique used to achieve exceptionally smooth and high-quality surfaces on a variety of materials, including metals, ceramics, glass, and semiconductors. Several techniques are commonly employed in diamond polishing –
Hand Polishing:
Hand polishing involves applying diamond paste directly onto the workpiece using a soft polishing cloth or pad.
The operator manually rubs or moves the workpiece against the cloth in a controlled manner.
This technique is suitable for small and intricate parts or for achieving specific localized finishes.
Rotary Polishing:
Rotary polishing utilizes a rotating lap or wheel that holds the workpiece and applies diamond paste.
The workpiece is pressed against the rotating lap, and the diamond paste is continuously dispensed onto the surface.
This technique is commonly used for achieving uniform finishes on larger or symmetrical parts.
Reciprocating Polishing:
Reciprocating polishing involves a back-and-forth motion of the workpiece against a fixed lap or polishing pad.
Diamond paste is applied to the polishing pad, and the reciprocating action ensures even distribution and consistent polishing.
Ultrasonic Polishing:
Ultrasonic polishing uses ultrasonic vibrations to enhance the polishing process.
The workpiece is placed in a tank of abrasive slurry (containing diamond particles) and subjected to high-frequency vibrations.
The rapid movement of the abrasive particles on the workpiece surface aids in material removal and polishing.
Vibratory Polishing:
Vibratory polishing involves placing the workpiece, along with abrasive media and diamond paste, into a vibratory tumbler or bowl.
The vibratory action of the equipment causes the media and diamond paste to interact with the workpiece, resulting in polishing and material removal.
Chemical Mechanical Polishing (CMP):
CMP is a specialized technique used in semiconductor manufacturing and optics.
It combines chemical reactions and mechanical abrasion to polish and planarize surfaces.
Diamond abrasive particles are often embedded in a polishing pad, and a chemical slurry is applied to aid in material removal.
Single-Pass and Multi-Step Polishing:
Depending on the desired surface finish, polishing may involve a single-pass or multiple steps with progressively finer diamond pastes.
Starting with a coarser diamond paste and gradually transitioning to finer pastes helps achieve a mirror-like finish.
Edge Polishing:
Edge polishing focuses on refining the edges of workpieces, such as glass or optical lenses.
Specialized equipment and techniques are used to ensure precise edge profiles and surface quality.
In-Situ Polishing:
In certain applications, such as the aerospace industry, in-situ polishing is used to maintain and repair surfaces without disassembling components.