Introduction
Blow molding is a highly versatile manufacturing process that plays a pivotal role in producing a wide range of plastic products. It is a technique that allows for the creation of hollow objects, such as bottles, containers, and automotive components, by utilizing the forces of pressure and heat to shape molten plastic materials. With its ability to produce large quantities of lightweight and durable products, blow molding has become an integral part of various industries, including packaging, automotive, and consumer goods.
Overview of Blow Molding
It is a manufacturing process that creates hollow plastic parts by inflating a tube-like piece of plastic called a parison or preform inside a mold. Parisons or preforms are made by melting plastic and extruding it through a hole or injecting it onto a core pin. Compressed air is then used to blow the plastic into the shape of the mold cavity.
There are three main types of blow molding: extrusion blow molding, injection blow molding, and injection stretch blow molding. Blow molding is widely used to produce bottles, containers, toys, automotive parts, and other hollow products.
History of Blow Molding
The history of this type of molding can be traced back to the ancient art of glassblowing, which was practiced by the Syrians in the first century BC. They discovered that a glass bulb on the end of a blowpipe could be shaped into various hollow forms by blowing air into it. The first use of a plastic material other than glass for blow molding was natural rubber, which was patented by Samuel Armstrong in the 1850s. However, it was not until the 1930s that the first blow molding machine was developed by Plax Corporation, using cellulose acetate as the raw material.
In the 1940s, Imperial Chemical Industries (ICI) developed low-density polyethylene (LDPE), which was suitable for making squeeze bottles. In 1950, Kautex Werke introduced the first commercially available blow molding equipment, using a rising mold technique with a continuously extruded open-ended parison. In the 1970s, polyethylene terephthalate (PET) was developed and used for making biaxially oriented bottles for carbonated beverages. The process involved two steps: making a preform on one machine and blowing it into a bottle on another machine.
Today, blow molding is a widely used process for making various hollow plastic products, such as bottles, containers, toys, automotive parts, and more. It has evolved into three main types: extrusion blow molding, injection blow molding, and injection stretch blow molding.
Working Process of Blow Molding । Blow Molding Process Step By Step Guides
Plastic Material Preparation
The blow molding process begins with selecting the appropriate plastic material, such as polyethylene (PE), polypropylene (PP), or polyethylene terephthalate (PET). The plastic material is typically in the form of small pellets or granules.
Melting the Plastic
The plastic material is melted in an extruder, which consists of a heated barrel and a screw mechanism. The plastic pellets are fed into the extruder, and as they move through the barrel, they are heated and gradually melted into a molten state. The screw mechanism ensures consistent melting and homogenization of the plastic.
Parison Formation
Once the plastic material is melted, it is forced through a die to form a parison. The die is a specially shaped opening that extrudes the molten plastic into a hollow tube-like form. The size and shape of the die determine the dimensions and geometry of the parison.
Mold Preparation
The parison is transferred to the mold, which consists of two halves, an upper half and a lower half. The mold is designed to match the desired shape and size of the final product. The two halves of the mold can be opened and closed to allow for the insertion and removal of the parison.
Parison Placement and Clamping
The parison is placed between the two halves of the mold, and the mold is closed tightly to secure the parison in place. The halves are clamped together to prevent any leaks or movement during the subsequent steps.
Blow Molding
Compressed air is introduced into the parison through a small opening in the mold. The air pressure causes the parison to expand and conform to the shape of the mold. The mold provides the desired shape and size of the final product, while the air pressure inside the parison forces the plastic material to take on the mold’s contours.
Cooling and Solidification
Once the parison has been inflated and takes the shape of the mold, the mold is cooled to solidify the plastic rapidly. Cooling can be achieved through various methods, such as circulating cool air or water within the mold. The cooling process allows the plastic to retain its shape and rigidity.
Mold Opening and Product Ejection
After the plastic has sufficiently cooled and solidified, the mold is opened. The halves of the mold are separated, and the newly formed plastic product, known as the blow-molded part, is ejected from the mold. Any excess plastic, called flash, is trimmed off, leaving behind the finished product.
Post-Processing
The blow-molded part may undergo additional post-processing steps, such as trimming, labeling, assembly, or packaging, depending on the specific product requirements.
