When it comes to materials that play a pivotal role in various industries, thermoset materials stand out as a class of polymers with remarkable properties and versatility. From aerospace and automotive to electronics and construction, thermoset materials find applications in a wide range of fields due to their unique characteristics. In this article, we delve into the world of thermoset materials, exploring their properties, processing methods, and diverse applications.
Understanding Thermoset Materials
Thermoset materials, also known as thermosetting polymers, are a subset of polymers that exhibit a distinct behavior when subjected to heat. Unlike thermoplastic materials, which soften when heated and harden when cooled, thermoset materials undergo a chemical reaction during curing that makes them infusible and insoluble. Once they are set, they retain their shape and mechanical properties even at elevated temperatures, making them ideal for applications where high-performance materials are required.
Key Properties of Thermoset Materials
- High-Temperature Resistance: One of the standout features of thermoset materials is their ability to withstand high temperatures without deformation or softening. This property makes them suitable for applications in which exposure to heat is a concern, such as automotive components near engines or electronic devices.
- Excellent Mechanical Strength: Thermoset materials often exhibit superior mechanical properties, including high tensile and compressive strength, as well as stiffness. This makes them valuable in structural components and load-bearing applications.
- Chemical Resistance: Many thermoset materials are highly resistant to chemicals, making them suitable for use in corrosive environments or when contact with various chemicals is expected.
- Dimensional Stability: Once cured, thermoset materials maintain their shape and size, ensuring dimensional stability over time. This characteristic is critical in precision engineering and manufacturing.
- Electrical Insulation: Thermoset materials are excellent electrical insulators, which is why they are commonly used in electrical and electronic applications to protect against electrical currents and provide thermal insulation.
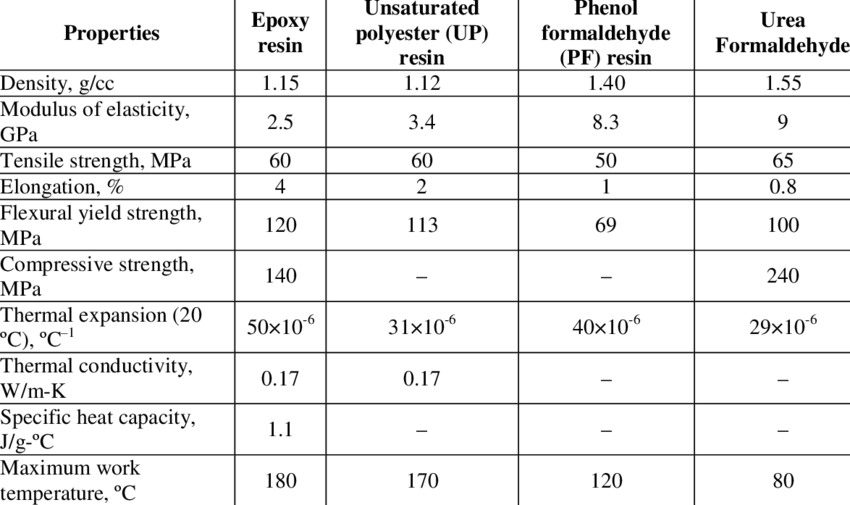
Characteristics of Thermoset Materials
- Irreversible Curing: Thermosets undergo a chemical curing process that is irreversible. Once cured, they cannot be re-melted or reshaped without undergoing degradation.
- Cross-Linking: During curing, thermosets form a three-dimensional network of covalent bonds, known as cross-linking. This network structure contributes to their rigidity and stability.
- Brittle Behavior: Thermosets tend to be brittle compared to thermoplastics. They are more prone to fracture under stress, although their high strength compensates for this.
- Excellent Creep Resistance: They exhibit minimal creep, meaning they resist deformation over time under a constant load.
- Limited Recycling: Unlike thermoplastics, thermosets cannot be easily recycled due to their irreversible cross-linking. This makes disposal and environmental considerations important.
Processing Thermoset Materials
The processing of thermoset materials is a critical step in their utilization. Unlike thermoplastics, which can be melted and reformed multiple times, thermoset materials cannot be reprocessed after curing. Instead, they are formed through a curing process that involves the following steps –
- Preparation: The raw thermoset material, often in the form of a resin, is mixed with a curing agent or catalyst. This mixture is typically in a liquid or semi-liquid state and is known as a pre-polymer.
- Molding: The pre-polymer is then introduced into a mold that is designed to give the final product its desired shape. This mold can take various forms, depending on the application.
- Curing: The mold containing the pre-polymer is heated to initiate the curing process. During curing, cross-linking reactions occur, forming a three-dimensional network of polymer chains. This network is responsible for the material’s infusibility and insolubility.
- Cooling and Demolding: After curing is complete, the material is allowed to cool, and it hardens into its final form. The mold is then opened, and the finished thermoset product is removed.
