Overview
In medical device manufacturing, precision, consistency, and reliability are paramount. Patients’ lives often depend on the quality and performance of medical devices, ranging from intricate surgical instruments to life-saving diagnostic tools. Behind the scenes, the backbone of this critical industry is often the vertical injection molding machine. In this comprehensive exploration, we delve into the role of vertical injection molding machines in the manufacturing of medical devices, highlighting their significance, advantages, challenges, and future prospects.
The Pinnacle of Precision
Medical device manufacturing requires unparalleled precision, and vertical injection molding machines deliver just that. These machines are designed to produce intricate, complex, and tiny components with micron-level accuracy. This level of precision is crucial for applications like –
1. Catheters and Tubing
Catheters and tubing used in minimally invasive procedures demand incredibly tight tolerances. Vertical injection molding machines can consistently produce thin-walled, multi-lumen components that meet stringent medical standards.
2. Surgical Instruments
The fine, intricate details of surgical instruments are essential for their functionality. Vertical machines excel at molding these components, ensuring that the instruments meet exacting specifications.
3. Drug Delivery Systems
Devices such as insulin pens and inhalers require precise molding of components that enable accurate drug dosing. Vertical injection molding ensures that every device functions flawlessly.
4. Diagnostic Equipment
Medical diagnostics rely on precise components for accurate test results. Vertical machines are instrumental in producing parts for devices like blood glucose meters and imaging equipment.
Advantages of Vertical Injection Molding in Medical Device Manufacturing
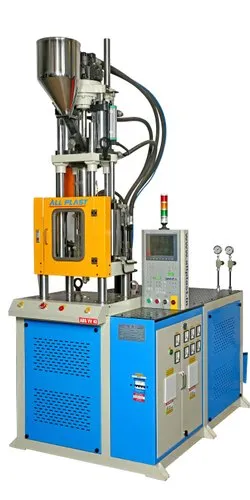
Vertical injection molding machines offer several advantages that make them indispensable in the production of medical devices –
1. Overmolding and Insert Molding
Overmolding and insert molding are standard techniques in medical device manufacturing. Overmolding allows for the encapsulation of one material with another, while insert molding involves molding around pre-placed components. Vertical machines are well-suited for these techniques, as their mold orientation allows for easy placement of inserts and precise over-molding.
2. Reduced Material Waste
Medical device manufacturing often involves expensive materials. Vertical injection molding machines can minimize material waste by precisely controlling the amount of material injected into the mold, ensuring that each shot produces a high-quality component.
3. Smaller Footprint
Space is often at a premium in cleanrooms and medical manufacturing facilities. Vertical machines have a smaller footprint compared to their horizontal counterparts, making them an ideal choice for facilities with limited space.
4. Enhanced Process Control
The vertical orientation of the injection and mold clamping units in these machines allows for better process control. This control is critical when working with sensitive materials or when producing components that require consistent, high-quality results.
5. Minimal Degassing Requirements
Certain medical-grade materials require degassing to remove trapped air or gases during the molding process. Vertical machines are advantageous in this regard, as the mold’s vertical orientation can facilitate better air release during the injection.
Challenges and Considerations
While vertical injection molding machines offer numerous benefits, they also present some challenges in medical device manufacturing –
1. Mold Complexity
The precision and intricacy of medical device components often require complex molds. Designing, machining, and maintaining these molds can be time-consuming and costly.
2. Tool Changes
Changing molds on vertical machines can be more labor-intensive than on horizontal machines. To minimize downtime, careful planning, and efficient tool change procedures are essential.
3. Cycle Time
Vertical machines may have slightly longer cycle times compared to their horizontal counterparts, which can affect production throughput. However, their precision and suitability for intricate parts often outweigh this limitation.
4. Initial Investment
Vertical injection molding machines may have a higher upfront cost, but this investment is often justified by the precision and capabilities they offer for medical device manufacturing.
