Introduction
In the dynamic world of manufacturing, precision, and surface quality are paramount. One technique that stands at the forefront of achieving flawless surfaces is surface grinding. This process, often regarded as an art and a science, has undergone significant evolution over the years. In this blog, we delve into the realm of surface grinding, exploring the techniques, technologies, and trends that are shaping the landscape of modern manufacturing.
What is a Surface Grinding Machine?
A surface grinding machine is a precision tool used for smoothing and finishing flat surfaces of a workpiece. It employs an abrasive grinding wheel that rotates at high speeds to remove small amounts of material from the surface of the workpiece. This process results in improved surface smoothness, flatness, and dimensional accuracy.
Components of Surface Grinding Machine
The basic components of a surface grinding machine typically include –
- Base: The machine’s foundation that supports all other components.
- Column: A vertical post that holds the wheel head and the worktable.
- Wheelhead: The assembly that holds and rotates the grinding wheel.
- Worktable: A horizontal table on which the workpiece is mounted and moved back and forth under the grinding wheel.
- Crossfeed: The mechanism that moves the worktable perpendicular to the wheel’s rotation, allowing for precise control of material removal.
- Longitudinal Feed: The mechanism that moves the worktable along the length of the machine, facilitating the grinding process.
- Grinding Wheel: The abrasive tool mounted on the wheel head that grinds and removes material from the workpiece’s surface.

The Art and Science of Surface Grinding Machine
Surface grinding is a machining process that involves the removal of material from a workpiece’s surface to achieve a desired level of flatness, smoothness, and dimensional accuracy. The process employs a grinding wheel that rotates at high speeds while making contact with the workpiece. As the abrasive grains on the wheel remove material, a precise and uniform surface finish is achieved.
Unveiling the Techniques of Surface Grinding Machine
Precision Flat Surface Grinding
This is the foundational technique of surface grinding. It involves grinding a workpiece to achieve a flat and parallel surface. Precision flat grinding is essential for components that require high levels of accuracy and uniformity, such as machine tool beds, automotive components, and precision instruments.
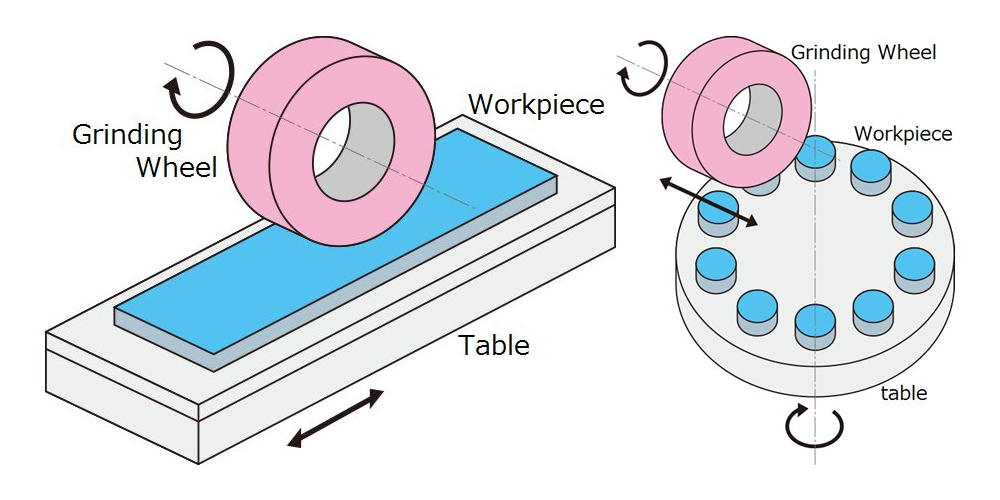
Applications of Precision Flat Grinding
- Tool and Die Making: It ensures that these critical components have flat and parallel surfaces, which are essential for achieving precise and consistent results in metal stamping, injection molding, and other manufacturing processes.
- Aerospace Components: Aerospace industry applications often demand strict adherence to dimensional accuracy and surface finish. Precision flat grinding is utilized for components like turbine blades, engine parts, and structural elements to achieve the required levels of flatness, parallelism, and surface integrity.
- Automotive Manufacturing: In the automotive sector, precision flat grinding is applied to engine components, transmission parts, and braking system components. It ensures optimal performance, reduces friction, and enhances the lifespan of these critical parts.
- Electronics and Semiconductor Manufacturing: Precision flat grinding is crucial in creating substrates, wafers, and other components used in electronics and semiconductor manufacturing. The flat and uniform surfaces achieved through this process contribute to the precise alignment and functioning of microelectronic devices.
- Optics and Photonics: Precision flat grinding is employed in producing optical components such as lenses, mirrors, and prisms. The process ensures the necessary surface quality for achieving accurate light transmission, image clarity, and optical performance.