What Are the Types of Blow Molding?
If we categorize this molding into different types, then we find there are basically 3 types of blow molding are & their basic details I have mentioned below –
- Extrusion Blow Molding – We call this molding EBM. This is the most common type of blow molding used for manufacturing bottles and containers. It involves the extrusion of a parison, which is then placed in a mold and blown using compressed air.
- Injection Blow Molding – In short, we called this type of molding IBM. IBM combines the processes of injection molding and blow molding. Initially, a preform is injection-molded, which is a solid piece with a small opening called a neck. The preform is then transferred to a blow mold, where it is stretched and blown into the final shape.
- Stretch Blow Molding – We called this type of molding EBM. SBM is commonly used for producing PET bottles. It involves stretching a preform using a stretching rod and then blowing it into the desired shape. This process results in a strong and lightweight container.
Blow Molding Machine
A blow molding machine is a specialized piece of equipment used in the blow molding process to manufacture hollow plastic products. These machines are designed to handle the various steps involved in blow molding, including plastic material melting, parison formation, mold clamping, inflation, cooling, and product ejection. They come in different types and configurations to accommodate different production requirements. These machines generally consist of the following components –
- Extruder – The extruder is responsible for melting the plastic material and pushing it through a die to form a parison. It typically consists of a heated barrel, a screw mechanism, and a motor. The plastic material, in the form of pellets or granules, is fed into the extruder’s hopper and gradually melts as it is heated and mixed by the rotating screw.
- Die Head – The die head is a critical component that shapes the molten plastic into a parison. It has an opening with a specific geometry that determines the size and shape of the parison. The die head allows for precise control over the thickness and distribution of the plastic material as it is extruded.
- Mold – The mold is a crucial part of the blow molding machine. It consists of two halves, an upper half and a lower half, that are designed to match the desired shape of the final product. The halves can be opened and closed to allow for the insertion and removal of the parison. The mold is typically made from durable materials like steel or aluminum to withstand the pressures and temperatures involved in the blow molding process.
- Clamping Unit – The clamping unit holds the mold halves together during the blow molding process. It ensures that the mold remains closed and tightly sealed while the parison is inflated with compressed air. The clamping unit is equipped with hydraulic or mechanical mechanisms to provide the necessary force for mold clamping and opening.
- Inflation System – The inflation system is responsible for introducing compressed air into the parison to expand it and shape it according to the mold’s contours. It typically consists of a blow pin or nozzle that is inserted into the parison and connected to a source of compressed air. The system controls the air pressure and flow rate to achieve the desired shape and thickness of the final product.
- Cooling System – The cooling system helps to rapidly cool and solidify the plastic after it has taken the shape of the mold. It may include cooling channels or passages within the mold that circulate cool air, water, or a combination of both. The cooling process ensures that the plastic retains its shape and dimensional stability before the mold is opened and the product is ejected.
Leading Blow Molding Machine
Here I have mentioned some top brands of blow molding machines manufacturers, you may look at once –
- Krones AG
- Sidel Group
- Bekum
- Jomar Corporation
- Graham Engineering Corporation
Note – While selecting a blow molding machine, it is essential to consider factors such as the required production capacity, product specifications, energy efficiency, and reliability. Working with reputable manufacturers and consulting with industry experts can help ensure the right machine is chosen for specific production needs.
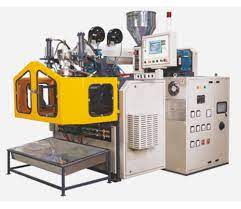
Image: Jagmohan JM
Blow Molding Defects
During the process, various defects can occur that may affect the quality and functionality of the final product. Identifying and understanding these defects is crucial for troubleshooting and improving the blow molding process. Here are some common blow molding defects –
- Blow Holes – Blow holes are small voids or bubbles that form on the surface of the blow-molded part. They are caused by trapped air or gases within the molten plastic during the blowing process. Blow holes can weaken the structural integrity of the product and negatively impact its aesthetics.
- Flash – Flash refers to the excess plastic material that protrudes from the mold joint line. It occurs when the mold halves are not properly aligned or when excessive air pressure causes the plastic to escape through small gaps in the mold. Flash can be trimmed off after the molding process, but excessive flash can lead to waste and increased production costs.
