Injection molding is a versatile manufacturing process, known for its ability to produce complex, durable, and high-precision components. Overmolding, a specialized technique within the realm of injection molding, takes this versatility a step further by combining multiple materials or substrates to create integrated, multi-material products. In this comprehensive guide, we will demystify overmolding by exploring its techniques, benefits, and wide-ranging applications across various industries.
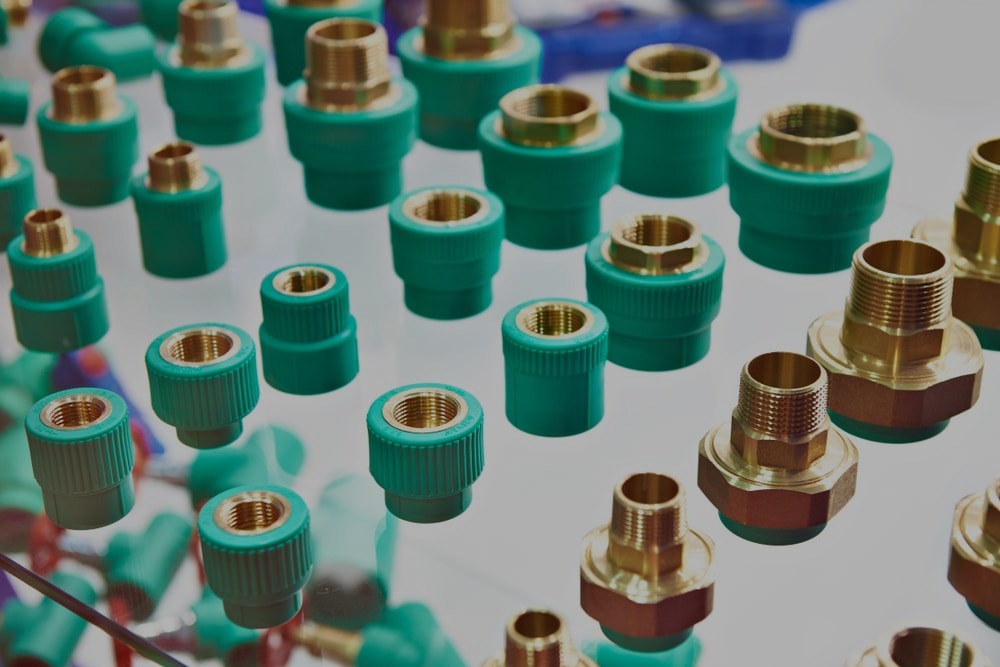
Understanding Overmolding
Overmolding is a manufacturing process where a base or substrate, typically made of plastic, metal, or another material, is molded over or around another material, known as the insert or core. This results in a single, integrated component with distinct layers or sections composed of different materials. The primary goal of over-molding is to enhance product functionality, aesthetics, durability, or ergonomics.
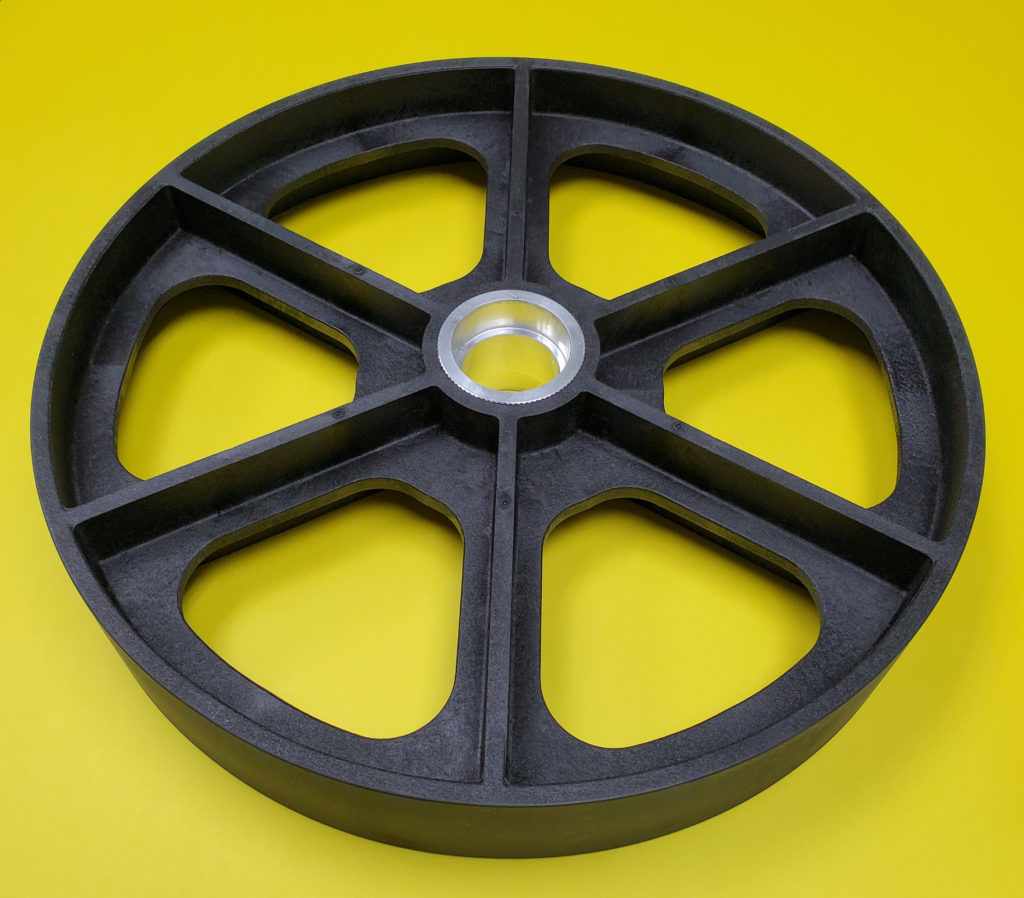
Overmolding Techniques
