What are Molding Defects?

Molding defects refer to undesirable irregularities, flaws, or imperfections that occur during the process of molding materials, such as plastics, metals, ceramics, or composites. The molding process involves shaping molten material by injecting, pressing, or pouring it into a mold or cavity, which then solidifies to take on a specific shape. However, various factors can lead to deviations from the desired quality, functionality, and appearance of the final molded product, resulting in defects.
These defects can manifest as physical, visual, or structural anomalies in the finished part. They can be caused by a combination of material properties, mold design, processing conditions, equipment settings, and external factors. Molding defects can compromise the mechanical strength, dimensional accuracy, surface finish, and overall integrity of the product, leading to potential performance issues or the need for costly rework.
50 Types Molding Defects: Their Causes & Troubleshooting
Certainly, here are 50 molding defects, along with their potential causes and troubleshooting steps –
Molding Defects Warping
- Cause: Non-uniform cooling rates causing differential shrinkage.
- Troubleshooting: Optimize the cooling system, control mold temperature, and ensure proper ejection.

Molding Defects Sink Marks
- Cause: Uneven cooling causing depressions in thicker sections.
- Troubleshooting: Adjust gate size and location, control mold temperature, and optimize packing pressure.

Molding Defects Flash
- Cause: Excessive clamping force, mold misalignment, or inadequate venting.
- Troubleshooting: Increase mold clamping force, align mold halves, improve venting, and reduce injection pressure.

Molding Defects Short Shots
- Cause: Insufficient material to fill the mold cavity.
- Troubleshooting: Increase melt temperature, injection pressure, and injection time; check for material blockages.

Air Traps
- Cause: Poor venting, high material viscosity, or air entrapment.
- Troubleshooting: Optimize mold venting, increase melt temperature, and adjust injection speed.
Molding Defects Burn Marks
- Cause: High melt temperature or extended residence time.
- Troubleshooting: Lower melt temperature, reduce residence time and ensure proper venting.
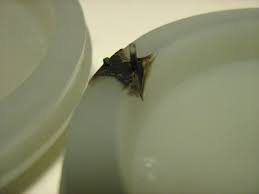
Molding Defects Jetting
- Cause: High injection speed causes the material to shoot or jet.
- Troubleshooting: Lower injection speed, optimize gate design and adjust melt temperature.

Molding Defects Voids
- Cause: Insufficient material flow or inadequate venting.
- Troubleshooting: Optimize gate design, improve mold venting, and adjust melt temperature.

Molding Defects Knit Lines
- Cause: Melt fronts meeting and forming visible seams.
- Troubleshooting: Optimize gate location, increase melt temperature, and adjust injection speed.
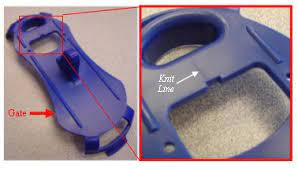
Molding Defects Cracking
- Cause: Thermal stress, poor material properties, or inadequate cooling.
- Troubleshooting: Optimize cooling rates, adjust mold temperature, and select materials with better properties.
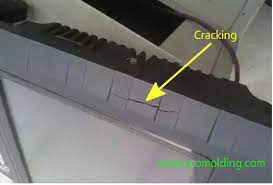
Molding Defects Splay
- Cause: Moisture or volatile gases in the material.
- Troubleshooting: Dry the material thoroughly, ensure proper material handling, and reduce melt temperature.
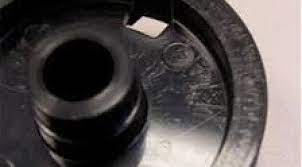
Molding Defects Flow Marks
- Cause: Disruptions in material flow during filling.
- Troubleshooting: Optimize gate design, increase melt temperature, and adjust injection speed.
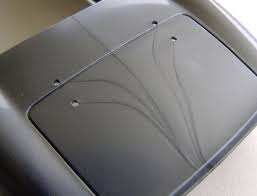
Molding Defects Blisters
- Cause: Trapped air or moisture forming bubbles.
