In this article, we will cover descaling machines, the descaling process, chemicals/solutions used in descaling machines, the need for descaling for molds, LPM, advantages & disadvantages of descaling machines.
Introduction
Molds are an integral part of many manufacturing processes, used in industries ranging from automotive to food and beverages. However, over time, molds can accumulate mineral deposits and scale, which not only hinders their performance but also poses a significant threat to the quality of the end product. To address this challenge, engineers and manufacturers have developed innovative solutions like descaling machines for molds, which promise to revolutionize the maintenance and efficiency of molding equipment. In this blog, we will explore the world of mold-descaling machines and how they deliver mold-descaling at its finest.
Understanding the Mold Descaling Process
Before diving into the intricacies of mold-descaling machines, let’s first understand the mold-descaling process itself. Descaling involves the removal of scale, rust, and mineral deposits that accumulate on the surfaces of molds over time. These deposits can result from the use of hard water, cooling systems, or even the materials used in the molding process. If left untreated, these buildups can lead to reduced heat transfer, uneven cooling, increased cycle times, and decreased product quality.
Traditionally, manual methods such as wire brushing, scraping, and chemical treatments were employed to descale molds. However, these methods are time-consuming, labor-intensive, and may not be effective in removing stubborn scales from intricate mold surfaces. This is where mold-descaling machines step in.
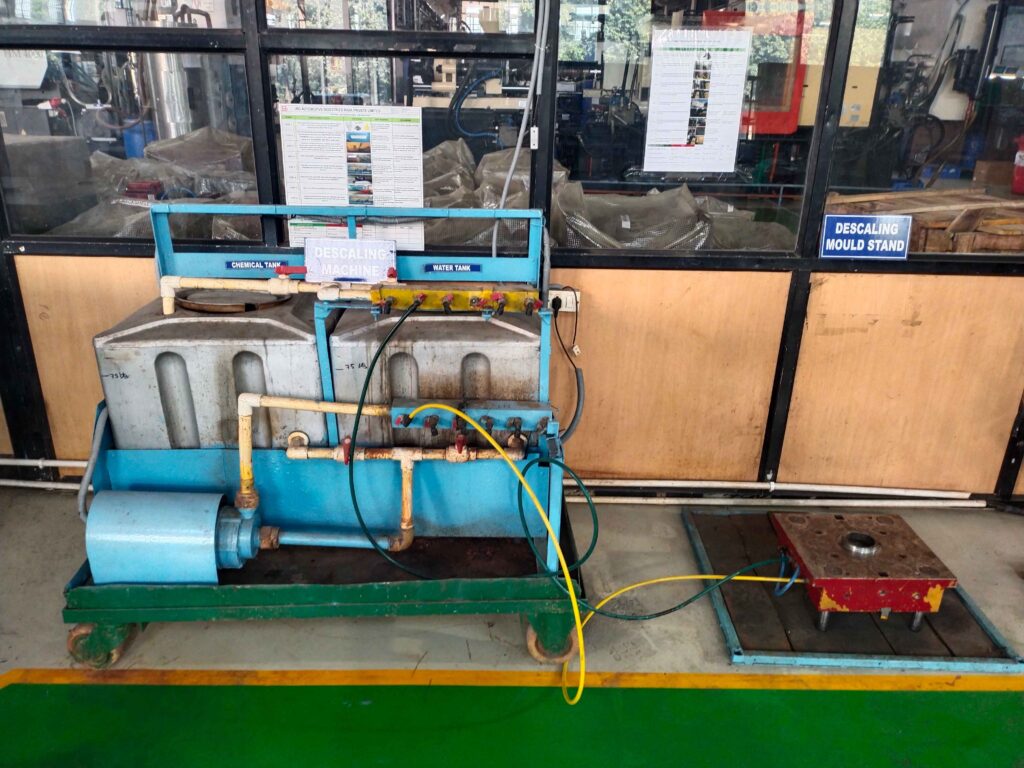
The Role of Mold Descaling Machines
Mold descaling machines are advanced systems designed to automate and optimize the descaling process. They incorporate cutting-edge technologies and features that significantly enhance the efficiency and effectiveness of mold maintenance. Here are some key benefits of using mold descaling machines –
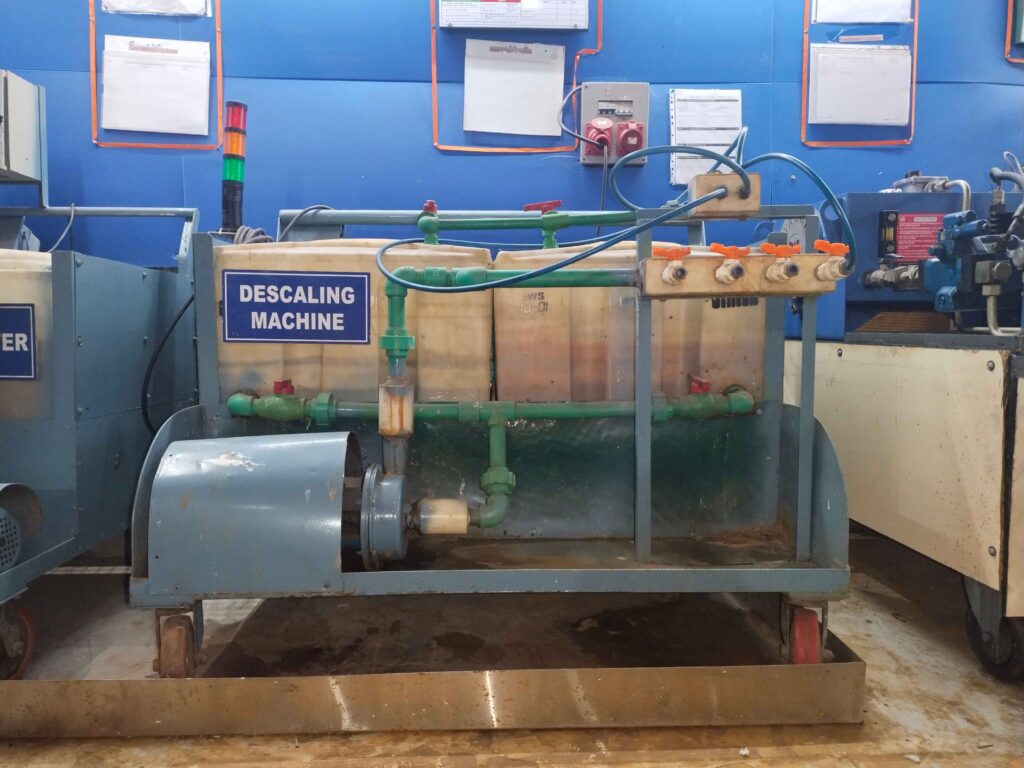
1. Precision Cleaning
Mold descaling machines utilize various cleaning methods, such as high-pressure water jets, abrasive blasting, or ultrasonic cleaning, to ensure thorough and precise removal of scales. These methods can reach even the most challenging areas of complex molds, leaving no scale behind.
2. Time and Cost Savings
