Compression Molding & its process details shared in this article. Read full article to clear all confusion about compression molding.
Compression Molding Process
Compression molding is a manufacturing process used to shape and produce plastic or composite materials into various products. It is a widely employed technique for creating complex parts with consistent quality and high production volumes.
In compression molding, a precise amount of raw material, typically in the form of granules, pellets, or pre-cut sheets, is placed into a heated mold cavity. The mold consists of two halves, an upper and a lower, which are designed to form the desired shape of the final product.
Once the mold is filled with the material, it is closed under high pressure. The pressure is applied to distribute the material evenly throughout the mold cavity and to force it to conform to the shape of the mold. The combination of heat and pressure causes the material to soften and flow, allowing it to take on the mold’s contours and details.
The mold remains closed for a specific period to allow the material to cure or solidify. The curing time depends on the type of material being used. After the curing process is complete, the mold is opened, and the finished part is ejected. The excess material, known as flash, is usually trimmed off to obtain the final product.
Compression molding offers several advantages. It can be used with a wide range of materials, including thermoplastics, thermosetting plastics, and composites. The process allows for the production of large and intricate parts with high strength and dimensional accuracy.
Types of Compression Mold
Compression mold is a construction of two halves called core & cavity, where the cavity is half clamped with the moving platen of the compression machine & cavity is half clamped with the fixed platen. When these two halves are closed together there is a gap between them which is filled with powder to take a molding shape during the process of heating supply. Compression molds are mainly 3 types –
1. Open Flash Compression Mold
2. Fully Positive Compression Mold
3. Semi Positive Compression Mold
Compression Molding Materials
1. Phenol-formaldehyde
2. Urea-formaldehyde
3. Melamine-formaldehyde
4. Unsaturated Polyester
5. Epoxy Resin
Compression Molding Techniques
Compression molding is a manufacturing technique that involves using heat and pressure to shape raw materials, such as plastics or composites, into a specific form. The process begins by placing the material in a heated mold cavity. The mold is then closed, and pressure is applied to distribute the material evenly and force it to conform to the shape of the mold. The material is allowed to cure or solidify, after which the mold is opened, and the finished product is removed. Compression molding is commonly used for producing complex parts with high strength and dimensional accuracy, especially in high-volume production.
Compression Molding Types
Compression molding is two types and they are discussed below –
Cold Compression Molding
In cold compression molding, the raw material is typically preheated to a temperature slightly above its glass transition temperature, but below its melting point. The heated material is then placed into the mold cavity and compressed under high pressure to shape it into the desired form. This process is commonly used for thermosetting plastics and composites.
Hot Compression Molding
In hot compression molding, the raw material is heated to a temperature above its melting point. The molten material is then placed into the mold cavity and compressed under high pressure. The heat and pressure cause the material to flow and conform to the shape of the mold. Hot compression molding is primarily used for thermoplastic materials.
Compression Molding Machines Top Companies In 2023
There are so many manufacturers of compression molding, out of them some top manufacturers are given below –
1. Huayuan Advanced Materials
2. Tooling Tech Group
3. Janco
4. Penn Compression Moulding
5. Trident Components
6. KT Plastics Incorporated
7. RCO Engineering
8. Tung Yu
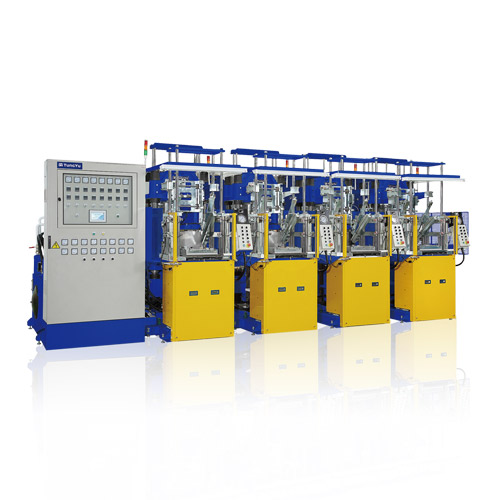
Image Credit : Tung Yu
Compression Molding Applications, Advantages & Disadvantages
Applications of Compression Molding
Compression molding finds applications in various industries due to its ability to produce high-quality, durable parts. Some common applications of compression molding include –
1. Automotive Industry
Compression molding is widely used in the automotive industry to manufacture parts such as bumpers, interior panels, dashboards, door trims, and engine components. The process allows for the production of large and complex parts with excellent dimensional accuracy and surface finish.