- Troubleshooting: Dry the material properly, improve mold venting, and adjust melt temperature.
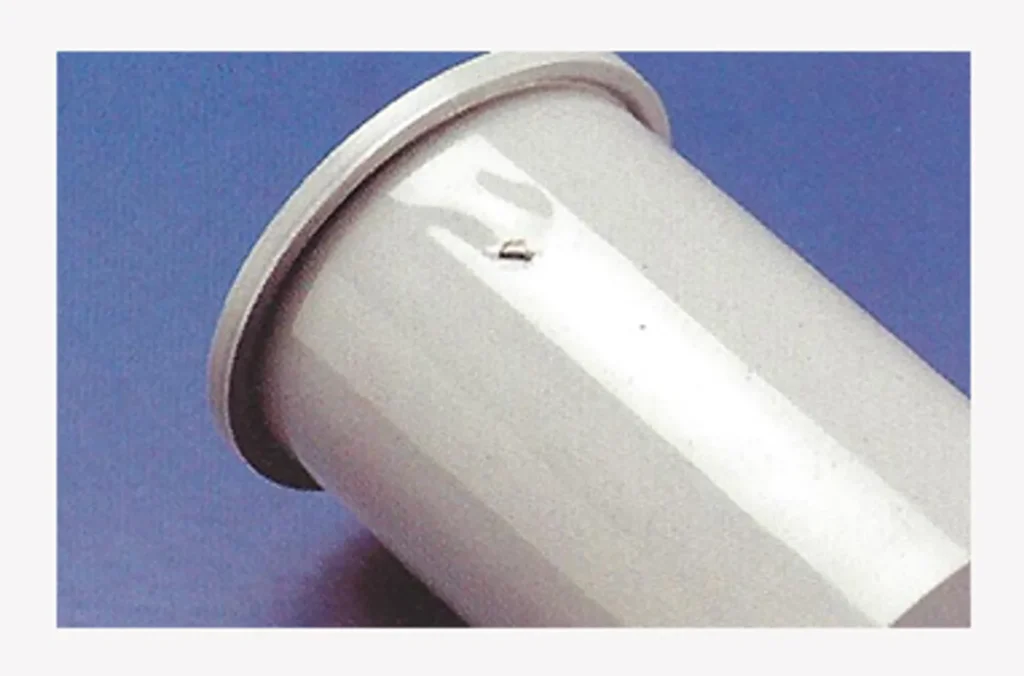
Molding Defects Hesitation Marks
- Cause: Brief interruptions in material flow during injection.
- Troubleshooting: Optimize gate design, ensure sufficient injection pressure, and improve material flow properties.
Molding Defects Sticking
- Cause: Part adhering to mold surface during ejection.
- Troubleshooting: Use mold release agents, adjust mold temperature, and optimize the ejection system.
Molding Defects Crystallization
- Cause: Rapid cooling leads to improper polymer crystalline structure.
- Troubleshooting: Adjust mold temperature, increase cooling time, and optimize melt temperature.
Molding Defects Crazing
- Cause: Incompatibility between material and mold release agents.
- Troubleshooting: Change mold release agents, ensure compatibility, and adjust ejection temperature.
Molding Defects Degradation
- Cause: Overheating of material during processing.
- Troubleshooting: Lower melt temperature, minimize residence time and improve material selection.
Mold Corrosion
- Cause: Chemical reactions between material and mold surfaces.
- Troubleshooting: Select corrosion-resistant mold materials, use mold coatings, and monitor processing conditions.
Mold Fouling
- Cause: Residue buildup on mold surfaces.
- Troubleshooting: Clean molds regularly, optimize material formulation, and use effective mold release agents.
Molding Defects Delamination
- Cause: Poor bonding between layers in multi-material parts.
- Troubleshooting: Ensure material compatibility, optimize processing conditions, and adjust mold design.