Types of Thermoset Materials
1. Epoxy Resins
- Composed of epoxide monomers and curing agents.
- Exceptional adhesion, chemical resistance, and mechanical strength.
- Commonly used in composites, coatings, and electronics.
2. Polyester Resins
- Made from unsaturated polyester and a cross-linking agent.
- Lightweight and corrosion-resistant.
- Used in fiberglass-reinforced plastics, automotive parts, and boat hulls.
3. Phenolic Resins
- Derived from phenol and formaldehyde.
- Excellent heat resistance and flame retardancy.
- Applications in electrical components, laminates, and brake linings.
4. Polyurethane Resins
- Comprise isocyanates and polyols.
- Offer versatility, elasticity, and impact resistance.
- Commonly found in foams, adhesives, and elastomers.
5. Vinyl Ester Resins
- A hybrid of epoxy and polyester resins.
- High resistance to chemicals and moisture.
- Used in marine, chemical processing, and corrosion-resistant applications.
6. Silicone Resins
- Based on silicon-oxygen polymers.
- Exceptional high-temperature stability and electrical insulation.
- Commonly used in electrical coatings, sealants, and aerospace components.
7. Melamine Resins
- Produced from melamine and formaldehyde.
- Heat-resistant and durable.
- Applications include tableware, laminates, and decorative surfaces.
8. Bismaleimide (BMI) Resins
- Known for high-temperature performance.
- Used in aerospace, electronics, and advanced composite materials.
9. Diallyl Phthalate (DAP) Resins
- Contain diallyl phthalate monomers.
- Known for high electrical insulation and heat resistance.
- Applications in electrical connectors and circuit boards.
10. Cyanate Ester Resins
- Feature cyanate ester monomers.
- Provide excellent thermal and electrical properties.
- Used in aerospace and electronic components.
Different Molding Methods for Thermoplastic Materials
Here are different molding methods for thermoplastic materials explained in a step-wise & concise manner –
1. Injection Molding
- Step 1: Pellets of thermoplastic material are heated until they melt.
- Step 2: The molten material is injected into a mold cavity under high pressure.
- Step 3: The material cools and solidifies within the mold.
- Step 4: The mold opens, and the finished part is ejected.
- Applications: Used for a wide range of products, from automotive components to consumer goods.
2. Extrusion
- Step 1: Thermoplastic resin is fed into an extruder, where it’s heated and melted.
- Step 2: The molten material is forced through a die, forming a continuous profile or shape.
- Step 3: The material is cooled and solidified, then cut into desired lengths.
- Applications: Produces pipes, tubing, and plastic sheets.
3. Blow Molding
- Step 1: A heated thermoplastic parison (hollow tube) is placed in a mold.
- Step 2: Compressed air is blown into the parison, expanding it to take the shape of the mold.
- Step 3: The material cools and solidifies, and the mold opens to release the hollow object.
- Applications: Common for producing bottles, containers, and hollow plastic products.
4. Thermoforming
- Step 1: A thermoplastic sheet is heated until it softens.
- Step 2: The softened sheet is stretched or pressed over a mold to take its shape.
- Step 3: The material cools and hardens, and the formed part is removed.
- Applications: Used for packaging trays, consumer goods, and automotive components.
5. Compression Molding
- Step 1: Heated thermoplastic material is placed in an open mold cavity.
- Step 2: The mold is closed, compressing the material into the desired shape.
- Step 3: The material cools and solidifies within the closed mold.
- Step 4: The mold opens, and the part is removed.
- Applications: Suitable for products requiring strong and durable components.
6. Rotational Molding
- Step 1: Powdered thermoplastic material is placed inside a heated, rotating mold.
- Step 2: The mold rotates in multiple axes, coating the interior and forming the desired shape.
- Step 3: The mold is cooled to solidify the part.
- Step 4: The mold stops, and the finished part is removed.
- Applications: Used for large, hollow products like tanks, playground equipment, and kayaks.
Thermoset Vs. Thermoplastic
Here’s a step-wise comparison between thermoset and thermoplastic materials in concise terms –
Thermoset Materials
1. Curing Process
- Step 1: Thermoset materials are initially in a soft or liquid state.
- Step 2: They undergo irreversible curing when exposed to heat, pressure, or a combination of both.
- Step 3: The curing process results in strong, rigid, and chemically stable materials.
2. Melting and Reshaping
- Step 1: Once cured, thermoset materials cannot be melted and reshaped.
- Step 2: They maintain their shape and properties even at high temperatures.
3. Properties
- Step 1: Thermosets have excellent heat resistance, chemical resistance, and dimensional stability.
- Step 2: They are electrically insulating and often used in high-temperature applications.
Thermoplastic Materials
1. Melting and Shaping
- Step 1: Thermoplastic materials start as solid pellets or sheets.