Automating the descaling process reduces the manual labor required for mold maintenance, leading to considerable time and cost savings. The machines are designed to work efficiently, reducing downtime and increasing productivity.
3. Consistent Results
Manual descaling methods may vary in effectiveness depending on the operator’s skill and effort. On the other hand, mold descaling machines deliver consistent and repeatable results, ensuring that each mold undergoes the same level of cleaning.
4. Eco-Friendly Solutions
Many mold-descaling machines employ eco-friendly cleaning agents and technologies, minimizing the use of harsh chemicals. This not only reduces the environmental impact but also ensures a safer working environment for operators.
5. Prolonged Mold Life
Regular and thorough descaling helps extend the lifespan of molds. By preventing scale buildup, the molds remain in optimal condition, leading to improved product quality and reduced mold replacement costs.
Need of Descaling for Injection Molds
Injection molding is a widely used manufacturing process in which molten material is injected into a mold cavity to create various complex and precise shapes. Over time, injection molds can accumulate rust, scale, or other contaminants in the cooling channel of the core, cavity, and part of the mold where the cooling channel is provided due to the constant exposure to high temperatures and the materials being processed. This build-up can negatively impact the mold’s performance and lead to several issues, highlighting the need for a descaling machine in injection molding operations. Here are some reasons why descaling machines are essential –
1. Maintenance and Longevity
Regular maintenance is critical to ensuring the longevity and optimum performance of injection molds. Descaling machines help remove mineral deposits and contaminants, thereby preventing corrosion from the cooling channels of the mold to extend the lifetime of the mold. By preserving the integrity of the mold, manufacturers can avoid costly replacements and downtime.
2. Improved Mold Cooling Efficiency
Scale deposits and contaminants in the mold cooling channel can hinder heat transfer and cooling efficiency during the injection molding process. Descaling the mold restores its heat transfer properties, allowing for more effective and uniform cooling. As a result, cycle times are reduced, productivity is increased and part quality is consistent.