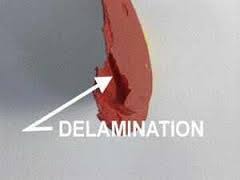
Mold Pitting
- Cause: Physical or chemical erosion of mold surfaces.
- Troubleshooting: Use wear-resistant mold materials, maintain proper cooling, and apply protective coatings.
Molding Defects Jet Flow
- Cause: High-speed material flow causing surface defects.
- Troubleshooting: Reduce injection speed, adjust gate design, and optimize material viscosity.
Molding Defects Black Specks
- Cause: Contaminants or degraded material in the melt.
- Troubleshooting: Ensure material cleanliness, clean processing equipment, and use effective filtration systems.
Molding Defects Stringing
- Cause: Excessive material remaining attached after ejection.
- Troubleshooting: Optimize melt temperature, injection speed, and mold release mechanisms.
Molding Defects Gloss Variation
- Cause: Inconsistent cooling or mold surface issues.
- Troubleshooting: Optimize mold temperature, cooling channels, and apply mold surface treatments.
Molding Defects Undercuts
- Cause: Features preventing easy part ejection from the mold.
- Troubleshooting: Redesign part geometry to eliminate undercuts or use sliding cores.
Molding Defects Ejector Marks
- Cause: Marks on the part due to ejection pins.
- Troubleshooting: Adjust ejection mechanisms, use smoother ejector pins, and optimize part ejection parameters.

Molding Defects Excessive Shrinkage
- Cause: Material composition or cooling issues causing high shrinkage.
- Troubleshooting: Adjust material formulation, optimize cooling rates, and control mold temperature.
Molding Defects Dimensional Inaccuracy
- Cause: Improper mold design or processing parameters.
- Troubleshooting: Ensure accurate mold design, optimize processing conditions, and control material properties.
Molding Defects Melt Fracture
- Cause: High shear rates causing material fracture.
- Troubleshooting: Lower injection speed, adjust gate design, and optimize material viscosity.
Molding Defects Jet Flow Lines
- Cause: High-speed material flow causing visible flow lines.
- Troubleshooting: Reduce injection speed, optimize gate design, and adjust melt temperature.
Parting Line Mismatch
- Cause: Misalignment of mold halves at the parting line.
- Troubleshooting: Ensure proper mold alignment, use shimming if necessary, and adjust clamping force.
Molding Defects Distortion
- Cause: Uneven cooling or internal stresses.
- Troubleshooting: Optimize cooling system, control mold temperature, and use proper ejection mechanisms.
Molding Defects Gas Burn Marks
- Cause: Gas trapped in the mold burning during injection.
- Troubleshooting: Improve mold venting, reduce injection speed, and ensure uniform melt flow.
Molding Defects Jet Flow
- Cause: Material velocity variations causing uneven surface finish.
- Troubleshooting: Optimize gate design, reduce injection speed, and adjust melt temperature.
Core Shift
- Cause: Movement of cores within the mold during injection.
- Troubleshooting: Improve core support, optimize molding parameters, and ensure proper clamping.
Mold Warpage
- Cause: Uneven mold cooling or inadequate support.
- Troubleshooting: Optimize cooling channels, control mold temperature, and use proper mold supports.
Mold Sticking
- Cause: Part adhering to the mold cavity.
- Troubleshooting: Use mold release agents, control mold temperature, and adjust ejection mechanisms.
Molding Defects Flow Imbalance
- Cause: Non-uniform material distribution in the mold cavity.
- Troubleshooting: Optimize gate design, adjust melt temperature, and ensure uniform injection pressure.
Molding Defects Vacuum Voids
- Cause: Vacuum forming within the mold cavity.
- Troubleshooting: Optimize venting, adjust injection speed, and reduce melt temperature.
Molding Defects Flow Restriction
- Cause: Constricted flow paths causing uneven material flow.
- Troubleshooting: Optimize gate design, increase gate size, and ensure uniform wall thickness.
Mold Erosion
- Cause: Abrasion or corrosion of mold surfaces.
