Injection Mold Types, Materials used in Injection Molding, Advantages, Disadvantages, Applications
Introduction
Injection molding is a widely used manufacturing process that has revolutionized the production of plastics and other materials. Its versatility, speed, and accuracy make it an essential technology in a variety of industries. In this comprehensive guide, we’ll explore the basic principles, process steps, benefits, and applications of injection molding. Whether you are new to the field or looking to expand your knowledge, this article aims to provide a thorough understanding of injection molding.
What is Injection Mold?
Injection mold, also known as injection molding or injection molding tooling, is a manufacturing process that involves injecting molten material into a specially designed mold cavity to create complex three-dimensional shapes. The process is widely used to produce a range of plastic products, including components, containers, packaging, toys, and more. Injection mold offers high production efficiency, consistency, and the ability to create intricate details with precise dimensions. There are several different types of injection molds used in the injection molding process. Let’s explore some of the common types –
- Two-Plate Mold : The two-plate mold, also known as the single cavity mold, is the simplest and most commonly used type of injection mold. It consists of two plates, the cavity plate, and the core plate, which come together to form the mold cavity when closed. This type of mold is suitable for producing relatively simple parts.
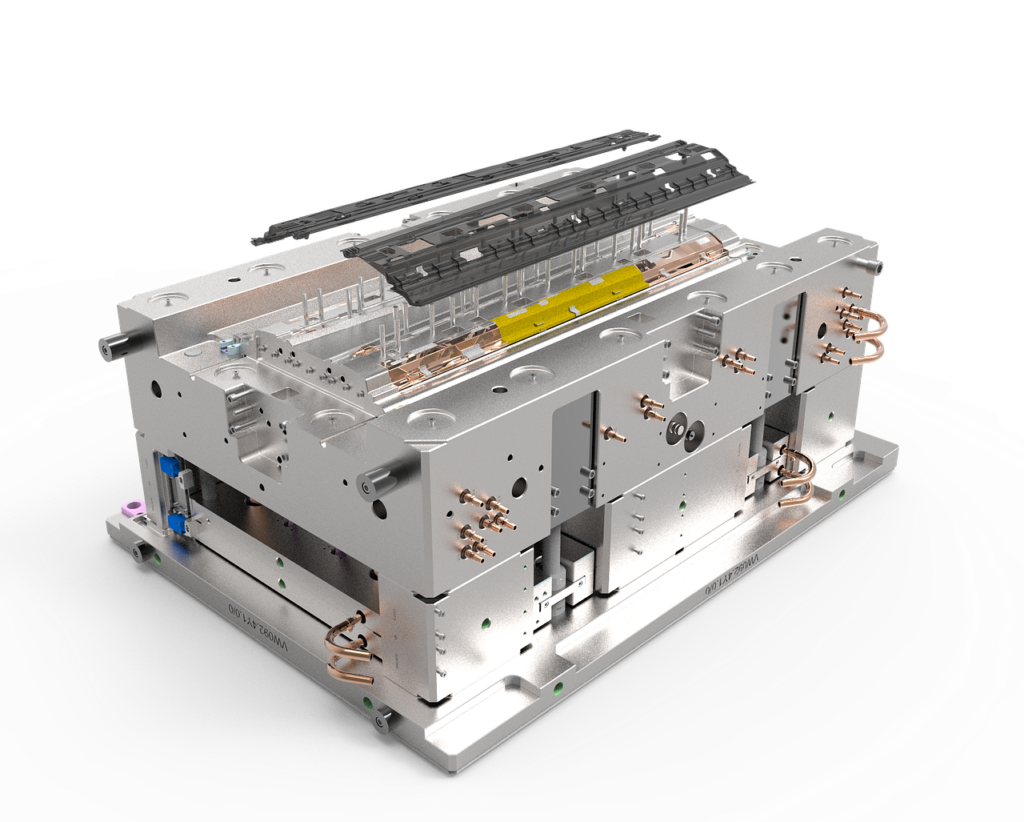
- Three-Plate Mold : It is also called a split mold, and has an additional plate known as the runner plate. This plate creates a separate runner system, allowing for the injection of material into multiple cavities or different parts of a complex part. The three-plate mold enables more flexibility in part design and increased productivity.
- Hot Runner Mold : In this type of mold, the runner system is heated, allowing the molten material to flow directly into the mold cavity without the need for separate runners. This eliminates the need for the runner system to be ejected and reduces material waste. Hot runner molds are often used for high-volume production and can improve cycle times and part quality.