- Parting Line Defects – Parting line defects occur along the seam where the two halves of the mold meet. These defects can include rough edges, mismatched surfaces, or visible lines. Parting line defects are often caused by misalignment of the mold halves, inadequate clamping force, or worn-out mold components.
- Wall Thickness Variation – Inconsistent wall thickness is a common defect in blow molding. It occurs when the molten plastic does not distribute evenly within the mold, resulting in variations in wall thickness across the blow-molded part. Wall thickness variation can lead to structural weaknesses, reduced product strength, and uneven appearance.
- Splay Marks – Splay marks appear as streaks or discoloration on the surface of the blow-molded part. They are caused by the presence of moisture or contaminants in the plastic material, which vaporize and create bubbles during the blowing process. Splay marks can affect the aesthetics of the product and reduce its overall quality.
- Sink Marks – Sink marks are depressions or indentations that occur on the surface of the blow-molded part. They are caused by the uneven cooling of the plastic material, resulting in shrinkage in certain areas. Sink marks can be a cosmetic issue and may affect the dimensional accuracy of the product.
- Warpage – Warpage refers to the distortion or bending of the blow-molded part from its intended shape. It occurs due to uneven cooling or improper cooling of the plastic material. Warpage can affect the functionality of the product and may lead to assembly and fitment issues.
Note – To address blow molding defects, manufacturers employ techniques such as adjusting process parameters, optimizing mold design, ensuring proper material selection, and maintaining regular maintenance and inspection of molds and machines. It is essential to identify the root causes of defects and implement appropriate corrective measures to improve product quality and efficiency in blow molding operations.
Blow Molding Advantages
It offers several advantages that make it a popular choice for manufacturing hollow plastic products. Here are some key advantages of the blow molding process –
- Cost-Effective – This molding is a cost-effective manufacturing method, especially for large-scale production. It allows for high production volumes with relatively low labor costs due to its automated and continuous nature. The process also requires less material compared to other manufacturing methods, reducing material costs.
- Versatility – In this molding is a process that can be used to produce a wide range of products including bottles, holders, automotive factors, toys, and more. It accommodates colorful shapes, sizes, and designs, making it suitable for a variety of labor tasks.
- Lightweight – Blow-molded products are lightweight, which is advantageous in many applications. Lightweight products reduce transportation costs, are easier to handle, and can provide better fuel efficiency in vehicles. This makes blow molding particularly suitable for industries such as packaging and automotive.
- Design Flexibility – This molding offers design flexibility, allowing for complex geometries, intricate details, and custom shapes. With advancements in technology, manufacturers can incorporate features like handles, threads, and inserts directly into the blow-molded parts during the molding process, eliminating the need for additional assembly steps.
- Efficient Production – This molding enables rapid and efficient production. Once the molds are set up, the process can be automated, resulting in high production rates and shorter cycle times. The ability to produce a large number of products in a relatively short time makes blow molding ideal for industries with high-volume demands.
- Seamless and Leak-Proof – Blow molding produces seamless and leak-proof products. The parison is inflated to take the shape of the mold, resulting in a continuous, homogenous structure without any seams or joints. This eliminates the risk of leaks and enhances the product’s durability and functionality, particularly for containers and bottles.
- Material Options – Blow molding can utilize various plastic materials, including polyethylene (PE), polypropylene (PP), polyethylene terephthalate (PET), and polyvinyl chloride (PVC), among others. This flexibility allows manufacturers to select materials with specific properties such as strength, flexibility, transparency, or chemical resistance to meet the requirements of different applications.
- Recyclability – Many blow-molded products are recyclable, contributing to sustainability and environmental conservation efforts. Plastics used in blow molding, such as PET, can be recycled and transformed into new products, reducing waste and promoting a circular economy.
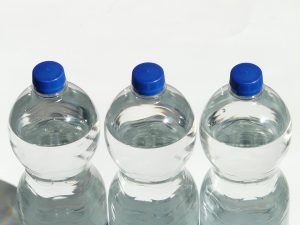
Blow Molding Disadvantages
While blow molding offers many advantages, there are also certain disadvantages associated with the process. Here are some common drawbacks of this molding –
- High Initial Investment – Setting up a blow molding operation requires a significant initial investment in machinery, molds, and equipment. The cost of acquiring and maintaining blow molding machines can be substantial, especially for large-scale production or specialized applications. This initial investment can be a barrier to entry for small or new businesses.