- Troubleshooting: Use wear-resistant mold materials, optimize processing conditions, and apply protective coatings.
Molding Defects Cold Slugs
- Cause: Unmelted material entering the mold cavity.
- Troubleshooting: Increase melt temperature, optimize nozzle design, and ensure proper purging.
Molding Defects Contaminant Marks
- Cause: Foreign particles or contaminants in the melt.
- Troubleshooting: Use clean materials, implement proper material handling, and improve filtration.
Molding Defects Flow Lines
- Cause: Material flow disruptions causing visible lines.
- Troubleshooting: Optimize gate design, reduce injection speed, and adjust melt temperature.
Degassing Marks
- Cause: Gas escaping from the melt during injection.
- Troubleshooting: Optimize material drying, reduce melt temperature, and ensure proper venting.
Fiber Breakage
- Cause: Breakage of reinforcing fibers in composite materials.
- Troubleshooting: Optimize material formulation, ensure proper fiber orientation, and adjust processing parameters.
Excessive Flash
- Cause: Excessive material escaping from the mold cavity.
- Troubleshooting: Increase clamping force, optimize venting, and adjust injection pressure.
Gate Blush
- Cause: Material cooling prematurely at the gate.
- Troubleshooting: Optimize gate design, control mold temperature, and adjust injection parameters.
Addressing these molding defects requires a deep understanding of the underlying causes and a systematic approach to troubleshooting. Regular monitoring, process optimization, and collaboration between material scientists, mold designers, and processing engineers can help prevent or mitigate these defects effectively.
Conclusion
To sum up, molding defects can undermine the integrity and aesthetics of molded products. Their origins lie in intricate factors like material properties, mold design, and processing conditions. By diagnosing these causes accurately, manufacturers can implement targeted solutions such as adjusting temperatures, optimizing injection parameters, and enhancing mold design. This proactive approach, combined with regular monitoring and collaboration among experts, can effectively counter molding defects. Ultimately, this leads to improved product quality, reduced waste, and enhanced customer satisfaction.
FAQ’s
How can mold material defects be prevented?
Preventing mold material defects involves several key strategies –
Material Selection: Choose mold materials that match the intended production environment and the materials being molded. Consider factors such as temperature, pressure, chemical compatibility, and wear resistance.
Material Inspection: Thoroughly inspect mold materials for any defects or imperfections before use. This includes checking for cracks, voids, inclusions, or inconsistencies in the material’s composition.
Proper Heat Treatment: Ensure that the chosen mold material undergoes the appropriate heat treatment processes to achieve the desired hardness and structural integrity.
Quality Supplier: Source mold materials from reputable suppliers known for providing high-quality materials. This reduces the risk of using subpar or counterfeit materials.
Material Handling: Handle mold materials with care to prevent physical damage or contamination. Store them in controlled environments to avoid exposure to moisture, corrosive substances, or extreme temperatures.
Regular Maintenance: Implement a maintenance schedule to inspect and maintain molds over time. This includes cleaning, repairing, and, if necessary, reworking the mold surfaces.
Coatings and Treatments: Apply appropriate coatings or surface treatments to enhance the mold’s wear resistance, reduce friction, and improve its release properties.
Monitoring and Analysis: Regularly monitor the performance of molds during production. Analyze the molds for signs of wear, corrosion, or any emerging defects.
Corrective Action: If defects or wear are detected, take immediate corrective actions such as repairing, reconditioning, or replacing affected mold components.
Collaboration: Foster collaboration between mold designers, material suppliers, and processing engineers to ensure the chosen mold materials align with the intended manufacturing process and product requirements.
By following these preventive measures, manufacturers can significantly reduce the risk of mold material defects, resulting in improved product quality, extended mold life, and smoother production processes.
What are remedies for Compression Molding Defects?
Remedies for compression molding defects involve addressing specific issues to improve the quality and consistency of molded products –
Flash:
Optimize mold design for better parting line alignment.
Adjust clamp pressure to ensure proper mold closure.
