In this article, you will learn about sprue bush, the role of sprue bush in mold, types of sprue bush, sprue bush material selection, sprue bush installation & maintenance, and so on.
What is a Sprue Bush?
A sprue bush, also known as a sprue nozzle, is a cylindrical component used in injection molding machines. It is an essential part of the molding system that connects the injection molding machine’s nozzle to the mold’s runner system. The primary function of the sprue bush is to guide the flow of molten plastic material from the injection molding machine into the mold cavity.
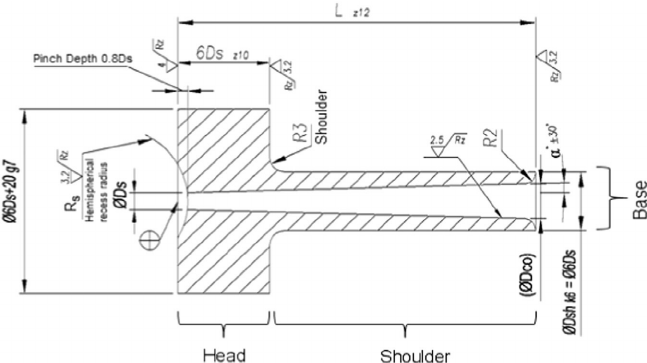
Role of Sprue Bush in Injection Molding
The sprue bush plays a crucial role in the injection molding process. Its main functions include –
1. Material Flow Control
As the molten plastic material is injected into the mold, the sprue bush directs and channels the flow to the mold cavity through the runner system. This ensures that the plastic material reaches all the required parts of the mold, creating the desired product.
2. Preventing Leakage
An essential aspect of sprue bush design is to prevent leakage of molten plastic material from the mold. A well-designed and properly installed sprue bush ensures a tight seal, minimizing the risk of material wastage and maintaining the integrity of the molding process.
3. Pressure Equalization
The sprue bush aids in equalizing the pressure within the mold during the injection process. Proper pressure distribution is vital to avoid defects in the final product, such as voids, sink marks, or warping.
4. Gate Formation
In some cases, the sprue bush itself serves as the gate through which the molten plastic enters the mold cavity. This type of design is common in simple molds with single cavities.
Types of Sprue Bushes
Sprue bushes come in various types and designs to suit different injection molding requirements. Some common types include –
1. Open Sprue Bush
An open sprue bush is a simple design with a direct connection between the injection nozzle and the mold cavity. This type is often used in molds with a single cavity or for products with minimal complexity.
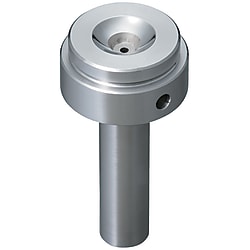
2. Closed Sprue Bush
A closed sprue bush features a small aperture or valve that controls the flow of plastic material into the mold cavity. This design allows for better control over the injection process and minimizes material leakage.
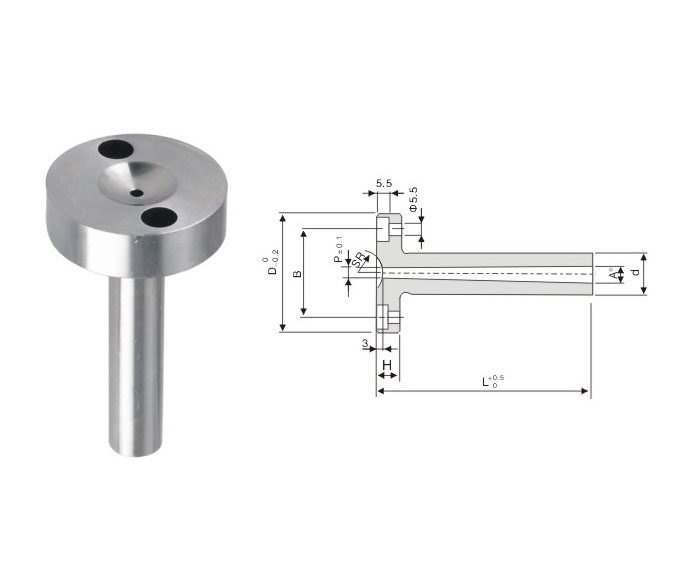
3. Hot Runner Sprue Bush
A hot runner sprue bush incorporates a heating element that keeps the plastic material in the runner system molten at all times. This prevents material cooling and reduces cycle times, making it suitable for high-volume production runs.