Compliance and Quality Assurance
Medical device manufacturing is subject to strict regulatory requirements to ensure patient safety. Manufacturers must adhere to standards such as ISO 13485 and meet the regulatory requirements of governing bodies like the FDA (Food and Drug Administration) in the United States. The precision and consistency offered by vertical injection molding machines play a vital role in meeting these rigorous standards.
Quality control and assurance are integral parts of the medical device manufacturing process. Manufacturers employ various techniques, including in-line inspection, dimensional measurement, and statistical process control, to ensure that every component meets the required specifications.
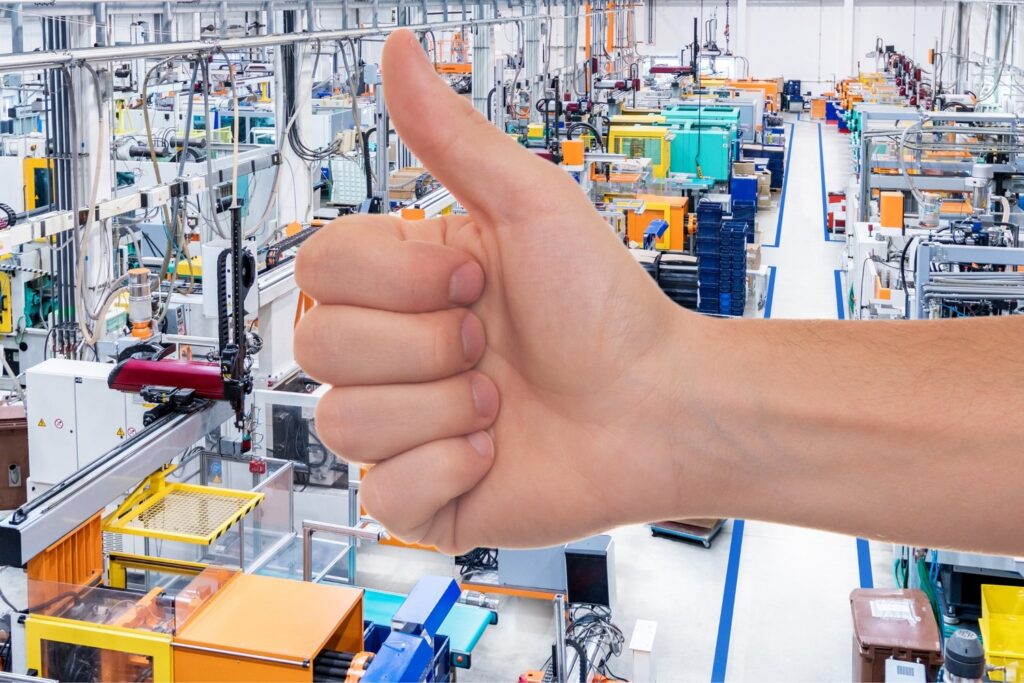
Breakdowns Troubleshooting of Vertical Injection Molding Machines
Vertical injection molding machines are versatile and precise tools for manufacturing a wide range of components. However, like any machinery, they are susceptible to breakdowns and operational issues. When these breakdowns occur, production can come to a halt, resulting in costly delays. In this guide, we will explore some of the major breakdowns that can affect vertical injection molding machines and provide troubleshooting strategies to address them effectively.
1. Injection Unit Issues
Problem: Injection Unit Does Not Move or Moves Slowly
Possible Causes:
- Hydraulic System Failure: A hydraulic system malfunction, such as a pump failure or low hydraulic fluid levels, can impede the movement of the injection unit.
Troubleshooting Steps:
- Check the hydraulic fluid position and add further if necessary.
- Check the hydraulic hoses and connections for any leakage and damage.
- Verify that the hydraulic pump is operational. If the hydraulic pump is not working, replace or repair it.
2. Mold Clamping Unit Problems
Problem: Mold Does Not Close or Close Unevenly
Possible Causes:
- Hydraulic System Issues: Similar to the injection unit, problems with the hydraulic system, such as low fluid levels or a malfunctioning pump, can affect the mold clamping unit’s performance.