- Limited Material Selection – Although blow molding can utilize various plastic materials, the options may be more limited compared to other plastic manufacturing processes such as injection molding. Some specialized materials may not be suitable for blow molding due to their properties or processing requirements. This limitation can restrict the choice of materials for specific applications.
- Design Limitations – While blow molding offers design flexibility, there are certain design limitations to consider. The process is better suited for producing hollow and symmetrical shapes, making it challenging to achieve complex geometries or thin wall sections. Design features such as undercuts or intricate details may be difficult to achieve with blow molding.
- Surface Finish – Blow-molded products may have limitations in achieving a high-quality surface finish. The process can result in surface imperfections such as slight roughness, flow lines, or blemishes. While these surface defects may not impact the functionality of the product, they can affect its aesthetics and may require additional finishing steps if a smooth surface is desired.
- Limited Production Speed – Although blow molding can achieve high production rates, the process may have limitations compared to other plastic manufacturing methods such as injection molding. The cycle time for blow molding can be longer due to the time required for parison formation, inflation, cooling, and ejection. This can impact overall production speed and efficiency.
- Mold Cost and Lead Time – The design and production of blow molding molds can be costly and time-consuming. Molds for blow molding are typically larger and more complex compared to molds used in other processes. The cost and lead time for mold fabrication can be significant factors to consider, especially for custom or low-volume production runs.
- Environmental Impact – Like other plastic manufacturing processes, blow molding has environmental considerations. It relies on plastic materials, some of which may have limited recyclability or pose challenges in terms of disposal and environmental impact. Efforts to improve sustainability and mitigate the environmental impact of blow molding continue to be important.
Applications of Blow Molding
Blow molding finds extensive applications across various industries due to its ability to produce hollow plastic products in a cost-effective and efficient manner. Some common applications of blow molding include –
- Packaging – This is widely used in the packaging industry to manufacture bottles, containers, and jars for various products. These include beverage bottles (water, soft drinks, juices), personal care products (shampoos, lotions), household cleaning products, food containers, and industrial packaging. Blow molding provides the versatility to create containers of different shapes, sizes, and functionalities while ensuring product safety, durability, and ease of use.
- Automotive – It plays a crucial role in the automotive industry for the production of components such as fuel tanks, air ducts, reservoirs, and interior trim parts. The lightweight and cost-effective nature of blow-molded parts makes them ideal for automotive applications, contributing to weight reduction, improved fuel efficiency, and overall vehicle performance.
- Consumer Goods – It is used to manufacture a wide range of consumer goods, including toys, sporting goods, storage bins, and cosmetic containers. The process allows for the creation of customized and visually appealing products with excellent durability and functionality. Blow-molded toys and sporting goods can have intricate shapes, vibrant colors, and varying levels of flexibility.
- Medical and Healthcare – It is employed in the medical industry to produce items such as plastic containers for pharmaceuticals, specimen collection containers, respiratory equipment, and fluid administration devices. The ability to create sterile and single-use products using blow molding ensures safety and hygiene in medical and healthcare settings.
- Medical and Healthcare – Blow molding is employed in the medical industry to produce items such as plastic containers for pharmaceuticals, specimen collection containers, respiratory equipment, and fluid administration devices. The ability to create sterile and single-use products using blow molding ensures safety and hygiene in medical and healthcare settings.
- Industrial and Technical Applications – Blow molding finds applications in industrial and technical sectors, where it is used to manufacture items such as industrial drums, storage tanks, ductwork, and utility pipes. Blow-molded parts can provide excellent chemical resistance, durability, and dimensional stability required for demanding industrial applications.
- Construction and Infrastructure – Blow molding is utilized in the construction industry for manufacturing products such as septic tanks, drainage pipes, and road barriers. These products require high strength, longevity, and resistance to harsh environmental conditions, which can be achieved through blow molding processes.