- Step 2: They can be melted when heated and reshaped into different forms.
- Step 3: Upon cooling, thermoplastics solidify but can be melted and reshaped multiple times without undergoing chemical changes.
2. Properties
- Step 1: Thermoplastics have varying properties, depending on the specific type.
- Step 2: They can range from flexible to rigid and transparent to opaque.
3. Recycling
- Step 1: Thermoplastics are recyclable because they can be melted and reprocessed.
- Step 2: Recycling thermoplastics reduces waste and conserves resources.
4. Applications:
- Step 1: Thermosets are commonly used in aerospace, automotive, and electrical applications due to their heat resistance.
- Step 2: Thermoplastics find use in a wide range of industries, including packaging, consumer goods, and 3D printing, thanks to their versatility and recyclability.
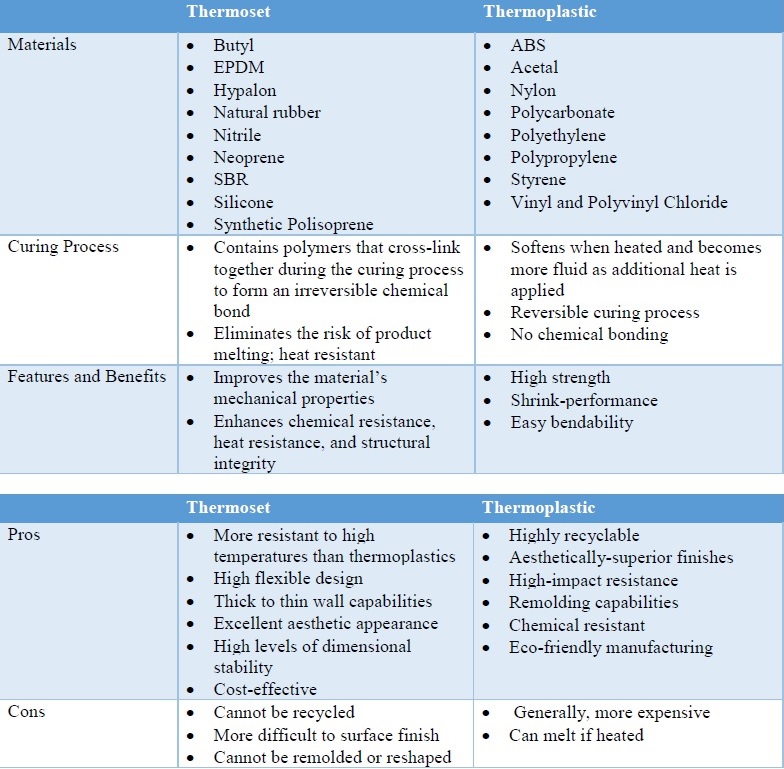
Diverse Applications of Thermoset Materials
The unique combination of properties and the ability to maintain their integrity under harsh conditions make thermoset materials invaluable in various industries –
- Aerospace: Thermoset composites are used to manufacture lightweight, high-strength components for aircraft and spacecraft, reducing fuel consumption and improving overall performance.
- Automotive: Thermoset materials find applications in automotive parts such as engine components, brake pads, and exterior body parts due to their heat resistance and durability.
- Electronics: The electrical insulation properties of thermoset materials make them ideal for insulating and protecting electronic components and circuitry from heat and moisture.
- Construction: Thermoset materials are used in the construction industry for making durable, heat-resistant, and chemically resistant materials such as coatings, adhesives, and composite reinforcements.
- Medical: Biocompatible thermoset materials are employed in the production of medical devices and implants, ensuring safe and long-lasting solutions for healthcare.
- Electrical Insulation: Transformers, power lines, and electrical equipment benefit from the electrical insulation properties of thermoset materials, safeguarding against electrical arcing and fires.
- Sporting Goods: Thermoset composites are used to create lightweight, high-strength materials for sporting equipment such as tennis rackets, golf clubs, and bicycle frames.
