Introduction
In the realm of manufacturing, where precision and aesthetics meet functionality, mold polishing emerges as a critical process that bridges the gap between raw form and refined excellence. Mold polishing, often regarded as an art as much as a science, plays a pivotal role in enhancing the quality, appearance, and performance of molded products. This article delves into the intricate world of mold polishing, unveiling various techniques, their applications, and the impact they have on diverse industries.
What is Mold Polishing?
Mold polishing is a precision finishing process used in manufacturing to refine the surface of a mold cavity, typically made of metal, to achieve a desired level of smoothness, shine, and detail. This process enhances the aesthetics, functionality, and quality of molded products. By meticulously removing imperfections, roughness, and irregularities from the mold’s surface, mold polishing helps create visually appealing and high-performance final products.
It involves various techniques, from traditional hand polishing to advanced methods like mechanical, electrochemical, and diamond polishing, each tailored to specific materials and applications. Mold polishing is vital in industries such as plastics, die casting, glass, jewelry, and more, where the quality of the mold’s finish directly impacts the appearance and performance of the manufactured items.
The Importance of Mold Polishing
Mold polishing, at its core, is the process of refining the surface of a mold cavity to achieve a desired level of smoothness, shine, and precision. While the primary objective is to enhance aesthetics, this process extends beyond the superficial. The mirror-like finish achieved through mold polishing serves multiple purposes, including reducing friction, preventing part defects, and facilitating easier release of molded products. The art of mold polishing, therefore, is not merely about making a product visually appealing, but also about optimizing its overall functionality and performance.
Exploring Mold Polishing Techniques
Hand Polishing
A traditional approach to mold polishing involves skilled craftsmen using a combination of abrasives, polishing compounds, and meticulous handwork to achieve the desired surface finish. This technique requires expertise and an acute understanding of the material properties to ensure consistency and precision. While time-consuming, hand polishing allows for intricate detailing and customization, making it indispensable for applications demanding the utmost aesthetic and functional standards.
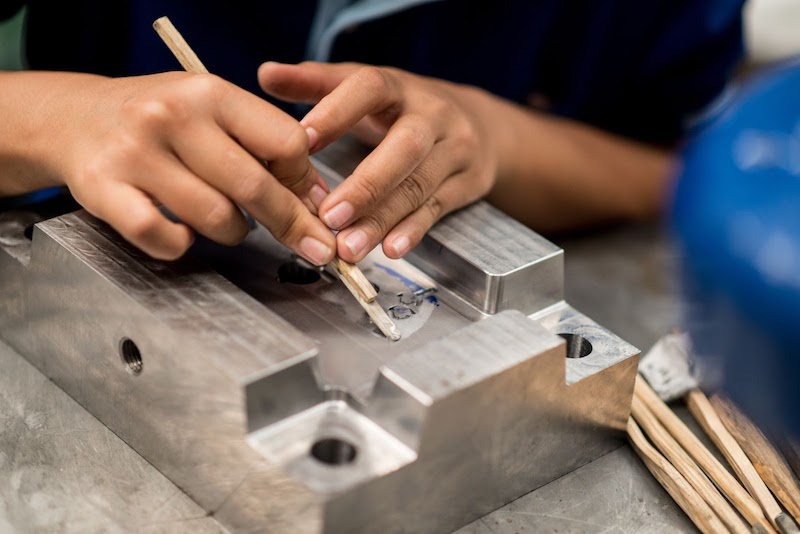
Mechanical Polishing
As technology advanced, mechanical polishing methods emerged, leveraging automated tools such as rotary polishers, micro-motor handpieces, and CNC-controlled systems. These tools expedite the process while maintaining a high degree of control and precision. Mechanical polishing is particularly advantageous for large-scale production and repetitive tasks, ensuring uniformity across multiple molds.