3. Preventing Production Delays
Mold scaling and contamination can cause frequent breakdowns and interruptions in the production process. Regular descaling can help prevent unexpected mold-related problems and reduce production delays, keeping the manufacturing process running smoothly and efficiently.
**In summary, a descaling machine is an essential tool in the maintenance and upkeep of injection molds. It helps improve mold performance, product quality, and production efficiency, while also ensuring a safer and healthier working environment. Regular descaling not only extends the life of the molds but also contributes to the overall success and profitability of injection molding operations.
How to Know When Descaling is Required in Mold?
Descaling injection molds is an essential maintenance practice to ensure the molds’ optimal performance and the quality of the molded parts. While there might not be an exact timeline for when descaling is required, certain indicators can help you determine when it’s time to descale an injection mold. Here are some signs that suggest descaling is necessary –
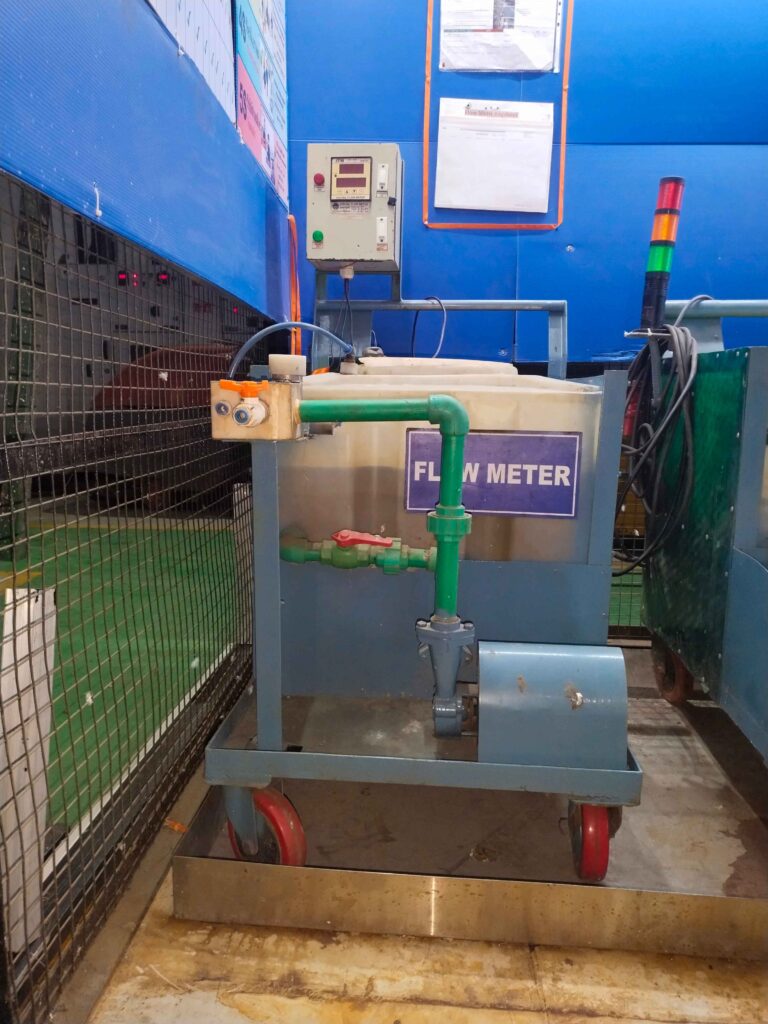
- Decreased Mold Cooling Efficiency: If you notice an increase in cycle times or inconsistent cooling of the molded parts, it may indicate that the mold’s cooling channels are partially or completely clogged with mineral deposits or scale. This reduced cooling efficiency can lead to longer production cycles and affect the quality of the parts.
- Surface Defects on Molded Parts: Scaling on the mold’s surface can transfer to the molded parts, causing surface defects like streaks, spots, or blemishes. If you observe an increase in the number of defective parts or inconsistent surface finish, it could be an indication that the mold needs descaling.
- Uneven Mold Temperature Distribution: During the injection molding process, an even mold temperature distribution is crucial for producing uniform and dimensionally accurate parts. If there are temperature variations across the mold surface, it may be a result of scale build-up affecting the heat transfer.
- Visible Scale or Deposits: Regular visual inspection of the mold can reveal the presence of scale or mineral deposits on the mold’s cooling channels, surfaces, or other critical areas. If you notice any visible signs of scaling, it’s time to consider descaling.
- Mold Corrosion: Mold corrosion can occur due to the presence of contaminants or the reaction of certain plastics with the mold material. Descaling can help remove these contaminants and prevent further corrosion, which could compromise the mold’s structural integrity.
