In the dynamic landscape of injection molding, innovation constantly reshapes the way we manufacture intricate parts with precision and efficiency. Among the technological advancements, 3 plate mold systems have emerged as a game-changer, revolutionizing complex part production. This article delves deep into the world of 3-plate molds, unraveling their design intricacies and exploring the manifold benefits they bring to the injection molding process
Understanding 3 Plate Mold Systems
A 3 plate mold, also known as a triple-plate mold, is an advanced injection molding system designed to enable the ejection of a part without the need for complex side actions or undercuts. Unlike traditional 2-plate molds that consist of a core and cavity plate, the 3-plate mold introduces an additional moving plate, known as the stripper plate, which segregates the molded part from the core and cavity components. This separation grants the mold the capacity to release complex parts effortlessly.
Mold Components of 3 Plate Mold
A 3-plate mold is a type of injection molding tool used in the production of plastic parts. It consists of three main plates: the A plate, the B plate, and the C plate. Each plate serves a specific purpose in the injection molding process –

A Plate (Cavity Plate or Stationary Plate)
The A-plate is the stationary component of the mold. It contains the cavities (impression of the part to be molded) and other critical mold components. Here are the key features of the A-plate –
- Cavities and Core Inserts: The A plate cavities create the molded part’s outer shape and surface finish. Core inserts, if needed, develop internal features and shapes. These inserts can be removable for maintenance and repair purposes.
- Sprue Bushing: The sprue bushing is where the molten plastic enters the mold. It connects to the injection molding machine’s nozzle and channels the plastic material into the mold’s runner system.
- Ejector Pins: Ejector pins push the molded part out of the cavity after it has solidified. They are positioned on the A plate and are typically located opposite the gating system (sprue and runner) to avoid part damage.
- Cooling Channels: These channels are integrated into the A plate to circulate cooling water. They help control the temperature of the mold and ensure proper cooling of the plastic material, which affects the part quality and cycle time.
B Plate (Moving Plate or Movable Plate)
The B plate is the moving part of the mold. It contains the mold’s runner system, which distributes the molten plastic to the individual cavities. Key components of the B plate include –
- Runner System: The runner system consists of channels that connect the sprue to the individual cavities. It distributes the plastic material evenly to ensure consistent part quality. The runners solidify along with the part and are typically removed during post-processing.
- Gate Inserts: Gate inserts are used to shape and control the flow of molten plastic from the runner into the cavities. They help prevent part defects such as flow lines and reduce gate marks on the final part.
- Ejector System: The B plate contains the moving half of the ejector system, which includes ejector pins and plates. When the mold opens, the ejector system pushes the solidified part out of the cavities and into the part drop area.
C Plate (Movable Retainer Plate or Ejection Plate)
The C plate acts as a retainer for the ejector system and provides support for the B plate’s ejector components. Its main components include –
- Ejector Retainers: The C plate holds the ejector pins and plates in place. It ensures that the ejector system operates smoothly during the part ejection process.
- Guide Pins and Bushings: Guide pins and bushings are used to align and guide the movement of the B plate as it closes and opens. This alignment is crucial for accurate part production and mold longevity.
- Alignment Features: The C plate often includes alignment features such as dowel pins and holes that ensure precise alignment between the mold halves (A and B plates) when they close.
- Sprue Puller: In some molds, a sprue puller may be present on the C plate. This component helps to detach the solidified sprue from the sprue bushing during mold opening.
Each plate in a 3 plate mold plays a vital role in the injection molding process, contributing to part quality, mold longevity, and efficient production. Proper design, maintenance, and operation of these components are essential for successful injection molding operations.
Design Considerations for 3 Plate Molds