Overmolding requires careful planning and execution to ensure successful adhesion between the materials involved. There are several techniques commonly used in over-molding –
1. Two-Shot Overmolding
- In this technique, the first material (usually the substrate) is injected into the mold cavity during the initial molding cycle.
- The mold is then partially opened, and the second material is injected to encapsulate the first material.
- Two-shot over-molding allows for precise control over the interface between the materials.
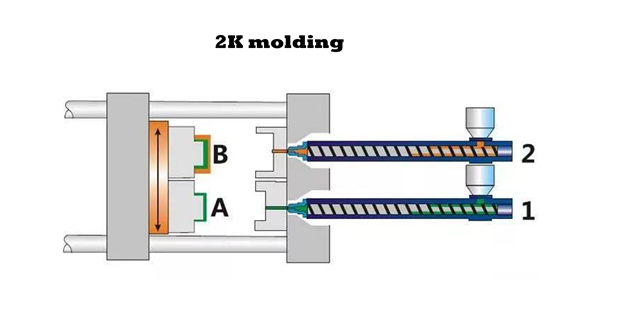
2. Insert Molding
- In insert molding, an existing part or insert, often made of metal or plastic, is placed into the mold cavity.
- The molten material is then injected, enveloping and bonding with the insert.
- This technique is commonly used in electrical connectors, where metal pins are over-molded with plastic.
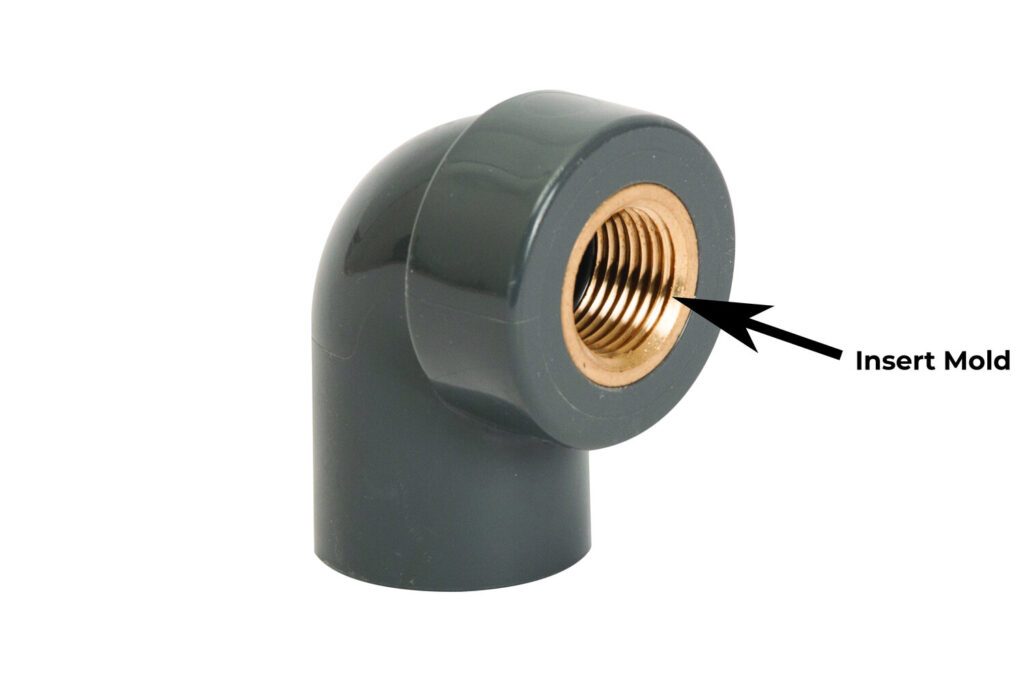
3. Multi-Material Injection Molding
- Multi-material molding uses advanced machinery and molds to inject multiple materials simultaneously or sequentially.