- Cold Runner Mold : In contrast to a hot runner mold, a cold runner mold has a runner system that is not heated. The molten material is injected into the runner system, where it solidifies, and then is ejected along with the part during the ejection phase. Cold runner molds are simpler and less expensive than hot runner molds but can result in more material waste.
- Insert Mold : An insert mold incorporates metal or other pre-formed inserts into the mold cavity during the injection molding process. The inserts can be threaded inserts, pins, electrical components, or other elements that need to be encapsulated within the plastic part. Insert molds allow for the creation of composite parts with added functionality.
- Over-mold : Over-molding involves the use of multiple materials or colors to create a single part. It combines a base material or substrate with one or more additional materials that are molded over it. Over-molding can provide improved grip, soft-touch surfaces, enhanced aesthetics, and the integration of multiple materials in a single part.
- Family Mold : A family mold, also known as a multi-cavity mold, allows for the production of multiple identical parts in a single molding cycle. It consists of multiple cavities within the mold, each corresponding to the desired part. Family molds increase production efficiency and reduce per-unit costs.
- Prototype Mold : prototype mold is used for low-volume production or to create functional prototypes for testing and validation purposes. These molds are typically less complex and less expensive than production molds and are designed to quickly produce small quantities of parts.
The Injection Molding Process
Injection molding is a manufacturing process for producing parts by injecting molten material, usually plastic, into a mold. The mold is a metal frame that has the shape of the desired part. The material is heated and mixed in an injection molding machine, then forced into the mold cavity by a screw or a plunger. The material cools and hardens in the mold, forming the part.
It is widely used for making various products, such as buttons, combs, toys, electronics, automotive parts, and more. It can produce complex shapes with high precision and quality, while reducing waste and cost. Injection molding has evolved since its invention in the late 19th century. It became popular during World War II when plastic replaced rare materials such as rubber and metal. This improved with the development of screw injection machines, gas-assisted injection molding systems, and aluminum molds.
Mold Design and Manufacturing
The first step in injection molding is the design and manufacture of the mold. The mold consists of two parts, the cavity and the core, which are precisely machined to form the desired shape of the final product. The design must consider factors such as part geometry, material flow, cooling channel and ejection mechanism. Computer-aided design (CAD) software and computer-aided manufacturing (CAM) equipment are commonly used in this step to optimize the mold design.
Material Preparation
The next step involves preparing the material for injection. Typically, plastic pellets or granules are melted in the heated barrel of an injection molding machine. The material is carefully selected on the basis of its properties, such as strength, ductility, heat resistance and color. Lists of common plastic materials generally used in injection molding are –
- High-Density Polyethylene (HDPE)
- Low-Density Polyethylene (LDPE)
- Polycarbonate (PC)
- Nylon
- Polyoxymethylene (POM)
- Polypropylene (PP)
- Acrylic Poly (Methyl Methacrylate) (PMMA)
- Thermoplastic Polyurethane (TPU)
- Thermoplastic Rubber (TPR)
Injection Molding Machine