2. Electrical Industry
Many electrical components are produced using compression molding, including insulators, connectors, switchgear components, and electrical enclosures. Compression molding provides excellent electrical insulation properties and can incorporate features such as high voltage resistance and flame retardancy.
3. Aerospace Industry
Compression molding is utilized in the aerospace industry for producing lightweight yet strong components. It is used for manufacturing parts such as interior panels, aircraft seats, ducting systems, and structural components.
4. Medical Industry
Compression molding is utilized in the medical field for producing items such as medical device components, laboratory equipment, prosthetics, and orthopedic supports. The process allows for the integration of specialized features and materials, such as biocompatible and sterilizable materials.
Advantages of Compression Molding
Compression molding offers several advantages, making it a popular choice for manufacturing various parts and components. Here are some of the key advantages of compression molding –
1. High Strength and Durability
Compression molding produces parts with excellent strength and durability. The application of high pressure during the molding process ensures that the material is densely packed and reinforced, resulting in robust and long-lasting products.
2. Complex Part Geometry
Compression molding enables the production of parts with intricate designs and complex geometries. The mold can be customized to include intricate details, undercuts, and varying wall thicknesses, allowing for the creation of highly precise and intricate components.
3. Excellent Dimensional Accuracy
Compression molding consistently produces parts with high dimensional accuracy. The pressure applied during the molding process ensures uniform distribution of the material, resulting in precise replication of the mold’s details and tight tolerances.
4. Production Scalability
Compression molding is well-suited for both small-scale and large-scale production. Once the mold is created, it can be used repeatedly to produce identical parts, ensuring consistency and scalability in manufacturing.
Disadvantages of Compression Molding
While compression molding offers numerous advantages, there are also a few limitations and disadvantages to consider. Here are some of the main disadvantages associated with compression molding –
1. Cycle Time
Compression molding generally has longer cycle times compared to other molding processes, such as injection molding. The curing or solidification time required for the material can extend the overall production time, which may impact production efficiency, especially for high-volume manufacturing.
2. Material Waste and Scrap
Compression molding can generate more waste material compared to other molding techniques. The excess material, known as flash, is typically trimmed off after the molding process, leading to additional material waste and potentially higher production costs.
3. Limited Material Flow
The nature of compression molding restricts the flow of material during the molding process. This limitation may make it challenging to achieve uniform material distribution in intricate or detailed parts, potentially resulting in variations in part quality and properties.
4. Limited Design Flexibility
While compression molding can produce parts with complex geometries, it may have limitations in terms of design flexibility compared to other molding processes. The high pressure applied during compression molding can make it challenging to achieve thin walls, sharp corners, or intricate features.
Pros and Cons of Compression Molding
Pros of Compression Molding
- High Strength and Durability: Compression molding produces parts with excellent strength and durability, making them suitable for demanding applications.
- Complex Part Geometry: Compression molding allows for the creation of parts with intricate designs and complex geometries, including undercuts and varying wall thicknesses.
- Material Versatility: Compression molding can be used with a wide range of materials, offering flexibility in selecting materials with specific properties for the intended application.
- Cost-Effective for High-Volume Production: Compression molding is a cost-effective option for high-volume production runs due to its potential for automation, increased productivity, and reduced per-part costs.
- Excellent Dimensional Accuracy: Compression molding consistently produces parts with high dimensional accuracy, ensuring tight tolerances and precise replication of mold details.
- Surface Finish and Appearance: Compression molding can achieve excellent surface finish and appearance on the molded parts, allowing for smooth surfaces or textured finishes.
Cons of Compression Molding
- Longer Cycle Times: Compression molding typically has longer cycle times compared to other molding processes, impacting production efficiency, especially for high-volume manufacturing.
- Limited Material Flow: The restricted material flow in compression molding can make it challenging to achieve uniform material distribution in intricate or detailed parts.
- Material Waste and Scrap: Compression molding can generate more waste material due to excess flash that needs to be trimmed off, leading to additional material waste and potentially higher production costs.
- Mold Design and Tooling Cost: Designing and fabricating molds for compression molding can be complex and costly, especially for parts with complex geometries, requiring durable and precise tooling.
- Limited Design Flexibility: Compression molding may have limitations in design flexibility compared to other molding processes, particularly for achieving thin walls, sharp corners, or intricate features.
- Surface Defects: Compression molding can result in surface defects such as flow lines or trapped air bubbles, necessitating additional post-processing or finishing operations.
- Material Selection: While compression molding can work with a wide range of materials, there may be limitations on the types of materials that can be effectively processed.
