Introduction
In the world of injection molding, precision is paramount. It’s an industry where the slightest imperfection in the mold or the tiniest inconsistency in the material can lead to costly defects and production delays. To achieve the high standards of quality and efficiency that this industry demands, injection molders turn to a variety of tools and techniques, and one of the unsung heroes in their arsenal is silicone spray.
Silicone spray, a lubricant and release agent, plays a crucial role in the injection molding process. In this article, we’ll explore the many facets of silicone spray, from its composition to its applications, and uncover the best practices that make it a game-changer for injection molders.
Understanding Silicone Spray
Before we dive into its best practices, let’s get to know silicone spray a little better. At its core, silicone spray is a lubricant and release agent formulated with silicone oil. This silicone oil is suspended in a solvent carrier, which allows for easy application and even distribution.
Composition of Silicone Spray –
- Silicone Oil: This is the active ingredient responsible for providing lubrication and acting as a release agent.
- Solvent Carrier: The solvent serves as a carrier for the silicone oil, allowing it to be evenly sprayed onto the mold surface. Common solvents include acetone or isopropanol.
- Propellant: In aerosol forms of silicone spray, a propellant is used to dispense the product from the container.
Now that we have a basic understanding of what silicone spray is let’s delve into its best practices in the context of injection molding.
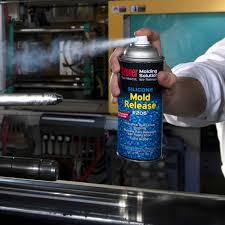
How to use Silicone Spray?
Using silicone spray on a mold is a crucial step in the injection molding process to ensure smooth and efficient operation. Silicone spray acts as a release agent, preventing molded parts from sticking to the mold cavity and promoting easy ejection. Here’s a step-by-step guide on how to use silicone spray effectively in mold preparation –
Note: Always follow safety guidelines and wear appropriate personal protective equipment (PPE) when working with this spray, as it may produce fumes that can be harmful if inhaled.
1. Prepare the Mold
Before applying this spray, ensure that the mold is clean and free of contaminants. Proper mold preparation is essential to achieve optimal results. Follow these steps:
- Clean the mold: Remove any residue, dirt, or previous mold release agents from the mold surface. Use a suitable mold cleaner and a lint-free cloth or paper towel to wipe down the mold thoroughly.
- Inspect the mold: Check for any damage, wear, or irregularities on the mold surface that may affect the molding process. Address any issues before proceeding.
- Preheat the mold (optional): Some molders choose to preheat the mold to the desired operating temperature. Preheating helps the silicone spray adhere better to the mold surface.
2. Shake the Silicone Spray Can
Shake the silicone spray canister vigorously before use. This ensures that the silicone oil and solvent carrier are properly mixed, leading to an even distribution of the spray.
3. Apply Silicone Spray
Follow these guidelines for applying silicone spray to the mold:
- Maintain proper ventilation: Work in a well-ventilated area or wear a respirator if necessary, as the solvent carrier may produce fumes.
- Hold the spray can at the correct angle: Position the spray can at a 45-degree angle to the mold surface for optimal coverage.
- Maintain the right distance: Hold the spray canister approximately 8 to 12 inches away from the mold to avoid overspray and ensure even coverage.
- Apply a light, even coat: Spray the silicone evenly across the entire mold surface, moving the canister in a sweeping motion. Ensure that no areas are missed, but avoid over-applying, which can lead to excess buildup.
- Allow for drying time: Give the silicone spray some time to dry, typically a few minutes, before proceeding with the molding process. The drying time may vary depending on environmental conditions and the specific silicone spray product used.
4. Perform Trial Runs
Before starting full-scale production, it’s advisable to conduct trial runs with the silicone-sprayed mold to ensure that the release agent performs as expected. Verify that molded parts are easily ejected and exhibit the desired surface finish.
5. Record Usage and Maintenance
Maintain a record of silicone spray usage, including application dates and quantities used. Regularly clean the spray nozzle to prevent clogs that can affect the even distribution of the spray. Proper maintenance and documentation help track the effectiveness of the silicone spray and ensure consistent results.
By following these steps and best practices, you can effectively use silicone spray in mold preparation, enhancing the efficiency and quality of the injection molding process while preventing parts from sticking to the mold cavity.
