Introduction
Injection molding is a process that is widely used manufacturing process for making plastic parts. Manufacturers employ various techniques to ensure the quality and reliability of the molded components, one of which is the Failure Mode and Effects Analysis (FMEA) process. In this article, we will delve into the world of Injection Mold FMEA, breaking down the process in easy-to-understand language.
What is Injection Mold FMEA?
FMEA stands for Failure Mode and Effects Analysis. It is a systematic approach to identifying and prioritizing potential failure modes in a process and evaluating their impact on the final product. When applied to injection molding, FMEA helps manufacturers anticipate and mitigate risks associated with the production of plastic parts.
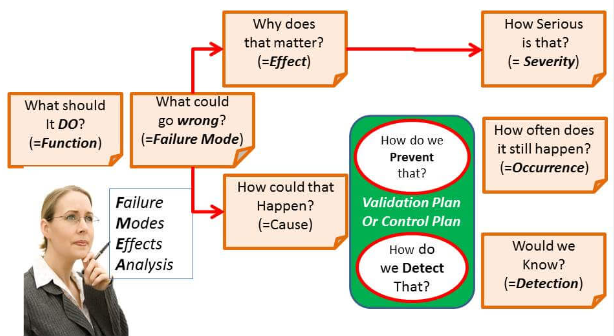
The Injection Mold FMEA process involves the following key steps –
- Team Formation:
- Assemble a cross-functional team that includes members from different departments, such as design, manufacturing, quality control, and maintenance.
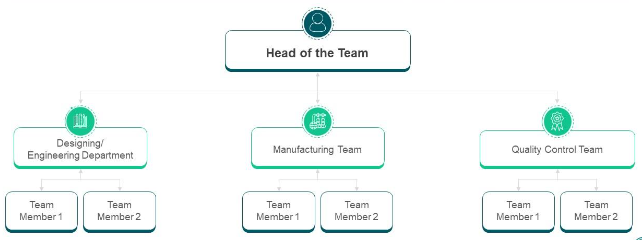
- Process Mapping:
- Create a detailed map of the injection molding process, identifying each step from material preparation to final part inspection.
- Identifying Failure Modes:
- Brainstorm and list all potential failure modes that could occur at each step of the injection molding process. Failure modes are any defects or issues that could affect the quality of the final product.
- Determining Causes and Effects:
- For each identified failure mode, determine its potential causes and effects on the final product. This step helps in understanding the root causes of potential issues.
- Assigning Severity, Occurrence, and Detection Ratings:
- Each failure mode is assigned a Severity, Occurrence, and Detection rating on a scale from 1 to 10. Severity reflects the impact of the failure on the end product, Occurrence represents the likelihood of the failure happening, and Detection assesses the likelihood of detecting the failure before it reaches the customer.
- Calculating Risk Priority Number (RPN):
- This technique, commonly used in the automotive industry, bases the risk priority number for an item failure mode on three factors.
- The RPN is calculated by multiplying the Severity, Occurrence, and Detection ratings. This number helps prioritize which failure modes should be addressed first.

- Prioritizing and Implementing Actions:
- Based on the RPN, prioritize the identified failure modes and develop action plans to mitigate or eliminate the risks. This may involve process changes, improved quality controls, or other preventive measures.
- Monitoring and Continuous Improvement:
- Regularly review and update the Injection Mould FMEA as the production process evolves. Continuous monitoring allows for the identification of new risks and the improvement of existing preventive measures.
Benefits of Injection Mold FMEA
Some Benefits of Injection Mould FMEA are –
- Risk Reduction:
- Identifying potential failure modes in advance allows manufacturers to implement measures to reduce or eliminate these risks, leading to improved product quality.
- Cost Savings:
- Addressing issues early in the design or manufacturing process can prevent costly recalls or rework, ultimately saving time and resources.
- Customer Satisfaction:
- By proactively addressing potential defects, manufacturers can ensure that the final product meets or exceeds customer expectations, enhancing overall satisfaction.
Pros & Cons of FMEA
Pros of the FMEA Process
- Risk Identification: FMEA systematically identifies potential failure modes in a process, helping organizations foresee and understand risks before they impact the final product.
- Proactive Problem Solving: By determining the causes and effects of potential issues, FMEA allows teams to proactively address problems, preventing them from occurring or minimizing their impact.
- Improved Product Quality: FMEA contributes to enhanced product quality by identifying and mitigating potential defects early in the design or manufacturing process.
- Cost Savings: Early identification and resolution of issues through FMEA can lead to significant cost savings by preventing expensive recalls, rework, or customer dissatisfaction.
- Customer Satisfaction: Implementing FMEA results in more reliable and consistent products, ultimately leading to increased customer satisfaction and loyalty.
- Structured Approach to Continuous Improvement: FMEA is an ongoing process that promotes a structured approach to continuous improvement, ensuring that organizations evolve and adapt to changing circumstances.
- Cross-Functional Collaboration: FMEA requires a cross-functional team, fostering collaboration and communication among different departments and stakeholders within an organization.