The injection molding machine is an important component in this process. It consists of a hopper, an injection unit and a clamping unit. The material is fed into the hopper of the machine, where it is heated and melted. Then the molten material is injected into the mold cavity under high pressure through the injection unit. List of common injection molding machines are –
- Toyo
- Toshiba
- L&T
- Haitian
- Husky
- ENGEL
- Milacron
- Sumitomo Demag
- Newbury
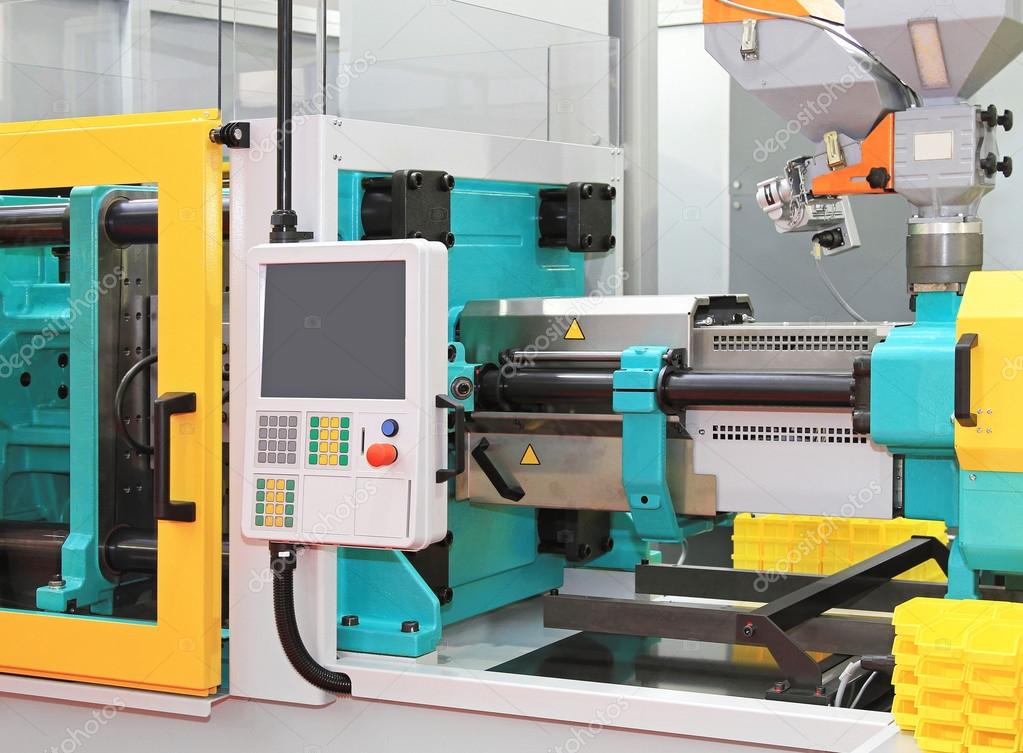
Injection Process
During the injection process, the molten material fills the mold cavity, and takes the shape of the mold’s design. The injection pressure and speed are carefully controlled to ensure proper filling and minimize defects such as air pockets or voids. Once the mold cavity is filled, the material is allowed to cool and solidify.
Cooling and Ejection
After the material solidifies within the mold, it goes through a cooling phase. Cooling channels within the mold help to dissipate heat and speed up the solidification process. Once the material has cooled and hardened, the mold is opened, and the finished product is ejected from the mold using an ejector pin or robotic arm.
Materials Used in Injection Molding
Injection molding supports a wide range of materials, each offering unique properties suited to different applications. The most commonly used materials include –
- Thermoplastics : These are commonly used materials in injection molding. They are capable of repeated thawing and freezing without significant degradation. Common thermoplastics include polyethylene (PE), polypropylene (PP), polystyrene (PS), acrylonitrile butadiene styrene (ABS), and polyvinyl chloride (PVC).
- Thermosetting Plastics : Unlike thermoplastics, undergo irreversible chemical reactions during curing. Once cured, they cannot be melted down or reprocessed. Examples of thermosetting plastics are epoxy resins, phenolic resins, and melamine formaldehyde.
- Elastomers : Elastomers, often referred to as rubber, exhibit high elasticity and are commonly used for products that require flexibility and ductility. Some elastomers used in injection molding include natural rubber, silicone rubber, and polyurethane.
Advantages of Injection Molding
- High Efficiency and Speed : Injection molding provides high production efficiency and rapid cycle times. With the ability to produce large quantities of identical parts in a short period of time, it is a cost-effective solution for mass production.
- Design Flexibility : Injection molds enable the creation of complex shapes and intricate details that would be difficult or impossible to achieve with other manufacturing methods. This allows multiple features such as undercuts, threads and inserts to be integrated into a single molded piece.
- Enhanced Product Quality : Injection molding ensures consistent part quality with minimal variations. This process provides tight tolerances, high surface finish and excellent dimensional stability, resulting in products that meet stringent specifications and customer requirements.
- Cost-effectiveness : Although the initial investment in mold design and manufacturing can be significant, injection molding offers long-term cost advantages. The ability to efficiently produce large quantities and the low per-unit cost make it an economically viable option for high-volume production.
- Wide Range of Applications : Injection molding has applications in various industries. It is used in automotive components, medical devices, consumer goods, electronic enclosures, packaging, and more. The versatility of an injection mold makes it a preferred choice for manufacturing a wide spectrum of products.
Common Applications of Injection Mold
- Consumer Products : Injection molding is widely used to produce consumer products such as household goods, kitchenware, toys, and electronics. This process allows for the creation of aesthetically pleasing designs with improved functionality.