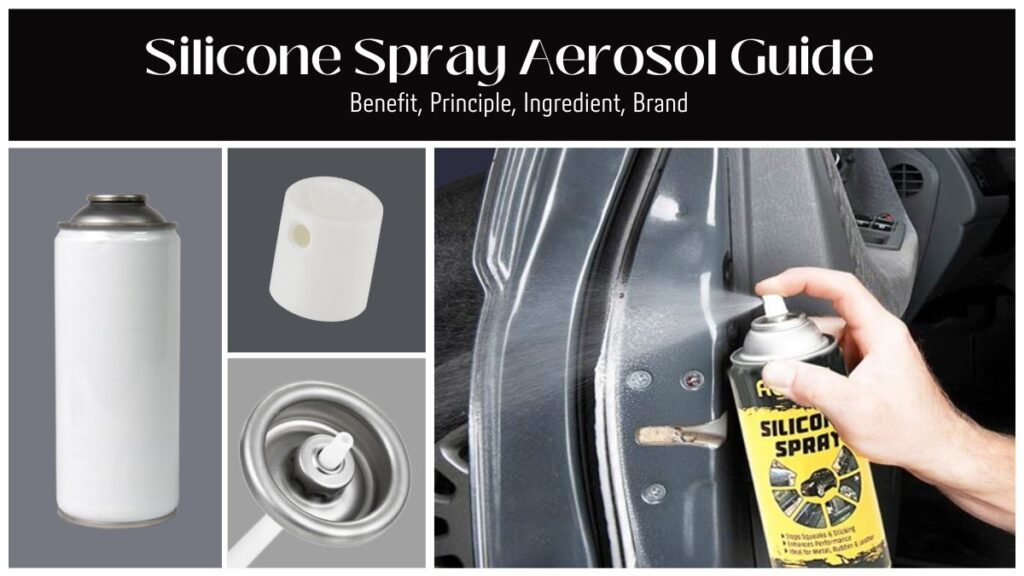
Silicone Spray Best Practices
1. Proper Application Technique
- Even Coating: Apply silicone spray evenly across the mold surface to ensure consistent coverage.
- Distance: Maintain an appropriate spraying distance, typically 8-12 inches from the mold, to avoid overspray and ensure efficient coverage.
- Spray Angle: Use a 45-degree angle for optimal coverage and minimal wastage.
2. Cleaning and Prepping the Mold
- Cleanliness: Before applying silicone spray, ensure that the mold is clean and free of contaminants, such as residue from previous runs.
- Preheating: Preheat the mold to the desired temperature, as this helps the silicone spray adhere better to the surface.
3. Proper Ventilation
- Safety First: Always work in a well-ventilated area and wear appropriate personal protective equipment (PPE) to avoid inhaling fumes from the solvent carrier.
4. Storage and Handling
- Storage Temperature: Store silicone spray at the recommended temperature to prevent separation of the silicone oil and solvent.
- Shake Well: Shake the canister well before use to ensure proper mixing of the silicone oil and solvent.
5. Regular Maintenance
- Clean Nozzles: Regularly clean the spray nozzle to prevent clogs that can affect the even distribution of the spray.
- Inspect for Contamination: Check the silicone spray for any contamination that might affect the molding process.
6. Testing and Verification
- Trial Runs: Conduct trial runs with the silicone spray to ensure it performs as expected and doesn’t negatively impact the quality of molded parts.
- Documentation: Maintain records of silicone spray usage, including application dates and quantities used, to track its effectiveness.
Applications of Silicone Spray in Injection Molding
Silicone spray serves multiple critical functions in the injection molding process –
1. Release Agent
- It acts as an effective mold release agent, preventing the molded parts from sticking to the mold cavity.
- This promotes smooth ejection of the parts, reducing the risk of damage and production delays.
2. Lubrication
- It provides lubrication to moving components within the mold, such as ejector pins and slides.
- This reduces friction and wear, extending the lifespan of mold components.
3. Surface Enhancement
- It can improve the surface finish of molded parts by reducing surface imperfections and enhancing overall part aesthetics.
4. Temperature Regulation
- By promoting efficient mold release, spray silicone helps maintain consistent temperatures within the mold, which is crucial for quality control.
5. Tool Preservation
- The use of this spray, helps protect and preserve the integrity of the mold, prolonging its lifespan and reducing the need for frequent mold replacements.
