Hello Readers! Before we begin learning about the injection molding process, let’s familiarize ourselves with the terms “molding” & “mold” which will be used in most –
Molding is a process of making plastic products having desirable shape and size as per our requirements with the help of rigid body frame known as mold. Mold is a robust construction of mainly two halves called core & cavity. A gap between these half remains when they close & this gap is filled with molten plastic material which filled in it through the sprue from the machine nozzle. This molten plastic material takes the shape as per gap design which is called molding.
Injection Molding Process
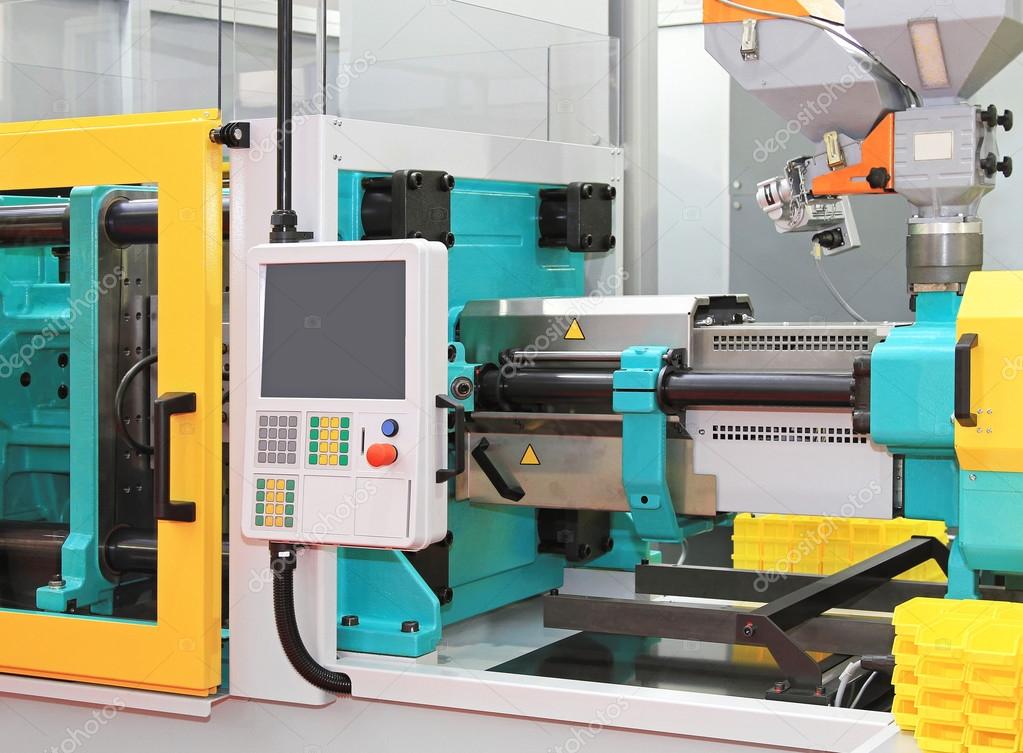
It is a manufacturing process for making parts by injecting molten plastic materials into the mold. These molten plastic materials may be elastomers, confections, thermoplastic polymers, thermosetting polymers, metals or glasses. After the material is injected into the mold cavity, it cools and hardens to the configuration of the the cavity.
What are 4 Stages of Injection Molding Process?
- Clamping
- Injection
- Cooling
- Ejection
What is Clamping Stage in Injection Molding Process?
Clamping stages in injection molding are the steps involved in securing and opening the mold during the injection molding process. The clamping unit is responsible for holding the mold halves together and applying sufficient force to withstand the injection pressure. This is the first stage, where the mold halves are attached to the injection molding machine and aligned with each other. The mold is closed by a hydraulic or mechanical mechanism that applies a clamping force. The clamping force depends on the size and shape of the part, the material properties, and the injection pressure. The clamping force should be high enough to prevent mold flash, but not too high to damage the mold or the machine.
What is Injection Stage in Injection Molding Process?
Injection stages in injection molding are the steps involved in injecting and solidifying the molten plastic into the mold cavity during the injection molding process. The injection unit is responsible for melting, metering, and injecting the plastic material into the mold under controlled conditions. It have different stages & they are –
- Filling :- This is the first stage, where the molten plastic is injected into the mold cavity through a nozzle at a high speed and pressure. The filling stage determines the flow behavior, orientation, and distribution of the plastic material in the mold.