- It allows for complex geometries and can achieve precise material placement within the mold.
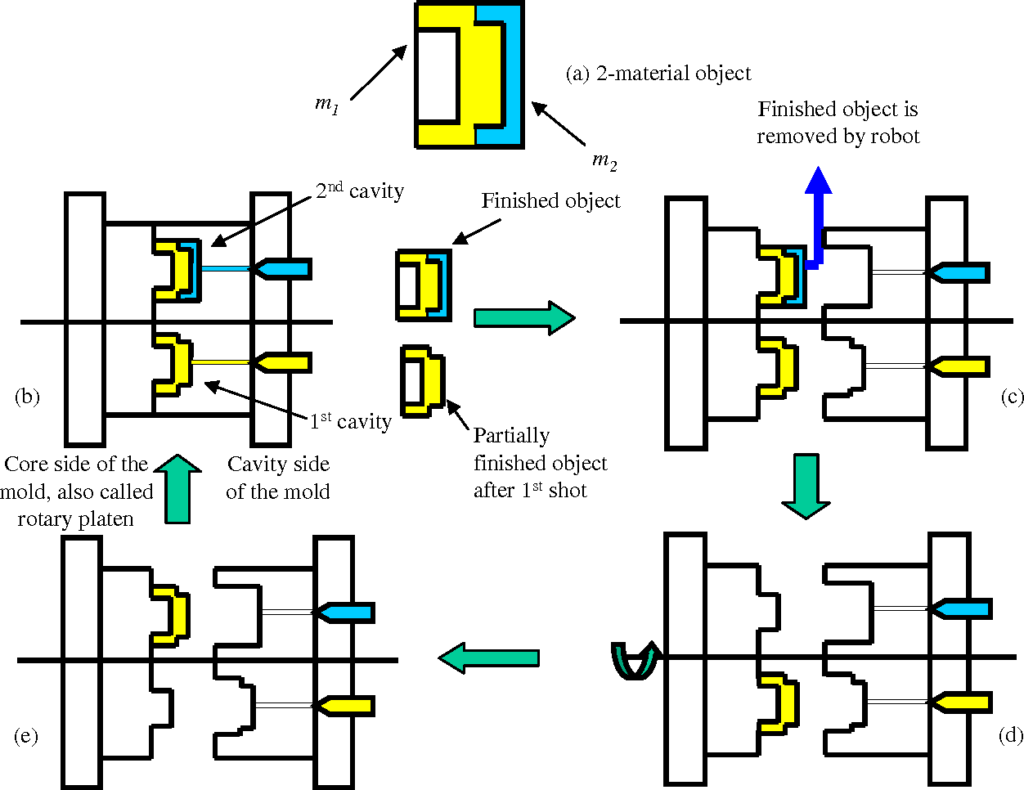
4. Hard-Soft Overmolding
- In hard-soft over-molding, a rigid material (hard plastic) is combined with a soft, elastomeric material (rubber or TPE) to create a product with both rigid and flexible sections.
- This technique is widely used in tool grips, handles, and medical devices.
Benefits of Overmolding
Overmolding offers a range of advantages that make it a preferred choice in various industries –
1. Enhanced Functionality
- Overmolding allows for the integration of multiple materials, enabling products with improved functionality, such as better grip, cushioning, or sealing.