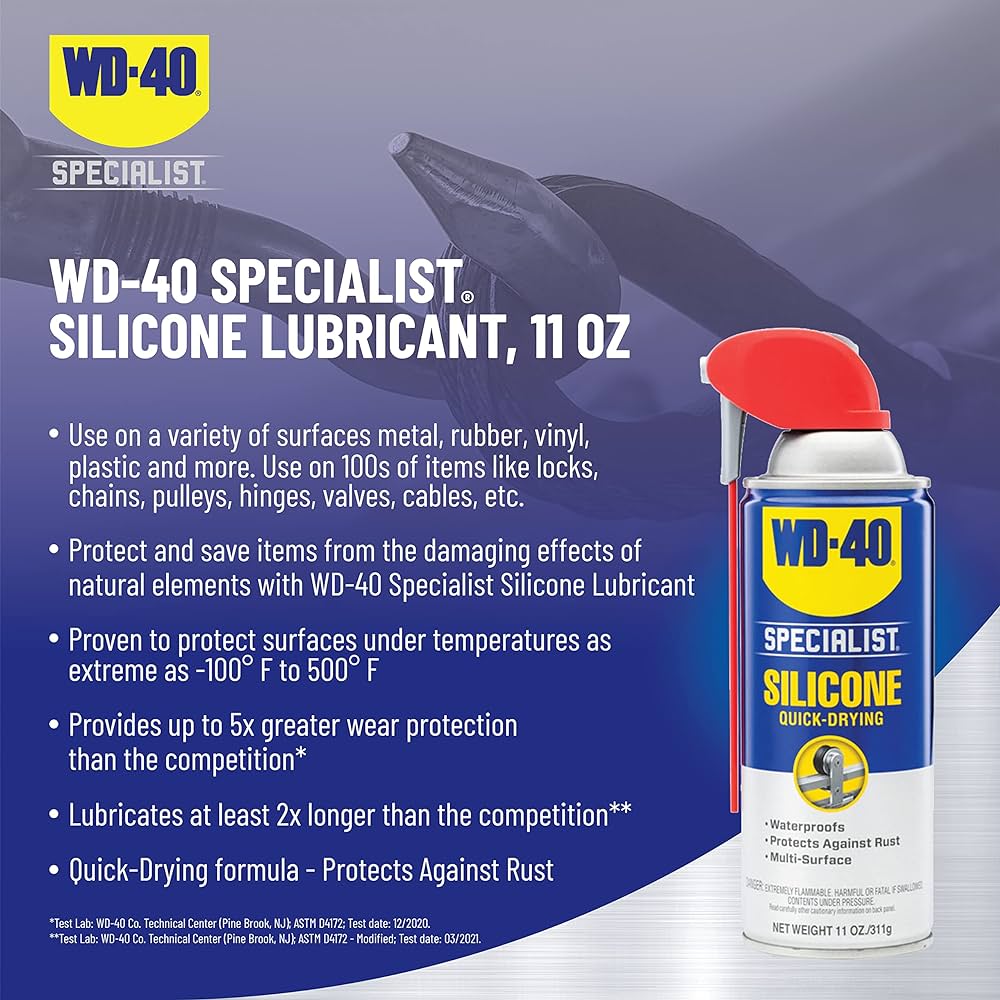
Challenges and Considerations
While silicone spray offers numerous benefits to injection molders, there are some challenges and considerations to keep in mind –
1. Residue Buildup
- Over time, repeated use of silicone spray can lead to residue buildup on the mold surface. Proper mold maintenance and cleaning are essential to mitigate this issue.
2. Material Compatibility
- Some materials may be sensitive to silicone contamination, which can affect part adhesion or subsequent processes like painting or bonding. Ensure compatibility with the materials being molded.
3. Environmental Impact
- Consider the environmental impact of spray silicone, especially in high-usage scenarios. Some silicone spray formulations are designed to be more eco-friendly.
4. Regulatory Compliance
- Be aware of regulatory requirements and compliance standards, especially when using silicone spray in industries with stringent quality and safety regulations.
Silicone Spray – MSDS
The Material Safety Data Sheet (MSDS), now commonly referred to as the Safety Data Sheet (SDS) in many regions, plays a crucial role in providing essential information about the properties, hazards, and safe handling of substances and products, including silicone spray. Here’s how the MSDS/SDS contributes to the safe and responsible use of spray silicone –
- Hazard Identification: The SDS for silicone spray provides a detailed overview of potential hazards associated with the product. This includes information on any hazardous ingredients, physical and chemical properties, and the overall risk profile. This section helps users understand the specific risks and precautions needed when handling the product.