- Regulatory Compliance: In industries with stringent regulatory requirements, FMEA can assist organizations in meeting compliance standards by addressing potential risks and ensuring product reliability.
Cons of the FMEA Process
- Time-Consuming: FMEA can be time-consuming, especially when conducted in detail. The thorough examination of each potential failure mode requires significant effort and resources.
- Subjectivity: The assignment of severity, occurrence, and detection ratings involves a level of subjectivity. Different team members may perceive risks differently, leading to variations in the assessment.
- Overemphasis on High-Risk Items: The prioritization based on the Risk Priority Number (RPN) may lead to an overemphasis on high-risk items, potentially neglecting lower-risk but still significant issues.
- Limited Predictive Accuracy: FMEA relies on past experiences and assumptions, and it may not accurately predict all potential failure modes or their effects.
- Lack of Real-Time Application: FMEA is often conducted at specific stages of product or process development, and its effectiveness may diminish if not applied in real-time to adapt to changing conditions.
- Complexity: The complexity of FMEA can be a barrier, especially for smaller organizations with limited resources. Implementing and managing the FMEA process may require additional training and expertise.
- Limited Scope: FMEA may not capture every possible risk, especially those arising from external factors or unforeseen circumstances.
- Difficulty in Quantifying Ratings: Assigning numerical values to severity, occurrence, and detection may be challenging, as it involves converting qualitative judgments into quantitative measures.
Conclusion
Injection Mold FMEA is a powerful tool for manufacturers to enhance the quality and reliability of plastic parts produced through injection molding. By systematically identifying, assessing, and addressing potential failure modes, companies can minimize risks, reduce costs, and ultimately deliver high-quality products to their customers.
FAQ
What does FMEA stand for?
It stands for Failure Mode and Effects Analysis.
What is the purpose of FMEA?
The primary purpose of FMEA is to systematically identify and prioritize potential failure modes in a process, assessing their impact and proactively implementing measures to prevent or mitigate these failures.
How does FMEA contribute to quality improvement?
FMEA contributes to quality improvement by helping organizations anticipate and address potential issues in a process before they impact the final product. It allows for the identification of risks, their root causes, and the implementation of preventive actions to enhance overall product quality.
What industries commonly use FMEA?
FMEA is widely used across various industries, including manufacturing, automotive, aerospace, healthcare, and electronics. It is applicable in any sector where process reliability and product quality are critical.
How are severity, occurrence, and detection ratings determined in FMEA?
Severity, occurrence, and detection ratings are determined on a scale from 1 to 10, with 1 being the least severe, least likely to occur, or easiest to detect, and 10 being the most severe, most likely to occur, or most difficult to detect.
What is the Risk Priority Number (RPN) in FMEA?
The Risk Priority Number (RPN) is a calculated value obtained by multiplying the severity, occurrence, and detection ratings assigned to each failure mode. It helps prioritize which failure modes should be addressed first based on their potential impact.
Is FMEA a one-time process or an ongoing activity?
FMEA is typically an ongoing activity. It is not a one-time event but rather a continuous improvement tool. Regular reviews and updates ensure that new risks are identified, and existing preventive measures are enhanced.
What are the benefits of implementing FMEA in an organization?
The benefits of implementing FMEA include risk reduction, cost savings through early issue identification, improved product quality, enhanced customer satisfaction, and a structured approach to continuous improvement in processes.
This webpage is phenomenal. The brilliant data reveals the proprietor’s interest. I’m awestruck and expect further such astonishing entries.
Ive read several just right stuff here Certainly price bookmarking for revisiting I wonder how a lot effort you place to create this kind of great informative website.
Hi i think that i saw you visited my web site thus i came to Return the favore Im attempting to find things to enhance my siteI suppose its ok to use a few of your ideas.
I truly appreciated the work you’ve put forth here. The sketch is tasteful, your authored material stylish, yet you appear to have developed some nervousness regarding what you intend to deliver next. Rest assured, I’ll return more regularly, much like I’ve done almost constantly, should you maintain this upward trajectory.
This website has quickly become my go-to source for [topic]. The content is consistently top-notch, covering diverse angles with clarity and expertise. I’m constantly recommending it to colleagues and friends. Keep inspiring us!
Hello my loved one! I want to say that this post is awesome, nice written and come with almost all important infos. I?¦d like to look extra posts like this .
Thank you for the auspicious writeup It in fact was a amusement account it Look advanced to far added agreeable from you However how can we communicate
I saw a lot of website but I think this one has got something special in it in it
hope you will visit again
Your blog is a true hidden gem on the internet. Your thoughtful analysis and in-depth commentary set you apart from the crowd. Keep up the excellent work!
thanks
thanks for such kind words, it motivate me write more and more
Simply wish to say your article is as amazing The clearness in your post is just nice and i could assume youre an expert on this subject Well with your permission let me to grab your feed to keep updated with forthcoming post Thanks a million and please carry on the gratifying work
Thanks