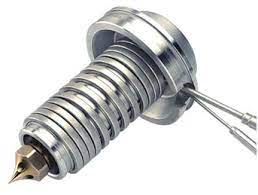
4. Insulated Sprue Bush
Insulated sprue bushes are used when processing temperature-sensitive materials. The insulation helps maintain the required temperature of the molten plastic material as it flows through the sprue bush and into the mold.
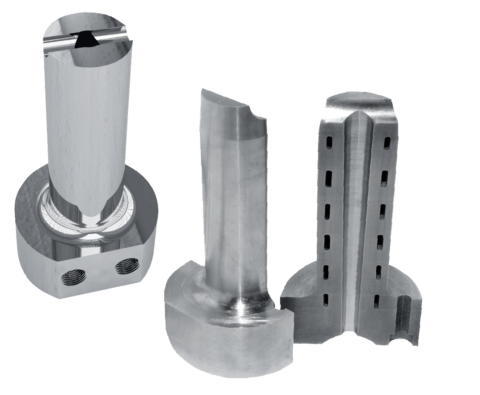
Material Selection for Sprue Bushes
Sprue bushes are typically made from materials that can withstand high temperatures and offer excellent wear resistance. Common materials used for sprue bushes include –
1. Tool Steel
Tool steels, such as H13 or D2, are commonly used for sprue bush manufacturing due to their high strength, toughness, and resistance to wear and thermal fatigue.
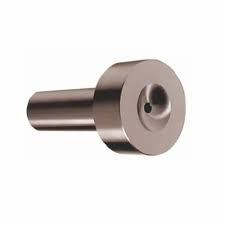
2. Stainless Steel
Stainless steel sprue bushes are preferred when processing corrosive materials or for applications where the risk of contamination needs to be minimized.
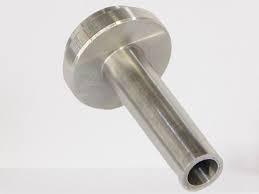
3. Ceramic
Ceramic sprue bushes are used in specific situations where very high processing temperatures are involved. Ceramics offer excellent thermal resistance and are suitable for processing high-temperature engineering plastics.
Design Considerations for Sprue Bushes
Designing an effective sprue bush is critical to the success of the injection molding process. Several factors should be considered during the design phase –
1. Diameter and Length
The diameter and length of the sprue bush should be optimized to ensure a smooth flow of molten plastic material without causing excessive pressure drop or cooling.
2. Gate Size and Location
For sprue bushes that serve as gates, the gate size and location play a crucial role in determining the filling pattern and quality of the final product.
3. Venting
Proper venting is essential to prevent air entrapment in the mold cavity, which can lead to defects in the product. Venting slots or grooves should be incorporated in the sprue bush design.
4. Cooling
A well-designed sprue bush should include cooling channels to help maintain the desired processing temperature and prevent premature solidification of the plastic material.
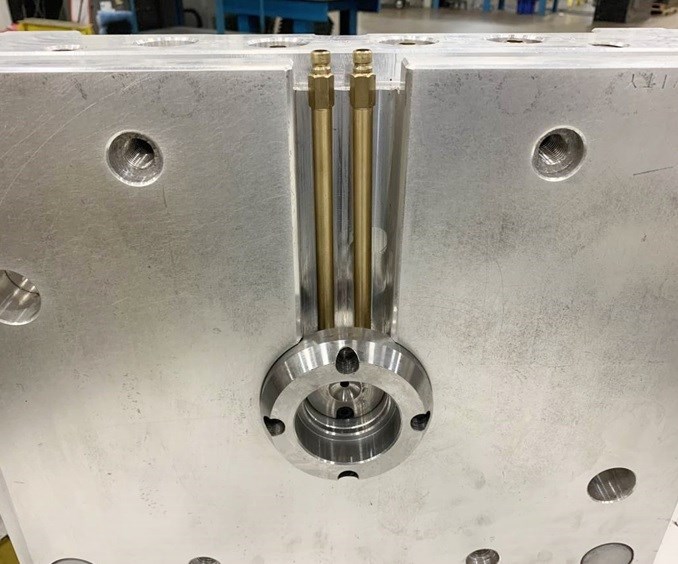
Generally, we provide the cooling system to sprue bush in hot runner molds.
