Overview of Cooling Connector for Injection Mold
The cooling connector for the injection mold is an important component used in the plastic injection molding process to efficiently manage and regulate the temperature of the mold during production. Injection molding is a widely used manufacturing technique to produce large quantities of plastic parts, and precise temperature control is essential to achieve high-quality and consistent results.
A cooling connector, also known as a cooling line or cooling channel, is integrated into the design of the mold and strategically placed to facilitate the circulation of the cooling medium, usually water or oil. Its primary purpose is to take out the excess heat generated during the molding process so that the molten plastic inside the mold cavities can cool down and cool down.
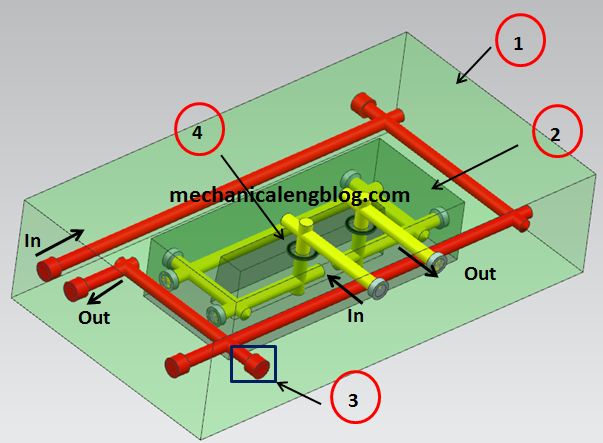
Key Features and Functions
- Temperature Regulation: The cooling connector plays a vital role in maintaining a controlled and consistent temperature throughout the mold. It aids in preventing defects like warping, shrinkage, and uneven surfaces by ensuring that the plastic cools and solidifies uniformly.
- Efficient Heat Dissipation: By circulating a cooling medium through the cooling channels, the connector facilitates the rapid dissipation of heat from the mold. This allows for faster cycle times, enabling higher production rates and cost-effectiveness.
- Mold Material Preservation: Proper cooling minimizes thermal stress on the mold, extending its lifespan and reducing the likelihood of premature wear and tear. This is especially crucial for high-volume production scenarios.
- Design Flexibility: Cooling connectors offer flexibility in mold design. They can be customized and strategically placed to cater to the specific cooling requirements of the molded part, ensuring optimal results for complex geometries.
- Water or Oil Cooling: Cooling connectors can be designed for either water-based or oil-based cooling systems, depending on the specific needs of the injection molding process and the type of material being molded.
- Temperature Monitoring: Some advanced cooling connectors may include temperature sensors or thermocouples to monitor the temperature of the mold in real time. This data can be used to make adjustments and optimize the cooling process further.

Importance of Cooling Connector
Cooling connector is an important element in the injection molding process because it directly affects the quality, efficiency, and cost-effectiveness of the product. Proper cooling reduces cycle time, which increases productivity and reduces lead time. It also contributes to the production of parts with high dimensional accuracy and a better surface finish.
- Optimizing the cooling process through a well-designed cooling connector can help manufacturers achieve consistent part quality, reduce material waste, and reduce energy consumption, ultimately improving their injection molding operations. The overall competitiveness is increased.
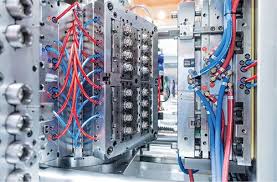
Types of Cooling Connectors for Injection Molding
Several types of cooling connectors are used in injection molding, each serving specific purposes and offering unique advantages. Let’s explore the most common types –
- Pin Cooling Connectors: Pin cooling connectors are cylindrical rods or pins that are integrated into the mold design. They help evenly distribute the cooling channels throughout the mold, providing consistent cooling throughout all areas of the plastic part. The design of pin cooling connectors can vary with straight, helical, or spiral configurations, depending on the specific cooling requirements of the part being molded.
- Pin cooling connectors are particularly effective in applications where uniform cooling is critical, as they help avoid temperature variations that can result in uneven shrinkage and warpage.
- Baffle Cooling Connectors: Baffle cooling connectors are used to divide cooling channels into separate sections, optimizing cooling efficiency and controlling temperature variation within the mold cavity. These connectors use baffle plates or inserts that redirect the flow of the cooling media, ensuring that each section of the mold receives adequate cooling.
- Baffle cooling connectors are valuable for parts with varying wall thickness or complex geometry, as they help maintain consistent cooling and prevent defects caused by uneven cooling rates.

- Spiral Cooling Connectors: Spiral cooling connectors have a spiral-shaped design, which allows for an extended cooling path within the mold. This design increases cooling time, increases part quality, and reduces the risk of defects. Spiral cooling connectors are particularly beneficial for large or thick-walled parts that require extended cooling times to achieve optimum solidification.