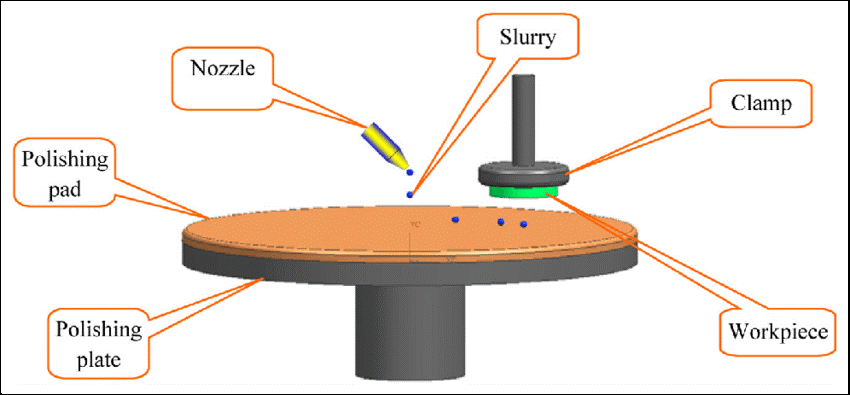
Electrolytic Mold Polishing
Electrolytic mold polishing is an advanced surface finishing technique used to achieve precise and controlled polishing of molds and other metallic surfaces through the application of controlled electrical currents. This method leverages the principles of electrochemistry to selectively remove material from the surface, resulting in improved surface smoothness, shine, and detail. Electrolytic mold polishing offers advantages such as enhanced control, efficiency, and the ability to achieve intricate geometries.
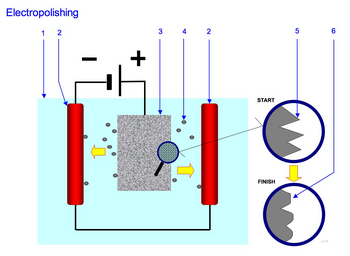
Here’s an overview of electrolytic mold polishing and its types –
Basic Electrolytic Mold Polishing Process
- Setup: The mold to be polished is immersed in an electrolyte solution, which is typically a mixture of water and specific chemicals. An electrode, often made of a conductive material like graphite, is also placed in the electrolyte.
- Electrical Current: When an electrical current is passed through the electrolyte solution, metal ions from the mold’s surface dissolve into the solution through a process called electrolysis. This selective dissolution targets high points and irregularities on the mold’s surface.
- Material Removal: As metal ions are dissolved from the mold’s surface, the surface becomes smoother and more refined. Material removal occurs predominantly on protruding areas, resulting in a leveling effect that improves overall surface uniformity.
- Control and Precision: The rate of material removal can be controlled by adjusting parameters such as current density, electrolyte composition, and processing time. This allows for precise tuning of the polishing process to achieve the desired surface finish.
Types of Electrolytic Mold Polishing
Cathodic Electrolytic Polishing (CEP)
In CEP, the mold to be polished is connected as the cathode (negative electrode), and the anode (positive electrode) is made of a sacrificial material that will dissolve in the electrolyte. As the electrical current flows, metal ions from the mold’s surface are drawn into the electrolyte, resulting in selective material removal and surface smoothing.
Anodic Electrolytic Polishing (AEP)
In AEP, the mold to be polished is connected to the anode, and the material for the cathode is chosen such that it will not dissolve. Metal ions from the anode’s surface are oxidized and dissolved into the electrolyte, leading to material removal and surface improvement.
Advantages of Electrolytic Mold Polishing
- Precision: Electrolytic polishing allows for precise control over material removal, making it suitable for achieving intricate surface features and complex geometries.
- Uniformity: The process promotes uniform material removal, resulting in a consistent surface finish across the mold’s entire surface.
- Efficiency: Electrolytic polishing can be faster and more efficient than traditional mechanical methods, especially for molds with complex shapes.
- Reduced Risk of Damage: Compared to aggressive mechanical polishing, electrolytic polishing is gentler on the mold’s surface, reducing the risk of introducing micro-cracks or other defects.