Troubleshooting Steps:
- Inspect the hydraulic fluid level and top it up if needed.
- Check hydraulic hoses and connections for leaks and repair any found.
- Ensure that the mold clamping mechanism is not obstructed or damaged.
- Test the hydraulic pump’s functionality and replace or repair it if necessary.
3. Temperature Control Problems
Problem: Inconsistent Mold Temperature
Possible Causes:
- Malfunctioning Heating or Cooling Elements: Issues with the heating or cooling elements in the mold temperature controller can lead to inconsistent mold temperatures.
Troubleshooting Steps:
- Examine the heating and cooling elements for any damage or signs of wear.
- Ensure that the temperature controller is set to the desired temperature.
- Replace faulty heating or cooling elements as needed.
- Check for clogs or blockages in the cooling water lines and clear them if necessary.
4. Material Feed Issues
Problem: Inadequate Material Feed or Material Stuck in the Hopper
Possible Causes:
- Material Hopper Blockage: Material can become stuck in the hopper, preventing a steady feed into the machine.
Troubleshooting Steps:
- Inspect the material hopper for blockages, such as bridging or material clumps.
- Clear any obstructions or clumps in the hopper.
- Adjust the material feed settings to ensure a consistent and even flow.
5. Ejection Problems
Problem: Parts Do Not Eject Properly
Possible Causes:
- Ejection System Malfunction: Issues with the ejection system, such as a malfunctioning ejector pin or ejector plate, can result in improper part ejection.
Troubleshooting Steps:
- Inspect the ejection system components for damage or wear.
- Lubricate or replace any damaged or worn parts.
- Ensure that the ejector pins and plates move freely without obstruction.
6. Electrical System Failures
Problem: Electrical Control Panel Issues
Possible Causes:
- Electrical Component Failure: Malfunctions or failures in electrical components, such as relays, fuses, or control panels, can disrupt the machine’s operation.
Troubleshooting Steps:
- Check the control panel for error codes or indicators of electrical issues.
- Inspect and test relays, fuses, and other electrical components.
- Replace any faulty electrical components as necessary.
7. Quality Defects
Problem: Production of Defective Parts
Possible Causes:
- Mold Issues: Problems with the mold design, maintenance, or wear can lead to defects in the produced parts.
Troubleshooting Steps:
- Inspect the mold for signs of damage, wear, or corrosion.
- Ensure that the mold is properly cleaned and lubricated.
- Review the mold design and consider adjustments or modifications to address specific defects.
Preventive Maintenance to Minimize Breakdowns
While troubleshooting is essential for addressing breakdowns when they occur, preventive maintenance is equally crucial for minimizing the likelihood of breakdowns in the first place. Here are some preventive maintenance practices for vertical injection molding machines –
- Regular Inspection: Implement a routine inspection schedule to check for wear, damage, and leaks in hydraulic systems, electrical components, and mold.
- Lubrication: Ensure that all moving parts, including mold components and hydraulic mechanisms, are adequately lubricated to reduce friction and wear.
- Cleanliness: Keep the machine and mold clean to prevent contamination and reduce the risk of defects in the final products.
- Temperature Control: Monitor and maintain consistent mold temperatures to improve part quality and prevent issues related to uneven cooling.
- Material Handling: Store and handle materials properly to prevent contamination and ensure a consistent feed into the machine.
- Training: Provide training for machine operators and maintenance personnel to ensure they can identify and address issues promptly.
- Documentation: Maintain detailed records of maintenance and repairs to track the machine’s performance and identify patterns of recurring issues.
In conclusion, vertical injection molding machines are indispensable tools in various industries, and addressing breakdowns promptly is crucial to minimize downtime and maintain production efficiency. Troubleshooting breakdowns involves identifying the root causes of issues and taking appropriate corrective actions. Additionally, implementing preventive maintenance practices can significantly reduce the likelihood of breakdowns, ensuring that these machines continue to be reliable workhorses in manufacturing processes.