- Packing :- In this second stage, where the molten plastic is compressed and packed into the mold cavity to compensate for the shrinkage that occurs during cooling. The packing stage involves applying a lower but constant pressure and holding it for a certain time until the gate freezes.
What is Cooling Stage in Injection Molding Process?
Cooling stages in injection molding are the steps involved in removing heat from the molten plastic in the mold cavity and allowing it to solidify and harden into the desired shape during the injection molding process. The cooling unit is responsible for circulating a cooling medium, such as water or oil, through the mold or around the mold to transfer heat from the plastic to the environment. It have different stages & they are –
- Cooling Start :- This is the first stage, where the cooling process begins after the packing and holding stage is completed. The packing and holding stage injects additional material into the mold cavity to compensate for the shrinkage that occurs during cooling.
- Cooling Duration :- This is the second stage, where the cooling process continues until the plastic reaches a temperature that allows it to be ejected from the mold without deformation or damage. The cooling duration stage is the longest and most important stage in the injection molding process, as it determines the cycle time, part quality, and energy consumption.
What is Ejection Stage in Injection Molding Process?
Ejection stages in injection molding are the steps involved in removing the solidified plastic part from the mold cavity and preparing the mold for the next cycle during the injection molding process. The ejection unit is responsible for opening the mold and pushing the part out of the mold by ejector pins or other mechanisms. It have different stages & they are –
- Mold Opening :- This is the first stage, where the mold is opened by a hydraulic or mechanical mechanism that separates the mold halves. The mold opening stage depends on factors such as part size, mold design, and clamping force.
- Part Ejection :- This is the second stage, where the part is ejected from the mold cavity by ejector pins or other mechanisms that are attached to the ejector plate. The part ejection stage requires sufficient force and speed to overcome the friction and adhesion between the part and the mold.
- Mold Closing :- This is the final stage, where the mold is closed again and ready for the next injection cycle. The mold closing stage involves aligning and clamping the mold halves together and applying a clamping force.
What are 5 Elements of Injection Molding Process?
- Temperature
- Speed
- Pressure
- Time
- Position
Temperature : The temperature element in injection molding is the factor that affects the heating and cooling of the plastic material and the mold during the injection molding process. The temperature element plays a vital role in determining the quality, consistency, and efficiency of the molded parts. The temperature element involves-
- Resin Temperature :- This is the temperature of the plastic material that is melted and injected into the mold cavity. The resin temperature depends on factors such as resin type, viscosity, flow rate, and injection pressure.
- Mold Temperature :- This is the temperature of the mold cavity that receives and solidifies the molten plastic. The mold temperature depends on factors such as mold design, cooling system, part geometry, and material properties.
- Ambient Temperature :- This is the temperature of the environment around the injection molding machine and the mold. The ambient temperature affects the heat transfer between the plastic material, the mold, and the air.
Speed : The speed element in injection molding is the factor that affects the rate and time of the injection, cooling, and ejection of the plastic material and the part during the injection molding process. The speed element plays a vital role in determining the flow, filling, packing, and solidification of the material and the part. The speed element involves-
- Injection Speed :- This is the speed at which the molten plastic is injected into the mold cavity through a nozzle. The injection speed depends on factors such as material viscosity, mold design, part geometry, and injection pressure.
- Cooling Speed :- This is the speed at which the molten plastic cools down and solidifies in the mold cavity. The cooling speed depends on factors such as material properties, mold temperature, cooling system, and part thickness.
- Ejector Speed :- This is the speed at which the solidified part is ejected from the mold cavity by ejector pins or other mechanisms. The ejection speed depends on factors such as part size, shape, weight, and surface finish.
Pressure : The pressure element in injection molding is the factor that affects the force and duration of the injection, holding, and back pressure of the plastic material and the part during the injection molding process. The pressure element plays a vital role in determining the flow, filling, packing, and solidification of the material and the part. The pressure element involves-
- Injection Pressure :- This is the pressure applied by the screw to push the molten plastic into the mold cavity through a nozzle. The injection pressure depends on factors such as material viscosity, mold design, part geometry, and injection speed.
- Holding Pressure :- This is the pressure applied by the screw to compress and pack the molten plastic into the mold cavity after the injection stage is completed. The holding pressure depends on factors such as material properties, mold temperature, cooling system, and part thickness.
- Back Pressure :- This is the pressure applied by the screw to control the flow of molten plastic back into the barrel during the recovery stage. The back pressure depends on factors such as material type, screw design, screw speed, and barrel temperature.