- Regular Maintenance Schedule: As a preventive measure, it’s a good practice to include descaling in the mold’s regular maintenance schedule. Even if there are no noticeable issues, periodic descaling can help prevent potential problems and ensure the mold’s long-term performance.
**To determine the appropriate descaling frequency, it’s essential to consider factors such as the material being processed, the frequency of mold use, and the water quality used for cooling. If you are unsure about whether descaling is required or how to perform it correctly, it’s best to consult the mold manufacturer’s guidelines or seek advice from mold maintenance experts. Proper and timely descaling can significantly contribute to the efficiency, productivity, and quality of injection molding operations.
Which Chemical is Used in Mold Descaling Machines
The chemical used in descaling machines for mold cooling line cleaning is typically a descaling solution or descaler. Descalers are specifically formulated to dissolve and remove mineral deposits, scale, and other contaminants that accumulate in the cooling lines of injection molds. The choice of a descaling chemical can vary depending on the type of scale or deposits present and the material of the injection mold.
Commonly used descaling chemicals include –
1. Citric Acid
Citric Acid is a mild organic acid that is effective in removing calcium-based scale deposits. It is relatively safe to handle and is biodegradable, making it an environmentally friendly choice.
2. Phosphoric Acid
Phosphoric Acid is another popular choice for descaling. It is effective in dissolving various types of scales, including calcium, rust, and mineral deposits.
3. Sulfamic Acid
Sulfamic Acid is a strong acid that is particularly effective against stubborn scale deposits. It is commonly used for heavy-duty descaling applications.
4. Hydrochloric Acid (Muriatic Acid)
Hydrochloric acid is a potent acid that can effectively dissolve tough mineral deposits and scale. However, it is highly corrosive and should be handled with extreme care and proper safety precautions.
5. Acetic Acid (Vinegar)
While not as powerful as other descaling agents, vinegar (a dilute acetic acid solution) can be used for mild scale removal in less severe cases.
**It’s important to note that the choice of descaling chemical should be made based on the type of scale or deposits present and the material of the injection mold. Some descaling chemicals can be corrosive and may cause damage to certain types of mold materials, especially if used improperly or at high concentrations. Always follow the manufacturer’s guidelines and recommended procedures when using descaling chemicals and ensure proper safety measures are in place to protect yourself and the environment.
Before using a descaling machine or chemical, it’s advisable to consult with the mold manufacturer or a qualified mold maintenance expert to determine the most suitable descaling solution for your specific application. Additionally, always ensure proper ventilation and personal protective equipment (PPE) are used when handling descaling chemicals to minimize any potential risks.
Safety Precautions Need to Follow While Working on Descaling Machine
Working on a descaling machine for mold cooling line cleaning involves handling chemicals and operating equipment that can pose certain risks to the operator’s safety and health. To ensure a safe working environment, it is essential to follow specific safety precautions. Here are some guidelines to consider when working with a descaling machine for mold cooling line cleaning –
1. Personal Protective Equipment (PPE)
- Wear appropriate PPE, including safety goggles or face shields, chemical-resistant gloves, and a lab coat or apron to protect against chemical splashes and spills.
2. Adequate Ventilation
- Ensure the work area is well-ventilated to prevent the accumulation of fumes and vapors from the descaling chemicals. If possible, use local exhaust ventilation or work in a fume hood to remove any airborne contaminants.
3. Chemical Handling
- Familiarize yourself with the descaling chemical’s safety data sheet (MSDS) to understand its potential hazards, safe handling, and disposal procedures.
- Only use chemicals that are specifically recommended for descaling injection molds.
- Avoid mixing different chemicals unless specified by the manufacturer, as this can lead to hazardous reactions.
4. Proper Dilution
- Dilute the descaling solution as per the manufacturer’s instructions. Using the correct concentration is essential to avoid damage to the mold or the descaling machine.
5. Containment and Spills
- Use appropriate containers or trays to contain the descaling solution during the cleaning process.
- Have a spill response plan in place and be prepared to handle any accidental spills promptly and safely.
6. Equipment Inspection
- Regularly inspect the descaling machine for any signs of damage or malfunction before use. If any issues are detected, have the equipment serviced or repaired before proceeding.
7. Training
- Ensure that operators and personnel working with the descaling machine are adequately trained in its operation, safety procedures, and emergency response protocols.
8. First Aid
- Have a well-equipped first aid kit readily available in the work area, and ensure that operators know how to administer first aid for chemical exposure or injuries.