- The spiral design creates a longer cooling path, allowing the cooling media to remove more heat from the plastic, resulting in shorter cycle times and improved part quality.
- To know about how to clean the chock cooling channel of mold we use a descaling machine… read more
Applications of Cooling Connectors in Injection Molding
Cooling connectors have a wide range of uses across a wide range of industries, providing vital solutions for a variety of injection molding applications. Some of the major applications include –
- Automotive Industry: In the automotive sector, cooling connectors are critical to the production of high-quality plastic components used in a variety of parts such as dashboards, interior trims, and engine components. The automotive industry demands precision and consistency in the production of plastic parts, and cooling connectors play an important role in achieving these standards.
- Consumer Electronics: Cooling connectors are widely used in the production of plastic components for consumer electronics, including smartphones, laptops, and home appliances. Electronic components require precision molding and excellent surface finish, and cooling connectors ensure that these parts are free of defects that could affect their performance and aesthetics.
- Medical Devices: Injection molding plays an important role in the manufacturing of medical devices, from syringe components to complex medical devices. Cooling connectors are indispensable for ensuring accurate dimensions and maintaining the desired properties of medical-grade plastics, ensuring the safety and efficacy of medical equipment.
- Packaging Industry: Cooling connectors are instrumental in the production of plastic packaging components such as bottles, containers, and lids. The packaging industry demands rapid production cycles and consistent part quality, making efficient cooling an important factor in meeting these requirements.
Benefits of Cooling Connectors in Injection Molding
Cooling connectors provide a number of benefits that have a significant impact on the efficiency and quality of the injection molding process. Some of the key benefits include –
- Improved Cycle Times: Efficient cooling connectors enable rapid and uniform cooling of the molten plastic, resulting in shorter cycle times and increased production efficiencies. Faster cycle times translate into higher production outputs, enabling cooling connectors to achieve cost-effective manufacturing.
- Enhanced Part Quality: Optimum heat management with cooling connectors minimizes warpage, sink marks, and other defects, resulting in improved part quality and stability. High-quality parts contribute to overall product reliability and customer satisfaction.
- Cost Savings: Reduced cycle times and increased part quality translate into cost savings for manufacturers, as they can produce more high-quality parts in less time. This efficiency also reduces material waste and energy consumption, further contributing to cost-effectiveness.
- Extended Mold Lifespan: Effective cooling connectors help maintain a constant temperature in the mold, reducing thermal stress and increasing the lifetime of the injection mold. Longer mold lifetime means fewer mold replacements, resulting in cost savings and uninterrupted production schedules.
- Design Flexibility: A variety of cooling connectors provide design flexibility, allowing mold designers to customize the cooling system to suit specific part geometry and cooling requirements. This flexibility enhances mold performance and ensures excellent part quality.
- Environmental Impact: The use of cooling connectors in injection molding contributes to sustainable practices by reducing energy consumption and reducing material waste. The more efficient cooling process results in a reduced carbon footprint in line with environmental goals and regulations.
Pros of Cooling Connector for Injection Mold
Pros
- Improved Part Quality: Cooling connectors facilitate uniform cooling of the molten plastic, thereby reducing distortion, shrinkage, and surface defects in molded parts. This results in high-quality finished products with improved dimensional accuracy and surface finish.
- Faster Cycle Times: Effective cooling through the connectors allows the plastic to solidify faster, reducing the overall cycle time for each injection molding process. Shorter cycle times lead to higher production rates and increased cost-effectiveness.
- Energy Efficiency: By efficiently dissipating heat from the mold, cooling connectors help reduce energy consumption during the injection molding process. This can result in significant cost savings, especially in high-volume production scenarios.
- Extended Mold Lifespan: Proper temperature regulation with cooling connectors minimizes thermal stress on the mold, increasing its operational lifetime. A well-maintained mold can endure production for a long time, reducing the need for frequent mold changes and the associated costs.
- Design Flexibility: Cooling connectors can be customized and strategically positioned within the mold to accommodate the specific cooling requirements of different part geometries. This design flexibility allows manufacturers to adapt the cooling process to different types of plastic components.
- Process Optimization: Some cooling connectors may include temperature sensors or monitoring capabilities, providing real-time data on the temperature of the mold. This information enables operators to make data-driven adjustments and optimize the cooling process for improved efficiency and part quality.
Cons
- Complex Mold Design: Integrating cooling connectors into the mold design adds complexity to the manufacturing process. Careful consideration and expertise are required to ensure that the cooling channels do not interfere with the structural integrity of the mold or final part.
- Increased Manufacturing Costs: Incorporating the cooling connector into the mold design increases the overall manufacturing cost. Initial expense can be high due to the complexity of machining the cooling channels and the need for high-quality materials to withstand the effects of the cooling medium.