**Electrolytic mold polishing is widely used in industries such as precision engineering, electronics, and mold manufacturing, where high-quality molds with smooth and flawless surfaces are essential for producing superior end products. The ability to achieve controlled and precise material removal through electrochemical processes makes electrolytic mold polishing a valuable tool in the manufacturing toolbox.
Ultrasonic Mold Polishing
Ultrasonic mold polishing is an advanced surface finishing technique that utilizes ultrasonic vibrations to enhance the precision and effectiveness of the polishing process. This method involves immersing the mold or workpiece in a liquid solution (usually a mixture of water and specialized polishing compounds) and subjecting it to high-frequency ultrasonic vibrations. These vibrations create cavitation bubbles that collapse near the surface, generating localized pressure and mechanical agitation. This phenomenon aids in the removal of material and results in improved surface smoothness and quality.
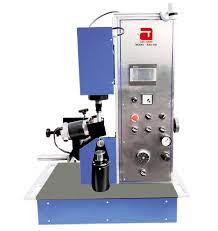
There are different types of ultrasonic mold polishing techniques, each with its unique approach to achieving desired surface finishes. Here are two common types –
Ultrasonic Vibration Polishing
In this method, the mold is submerged in a bath of liquid solution that contains abrasive particles. Ultrasonic vibrations are applied to the solution, causing cavitation bubbles to form and collapse near the mold’s surface. As the bubbles collapse, they create micro-jets of liquid and abrasive particles that impact the mold’s surface, facilitating controlled material removal. This technique is particularly effective for achieving fine finishes and polishing intricate details, as the ultrasonic energy can reach areas that might be difficult to access using traditional methods.
Ultrasonic Cavitation Peening
Ultrasonic cavitation peening is a variation of ultrasonic mold polishing that focuses on imparting compressive stress to the mold’s surface, enhancing its durability and resistance to wear and fatigue. In addition to abrasive particles, the liquid solution used in this process can contain specialized peening media. Ultrasonic vibrations induce cavitation, which results in controlled micro-hammering on the mold’s surface. This micro-hammering generates compressive stresses that improve the material’s mechanical properties and enhance its resistance to cracking and other forms of surface degradation.
Advantages of Ultrasonic Mold Polishing
- Precision: Ultrasonic vibrations provide precise control over material removal, allowing for targeted polishing and improved surface quality.
- Uniformity: The mechanical agitation generated by ultrasonic cavitation results in a more uniform distribution of abrasives across the mold’s surface.
- Accessibility: Ultrasonic energy can reach complex shapes and tight spaces that may be challenging to reach using traditional polishing methods.
- Enhanced Durability: Ultrasonic cavitation peening can improve the mechanical properties of the mold’s surface, increasing its resistance to wear and fatigue.
**Ultrasonic mold polishing is employed in various industries where precision, surface quality, and uniformity are critical, including electronics, medical device manufacturing, aerospace, and jewelry production. The ability to achieve consistent and controlled material removal using ultrasonic energy makes this technique a valuable tool for enhancing the performance and aesthetics of molded products and precision components.
Chemical Mold Polishing
Chemical mold polishing, also known as chemical mechanical polishing (CMP), is an advanced surface finishing technique used to achieve precise and controlled smoothing and polishing of molds and other materials. Unlike traditional mechanical methods that involve abrasives, chemical mold polishing relies on a combination of chemical reactions and mechanical action to achieve the desired surface finish. This technique is commonly employed in industries where extremely smooth and flawless surfaces are essential, such as semiconductor manufacturing, optics, and precision engineering.
Here’s a brief explanation of the chemical mold polishing process –
- Chemical Slurry: A chemical slurry is prepared by mixing abrasive particles, chemicals, and a carrier fluid. The abrasive particles can be nanoparticles or microparticles of various materials, such as silica, alumina, ceria, or diamond.