- Medical Devices: The medical industry relies on precision flat grinding for manufacturing surgical instruments, medical implants, and diagnostic equipment. Flat and smooth surfaces are essential for ensuring biocompatibility, ease of sterilization, and patient safety.
Advantages of Precision Flat Grinding
- Dimensional Accuracy: Precision flat grinding offers exceptional control over the dimensional accuracy of workpieces. This ensures that components meet tight tolerances and specifications, minimizing the need for additional finishing operations.
- Surface Finish: The process yields excellent surface finishes, ranging from smooth to mirror-like, depending on the application requirements. This enhances the aesthetics, functionality, and performance of the final product.
- Parallelism and Flatness: Precision flat grinding ensures the creation of flat and parallel surfaces, which is essential for components that require proper alignment, assembly, or contact with other parts.
- Material Removal Control: Manufacturers can precisely control the amount of material removed during precision flat grinding. This reduces waste, optimizes material usage, and enhances cost-effectiveness.
- Reduced Warping: Precision flat grinding can mitigate or correct warping and distortion that may occur during earlier manufacturing processes, ensuring the final product meets design specifications.
Creep Feed Grinding
In this technique, deep cuts are made into the workpiece at slow speeds. Creep feed grinding is ideal for removing large amounts of material efficiently, making it suitable for aerospace components and turbine blades.
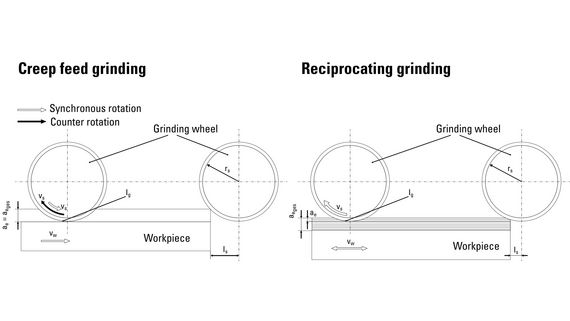
Applications of Creep Feed Grinding
- Aerospace Components: Creep feed grinding is widely used in the aerospace industry for precision machining of turbine blades, engine components, and other critical parts. It ensures that these components meet stringent requirements for surface finish, geometric tolerances, and overall performance.
- Gas Turbine Components: The complex geometries of gas turbine components, such as vanes and blades, make them ideal candidates for creep feed grinding. This process achieves the necessary precision and surface quality required for efficient and reliable turbine operation.
- Automotive and Diesel Engines: Creep feed grinding is applied to produce critical engine components like fuel injection nozzles, valve seats, and camshafts. It helps achieve precise geometries and superior surface finishes for optimal engine performance.
- Medical Implants: Creep feed grinding is used in the production of medical implants, such as hip and knee joint replacements. The technique ensures that implants have accurate dimensions, smooth surfaces, and proper fitment, enhancing patient comfort and recovery.
- Precision Tooling: Creep feed grinding is employed in the manufacturing of precision tools, including cutting inserts, drills, and end mills. It enables the creation of intricate profiles and sharp cutting edges while maintaining exceptional dimensional accuracy.
- Mold and Die Components: Complex mold and die components benefit from creep feed grinding due to their ability to achieve precise geometries and surface finishes. This is crucial in industries such as injection molding and die casting.
Advantages of Creep Feed Grinding
- Material Removal Efficiency: Creep feed grinding removes a significant amount of material in each pass, making it an efficient process for components with high material removal requirements.
- Surface Finish: The slow grinding speeds of creep feed grinding result in exceptional surface finishes, reducing the need for subsequent finishing operations.
- Low Thermal Damage: The deep cuts and slow speeds minimize heat generation, reducing the risk of thermal damage to the workpiece and preserving material integrity.
- Reduced Residual Stresses: Creep feed grinding generates lower residual stresses compared to traditional grinding methods, contributing to improved part durability and longevity.
- Complex Geometries: The process can handle intricate and complex part geometries, allowing for the production of components with challenging shapes and profiles.
- Minimal Wheel Wear: Creep feed grinding typically uses large grinding wheels, which experience less wear compared to smaller wheels used in conventional grinding methods. This leads to longer wheel life and reduced downtime for wheel changes.
- Improved Geometric Tolerances: Creep feed grinding can achieve tight dimensional tolerances, ensuring parts meet design specifications with high accuracy.
- Process Control: Modern creep feed grinding machines often incorporate advanced control systems and monitoring capabilities, enhancing process reliability and repeatability.
Cylindrical Grinding
Although commonly associated with external surfaces, surface grinding also extends to cylindrical components. Cylindrical grinding is used to achieve precise roundness and smoothness on shafts, sleeves, and other cylindrical parts.