- Maintenance Challenges: Cooling connectors require regular maintenance to prevent clogging, scaling, or leakage problems. Neglecting maintenance can result in reduced cooling efficiency, compromised part quality, and potentially costly downtime for mold cleaning and repair.
- Limited Material Compatibility: Some high-temperature plastics or specialty materials may not be compatible with water-based cooling systems due to their chemical properties or potential reaction with the cooling medium. In such cases, alternative cooling methods may be necessary.
- Water Contamination: In water-based cooling systems, there is a risk of water contamination, especially if proper water treatment measures are not taken. Contaminated cooling water can have a negative effect on part quality and increase maintenance requirements.
- Uneven Cooling Potential: Despite careful design, cooling connectors cannot always provide perfectly uniform cooling throughout the mold, especially for complex part geometries. Variations in cooling may result in slight variations in part quality and dimensions.
Here I am trying to answer some basic questions asked about cooling connectors –
What is the use of a cooling connector?
A cooling connector is used in plastic injection molds to regulate the temperature by circulating a cooling medium, such as water or oil, through strategically placed channels. This ensures uniform cooling, faster cycle times, and improved part quality in the injection molding process.
How to remove broken/damaged cooling connectors from mold?
Removing a broken cooling connector from a mold requires careful and precise steps to avoid causing further damage to the mold. You can easily remove broken/damaged connectors by following the steps mentioned below –
1. Assess the Damage: Examine the broken cooling connector and surrounding area to understand the extent of the damage. Identify any potential risks or challenges before proceeding with the removal.
2. Power Off the Injection Molding Machine: Before attempting any repairs, ensure that the injection molding machine is powered off and disconnected from the power source to guarantee safety during the process.
3. Drain Cooling System: If the cooling system is still filled with water or oil, drain it completely to prevent spillage and potential contamination.
4. Remove Adjacent Components: If there are any nearby components or elements obstructing access to the broken cooling connector, remove them carefully to create enough space for the removal process.
5. Loosen Fasteners: If the cooling connector is held in place by fasteners (screws or bolts), use the appropriate tools to carefully loosen and remove them.
6. Heat Treatment (Optional): If the broken cooling connector is stuck or corroded, heat treatment can be applied to expand the metal slightly, making it easier to remove. Use a heat gun or a torch, but be cautious not to overheat or damage surrounding components.
7. Extraction Tools: Specialized extraction tools like screw extractors or pliers designed for removing broken components may be used to carefully extract the broken cooling connector. These tools provide a better grip and reduce the risk of further damage.
8. Apply Lubricant (If Necessary): If the cooling connector seems stuck, applying a suitable lubricant can help ease its removal. Allow the lubricant to penetrate the area before attempting extraction.
9. Gently Extract the Broken Connector: Using the extraction tools, apply gentle and steady pressure to remove the broken cooling connector from the mold. Avoid excessive force, as it could cause additional damage.
10. Inspect and Clean: Once the broken cooling connector is removed, inspect the area for any signs of damage or wear.
11. Replace or Repair: Depending on the condition of the cooling connector and the mold, decide whether to replace the broken connector with a new one or repair it if possible.
12. Reassemble: After replacing or repairing the cooling connector, reassemble all the components and fasteners securely.
13. Test the Cooling System: Before restarting the injection molding process, test the cooling system to ensure proper functioning and no leaks.
What is PU-Connector?
A PU connector refers to a connector made from Polyurethane (PU) material. Polyurethane is a versatile polymer known for its excellent mechanical properties, such as high tensile strength, flexibility, and resistance to abrasion and impact. PU connectors find various applications in industries like manufacturing, automotive, and construction due to their durability and performance characteristics.
In specific contexts, a PU connector may refer to a type of quick-release connector used in fluid systems. These connectors are designed to provide a secure and leak-proof connection between hoses or tubes carrying liquids or gases. PU connectors are commonly used in pneumatic and hydraulic systems, air tools, and other fluid transfer applications.
The key features of PU connectors include:
1. Flexibility: PU material offers flexibility, allowing the connector to withstand bending and twisting without compromising its integrity.
2. High Tensile Strength: PU connectors can handle high pressure and mechanical stress, making them suitable for demanding fluid transfer applications.
3. Leak-Proof Seal: When properly connected, PU connectors create a tight seal, preventing any leakage of fluids or gases.
4. Easy Installation: The quick-release design of PU connectors enables easy and swift assembly and disassembly, saving time and effort during maintenance or system modifications.
5. Resistance to Abrasion and Wear: PU connectors can withstand harsh conditions and resist abrasion, extending their service life.
6. Compatibility: PU connectors come in various sizes and configurations to fit different hose or tube diameters, ensuring compatibility with diverse fluid system setups.
7. Temperature Resistance: Polyurethane can handle a wide range of temperatures, making PU connectors suitable for both low and high-temperature applications.