- Mechanical Action: The mold or substrate to be polished is placed in contact with a polishing pad or platen. The chemical slurry is dispensed onto the pad, and the mold is pressed against the pad with controlled pressure.
- Chemical Reactions: The abrasive particles in the slurry interact with the material’s surface, initiating a combination of chemical reactions and mechanical abrasion. The chemical reactions help dissolve or chemically alter the surface layer of the mold, while the mechanical action assists in material removal.
- Material Removal: As the mold is moved against the pad, the abrasive particles gently remove the surface material through a combination of mechanical abrasion and chemical dissolution. This process selectively targets high points, irregularities, and defects on the mold’s surface.
- Uniformity and Control: Chemical mold polishing offers excellent control over material removal rates and surface characteristics. The process can be fine-tuned to achieve specific levels of smoothness, flatness, and surface quality across the mold’s entire surface.
- Rinsing and Cleaning: After the polishing process, the mold is thoroughly rinsed and cleaned to remove any residual chemicals and abrasive particles, ensuring a clean and pristine surface finish.
**Chemical mold polishing has several advantages, including the ability to polish complex shapes, achieve nanoscale precision, and maintain a high degree of uniformity across large surfaces. It can also be used for materials that are difficult to polish using traditional mechanical methods. However, chemical mold polishing requires careful control of process parameters, such as slurry composition, pressure, and temperature, to achieve consistent and predictable results.
Diamond Polishing
Diamond abrasives, with their exceptional hardness, have become a cornerstone of mold polishing. Diamond polishing compounds, coupled with rotary tools or ultrasonic systems, facilitate efficient material removal and superior surface smoothness. This technique excels in producing high-gloss finishes, making it a preferred choice for applications where impeccable aesthetics are paramount.
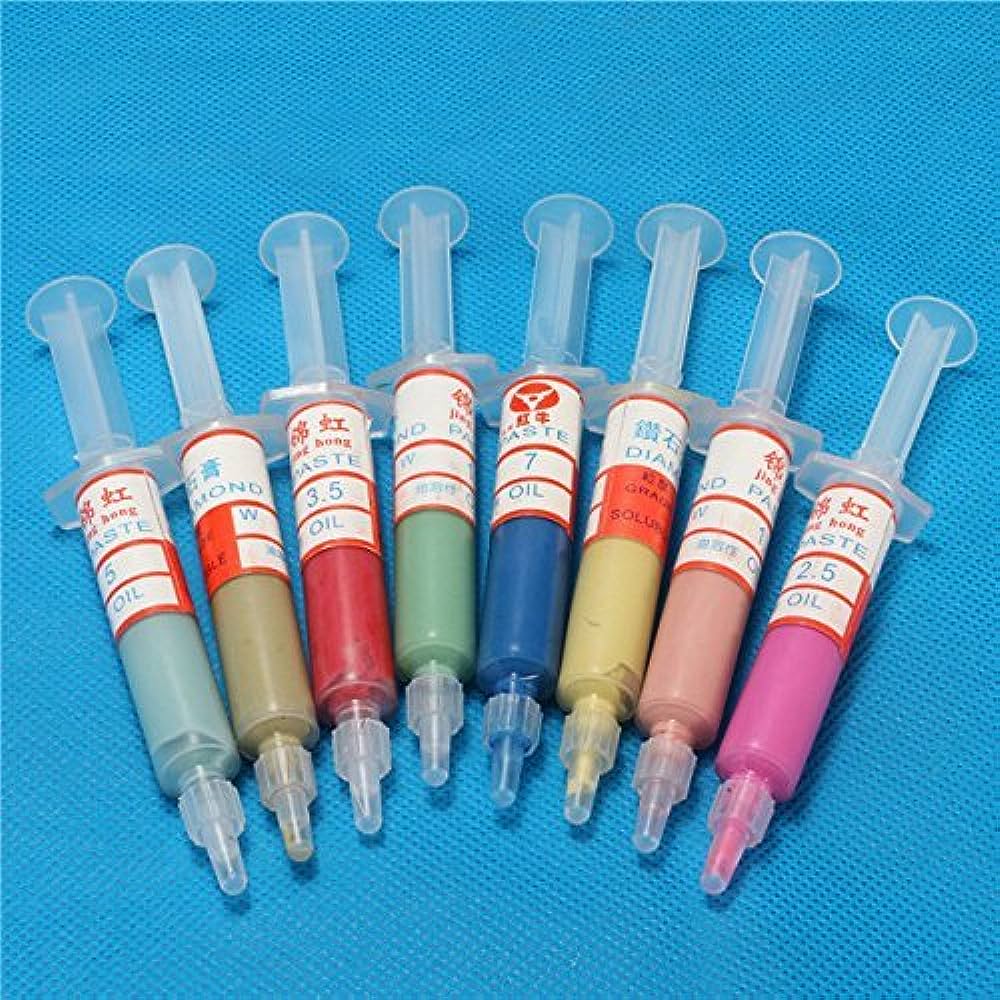
Fluidized Abrasive Polishing
Leveraging a suspension of fine abrasive particles in a liquid medium, fluidized abrasive polishing offers a gentle yet effective approach to mold polishing. The fluidized mixture flows evenly over the mold surface, minimizing the risk of localized scratches or inconsistencies. This technique is particularly suited for molds with intricate geometries, fragile materials, or those requiring minimal material removal.
Here are two common types of fluidized abrasive mold polishing techniques –