- Furniture – Blow molding is employed in the production of plastic furniture components such as chairs, tables, and outdoor furniture. Blow-molded furniture parts offer lightweight characteristics, resistance to weathering, and cost-effectiveness compared to traditional materials such as wood or metal.
- Electronics and Electrical Industry – Blow molding is used to manufacture casings and enclosures for electronic devices, power tool housings, cable management systems, and wire spools. Blow-molded parts provide electrical insulation properties, protection against impact and environmental factors, and efficient manufacturing processes for the electronics and electrical industry.
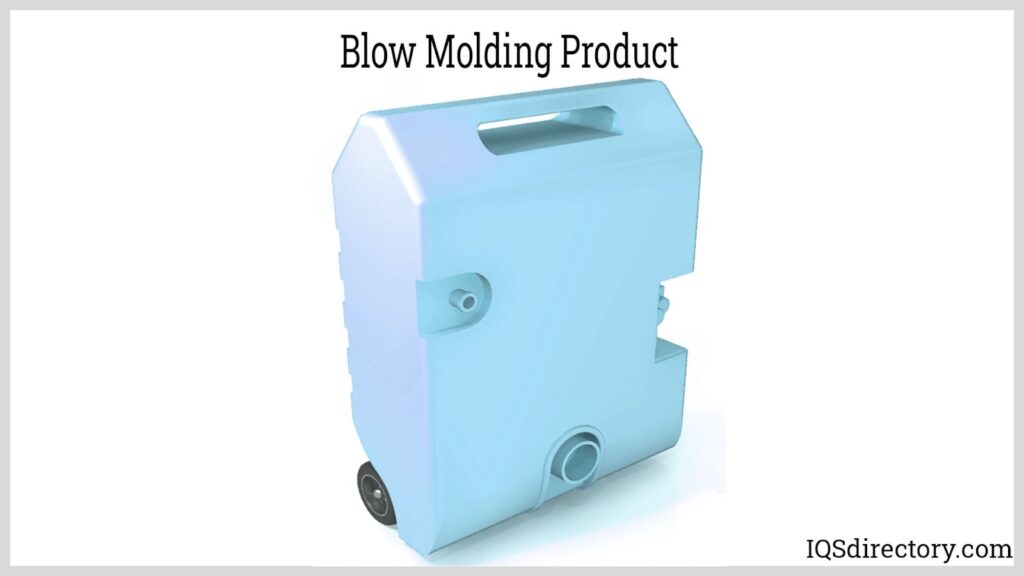
Conclusion
It is a highly versatile and efficient process for producing hollow plastic products. It have huge range of applications in industries such as packaging, automotive, consumer goods, medical, construction, and electronics showcases its adaptability and effectiveness.
Blow molding offers several advantages, including cost-effectiveness, design flexibility, efficient production, lightweight products, and recyclability. It enables the production of complex shapes, custom designs, and seamless, leak-proof products. The process allows for high-volume production with consistent quality and dimensional accuracy.
However, blow molding does come with certain limitations and challenges. These include the initial investment required for machinery and molds, design constraints, surface finish considerations, and limitations in material selection. Addressing these limitations requires careful planning, proper process optimization, and choosing the appropriate blow molding techniques for specific applications.
Despite these challenges, blow molding remains a widely utilized manufacturing process due to its ability to meet diverse industry needs, deliver cost-effective solutions, and produce high-quality products. Ongoing advancements in technology and material development continue to enhance the capabilities and scope of blow molding, ensuring its relevance and competitiveness in the ever-evolving manufacturing landscape.
Overall, blow molding serves as a key manufacturing process that provides innovative, lightweight, and durable plastic products for various industries. Its efficiency, versatility, and ability to create customized solutions make it a valuable technique for meeting the demands of modern production requirements.
What is Blow Molding?
Blow molding is a highly versatile manufacturing process that plays a pivotal role in producing a wide range of plastic products. It is a technique that allows for the creation of hollow objects, such as bottles, containers, and automotive components, by utilizing the forces of pressure and heat to shape molten plastic materials. With its ability to produce large quantities of lightweight and durable products, blow molding has become an integral part of various industries, including packaging, automotive, and consumer goods.
How does Blow Molding work?