2. Reduced Assembly
- By combining multiple components into a single over-molded part, manufacturers can reduce assembly steps, minimize labor costs, and lower the risk of assembly errors.
3. Improved Aesthetics
- Overmolding enables the incorporation of contrasting colors, textures, and finishes, enhancing the visual appeal of products.
4. Durability and Strength
- The bonding between materials in over-molding often results in increased durability and strength, particularly in areas prone to wear and tear.
5. Waterproofing and Sealing
- Overmolding can create water-tight seals, making products resistant to moisture, chemicals, and environmental factors.
6. Vibration Damping
- Soft over-molded materials, like rubber or TPE, absorb vibrations and reduce noise, making them ideal for tool handles and electronic devices.
7. Ergonomic Design
- Overmolding allows for the creation of ergonomic and comfortable grips, handles, and interfaces, improving user experience.
Applications Across Industries
Overmolding finds applications in a wide range of industries, each benefiting from its unique properties and advantages –
1. Consumer Electronics
- Overmolding is commonly used in electronic devices, such as remote controls and handheld gadgets, to provide durability, aesthetics, and improved ergonomics.
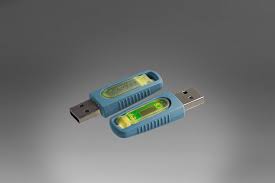
2. Automotive
- The automotive industry employs over-molding in interior components, including steering wheel grips, shift knobs, and dashboards, for enhanced comfort and aesthetics.
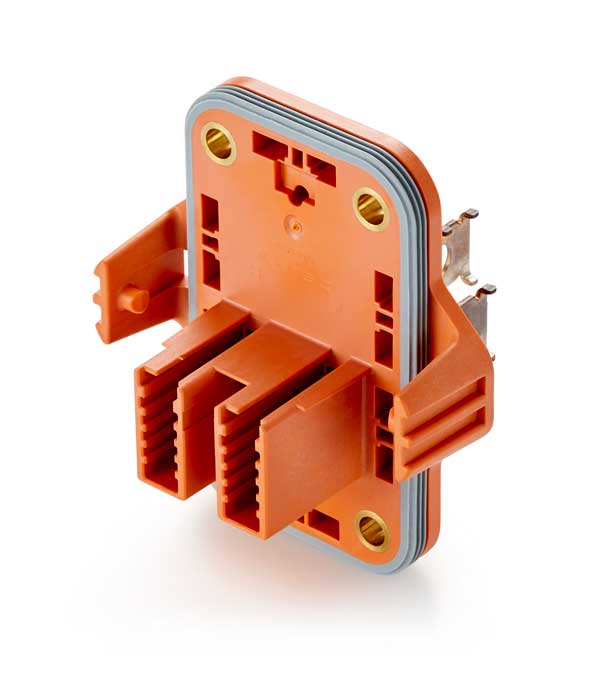
3. Medical Devices
- Overmolding is crucial in the medical field, where soft, biocompatible materials are overmolded onto device housings and handle to ensure patient comfort and safety.
4. Tooling and Equipment
- Hand tools, power tools, and industrial equipment benefit from over-molding to create ergonomic handles and improve grip and vibration damping.
5. Consumer Products
- Items like toothbrushes, razors, and kitchen utensils use over-molding to enhance aesthetics and ergonomic design.
6. Aerospace
- The aerospace industry utilizes over-molding in aircraft interiors for improved passenger comfort and safety.
7. Electrical Connectors
- Overmolding is a standard practice in the production of electrical connectors, ensuring insulation, strain relief, and environmental protection.
8. Sporting Goods
- Products like bicycle grips, golf club handles, and fitness equipment employ over-molding to optimize grip and comfort.
Material Selection in Overmolding
The success of an over-molding project heavily depends on selecting compatible materials. Factors to consider include –
- Adhesion: Ensuring that the two materials adhere well to each other.
- Thermal Compatibility: Materials should have similar melting and cooling rates.
- Chemical Compatibility: Compatibility with any chemicals or solvents the part may encounter.
- Mechanical Properties: Material selection should align with the desired mechanical characteristics of the final part.
Common material combinations in over-molding include thermoplastic elastomers (TPE) over rigid plastics, rubber over metal, and silicone over plastic.