Manufacturers of Vertical Injection Molding Machines
Some manufacturers are known for producing vertical injection molding machines –
- Nissei Plastic Industrial Co., Ltd: Nissei is a well-established Japanese company that offers a range of injection molding machines, including vertical machines.
- Arburg GmbH + Co KG: Arburg, based in Germany, manufactures a variety of injection molding machines, including vertical and hybrid machines, renowned for their innovative technology and quality.
- Sumitomo (SHI) Demag: Sumitomo (SHI) Demag is a global company with a strong presence in the field of injection molding machines, including vertical models. They are recognized for their energy-efficient solutions.
- ENGEL Austria GmbH: ENGEL, headquartered in Austria, is a prominent manufacturer of injection molding machines, offering vertical and horizontal machines known for their advanced technology and automation options.
- Mitsubishi Heavy Industries Plastic Technology Co., Ltd. (MHIPT): MHIPT, a subsidiary of Mitsubishi Heavy Industries, produces vertical injection molding machines that combine precision and performance.
- FCS Group: FCS Group, based in Taiwan, manufactures a wide range of injection molding machines, including vertical and horizontal models, known for their efficiency and competitive pricing.
- Taiwang Machinery Company: Taiwang Machinery, headquartered in Taiwan, specializes in vertical injection molding machines, particularly for small and medium-sized parts.
- KAWAGUCHI Ltd. Kawaguchi, a Japanese manufacturer, offers vertical and horizontal injection molding machines known for their reliability and durability.
- Yuh-Dak Machinery Co., Ltd.: Yuh-Dak, based in Taiwan, is known for its vertical injection molding machines suitable for various applications.
- Multiplas Enginery Co., Ltd: Multiplas, also based in Taiwan, manufactures vertical and horizontal injection molding machines, known for their versatility and precision.
These manufacturers provide a range of vertical injection molding machines to meet different industry needs, from automotive and electronics to medical device manufacturing and beyond. When selecting a machine, it’s essential to consider your specific requirements and application to find the right fit for your production needs.
Automation and Industry 4.0 Integration
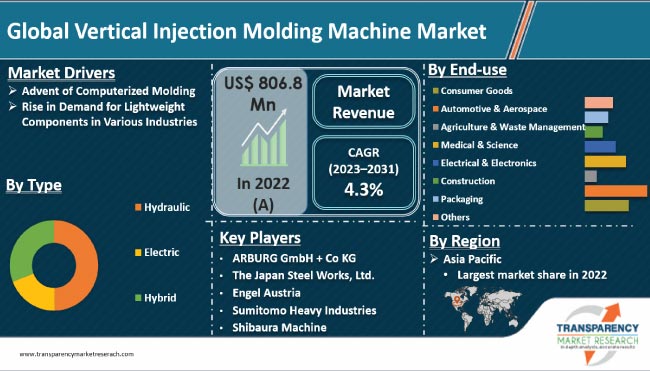
The future of medical device manufacturing will see increasing integration of automation and Industry 4.0 principles into the production process. Vertical injection molding machines are no exception to this trend. Automation can streamline operations, reduce labor costs, and improve overall efficiency.
Key developments in the field of vertical injection molding include –
1. Robot-Assisted Manufacturing
Robotic systems can be integrated with vertical injection molding machines to automate tasks such as part removal, inspection, and packaging. This reduces the need for manual labor and enhances precision and consistency.