Time : The time element in injection molding is the factor that affects the duration and sequence of the injection, cooling, and ejection of the plastic material and the part during the injection molding process. The time element plays a vital role in determining the cycle time, productivity, and efficiency of the injection molding process. The time element involves-
- Clamping Time :- This is the time taken to close and clamp the mold halves together and apply sufficient force to withstand the injection pressure. The clamping time depends on factors such as mold size, machine type, and clamping force.
- Injection Time :- This is the time taken by the screw to inject the molten plastic into the mold cavity and pack it under pressure. The injection time includes injection melt filling time and pressure holding time. The injection melt filling time is the time taken by the screw to move forward and push the melt into the mold and fill the cavity. The pressure holding time is the time to maintain the pressure on the melt to prevent shrinkage and ensure quality.
- Cooling Time :- This is the time taken by the molten plastic to cool down and solidify in the mold cavity. The cooling time depends on factors such as material properties, mold temperature, cooling system, and part thickness. The cooling time is the longest and most important stage in the injection molding process, as it determines the cycle time, part quality, and energy consumption.
- Ejection Time :- This is the time taken by the solidified part to be ejected from the mold cavity by ejector pins or other mechanisms. The ejection time depends on factors such as part size, shape, weight, and surface finish. The ejection time should be minimized to reduce cycle time and avoid damage or deformation of the part.
- Cycle Time :- The cycle time in injection molding is the total time needed to complete the stages of the molding process: clamping, injection, cooling, and ejection. The cycle time performs a critical function in determining the productivity and efficiency of the injection molding process and directly impacts customer lead times and the overall economics of the injection molding plant.
Position : The position element in injection molding is the factor that affects the relative positional accuracy between the mold core, cavity, and the moving parts during the injection molding process. The position element plays a vital role in ensuring the alignment, fit, and function of the molded parts. The position element involves-
- Guiding System :- This is the system that ensures that the moving parts travel as per the predefined trajectory during the mold opening and closing. The guiding system consists of components such as guide pins, guide bushings, guide posts, guide rails, or guide bars that are installed on the mold plates or the machine platens.
- Positioning System :- This is the system that ensures the relative positional accuracy between the mold core, cavity, and the moving parts during the injection and cooling stages. The positioning system consists of components such as locating rings, support pillars, support blocks, dowel pins, or interlocks that are installed on the mold plates or the machine platens.
Molding Defects
Molding defects are the flaws or imperfections that affect the quality, appearance, or functionality of plastic or rubber parts produced by injection molding. Molding defects can be caused by various factors, such as the molding process, the material used, the mold design, or the machine condition. Molding defects can result in customer complaints, product returns, rework, or scrap. Some of the common molding defects and how to prevent them are given below, have a look –
- Flow Lines :- These are wavy or streaky patterns that appear on the surface of molded parts, usually in a different color or shade than the surrounding area. Flow lines are caused by variations in the cooling speed or direction of the molten material as it flows through the mold cavity.
- Sink Marks :- These are depressions or dimples that appear on the surface or near the edges of molded parts, usually in thicker areas. Sink marks are caused by insufficient pressure or time to pack and hold the molten material in the mold cavity, resulting in shrinkage and contraction as it cools.
- Weld Lines :- These are lines or seams that appear on the surface of molded parts where two or more flow fronts of molten material meet and fuse together. Weld lines are caused by multiple gates, holes, inserts, or obstructions in the mold cavity that interrupt the flow of the material. Weld lines can weaken the strength and appearance of molded parts.
- Burn Marks :- These are brown or black marks or streaks that appear on the surface of molded parts, usually near the gate or vent areas. Burn marks are caused by excessive injection speed, pressure, or temperature that cause air or gas to be trapped and overheated in the mold cavity. Burn marks can damage the surface quality and aesthetics of molded parts.
- Flash :- This is excess material that appears on the edge or outside of molded parts, usually along the parting line or around inserts. Flash is caused by excessive injection pressure or clamping force that cause molten material to escape from the mold cavity through gaps or cracks. Flash can affect the dimensional accuracy and appearance of molded parts.
- Scratch Marks :- of molded parts, usually caused by friction or abrasion during ejection, handling, or assembly. Scratch marks can affect the appearance and aesthetics of molded parts, especially for high-gloss or transparent parts.