Design Considerations
Effective design is critical in over-molding projects. Key design considerations include –
- Proper Fit: The insert should fit snugly within the mold cavity to prevent flash or gaps.
- Material Flow: Design the mold to ensure proper material flow and adhesion between layers.
- Gate Placement: Strategically position gates to minimize material flow disruption and ensure even distribution.
- Shrinkage and Warpage: Account for material shrinkage and warpage during the design phase.
Overmolding Challenges
While over-molding offers numerous benefits, it also presents challenges –
- Material Compatibility: Ensuring that the selected materials bond effectively can be challenging.
- Cycle Time: Overmolding often requires longer cycle times due to cooling requirements.
- Tooling Complexity: Designing molds for overmolding can be complex and costly.
- Quality Control: Ensuring consistent quality and adhesion between layers is crucial.
Conclusion
Overmolding is a versatile and innovative manufacturing technique with applications across a spectrum of industries. By understanding its techniques, benefits, and challenges, manufacturers can harness the full potential of over-molding to create products that excel in functionality, aesthetics, and durability. As technology and materials continue to evolve, over-molding is poised to play an even more significant role in shaping the products of the future.
FAQ’s
What is an example of Overmolding?
An excellent example of over-molding can be found in the manufacturing of toothbrushes. Overmolding is employed to enhance the functionality, aesthetics, and comfort of toothbrush handles. Here’s how it works –
Materials Used:
Rigid Plastic: The inner core of the toothbrush handle is typically made of a rigid and durable plastic material that provides structural integrity to the toothbrush.
Thermoplastic Elastomer (TPE): The outer layer of the toothbrush handle is made of a soft and grippy thermoplastic elastomer, often in a different color from the core plastic.
Overmolding Process:
Insert Molding: The rigid plastic core, including the head and neck of the toothbrush handle, is first molded separately using traditional injection molding.
Mold Preparation: The mold is then prepared for the overmolding process. The core plastic components are placed into the mold cavities, and the TPE material is preloaded into the over-molding machine.
Overmolding: The TPE material is injected into the mold, encapsulating the pre-molded rigid plastic core. The over-molding process ensures a secure bond between the two materials.
Benefits and Features:
Enhanced Grip: The soft TPE outer layer provides a comfortable and non-slip grip, making the toothbrush easier to hold, even when wet.
Aesthetics: Overmolding allows for the use of contrasting colors and textures, making the toothbrush visually appealing.
Durability: The over-molded TPE layer adds durability and impact resistance to the toothbrush handle.
Ergonomics: The over-molding process can create ergonomic contours and shapes that improve the user’s brushing experience.
This toothbrush example illustrates how over-molding can combine different materials to create a single, integrated product with improved functionality, aesthetics, and user comfort. It showcases the versatility and advantages of over-molding in the consumer products industry.
What is Overmolding in Manufacturing?
Overmolding in manufacturing is a specialized injection molding process that involves combining multiple materials or substrates to create a single, integrated component. This technique is used to enhance the functionality, aesthetics, durability, and ergonomics of the final product. Overmolding typically involves the following key aspects –
Multiple Materials: Overmolding combines two or more materials, each with distinct properties, into a single part. Common material combinations include a rigid substrate (often made of plastic, metal, or another material) and a soft, elastomeric material like thermoplastic elastomer (TPE) or rubber.
Mold Design: The mold used in over-molding is designed to accommodate multiple materials. It includes cavities for the primary substrate (usually referred to as the “core” or “insert”) and additional cavities for the secondary material (the “overmold” or “skin”).
Injection Process: Overmolding is typically achieved through injection molding, a process where molten material is injected into the mold cavities under pressure. The core material is molded first, and then the overmold material is injected to encapsulate or bond with the core material.
Material Compatibility: Ensuring that the selected materials are compatible and will adhere to each other is crucial. Proper material selection and preparation are essential for achieving a strong bond between the layers.
Bonding: The success of overmolding relies on achieving a secure and durable bond between the core and overmold materials. The injection process, mold design, and material selection are all factors that contribute to this bonding.
Benefits: Overmolding offers various benefits, including enhanced functionality (e.g., better grip, cushioning, or sealing), improved aesthetics (e.g., color contrast and texture), increased durability, and ergonomic design.
Applications: Overmolding is widely used in various industries, including consumer electronics, automotive, medical devices, tooling and equipment, consumer products, aerospace, and more. It is employed to create a wide range of products, from toothbrush handles to automotive interior components.