5. Tapered Design
A tapered design in the sprue bush can help ease the demolding process and reduce the risk of part distortion.
Machine Nozzle Radius
The machine nozzle radius refers to the curvature or rounded edge at the end of the injection molding machine’s nozzle, which mates with the sprue bush in the mold. The nozzle radius is an important design consideration and can impact the efficiency and quality of the injection molding process.
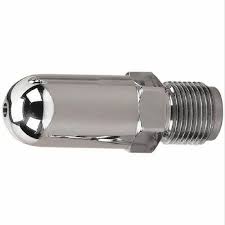
Factors Influenced by the Machine Nozzle Radius
1. Seal
The nozzle radius must fit snugly into the sprue bush to prevent any leaks or material loss during the injection process. A proper seal ensures that molten plastic is forced into the mold cavity without any wastage.
2. Flow Characteristics
The design of the nozzle radius affects the flow of molten plastic into the sprue bush and subsequently into the mold. An optimal nozzle radius can help control flow patterns and minimize the risk of flow-related defects in the final part.
3. Wear and Maintenance
The nozzle radius is subject to wear and tear due to the high temperatures and pressures involved in injection molding. A well-designed nozzle radius can reduce wear and facilitate easier maintenance and replacement.
- Manufacturers and mold designers carefully consider the dimensions and tolerances of both the sprue bush and machine nozzle radius to ensure efficient and reliable injection molding processes. Factors like the type of plastic material, part design, and required production volume also influence the selection and design of these components.
- The sprue bush and machine nozzle radius are critical elements in the injection molding process, working together to facilitate the controlled flow of molten plastic into the mold cavity. Proper design and maintenance of these components are essential for achieving high-quality plastic parts and optimizing the overall efficiency of the injection molding operation.
Sprue Bush Installation & Maintenance
Proper installation and regular maintenance of the sprue bush are essential to ensure its effective functioning and longevity. Some key points to consider –
1. Precise Alignment
During installation, ensure that the sprue bush is precisely aligned with the mold’s runner system and nozzle to avoid leakage and uneven material flow.
2. Cleaning and Lubrication
Regular cleaning and lubrication of the sprue bush will help prevent material buildup and ensure smooth operation.
3. Periodic Inspection
Periodically inspect the sprue bush for signs of wear, damage, or deformation. Replace it when necessary to maintain optimal performance.
Sprue Bush Standard Size
The standard size of a sprue bush can vary depending on the specific requirements of the injection molding process, the type of material being used, and the design of the mold. However, there are some common industry practices and guidelines that are often followed.
- The typical outer diameter (OD) of a sprue bush ranges from 10 mm to 25 mm (0.4 inches to 1 inch). The inner diameter (ID) of the sprue bush is usually designed to match the diameter of the injection molding machine’s nozzle, which can also vary based on the machine’s specifications.
- The length of the sprue bush is determined by the thickness of the mold plates and the distance required to guide the molten plastic material into the mold cavity. It can range from around 25 mm to 75 mm (1 inch to 3 inches) or more.
- The size of the gate, which is the aperture in the sprue bush that controls the flow of molten plastic into the mold cavity, can vary depending on the requirements of the specific part being molded. Gate sizes are typically in the range of 1 mm to 4 mm (0.04 inches to 0.16 inches) or more.
- It’s important to note that these dimensions are general guidelines, and the actual size of the sprue bush will be determined by factors such as the part geometry, wall thickness, injection molding machine specifications, and the material being used. Additionally, custom molds or specialized applications may require unique sprue bush designs and sizes.
- To ensure the proper functioning and efficiency of the injection molding process, mold designers and manufacturers carefully consider the size and specifications of the sprue bush to match the specific requirements of the project.
Sprue Bush Angle
- The sprue bush angle, also known as the draft angle or taper, refers to the slight incline or angle applied to the inner walls of the sprue bush in an injection mold. This angle is specifically designed to facilitate the ejection of the molded part from the mold without causing damage or deformation.
- The sprue bush angle is a critical design consideration in injection molding because it helps address the issue of “undercut.” Undercut occurs when a feature of the molded part, such as a sidewall or rib, is perpendicular to the direction of the mold opening. If there were no draft angle, the part would become trapped in the mold, making it difficult or impossible to eject without potentially damaging the part or the mold.