Blow Molding mainly works in 7 steps and they –
Step 1 – Material Selection
Step 2 – Extrusion
Step 3 – Mold Preparation
Step 4 – Parison Placement and Clamping
Step 5 – Blow Molding
Step 6 – Cooling and Solidification
Step 7 – Mold Opening and Product Ejection
** For detail working information please visit this article from starting.
What is Extrusion Blow Molding?
It is also known as EBM. This is the most common type of blow molding used for manufacturing bottles and containers. It involves the extrusion of a parison, which is then placed in a mold and blown using compressed air
What is Blow Molding Method?
Blow molding involves melting plastic, forming it into a hollow tube, inflating it inside a mold, cooling it, and then removing the final product from the mold. It is a versatile and efficient process used to produce various hollow plastic products like bottles, containers, and automotive parts.
What are 4 stages of Blow Molding?
1. Plastic Material Preparation
2. Parison Extrusion
3. Parison Placement
4. Inflation & Shaping.
A heartfelt thank you! 💖
It’s going to be finish of mine day, however before finish I am
reading this impressive piece of writing to increase my experience.
Terima kasih telah membagikan artikel ini. Saya benar-benar terkesan oleh bagaimana Anda mengupas
topik ini dengan gaya yang lugas.
Saya percaya artikel seperti ini memiliki nilai edukatif tinggi, karena pembaca tidak hanya mendapatkan jawaban, tapi juga diajak berpikir kritis dan mempertimbangkan banyak aspek.
Menariknya, ada beberapa ide yang saya pikir bisa jadi tambahan bila Anda tertarik mengembangkan versi lanjutan dari
tulisan ini. Misalnya tentang dampak [isu turunan] atau studi kasus di [industri tertentu].
Gaya penulisan Anda yang santai tapi tetap informatif juga membuat pembaca awam pun bisa mengikuti.
Ini penting, karena sering kali topik seperti ini terlalu teknis
atau terlalu dangkal. Anda berhasil menjaga keseimbangan itu.
Meskipun saya merasa sudah banyak hal yang dipelajari dari artikel ini, saya justru semakin ingin tahu lebih dalam tentang aspek
[tambahan/topik turunan]. Apakah Anda berencana membuat
lanjutan atau seri dari artikel ini? Saya yakin pembaca akan sangat antusias.
Sekali lagi, terima kasih atas dedikasi Anda dalam menulis konten berkualitas seperti ini.
Dunia digital kita butuh lebih banyak penulis seperti Anda.
Terus berkarya dan menyebarkan ilmu, karena tulisan Anda
adalah kontribusi yang sangat berarti.
thanks dear & yes i am ready for collaboration. For any details you can visit about section.
Thanks for your appreciation.
Artikel ini adalah salah satu dari sedikit tulisan yang mampu membahas [topik] secara komprehensif tanpa terasa membosankan. Saya
menikmati setiap paragrafnya.
Saya percaya artikel seperti ini memiliki nilai edukatif tinggi, karena pembaca
tidak hanya mendapatkan jawaban, tapi juga diajak berpikir kritis dan mempertimbangkan banyak aspek.
Saya pribadi juga sedang mendalami hal serupa, terutama dalam konteks manajemen waktu, dan banyak poin dalam artikel ini yang
saya anggap relevan.
Saya ingin menyoroti juga tentang bagian ketika Anda menjelaskan [bagian isi], karena itu sangat mencerahkan dalam memahami kompleksitas isu ini.
Saya sampai membaca bagian itu dua kali karena ingin memastikan tidak melewatkan satu pun detail penting.
Meskipun saya merasa sudah banyak hal yang dipelajari dari artikel ini, saya justru semakin ingin tahu lebih dalam tentang aspek
[tambahan/topik turunan]. Apakah Anda berencana membuat
lanjutan atau seri dari artikel ini? Saya yakin pembaca akan sangat antusias.
Semoga semakin banyak orang yang menemukan tulisan ini dan mendapatkan manfaat sebesar yang
saya dapatkan. Saya menantikan konten-konten berkualitas lainnya
dari Anda di masa depan.
Sukses selalu!
Thanks so much for your appreciation & you can ask if any topic you need separate blog in comment section. Thanks again.