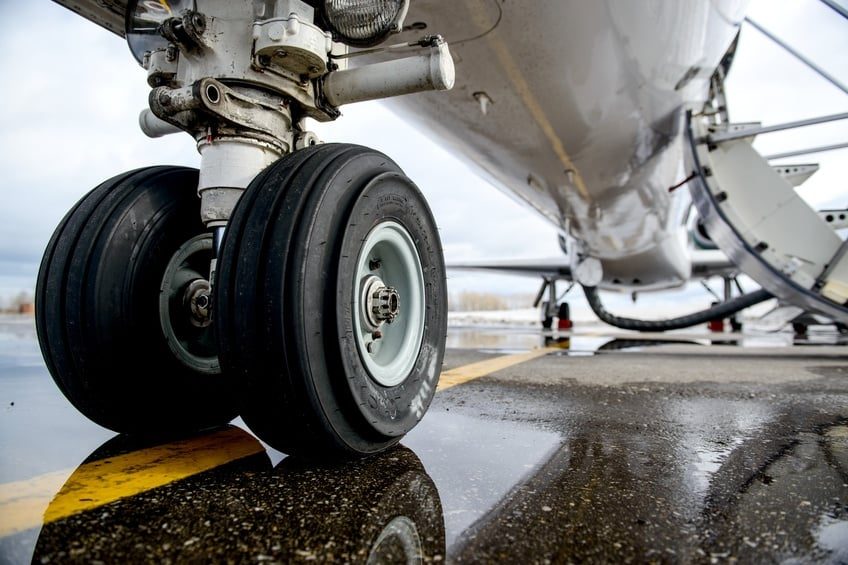
Conclusion
Thermoset materials have carved out a prominent niche in the world of materials science and engineering, offering a unique blend of properties that make them indispensable in various industries. From their exceptional temperature resistance to their formidable mechanical strength, these materials continue to drive innovation and advancement across sectors as diverse as aerospace, automotive, electronics, and healthcare. Understanding the properties, processing methods, and applications of thermoset materials is key to unlocking their full potential and harnessing their capabilities for future technological advancements.
Frequently Asked Questions (FAQ)
What are thermoset materials?
Thermoset materials are a class of polymers that, once cured or molded, undergo a chemical change that irreversibly solidifies them. Unlike thermoplastics, they cannot be melted and reshaped.
How do thermoset materials differ from thermoplastics?
Thermoset materials cannot be melted and reshaped after curing, whereas thermoplastics can be melted and reshaped multiple times without undergoing chemical changes.
What is the curing process for thermoset materials?
Thermoset materials undergo curing through a chemical reaction triggered by heat, pressure, or a combination of both. This process transforms them from a liquid or soft state to a solid, durable form.
What are some common examples of thermoset materials?
Common examples include epoxy resins, phenolic resins, melamine formaldehyde, and unsaturated polyester resins.
What are the key properties of thermoset materials?
Thermosets are known for their excellent heat resistance, dimensional stability, and resistance to chemicals and UV radiation. They are also electrically insulating.
Where are thermoset materials commonly used?
Thermosets find applications in a wide range of industries, including aerospace (composite materials), automotive (brake pads), electronics (printed circuit boards), and construction (insulating materials).
Can thermoset materials be recycled?
Thermoset materials are typically difficult to recycle due to their irreversible curing process. However, some advancements in recycling techniques are being explored.
How are thermoset materials molded or shaped?
Thermoset materials are typically molded using a heat and pressure process. The material is heated until it becomes soft, then it’s placed in a mold where it cures and hardens into the desired shape.
Are thermoset materials biodegradable?
Thermoset materials are generally not biodegradable due to their stable and durable nature.
What are the advantages of using thermoset materials in high-temperature applications?
Thermoset materials can withstand high temperatures without softening or deforming, making them suitable for applications where heat resistance is critical.
Are there any health concerns associated with thermoset materials?
When properly cured and used in accordance with safety guidelines, thermoset materials are generally safe. However, some resins may emit volatile organic compounds (VOCs) during curing, which can be harmful if not properly controlled.
Can thermoset materials be repaired if damaged?
Repairing thermoset materials can be challenging due to their irreversible curing process. In some cases, minor repairs can be made, but it’s often more practical to replace the damaged part.
Are there environmentally friendly alternatives to traditional thermoset materials?
Some bio-based thermoset materials and thermoset composites made from sustainable sources are being developed to reduce the environmental impact of thermoset products.
Do thermoset materials have any limitations?
Thermoset materials cannot be recycled as easily as thermoplastics, and their disposal can pose environmental challenges. Additionally, they may be brittle and less impact-resistant compared to some thermoplastics.
How are thermoset materials tested for quality and performance?
Quality control and performance testing methods for thermoset materials include mechanical testing, thermal analysis, chemical resistance tests, and non-destructive testing techniques.
Can thermoset materials be used for 3D printing?
While thermoset materials are less common in 3D printing compared to thermoplastics, there are 3D printing technologies that can handle certain types of thermoset resins.
I recently discovered your blog, and I must say that I genuinely enjoyed reading your posts. I’m planning to subscribe to your updates, and I hope you continue to provide new content regularly.
You could certainly see your skills in the article yyou write.
The sector hopes for even more passionate writers such as
you who aren’t afraid to mention how they believe. All the time go after yor
heart.
Its wonderful as your other posts : D, regards for posting. “It takes less time to do things right than to explain why you did it wrong.” by Henry Wadsworth Longfellow.
I like this post, enjoyed this one thanks for posting.
Hiya! I just wish to give a huge thumbs up for the good data you might have right here on this post. I shall be coming again to your blog for extra soon.
Thanks