- By adding a draft angle to the sprue bush, the mold designer ensures that the molten plastic material flows smoothly into the mold cavity during injection and that the part can be easily ejected afterward. The draft angle allows the part to release from the mold without clinging to the sprue bush or other mold components.
- The optimal sprue bush angle depends on various factors, including the type of plastic material being used, the complexity of the part design, and the specific requirements of the molding process. Generally, draft angles of 1 to 3 degrees are common for most injection molding applications.
- However, it’s essential to strike a balance when determining the draft angle, as a larger angle can make it easier to eject the part, but it might also result in additional flash (excess material) around the parting line, increasing waste and post-processing efforts. On the other hand, too small of a draft angle might make ejection difficult, leading to potential part damage or production issues.
Sprue Bush Replacement
Sprue bush replacement is a maintenance procedure in injection molding that involves removing the existing sprue bush and installing a new one. The sprue bush is a critical component that connects the injection molding machine’s nozzle to the mold, allowing molten plastic to flow into the mold cavity.
Reasons for Sprue Bush Replacement
1. Wear and Tear
Due to the high temperatures and pressures involved in the injection molding process, the sprue bush is subject to wear and can degrade over time.
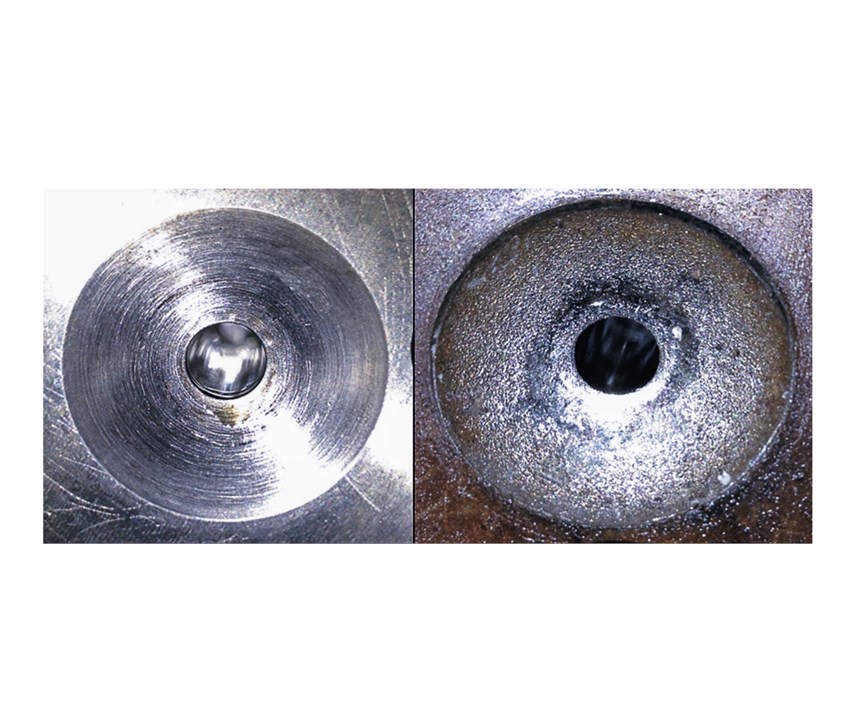
2. Damage
Accidents or mishandling during production can cause damage to the sprue bush, affecting its performance and integrity.
3. Material Change
When switching to a different type of plastic material for molding, the sprue bush may need replacement to match the new material’s requirements.
4. Design Changes
Mold modifications or improvements might necessitate changes to the sprue bush to optimize the molding process.
Sprue Bush Replacement Procedure
1. Mold Inspection
The mold is inspected to identify any signs of wear, damage, or other issues with the current sprue bush.
2. Removal
The old sprue bush is carefully removed from the mold using appropriate tools and techniques.
3. Cleaning
The area around the sprue bush location is cleaned to ensure a smooth surface for the new sprue bush installation.
4. New Sprue Bush Installation
A new sprue bush, designed to match the specific mold and production requirements, is inserted into the mold.
5. Alignment
The sprue bush is aligned properly to ensure a good fit with the injection molding machine’s nozzle.
6. Fastening
The new sprue bush is securely fastened in place within the mold to prevent movement during the molding process.