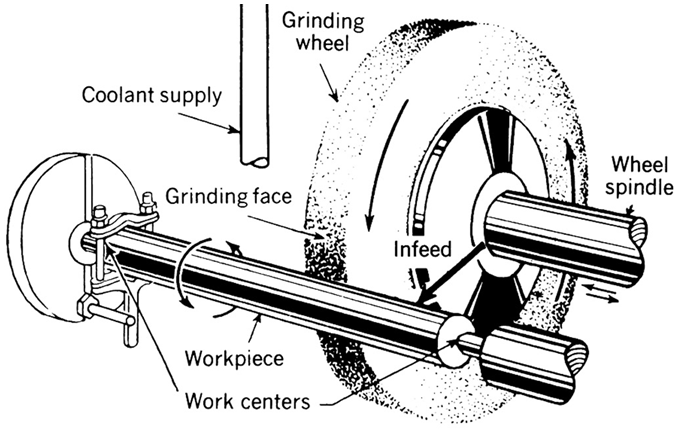
Applications of Cylindrical Grinding
- Shafts and Rods: Cylindrical grinding is commonly used for producing precision shafts, rods, and axles that require accurate roundness, straightness, and surface finish.
- Cylindrical Components: Components with cylindrical features, such as hydraulic pistons, valve stems, and roller bearings, are often manufactured using cylindrical grinding to ensure optimal performance and fitment.
- Rotating Machinery: Cylindrical grinding is crucial for manufacturing rotating machinery components like crankshafts, camshafts, and gears. These components require precise dimensions and surface finishes to ensure smooth and efficient operation.
- Aerospace and Defense: The aerospace and defense industries use cylindrical grinding for producing critical components, such as landing gear components, engine parts, and missile guidance systems.
- Automotive Industry: Cylindrical grinding is applied in the production of automotive parts like drive shafts, steering components, and transmission parts, ensuring the required precision and functionality.
- Medical Devices: Medical industry applications include the manufacturing of surgical instruments, medical implants, and orthopedic devices that demand precise roundness and surface quality.
Advantages of Cylindrical Grinding
- Precision: Cylindrical grinding offers exceptional precision and control over dimensional accuracy, ensuring that workpieces meet tight tolerances and specifications.
- Versatility: The process can accommodate a wide range of workpiece materials, including metals, ceramics, and composites, making it versatile for various industries.
- Surface Finish: Cylindrical grinding produces superior surface finishes, which reduces the need for additional finishing operations and enhances the aesthetics and functionality of the final product.
- Roundness and Straightness: Cylindrical grinding achieves accurate roundness and straightness of cylindrical workpieces, essential for components that require proper alignment and fitment.
- Efficient Material Removal: The process efficiently removes material, especially in cases where large stock removal is needed, leading to reduced machining times and increased productivity.
Profile Grinding
Profile grinding is employed to create complex shapes or contours on the workpiece surface. It is often used in the production of molds, dies, and intricate components.
Applications of Profile Grinding
- Mold and Die Making: Profile grinding is extensively used in mold and die-making to produce intricate shapes and contours on mold cavities, cores, and dies. This ensures precise replication of desired shapes in materials such as plastics, metals, and ceramics.
- Aerospace Components: Aerospace industry applications include the production of turbine blades, engine components, and structural parts with complex profiles that require tight tolerances and superior surface finish.
- Automotive Industry: Profile grinding is applied in the manufacturing of various automotive components, such as gear teeth, camshafts, and transmission parts. These components demand precise profiles and surface finishes for optimal performance.
- Medical Devices: Profile grinding is crucial in producing medical implants, surgical instruments, and orthopedic devices with specialized profiles to ensure proper fitment and functionality.
- Cutting Tools: Profile grinding is used in manufacturing cutting tools like end mills, drills, and inserts. This process imparts precise profiles and cutting geometries to the tools, enhancing their cutting performance and efficiency.
- Consumer Products: Profile grinding is employed to create decorative patterns, engravings, and customized shapes on consumer products such as jewelry, watches, and decorative items.
Advantages of Profile Grinding
- Complex Geometries: Profile grinding excels in producing intricate and complex shapes that are challenging to achieve with other machining processes. It allows manufacturers to create custom profiles with high precision.
- High Accuracy and Precision: Profile grinding offers exceptional accuracy and precision, ensuring that workpieces meet tight tolerances and geometric specifications.
- Superior Surface Finish: The process delivers superior surface finishes, eliminating the need for additional finishing operations and enhancing the aesthetics and functionality of the final product.
- Consistent Replication: Profile grinding allows for consistent replication of specific profiles, ensuring uniformity across multiple workpieces.
- Reduced Tool Wear: Profile grinding can reduce tool wear by precisely controlling the grinding process, resulting in longer tool life and reduced downtime for tool changes.