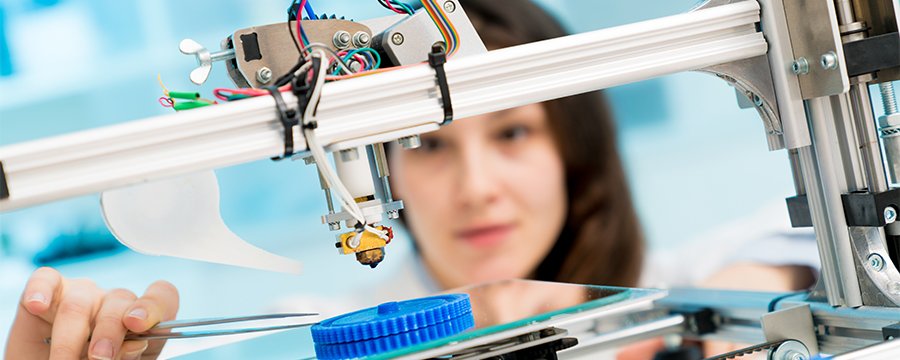
2. Data Analytics and Monitoring
Industry 4.0 technologies enable real-time monitoring of machine performance and quality metrics. Data analytics can provide insights into process optimization and early detection of deviations from quality standards.
3. Predictive Maintenance
Predictive maintenance uses data from sensors and monitoring systems to predict when maintenance or repairs are needed. This approach reduces unplanned downtime and ensures that machines are always in optimal working condition.
4. Digital Twin Technology
Digital twins, virtual replicas of physical machines, can be used to simulate and optimize the injection molding process. This technology allows for the testing of various process parameters without affecting production.
The Human Element
While automation and technology are advancing rapidly in medical device manufacturing, the human element remains essential. Skilled operators and engineers are crucial for mold design, maintenance, process optimization, and quality assurance. They ensure that the machines operate at their full potential and consistently produce high-quality medical components.
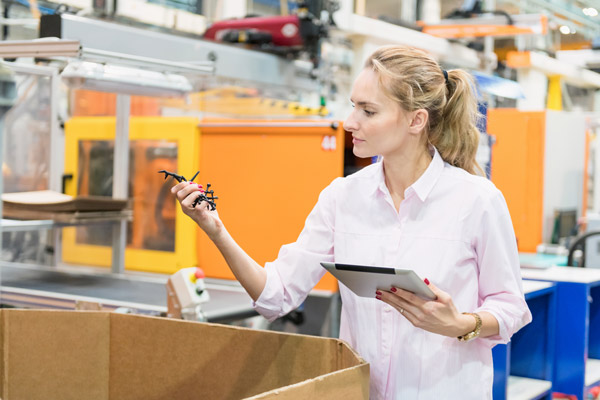
Conclusion
Vertical injection molding machines are the unsung heroes of medical device manufacturing, playing a vital role in producing precise, intricate, and high-quality components that save lives and improve patient care. As the healthcare industry continues to evolve and the demand for medical devices grows, the importance of vertical injection molding machines will only increase.
Manufacturers in this field must invest in cutting-edge technology, embrace automation and Industry 4.0 principles, and maintain a commitment to compliance and quality assurance. By doing so, they can ensure that the backbone of medical device manufacturing remains strong, resilient, and capable of meeting the ever-growing demands of the healthcare sector. In the end, it’s not just about molding plastic; it’s about molding a healthier, safer future for us all.
FAQ’s
Working of Vertical Injection Molding Machine
Here’s a step-by-step overview of the working of a vertical injection molding machine –
Mold Clamping: The process begins with the clamping unit securing the mold in a vertical orientation. This unit ensures that the mold remains closed and properly aligned during the injection process.
Injection Unit: The injection unit consists of a barrel, screw, and nozzle. Plastic pellets are fed into the barrel, where they are heated and melted by electric or hydraulic heaters.
Material Injection: Once the plastic material reaches the desired temperature and consistency, the screw injects the molten plastic into the mold cavity under high pressure.
Mold Filling: The molten plastic flows into the mold cavity, taking the shape of the mold’s interior. The injection pressure is maintained until the mold is completely filled.
Cooling: After the mold is filled, the cooling process begins. Cooling channels within the mold allow coolant to circulate and rapidly cool the plastic, solidifying it into the desired shape.