7. Testing
After replacement, the mold might undergo testing to ensure the sprue bush functions correctly and that there are no leaks or defects.
- Regular sprue bush replacement and proper maintenance are essential to ensure the efficient and reliable operation of the injection molding process. Well-maintained sprue bushes help prevent part defects, reduce downtime, and improve the overall quality and productivity of the molding process.
Troubleshooting Common Sprue Bush Issues
Despite careful design and maintenance, sprue bushes may encounter issues during the injection molding process. Here I talk about how to deal with these issues –
1. Material Leakage
If material leakage occurs at the sprue bush, check for improper alignment, worn seals, or damage to the bush surface. Address these issues promptly to avoid material wastage.
2. Gate Blockage
A blocked gate can lead to incomplete filling of the mold cavity. Check for obstructions and clear the gate if necessary.
3. Premature Solidification
If the plastic material solidifies too quickly in the sprue bush, it may cause flow disruptions. Ensure proper cooling and heating to maintain the required temperature.
Conclusion
sprue bushes are a crucial component in the injection molding process, providing essential material flow control and pressure equalization. While they offer numerous advantages in terms of product quality, efficiency, and compatibility with hot runner systems, they also have some drawbacks, including material waste, maintenance requirements, and potential design complexities. However, by choosing the right material, careful design, and regular maintenance, manufacturers can harness the benefits of sprue bushes and enhance their injection molding operations.
What are the Pros and Cons of Sprue Bush?
Pros of Sprue Bush for Injection Molding –
1. Material Flow Control: Sprue bushes play a crucial role in directing the flow of molten plastic material from the injection molding machine into the mold cavity. This control ensures that the material reaches all the necessary parts of the mold, resulting in a well-formed and accurate final product.
2. Preventing Material Leakage: A properly designed and installed sprue bush helps maintain a tight seal between the injection nozzle and the mold. This prevents material leakage during the injection process, reducing material waste and ensuring a more efficient molding operation.
3. Pressure Equalization: Sprue bushes aid in equalizing the pressure within the mold during the injection process. Proper pressure distribution is essential for producing high-quality parts and minimizing defects like voids or sink marks.
4. Gate Formation and Control: In certain designs, the sprue bush serves as the gate through which the molten plastic enters the mold cavity. This allows for controlled gate sizing and placement, contributing to better part quality and reduced waste.
5. Compatibility with Hot Runner Systems: Sprue bushes can be integrated into hot runner systems, which keep the plastic material in the runner system molten at all times. This results in reduced cycle times and increased productivity for high-volume production runs.
6. Material Options for Various Requirements: Sprue bushes can be made from different materials, including tool steel, stainless steel, and ceramic, to suit specific molding requirements. The material selection ensures the sprue bush’s durability, resistance to wear, and corrosion protection.
7. Ease of Maintenance: Regular maintenance of sprue bushes is relatively straightforward. Cleaning and lubrication help prevent material buildup and ensure smooth operation.
Cons of Sprue Bush for Injection Molding
1. Material Waste: While sprue bushes help prevent material leakage during the injection process, there will still be some material loss in the form of sprue, runners, and gates. This material waste can add to the overall production costs.
2. Flow Disruptions: If the sprue bush is not properly designed or maintained, it can lead to flow disruptions in the mold cavity. These disruptions may result in incomplete filling, voids, or other defects in the final product.
3. Tooling Costs: The design, manufacturing, and installation of sprue bushes add to the overall tooling costs of injection molding. However, this cost is usually considered essential for the efficiency and quality of the molding process.
4. Demolding Challenges: In some cases, the design of the sprue bush may cause challenges during the demolding process. Improperly designed sprue bushes can lead to part distortion or difficulties in removing the finished product from the mold.
5. Maintenance and Replacement: Sprue bushes may experience wear and tear over time due to the high temperatures and pressures involved in injection molding. Regular inspection and replacement may be required to maintain optimal performance.
6. Design Complexity: As the injection molding process becomes more complex, the design of sprue bushes may also become more intricate. This complexity may increase the risk of design errors and the need for careful attention during the molding process.
7. Mold Size and Configuration: In large and complex molds, the design and placement of sprue bushes can be challenging. Ensuring uniform material flow and pressure distribution in such molds can be more demanding, requiring precise engineering.