- Customization and Flexibility: Profile grinding offers flexibility in creating custom profiles, allowing manufacturers to meet unique design requirements and customer preferences.
The Technological Leap of Surface Grinding Machine
Computer Numerical Control (CNC)
The integration of CNC technology has revolutionized surface grinding. CNC-controlled grinding machines offer unprecedented levels of precision, repeatability, and automation. The ability to program intricate grinding paths allows manufacturers to achieve complex surface profiles with remarkable accuracy.
Advanced Grinding Wheels
The development of high-performance grinding wheels has contributed to enhanced material removal rates and surface finish quality. Superabrasive wheels, often embedded with diamond or cubic boron nitride (CBN) particles, enable the grinding of hard and exotic materials, including ceramics and hardened steels.
Coolant and Lubrication Systems
Effective cooling and lubrication are crucial in surface grinding to prevent overheating and maintain dimensional accuracy. Modern grinding machines are equipped with advanced coolant delivery systems that optimize cooling and chip evacuation, resulting in improved surface integrity.
Riding the Trends: Surface Grinding Machine
High-Speed Grinding
As manufacturing demands faster production rates, high-speed grinding has gained traction. This approach involves using grinding wheels that rotate at significantly higher speeds, leading to improved material removal rates and reduced cycle times.
Environmentally Friendly Practices
Sustainability is shaping the future of manufacturing. Surface grinding is adopting environmentally friendly grinding fluids and techniques that minimize waste, reduce energy consumption, and promote responsible manufacturing practices.
In-Process Measurement and Monitoring
Real-time measurement and monitoring systems are becoming integral to surface grinding. These systems ensure dimensional accuracy and surface finish quality by making adjustments on-the-fly, compensating for variations, and reducing scrap rates.
Beyond the Horizons: Surface Grinding Machine
The world of surface grinding continues to evolve, driven by the pursuit of higher precision, efficiency, and sustainability. From traditional techniques to cutting-edge technologies, surface grinding remains a cornerstone of modern manufacturing, enabling the creation of components that meet the highest standards of quality and performance.
In conclusion, surface grinding has been unleashed as a powerful tool that combines artistry with technological innovation. It empowers manufacturers to transform raw materials into finely crafted components, shaping the way we interact with everyday products. As techniques refine, technologies advance, and trends shape the landscape, surface grinding will undoubtedly play a pivotal role in shaping the future of manufacturing. To know about lathe machines and milling machines read more
Conclusion: Surface Grinding Machine
The surface grinding machine stands as a cornerstone of modern manufacturing, bridging the gap between precision craftsmanship and cutting-edge technology. This versatile and precise tool plays a pivotal role in achieving the highest standards of surface finish, dimensional accuracy, and overall product quality across a myriad of industries.
From aerospace to automotive, medical devices to consumer goods, the applications of surface grinding are as diverse as they are essential. The machine’s ability to transform raw materials into finely crafted components with smooth, flat, and precisely dimensioned surfaces shapes the way we interact with and rely on everyday products.
The advantages of surface grinding are undeniable. It offers unparalleled precision, allowing for tight tolerances to be met consistently. The surface finish achieved through this method enhances both the aesthetics and functionality of the end product, often eliminating the need for additional finishing steps. Moreover, surface grinding machines, especially those equipped with CNC technology, contribute to improved efficiency, reduced lead times, and increased productivity.
As industries continue to evolve and demand increasingly intricate designs and superior quality, surface grinding machines remain at the forefront of innovation. The fusion of traditional craftsmanship with advanced automation and digital control systems signifies the enduring relevance and adaptability of this machining technique.
In essence, the surface grinding machine is not merely a tool; it embodies the synthesis of artistry, engineering precision, and technological advancement. It empowers manufacturers to shape a wide array of materials into components that bear the marks of excellence—components that contribute to our daily lives, propel industries forward, and exemplify the remarkable potential of human ingenuity. As we look to the future, the surface grinding machine continues to be a symbol of the relentless pursuit of perfection and the boundless possibilities of modern manufacturing.
I’m thankful you explained to us that precision flat surface grinding is the foundational technique of surface grinding since this involves grinding a workpiece to achieve a flat and parallel surface, which is why it is essential for components that require high-level accuracy and uniformity. My brother runs a manufacturing company, and he needs new grinding equipment for their business operations next year if he wants to continue working with peak performance. I’ll keep this in mind while I help my brother find precision grinding services in Dayton to contact about their machinery products soon.
Thanks sir for your valuable feedback.
If any support requires just ask to us..
Wonderful goods from you, man. I’ve understand your stuff previous to and you are just extremely excellent. I actually like what you have acquired here, really like what you are stating and the way in which you say it. You make it enjoyable and you still care for to keep it wise. I can not wait to read much more from you. This is really a terrific website.