Slurry Polishing
In slurry polishing, a mixture of abrasive particles and a liquid carrier is used to create a slurry that is applied to the mold’s surface. The abrasive particles are typically suspended in a liquid solution, which can be water or a specialized polishing fluid. The slurry is often circulated or agitated to maintain an even distribution of abrasive particles. The mold to be polished is then placed in contact with a polishing pad or platen.
As the slurry is applied to the pad, the mold is pressed against it, and the combination of abrasive particles and controlled mechanical action results in material removal and surface smoothing. Slurry polishing is particularly effective for achieving fine finishes and maintaining surface integrity on delicate or complex molds.
Abrasive Flow Machining (AFM)
Abrasive Flow Machining is a specialized variant of fluidized abrasive polishing. In AFM, a highly viscous abrasive media, often consisting of polymer-bonded abrasive particles, is forced through the mold’s internal passages and cavities under pressure. This flow of abrasive media exerts a controlled and uniform polishing action on the mold’s intricate features, resulting in improved surface quality.
The viscosity of the abrasive media in AFM allows for precise control over material removal and surface finish. AFM is particularly useful for molds with complex internal geometries, such as those used in die casting or plastic injection molding. It can reach recessed areas that might be challenging to access using traditional polishing methods.
Advantages of Fluidized Abrasive Mold Polishing
- Gentle Material Removal: Fluidized abrasive polishing is less aggressive than some other polishing methods, reducing the risk of surface damage or alteration.
- Consistent Finish: The suspension of abrasive particles in a liquid carrier helps maintain a consistent distribution of abrasives across the mold’s surface, resulting in uniform polishing.
- Intricate Geometries: Fluidized abrasive polishing is well-suited for molds with complex shapes, internal passages, and fine details.
- Delicate Materials: This method is suitable for polishing delicate materials that may be susceptible to damage from more aggressive polishing techniques.
**Fluidized abrasive mold polishing techniques offer a valuable approach for achieving high-quality surface finishes on molds used in various industries, including aerospace, automotive, medical devices, and consumer products. The ability to achieve precision and uniformity while preserving intricate details makes fluidized abrasive polishing a valuable tool for enhancing the performance and appearance of molded products.