- Composition and Ingredient Information: The SDS lists the chemical composition of the silicone spray, including its primary ingredients and any additives. This information is vital for users who need to assess potential health and environmental impacts.
- First Aid Measures: In the event of accidental exposure or contact with the product, the SDS provides guidance on appropriate first aid measures. This may include instructions for eye contact, skin contact, ingestion, or inhalation.
- Fire-fighting Measures: The SDS outlines fire hazards associated with the product and provides recommendations for extinguishing fires involving the substance. It also describes any firefighting equipment or techniques that should be used.
- Accidental Release Measures: In case of a spill or accidental release of silicone spray, the SDS offers guidance on containment, cleanup procedures, and protective measures to prevent exposure.
- Handling and Storage: This section provides essential information on safe handling practices, including recommended protective equipment and precautions for storage, such as temperature and humidity considerations.
- Exposure Controls/Personal Protection: The SDS details exposure limits, ventilation requirements, and personal protective equipment (PPE) recommendations for individuals working with the product. This section is crucial for ensuring the safety of workers.
- Physical and Chemical Properties: Users can find information about the physical and chemical characteristics of the product, such as its appearance, odor, and stability. This data helps individuals understand the product’s behavior under various conditions.
- Toxicological Information: The SDS includes toxicological data, which provides insights into the potential health effects of exposure to the product. This information aids in risk assessment and the development of safety protocols.
- Ecological Information: For environmentally conscious users, the SDS may contain ecological data, including information on the product’s impact on the environment, aquatic toxicity, and biodegradability.
- Disposal Considerations: Proper disposal of silicone spray is essential to minimize environmental impact. The SDS offers guidance on safe disposal methods and any regulatory requirements.
- Transport Information: When transporting silicone spray, users can refer to the SDS for information on transport classification, labeling requirements, and any restrictions or precautions associated with shipping.
- Regulatory Information: The SDS often includes regulatory information, such as hazard classifications and compliance with specific regulations or standards, depending on the region or jurisdiction.
- Other Information: Any additional information or recommendations related to the product’s safe use, storage, or disposal may be provided in this section.
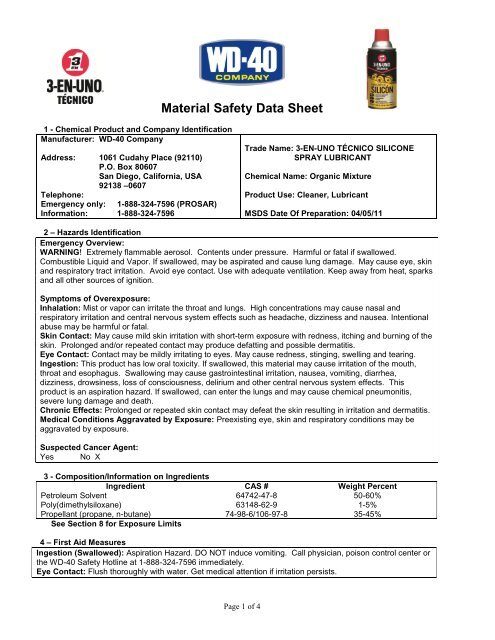
Conclusion
Silicone spray, often overlooked but indispensable, is a versatile tool that injection molders rely on for achieving precision, efficiency, and quality in their operations. By adhering to best practices in its application and maintenance, injection molders can harness the full potential of silicone spray. Its role as a release agent, lubricant, and surface enhancer makes it a game-changer in the injection molding industry, contributing to smoother production processes, reduced downtime, and enhanced product quality. As the injection molding industry continues to evolve, spray silicone remains a steadfast ally in the pursuit of perfection.
FAQ’s
What is Silicone Spray Used for?
This spray is a versatile lubricant and release agent used in various applications. It prevents sticking and enhances smooth movement in mechanical components, serves as a mold release agent in manufacturing processes like injection molding, lubricates locks and hinges, and protects surfaces from moisture and corrosion.
What are the disadvantages of Silicone Spray?