Use proper mold release agents to prevent sticking.
Air Traps:
Enhance mold venting to allow trapped air to escape.
Adjust material temperature and injection speed for better flow.
Incomplete Fill:
Increase material temperature to ensure complete flow.
Optimize mold design to facilitate material distribution.
Warping:
Control mold temperature to ensure uniform cooling.
Optimize cooling system design for balanced cooling rates.
Cure Variations:
Monitor and adjust cure time and temperature for consistent results.
Use proper material mixing and preparation techniques.
Surface Defects:
Maintain cleanliness of mold surfaces and cavity.
Implement proper mold release agents and coatings.
Dimensional Inaccuracies:
Optimize material loading and distribution to avoid variations.
Use precision molds and calibrated equipment.
Blisters:
Adjust mold venting to prevent air entrapment.
Optimize material moisture content and processing conditions.
Void Formation:
Enhance material flow by adjusting temperature and pressure.
Use mold design that minimizes material trapping.
Brittleness:
Adjust cure time and temperature to optimize material properties.
Evaluate material formulation for improved flexibility.
Surface Finish Issues:
Implement proper mold polishing or texturing.
Use mold release agents and coatings for smoother finishes.
Delamination:
Ensure proper material compatibility in multi-layer molds.
Optimize bonding processes and mold design.
By addressing these remedies, manufacturers can mitigate compression molding defects and achieve consistent, high-quality molded products. Each remedy should be tailored to the specific defect and its underlying cause. Regular process monitoring and adjustments are key to successful defect prevention in compression molding.
How can you you improve the quality of injection molding?
Certainly, here are key points outlining how to improve the quality of injection molding –
Material Selection:
Choose materials with appropriate properties for the intended application.
Consider factors like flow characteristics, mechanical strength, and thermal stability.
Mold Design:
Design molds with proper gating, venting, and cooling systems.
Optimize part geometry for uniform filling and minimal stress concentration.
Mold Maintenance:
Regularly clean and maintain molds to prevent wear and buildup.
Address any signs of damage or degradation promptly.
Process Optimization:
Fine-tune injection parameters for optimal material flow and part formation.
Adjust melt temperature, injection speed, and pressure for consistent results.
Uniform Cooling:
Ensure uniform mold cooling to prevent warping and reduce cycle times.
Optimize cooling channels and use temperature control systems.
Quality Control Checks:
Implement rigorous quality checks throughout the production process.
Inspect parts for defects, dimensions, and surface finish.
Real-time Monitoring:
Utilize monitoring systems to track process variables and detect deviations.
Make immediate adjustments to maintain consistent quality.
Operator Training:
Train operators in proper machine operation, mold handling, and troubleshooting.
Knowledgeable operators can address issues effectively and ensure smooth production.
Material Handling:
Store and handle materials properly to prevent contamination and degradation.
Ensure proper drying of hygroscopic materials before molding.
Documentation and Traceability:
Maintain detailed records of process parameters, materials used, and production conditions.
Establish traceability to quickly identify and rectify any quality issues.
Continuous Improvement:
Regularly analyze data and feedback to identify trends and areas for improvement.
Implement changes and innovations to enhance quality over time.
By focusing on these aspects, manufacturers can enhance the quality of their injection molding processes, leading to better product performance, reduced defects, and improved customer satisfaction.
Saved as a favorite, I really like your web site!
It’s a pity you don’t have a donate button! I’d without a doubt donate to this superb
blog! I guess for now i’ll settle for book-marking and
adding your RSS feed to my Google account. I look forward to fresh updates and will share this blog with my Facebook group.
Chat soon!
Thank you so much for your kind words and support — it truly means a lot! 😊
I’m honored that you find the blog valuable enough to consider donating. While there’s no donate button at the moment, your gesture of bookmarking, subscribing to the RSS feed, and sharing it with your Facebook group is more than appreciated.
Stay tuned for more updates — and feel free to reach out anytime at https://autoplasticsworld.com/about-us/