Mold Opening: Once the plastic has cooled and solidified, the mold opens vertically, exposing the newly formed part.
Ejection: An ejection mechanism, typically consisting of ejector pins or plates, pushes the part out of the mold cavity.
Part Removal: The finished part is removed manually or using automation, and the mold is ready for the next cycle.
Repeat: The entire process repeats for the production of additional parts.
Vertical injection molding machines are particularly suitable for applications that require precision, over-molding, or insert molding. Their vertical orientation allows for easy access to the mold and facilitates operations involving multiple materials or components.
Write the Pros and Cons of Vertical Injection Molding Machines.
Here are the pros and cons of vertical injection molding machines in a step-wise format –
Pros:
Precision: Vertical machines are known for their precision and are ideal for applications that require tight tolerances and intricate part geometries.
Overmolding and Insert Molding: They excel at over-molding and insert molding, allowing for the encapsulation of multiple materials or components within a single part.
Space Efficiency: Vertical machines have a smaller footprint compared to horizontal machines, making them suitable for facilities with limited space.
Reduced Material Waste: They often produce less material waste, which can lead to cost savings over time.
Better Degassing: Vertical orientation facilitates better air release during injection, making them advantageous for materials that require degassing.
Ease of Tool Changes: Tool changes on vertical machines can be quicker and more straightforward, reducing downtime.
Cons:
Production Speed: They may have slightly slower cycle times compared to horizontal machines, especially for projects with multiple cavities.
Limited for High-Volume Production: Their efficiency decreases for high-volume production compared to horizontal machines.
Complex Mold Design: Complex mold designs can be challenging to implement due to their vertical orientation.
Limited Material Compatibility: While they can work with various materials, some materials may be better suited for horizontal machines.
Tool Change Complexity: Tool changes on vertical machines may be more labor-intensive for large molds, affecting overall productivity.
Initial Investment: They can have a higher upfront cost, which may be a barrier for some businesses.
Vertical Vs. Horizontal Injection Molding Machines.
Here’s a step-wise comparison between vertical and horizontal injection molding machines –
1. Mold Orientation:
Vertical Injection Molding: In vertical machines, the mold is oriented vertically, with the injection unit injecting plastic from the top.
Horizontal Injection Molding: In horizontal machines, the mold is oriented horizontally, and plastic is injected from the side.
2. Space and Footprint:
Vertical Injection Molding: Vertical machines have a smaller footprint, making them suitable for facilities with limited space.
Horizontal Injection Molding: Horizontal machines are typically larger and require more floor space, making them ideal for high-volume production.
3. Tooling and Mold Design:
Vertical Injection Molding: Vertical machines are well-suited for insert molding and over-molding due to their mold orientation. They can handle complex part geometries.
Horizontal Injection Molding: Horizontal machines are versatile and can accommodate larger and more intricate molds. They are ideal for projects with multiple cavities.
4. Production Speed:
Vertical Injection Molding: Vertical machines may have slightly slower cycle times, especially for multi-cavity projects. They excel in precision.
Horizontal Injection Molding: Horizontal machines are known for high-speed production, making them suitable for mass production.
5. Material Flow and Degassing:
Vertical Injection Molding: Vertical machines are advantageous for materials that require degassing as air can escape more easily during injection.
Horizontal Injection Molding: Horizontal machines may require additional measures for proper degassing.
6. Tool Changes and Maintenance:
Vertical Injection Molding: Tool changes are often quicker and simpler on vertical machines, reducing downtime.
Horizontal Injection Molding: Tool changes on horizontal machines can be more complex and time-consuming.
7. Material Options:
Vertical Injection Molding: Vertical machines can work with a wide range of materials, making them suitable for specialized applications.
Horizontal Injection Molding: Horizontal machines are also versatile with material options, including those used in mass production.
Wow! Thank you! I always wanted to write on my site something like that. Can I include a part of your post to my blog?