Silicone spray, while versatile, has some disadvantages. It can leave a residue on surfaces over time, which may require frequent cleaning. In certain applications, like painting or adhesive bonding, silicone residue can hinder adhesion. Additionally, its use near high-heat applications can produce harmful fumes.
What will remove the Silicone Spray?
Silicone spray residue can be removed using several methods, including –
Solvents: Isopropyl alcohol or acetone can dissolve and remove silicone residue.
Degreasers: Commercial degreasers can effectively clean surfaces.
Scrubbing: Mechanical scrubbing with a brush or abrasive pad can remove stubborn residue.
Heat: In some cases, heating the residue can soften it for easier removal. Always test on a small, inconspicuous area before applying any method to a larger surface.
Is Silicone Spray safe?
It is generally safe when used as directed, following safety precautions. It poses minimal health risks if handled properly, but inhalation of fumes or prolonged skin contact should be avoided. Users should wear appropriate personal protective equipment (PPE) and work in well-ventilated areas to ensure safety during application.
Does Silicone Spray stop rust?
Yes, this spray can provide a protective barrier that helps inhibit rust formation on metal surfaces. It repels moisture and prevents water from reaching the metal, reducing the risk of corrosion. However, it may not be as effective as specialized rust inhibitors or coatings for long-term rust prevention.
How long does Silicone Spray take to dry?
The drying time of silicone spray can vary depending on environmental conditions and the specific product formulation. Generally, silicone spray dries within a few minutes after application. However, factors like temperature, humidity, and thickness of the application can affect the drying time.
What is Non Silicone Spray? Write its uses.
Non-silicone spray, often referred to as silicone-free spray, is a lubricant and release agent that doesn’t contain silicone compounds. It is used in various applications where silicone contamination is undesirable. Common uses include –
Industrial Maintenance: Lubricating machinery and equipment, especially in environments sensitive to silicone contamination.
Painting and Coating: As a mold release agent or parting agent to prevent adhesion in painting and coating processes.
Woodworking: Reducing friction on cutting tools, saw blades, and woodworking machinery.
Printing: Preventing ink buildup on printing presses and ensuring smooth paper feed.
Automotive: Lubricating rubber and plastic components without causing compatibility issues.
Textile Industry: Reducing friction in sewing machines and textile production.
Non-silicone spray is favored in applications where silicone residue can negatively impact adhesion, painting, or subsequent processes. It offers an alternative to silicone-based lubricants and release agents.
Silicone Spray Brands & Manufacturers.
Here are 10 well-known silicone spray brands and manufacturers, along with a brief explanation of their products –
WD-40 Specialist Silicone Spray: WD-40 is a trusted name in lubricants and maintenance products, offering a spray that provides lubrication and protection for various applications.
CRC Silicone Spray: CRC manufactures a range of sprays silicone designed for industrial and automotive use. Their products offer lubrication, protection, and water repellency.
3M Silicone Lubricant: 3M produces silicone-based lubricants and sprays used in industries like automotive, manufacturing, and maintenance for reducing friction and preventing sticking.
Permatex Silicone Spray Lubricant: Permatex offers spray silicone that lubricate, waterproof, and protect surfaces. They are widely used in automotive and home repair applications.
Loctite Silicone Spray: Loctite produces silicone sprays that provide lubrication and protection against moisture and corrosion. They are suitable for various industries, including manufacturing and maintenance.
Blaster Silicone Lubricant: Blaster’s silicone lubricant is known for its versatility and effectiveness in reducing friction, preventing rust, and protecting surfaces in industrial and automotive settings.
Super Lube Silicone Lubricating Brake Grease: Super Lube manufactures silicone-based lubricants, including brake grease used in automotive and heavy-duty applications for enhanced performance and corrosion resistance.
Sprayon S00210 Silicone Release Agent: Sprayon offers silicone release agents designed to facilitate easy mold release in manufacturing and molding processes.
Misty Silicone Lubricant: Misty’s silicone lubricant products are used in various industries to reduce friction, protect surfaces, and provide long-lasting lubrication.
GUNK M506C Silicone Lubricating Spray: GUNK produces silicone lubricating sprays that are suitable for automotive, marine, and industrial applications, offering protection against moisture and corrosion.
These brands and manufacturers offer a wide range of spray silicone products, catering to the diverse needs of industries, from automotive maintenance to industrial manufacturing and beyond.