- Dent Marks :- This is a defect that appears as a small indentation or depression on the surface of molded parts, usually in thicker areas. Dent marks are similar to sink marks, but they are smaller and more localized. Dent marks are caused by insufficient pressure or time to pack and hold the molten material in the mold cavity, resulting in shrinkage and contraction as it cools. Dent marks can affect the appearance and quality of molded parts. Dent marks can be prevented by increasing the holding pressure and time; reducing the mold temperature and cooling time; reducing the wall thickness or using ribs to reinforce thicker areas; and avoiding abrupt changes in wall thickness.
- Silver Marks :- This is a defect that appears as a silvery or shiny streak or line on the surface of molded parts, usually along the direction of melt flow. Silver marks are caused by air or gas trapped in the molten material or mold cavity, which cannot escape quickly enough during injection. Silver marks can affect the appearance and strength of molded parts.
- Warpage :- This is a defect that appears as a distortion or deformation of the shape or dimensions of molded parts, usually caused by uneven shrinkage or stress during cooling. Warpage can affect the appearance, fit, and function of molded parts.
- Vacuum Voids :- These are defects that appear as bubbles or pockets of air or gas trapped inside molded parts, usually caused by insufficient packing pressure or time, low melt temperature, high mold temperature, or large wall thickness. Vacuum voids can affect the strength, quality, and appearance of molded parts.
- Jetting :- This is a defect that appears as snake-like lines or marks on the surface of molded parts, usually along the direction of melt flow. Jetting is caused by high injection speed or pressure that cause the molten material to jet out of the gate and hit the opposite wall of the mold cavity, creating turbulence and splashing. Jetting can affect the appearance and quality of molded parts.
- Short Shots :- These are defects that appear as incomplete or partially filled parts, usually caused by insufficient injection pressure, speed, or time; low melt temperature; high mold temperature; large wall thickness; or blocked or narrow gates. Short shots can affect the appearance, quality, and functionality of molded parts.
- Delamination :- These are defects that appear as thin layers or flakes on the surface of molded parts that can be easily peeled off, usually caused by foreign material contamination, excessive moisture, or incompatible materials. Delamination can affect the strength, quality, and appearance of molded parts.
- Discoloration :- These are defects that appear as changes in color or shade on the surface of molded parts, usually caused by overheating, degradation, oxidation, or contamination of the material. Discoloration can affect the appearance and aesthetics of molded parts. Discoloration can be prevented by reducing the melt temperature, injection speed, or pressure; shortening the cycle time; cleaning the barrel, nozzle, and mold regularly; purging the machine before changing materials; using stabilizers or antioxidants for heat-sensitive materials; and using materials with consistent color and quality.
- Oil Marks :- This is a defect that appears as a greasy or oily stain on the surface of molded parts, usually caused by oil leakage from the injection machine or mold components. Oil marks can affect the appearance and quality of molded parts.
- Water Marks :- This is a defect that appears as a ring-shaped or circular stain on the surface of molded parts, usually caused by moisture condensation on the mold surface or in the material. Water marks can affect the appearance and aesthetics of molded parts.
- Dust Marks :- This is a defect that appears as a speck or spot of dust or dirt on the surface of molded parts, usually caused by contamination of the material, mold, or machine. Dust marks can affect the appearance and quality of molded parts.
- Ejector Marks :- Ejector mark is a defect that appears as a dent, bump, or scratch on the surface of molded parts, usually caused by the ejection mechanism that pushes the part out of the mold. Ejector mark can affect the appearance and quality of molded parts.
- Black Spot :- This is a defect that appears as a black or dark-colored spot or streak on the surface of molded parts, usually caused by degradation, oxidation, or burning of the material. Black spots can affect the appearance and quality of molded parts. Black spots can be prevented by reducing the melt temperature, injection speed, or pressure; shortening the cycle time; cleaning the barrel, nozzle, and mold cavity regularly; purging the machine before changing materials; using stabilizers or antioxidants for heat-sensitive materials; and using materials with low degradation or oxidation tendency .