What is the difference between Overmolding and Injection Molding?
Overmolding and injection molding are both plastic manufacturing processes, but they differ in terms of technique, materials, and the final products they produce. Here are the key differences between over-molding and injection molding:
1. Technique:
Injection Molding: Injection molding is a standard plastic manufacturing process where molten plastic material is injected into a mold cavity. The mold is typically composed of two halves (a core and a cavity) that are clamped together during the molding process. After injection, the plastic material cools and solidifies to form the final part.
Overmolding: Overmolding is a specialized form of injection molding that involves molding multiple materials or substrates together to create a single, integrated component. It often includes an initial injection of one material (the core) and a subsequent injection of another material (the overmold) to encapsulate or bond with the core.
2. Materials:
Injection Molding: Injection molding typically uses a single type of material, which can be a wide range of thermoplastics or thermosetting plastics. The material is chosen based on the specific requirements of the part being produced.
Overmolding: Overmolding involves the use of two or more different materials with distinct properties. It combines a rigid substrate (core) with a softer, elastomeric material (overmold) to create a multi-material component. This allows for enhanced functionality, aesthetics, and other benefits.
3. Purpose:
Injection Molding: Injection molding is used to produce standalone plastic parts or components. It is suitable for applications where a single material with specific characteristics is sufficient.
Overmolding: Overmolding is employed to create integrated parts that benefit from the combination of different materials. It is used to enhance functionality, aesthetics, durability, or ergonomic features by applying the overmold material onto the core material.
4. Applications:
Injection Molding: Injection molding is widely used across various industries to produce a broad range of plastic parts, such as housings, connectors, and components for consumer products, automotive, electronics, and more.
Overmolding: Overmolding finds applications in industries where multi-material parts are beneficial. Common examples include toothbrush handles (with soft grips), automotive interior components (with soft-touch surfaces), and medical devices (with biocompatible and ergonomic features).
5. Complexity:
Injection Molding: Injection molding can be used for both simple and complex parts. It is well-suited for high-volume production and can create intricate geometries.
Overmolding: Overmolding is often associated with more complex parts due to the combination of materials and the need for precise bonding between them. It is commonly used for parts that require added functionality or improved aesthetics.
What are the Injection Overmolding Techniques?
Injection over-molding, also known as over-molding, is a specialized plastic molding technique that combines two or more different materials to create a single, integrated component. This technique enhances the functionality, aesthetics, and overall performance of the final product. There are several injection over-molding techniques commonly used in manufacturing:
Two-Shot Overmolding:
In two-shot over-molding, also known as 2K molding, two different materials are injected sequentially into the same mold cavity.
The first material, often a rigid substrate or core, is injected during the initial molding cycle.
After the core material has partially cooled and solidified, the mold is partially opened to allow for the injection of the second material (the overmold) around or onto the core.
This technique results in a part with two distinct materials that are securely bonded.
Insert Molding:
Insert molding is a variation of overmolding where a pre-manufactured component, known as an insert, is placed into the mold cavity before the injection of the overmold material.
The overmold material is injected, enveloping and bonding with the insert.
Insert molding is commonly used for applications like electrical connectors, where metal pins or components are overmolded with plastic for insulation, strain relief, and enhanced functionality.
Multi-Material Injection Molding:
Multi-material injection molding involves advanced machinery and molds that can inject multiple materials simultaneously or sequentially to create complex multi-material parts.
This technique allows for precise material placement within the mold, enabling the creation of intricate designs and features.
Hard-Soft Overmolding:
Hard-soft over-molding combines a rigid material, typically hard plastic, with a soft, elastomeric material like rubber or thermoplastic elastomer (TPE).
This technique is used to create parts with both rigid and flexible sections, such as tool grips, handles, and medical devices, where comfort, grip, and durability are crucial.
Multi-Shot Overmolding:
Multi-shot over-molding takes over-molding to the next level by allowing for the injection of more than two materials in separate shots.
It enables the creation of parts with multiple layers or sections of different materials.
Multi-shot over-molding is used in applications where precise material placement and layering are essential, such as automotive interiors and advanced consumer products.
Sequential Overmolding:
In sequential over-molding, two or more materials are injected in a specific order to achieve desired properties.
For example, a hard material may be injected first, followed by a soft material to create a rigid base with a cushioned surface.