9. Emergency Procedures
- Establish and communicate clear emergency procedures, including evacuation routes and assembly points, in case of accidents or chemical spills.
Environmental Consideration
- Dispose of used descaling solutions and waste materials properly, following local regulations and environmental guidelines.
By adhering to these safety precautions, operators can minimize risks and create a safer working environment when using a descaling machine for mold cooling line cleaning. Safety should always be a top priority when working with chemicals and industrial equipment to prevent accidents, injuries, and environmental harm.
Pros and Cons of Descaling Machine for Molds
Using a descaling machine for injection molds has its advantages and disadvantages. Let’s explore the pros and cons –
Pros of Descaling Machine for Injection Mold
1. Efficient Scale Removal
Descaling machines are designed to efficiently remove mineral deposits, scale, rust, and other contaminants from injection molds. They use specialized descaling solutions and techniques, ensuring thorough and effective cleaning of the molds’ cooling channels and surfaces.
2. Improved Mold Performance
By eliminating scale and deposits, the descaling process enhances the mold’s cooling efficiency. This results in better heat transfer during the injection molding process, leading to shorter cycle times, increased productivity, and improved part quality.
3. Prevents Surface Defects
Descaling helps maintain a clean mold surface, preventing contaminants from transferring onto the molded parts. This reduces the occurrence of surface defects, streaks, and blemishes, ensuring consistent and high-quality molded products.
4. Prolongs Mold Lifespan
Regular descaling prevents the accumulation of scale and corrosion, which can lead to mold deterioration over time. By extending the mold’s lifespan, manufacturers can avoid costly replacements and ensure continued production efficiency.
5. Safer Working Environment
Mold scaling can harbor harmful contaminants that pose health risks to operators and personnel. Descaling machines help create a safer working environment by removing these potential hazards.
6. Versatility
Descaling machines are available in various sizes and configurations, making them adaptable to different mold types and sizes.
Cons of Descaling Machine for Injection Mold
1. Initial Investment
Purchasing a descaling machine represents a capital expense, which might be a deterrent for some smaller manufacturers or those with limited budgets.
2. Chemical Handling
Descaling machines use chemical solutions, which require proper handling and storage to ensure safety and avoid environmental hazards. Operators must follow safety protocols and wear appropriate personal protective equipment (PPE) when working with these chemicals.
3. Potential Corrosion Risks
Some descaling chemicals, if used incorrectly or on certain mold materials, can cause corrosion or damage. Care must be taken to select the right descaling solution suitable for the specific mold material.
4. Regular Maintenance
The descaling machine itself requires regular maintenance to ensure its proper functioning. This includes cleaning, calibration, and replacement of components as needed.
5. Operator Training
Proper training is necessary for operators to use the descaling machine effectively and safely. Inadequate training could lead to errors or accidents during the descaling process.
6. Environmental Impact
Depending on the descaling solution used, there might be environmental implications if the chemicals are not disposed of properly or if they interact negatively with wastewater treatment systems.
Conclusion
Mold descaling machines have undoubtedly revolutionized the way molds are cleaned and maintained. Through their precision, automation, and advanced features, these machines deliver mold descaling at its finest. By investing in these innovative solutions, industries can ensure the longevity and efficiency of their molds while guaranteeing the production of high-quality products.
As technology continues to advance, we can expect further improvements in mold-descaling machines, making them even more versatile and efficient. Manufacturers and engineers must stay abreast of these developments to embrace the latest advancements in mold maintenance and stay competitive in their respective industries. With mold descaling machines, the future of mold maintenance looks brighter than ever before.
Here I have picked up some questions which are generally asked on Google, I have looked on it –
What is the full form of LPM?
Litre Per Minute
What is the use of LPM in a descaling machine for mold?
It’s important to note that the LPM requirement for a descaling machine may vary depending on the size and complexity of the injection mold, the type and severity of scale or deposits, and the specific descaling solution being used. Manufacturers and operators should refer to the descaling machine’s specifications and the descaling solution manufacturer’s guidelines to determine the appropriate LPM setting for each cleaning application.
Overall, the use of LPM in a descaling machine is a critical parameter that directly influences the effectiveness and efficiency of mold cooling line cleaning, contributing to the maintenance and performance of injection molds in the long run.
What is the price of a descaling machine?
In general, descaling machines for molds can range from a few hundred dollars for small, manual machines to several thousand dollars for large, automated systems with advanced features. Higher-end, industrial-grade descaling machines can cost even more, especially if they come with sophisticated controls, higher flow rates, and additional functionalities.