Compression Molding Vs Injection Moulding
Compression molding and injection molding are two popular manufacturing processes used for producing plastic and composite parts. Here’s a comparison of the key differences between compression molding and injection molding –
Process
In compression molding, a precise amount of raw material is placed into a heated mold cavity, and the mold is closed under high pressure. The material is then compressed and shaped by heat and pressure.
In injection molding, the raw material, typically in the form of pellets or granules, is melted and injected into a mold cavity under high pressure. The material then cools and solidifies to form the desired shape.
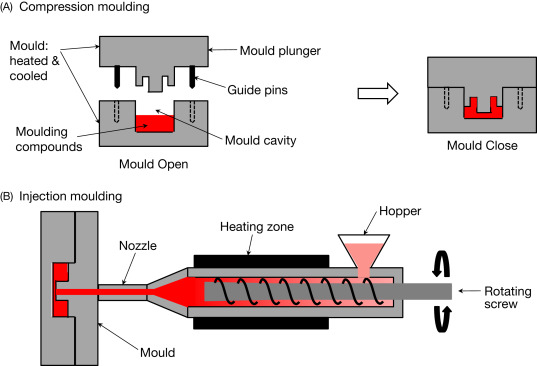
Material Flow:
Compression molding relies on the controlled flow of the material through the mold cavity, often with pre-cut or pre-weighed material forms. The material is forced to flow and fill the mold cavity.
Injection molding relies on the ability of the molten material to flow and fill the mold cavity, driven by the injection pressure and the design of the mold.
Production Volume:
Compression molding is cost-effective for high-volume production runs, as it allows for the production of multiple parts simultaneously in a single mold.
Injection molding is suitable for both low and high production volumes, with efficient automation and fast production rates.
Material Selection:
Compression molding can work with a wide range of materials, including thermoplastics, thermosetting plastics, and composites.
Injection molding works primarily with thermoplastics, although certain thermosetting plastics can also be used with specific considerations.
What are examples of compression molding?
A wide range of products are manufactured from compression molding – –
1. Automotive Parts such as bumpers, interior panels, door trims, instrument panels, and engine components.
2. Electrical Insulation components such as insulators, connectors, switchgear components, and electrical enclosures.
3. Consumer Goods including kitchenware, bathroom fixtures, toys, sporting goods, and electronic device casings.
What materials can be compression molded?
Compression molding is a versatile process that can be used with a wide range of materials. The choice of material depends on the desired properties of the final product and the specific application. Here are some common materials that can be compression molded –
1. Thermosetting Plastics: Phenolic Resins, Epoxy Resins, Melamine Formaldehyde, and Urea Formaldehyde.
2. Thermoplastics: Polypropylene (PP), Polyethylene (PE), PolyVinyl Chloride (PVC), and certain Engineering Plastics.
3. Rubber: Natural Rubber (NR), Synthetic Rubbers like Styrene-Butadiene Rubber (SBR) and Nitrile Rubber (NBR), and Elastomers like Silicone Rubber.
4. Composites: Carbon Fiber Composites, Glass Fiber Composites, and Aramid Fiber Composites.
Why does injection molding have shorter cycle times than compression molding?
Injection Molding has a shorter cycle time due to the following reasons –
1. Rapid Cooling: In injection molding, the molten material is injected into the mold cavity at high pressure and rapidly cools down. The cooling time is shorter because the molten material has a larger surface area exposed to the cooler mold, allowing for quicker solidification.
2. Continuous Material Flow: Injection molding involves the continuous flow of molten material into the mold cavity, which enables faster filling and eliminates the need for additional material compression or performing steps.
3. Efficient Heat Transfer: Injection molding benefits from efficient heat transfer due to the direct contact of the molten material with the mold surfaces. This allows for faster heat extraction from the material, resulting in quicker solidification and shorter cycle times.
4. High Automation: Injection molding processes are highly automated, with advanced.
What are typical mold temperatures for compression molding?
The mold temperature in compression molding varies depending on the specific material being used, the desired properties of the final product, and the process requirements. However, here are some general temperature ranges for common materials used in compression molding –
1. Thermosetting Plastics: Mold temperatures range from 130°C to 180°C (266°F to 356°F).
2. Thermoplastics: Mold temperatures range from 80°C to 160°C (176°F to 320°F).
3. Rubber: Mold temperatures range from 100°C to 200°C (212°F to 392°F).
4. Composites: Mold temperatures range from 150°C to 200°C (302°F to 392°F).