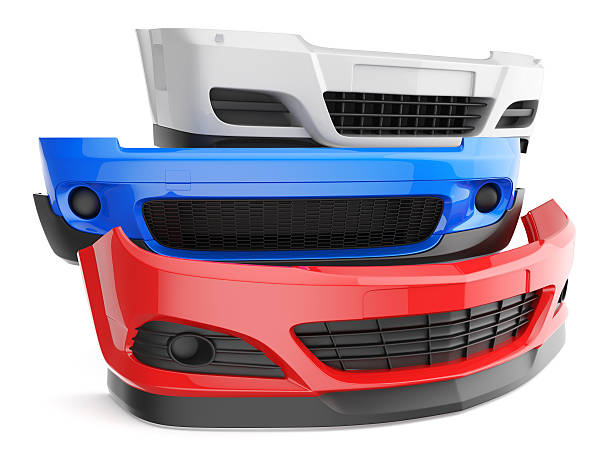
Injection Molding Applications
The application area of injection molding is the field or industry where injection molding is used to produce plastic parts or products. Injection molding is a versatile and widely used manufacturing process that can create parts with complex shapes, high quality, and low cost. Injection molding has applications in various areas, such as-
- Automotive Parts :- Injection molding is commonly used to create automobile parts, including door panels, dashboards, bumpers, lighting components, engine covers, and more.
- Medical Devices :- Injection molding can be used to create medical devices such as blood pressure cuffs, stethoscopes, syringes, surgical instruments, implants, and more.
- Consumer Electronics :- Injection molding can be used to create consumer electronics such as smartphones, tablets, laptops, keyboards, mice, headphones, and more.
- Packaging :- Injection molding can be used to create packaging products such as bottles, caps, containers, trays, boxes, and more.
What are the advantages of Injection Molding Process?
- High Production Rate :- Injection molding can produce a large number of parts in a short time, as the process is fast and efficient. The cycle time can be as short as 10 seconds, depending on the part size and complexity.
- Low Cost per Part :- Injection molding can reduce the cost per part for high-volume production runs, as the mold and machine costs are amortized over a large number of parts.
- High Repeatability & Consistency :- Injection molding can produce identical parts with high precision and accuracy, as the process is highly controlled and repeatable.
- Large Material Choice :- Injection molding can use a wide range of plastic materials, depending on the properties and requirements of the parts. There are over 25,000 engineered materials compatible with injection molding, including thermoplastics, thermosets, elastomers, biodegradable materials, and more.
- Low Waste :- Injection molding produces very little waste compared to other manufacturing processes, as the excess or scrap plastic can be reground and reused for future production.
- High Detail & Surface Finish :- Injection molding can produce parts with high detail and surface finish, as the molten plastic is injected into the mold cavity under high pressure and fills every feature of the mold. Injection molding can also apply different surface textures or finishes to the mold, which will be transferred to the parts.
What are the disadvantages of Injection Molding Process?
- High Initial Cost :- Injection molding requires a high upfront investment to create the molds and set up the machinery for the production process. The mold and machine costs can be quite high depending on the complexity and size of the part, as well as the material and quality requirements.
- Long Lead Time :- refine the molds before starting the production process. The mold design and fabrication can take weeks or months, depending on the part geometry and specifications. The mold design also needs to be done by skilled workers or engineers, who may charge high fees for their services.
- Design Limitation :- Injection molding has some restrictions on part design, as the parts need to be designed to fit the mold and follow certain rules and guidelines. For example, the parts need to have uniform wall thickness, avoid undercuts or overhangs, have draft angles for easy ejection, have rounded corners and transitions, and have adequate venting and gating.
- Design Changes & Repair :- Injection molding makes it difficult and costly to change or modify the part design once the molds are made. Any design changes require new molds or modifications to existing molds, which can increase the cost and lead time significantly.
- Environment Concerns :- Injection molding produces some environmental concerns, as it uses a lot of heating and cooling energy, which can contribute to greenhouse gas emissions and climate change. Injection molding also uses plastic materials that are hardy and difficult to recycle, leading to plastic waste and pollution.
Frequently Asked Questions
What is molding called?
Molding is a process of manufacturing by shaping liquid or pliable raw material using a rigid frame called a mold or matrix. Molding can be used to produce various objects, such as plastic parts, metal parts, ceramic parts, etc..
What makes Injection Molding such a useful process?
(1) It allows for complex geometries with tight tolerances.
(2) It provides high efficiency and fast production. Injection molding can produce parts at a very high speed, with cycle times as short as 10 seconds.
(3) It offers flexibility in color and material. Injection molding can use a wide range of plastic materials, each with different properties and characteristics. It can also use fillers, additives, or blends to enhance the performance or appearance of the parts.
(4) It reduces waste and cost. Injection molding produces very little waste, as the excess or scrap material can be recycled and reused.
What is the use Injection Molding process diagram?
An injection molding diagram is a graphical representation of the injection molding process, which is a manufacturing method for producing plastic parts by injecting molten plastic into a mold. The use of an injection molding diagram is to help understand, explain, or optimize the injection molding process.