- Automotive Industry : The automotive industry uses injection molding extensively to manufacture a variety of components, including interior and exterior trim, dashboard parts, bumpers, lighting, and engine components. Injection molding provides lightweight, durable and cost-effective solutions to the automotive sector.
- Medical and Healthcare : Injection molding plays an important role in the medical and healthcare sector, where precision and quality are critical. It is used to produce medical instruments, laboratory equipment, surgical instruments and disposable items such as syringes and vials.
- Packaging : Injection mold contributes to the production of plastic packaging containers, caps, closures and bottles. Its ability to create complex designs, logos and branding elements on packaging materials adds value to product presentation.
- Aerospace : The aerospace industry relies on injection molding to manufacture lightweight and high-strength components, including air ducts, brackets, interior panels, and connectors. This process enables the production of complex shapes with excellent dimensional accuracy.
Challenges and Considerations in Injection Molding
- Design Considerations : Proper design is essential to avoid problems such as sink marks, warpage and part ejection problems. Designers must consider factors such as wall thickness, draft angle, corner radius, and location of gate and ejector pins.
- Material Selection : It is very important for confirming the right material for the intended application. Factors such as mechanical properties, chemical resistance, heat resistance and cost must be carefully evaluated.
- Tooling and Mold Maintenance : Regular maintenance of injection molds is essential to ensure consistent product quality and mold longevity. Mold cleaning, inspection and repair are essential steps to maintain production efficiency.
- Quality Control and Inspection : Injection molding requires stringent quality control measures to identify and correct defects. Various inspection techniques such as dimensional checking, visual inspection and non-destructive testing are employed to ensure part conformance.
Future Trends in Injection Molding
Injection molding continues to evolve with advances in technology and materials. Some future trends include the integration of automation and robotics for improved efficiency, the use of sustainable and bio-based materials, and the development of smart molds with real-time monitoring capabilities.
Conclusion
Injection mold is a versatile manufacturing process that has transformed the production of plastic and other materials. Its ability to create complex shapes, maintain high precision, and deliver consistent quality has made it an indispensable technique in numerous industries. By understanding the fundamentals, process steps, benefits, and applications of injection molding, manufacturers and designers can harness its potential to bring innovative products to the market efficiently and cost-effectively.
In this guide, we have covered the basics of injection molding, the materials used, its advantages and challenges, as well as its applications in various sectors. By keeping up with emerging trends, such as automation and sustainable materials, the future of injection molding looks promising. With this knowledge, you are now equipped to delve deeper into the world of injection mold and explore its endless possibilities.
What is injection molding?
Injection molding is a manufacturing process that involves injecting a molten material, usually plastic, into a specially designed mold cavity. The material solidifies within the mold and takes the shape of the desired product. It is a widely used technology for producing plastic parts with high precision and efficiency.
How is an injection mold designed?
Designing an injection mold involves considering factors such as part geometry, material flow, cooling channels, and ejection mechanisms. Computer-aided design (CAD) software and computer-aided manufacturing (CAM) tools are commonly used for mold design and optimization.
What factors should be considered in injection mold design?
Several factors influence injection mold design, including part geometry, wall thickness, draft angles, gate location, ejector pin placement, and venting. These factors impact the mold’s functionality, ease of production, and part quality.
What industries use injection molding?
Injection molding finds applications in various industries, including automotive, consumer products, medical and healthcare, packaging, electronics, and aerospace. It is used to manufacture components, parts, containers, and more.
How long does the injection molding process take?
The time required for the injection molding process depends on factors such as part complexity, size, material, and machine capabilities. Cycle times can range from a few seconds to several minutes.
Can injection molds be reused for different parts?
Injection molds can be reused for different parts, provided the design and dimensions are compatible. In such cases, the mold may require adjustments or modifications to accommodate the new part requirements.
Are there any environmental considerations with injection molding?
Injection molding can generate waste material, such as sprues and runners, but these can often be recycled and reused. Additionally, the industry is exploring sustainable alternatives, including bio-based and recycled materials, to reduce its environmental impact.
What are some future trends in injection molding?
Future trends in injection molding include the integration of automation and robotics for increased efficiency, the use of sustainable and biodegradable materials, advancements in mold technology with real-time monitoring, and improved process control for enhanced part quality.
Nice
Thanks dear for your feedback.
qFphmHaJFnIJASvwzX
MaqyyVBBSDjYlOjdT