Applications Across Industries
Plastic Injection Molding
In the plastic injection molding industry, mold polishing is a cornerstone of achieving flawless, glossy surfaces for consumer products, automotive components, and medical devices. The precision of mold polishing directly influences the appearance and tactile experience of the final product, often dictating consumer perception and market competitiveness.
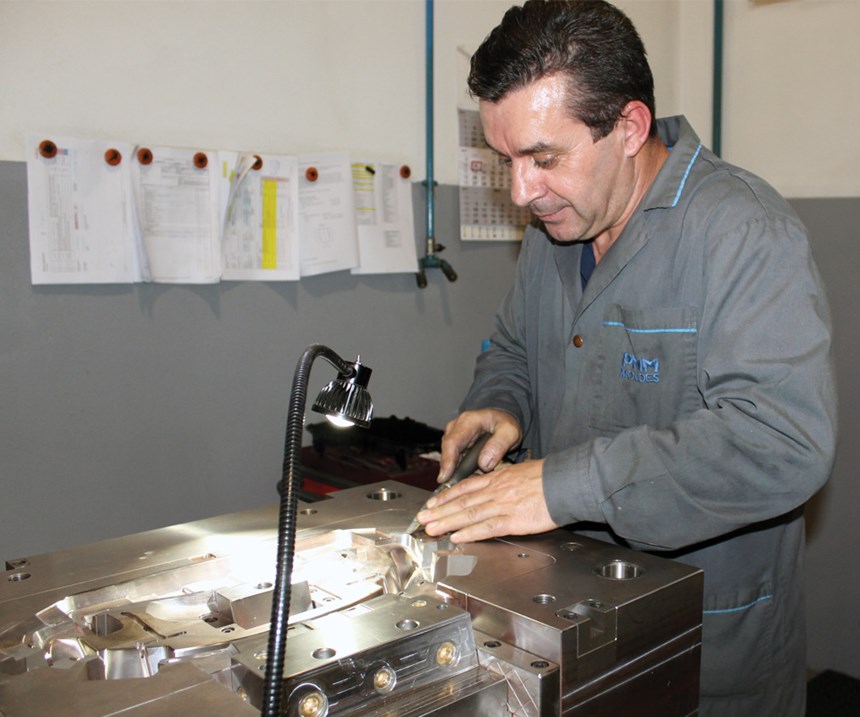
Die Casting
In die casting, mold surfaces need to withstand high temperatures and pressures. Mold polishing not only enhances the visual appeal of die-cast products but also minimizes defects and facilitates smoother ejection. Polished molds reduce the likelihood of porosity, flash, and other imperfections that can compromise the integrity of the final product.
Glass and Ceramic Molding
Mold polishing is equally relevant in the production of glass and ceramic components, where surface quality is crucial for optical clarity, light transmission, and texture. Molds for glass lenses, decorative glassware, and intricate ceramic pieces benefit from meticulous polishing to achieve desired visual and functional characteristics.
Jewelry and Precision Components
Mold polishing plays a pivotal role in the jewelry industry, ensuring that intricate designs and precious metals are presented in their finest form. Moreover, precision components used in aerospace, electronics, and watchmaking rely on mold polishing to achieve the required surface finish and dimensional accuracy.
Confectionery and Food Processing
Even in the realm of confectionery and food processing, mold polishing is vital for creating molds that facilitate the easy release of delicate chocolates, candies, and baked goods. Smooth, polished mold surfaces minimize sticking and improve the appearance of the final edible products.
Conclusion
Mold polishing, an intricate blend of craftsmanship and technology, is a testament to the marriage of form and function. Beyond the superficial sheen, mold polishing techniques enhance the quality, performance, and marketability of a diverse range of products across industries.
From achieving flawless finishes in plastic injection molding to optimizing the surface characteristics of delicate glassware, the art of mold polishing continues to shape the way we perceive and interact with the world of manufactured goods. As technology evolves and new materials emerge, the exploration of mold polishing techniques and their applications remains a dynamic field that underscores the pursuit of excellence in manufacturing.