The design of a 3-plate mold requires careful consideration of several factors to ensure optimal functionality –
- Part Complexity: 3-plate molds shine in producing parts with intricate geometries, deep undercuts, or complex shapes that would otherwise pose challenges in a 2-plate mold.
- Stripper Plate Mechanism: The design of the stripper plate and its interaction with the core and cavity plates determine the efficiency of the ejection process.
- Ejection Mechanism: The ejection system, including lifters, pins, and air assistance, needs to be integrated seamlessly into the mold design to facilitate smooth part release.
- Runner System: Proper runner design is crucial to ensure balanced filling and minimal waste material, especially in multi-cavity molds.
- Cooling Channels: Efficient cooling channels should be incorporated to maintain consistent part quality and cycle times.
Advantages of 3 Plate Mold
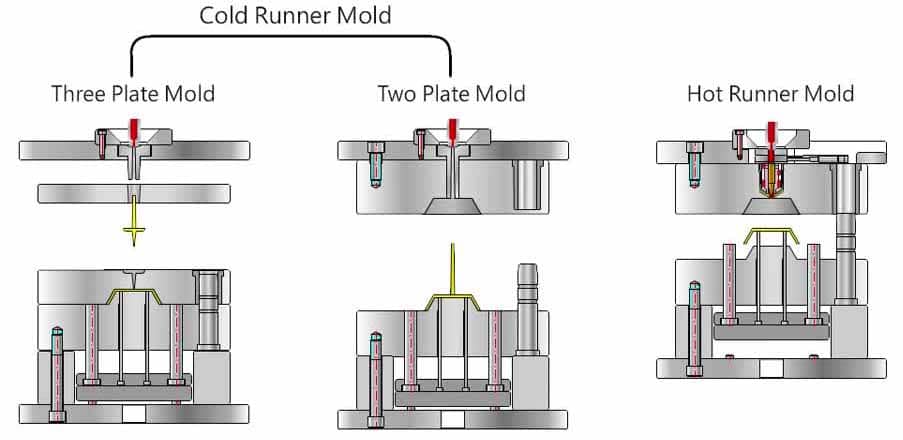
- Complex Part Production: The ability to eject parts with intricate geometries and challenging undercuts simplifies the molding of complex components, expanding design possibilities.
- Reduced Cycle Times: 3-plate molds enable efficient ejection without the need for multiple side actions, leading to shorter cycle times and increased productivity.
- Enhanced Part Quality: Smooth ejection minimizes the risk of part deformation, improving overall part quality and consistency.
- Increased Automation: The streamlined ejection process enhances the feasibility of automation, reducing the need for manual intervention and ensuring consistent production.
- Versatility: 3-plate molds cater to a wide range of industries, including automotive, consumer goods, electronics, and medical devices, providing versatility across sectors.
- Elimination of Secondary Operations: With the ability to release complex parts without additional operations, 3-plate molds reduce the need for post-molding assembly or finishing.
Challenges and Considerations
While 3-plate molds offer numerous advantages, certain challenges must be addressed during their implementation –
- Design Complexity: The design process for 3-plate molds is more intricate than that for traditional molds, requiring careful planning and engineering expertise.
- Tight Tolerances: Precision is paramount in 3-plate molds due to the complexity of part geometries, necessitating accurate mold manufacturing and maintenance.
- Cost Implications: The additional components and complexity in the mold design can result in higher upfront costs, which need to be balanced against the benefits.
Applications Across Industries
3 plate molds find application across diverse industries –
- Automotive: Complex interior components, intricate lighting housings, and precise connectors benefit from the versatility of 3 plate molds.
- Electronics: Miniaturized and intricate electronic parts requiring high precision are produced efficiently with 3 plate molds.
- Medical Devices: The medical sector benefits from the production of intricate medical components that require stringent quality and design standards.
- Consumer Goods: From intricate packaging to innovative product designs, 3 plate molds enhance the aesthetics and functionality of consumer goods.

Pros and Cons of 3 Plate Molds
A 3 plate mold is a specialized injection molding tool with distinct advantages and disadvantages.
Pros
- Efficient Part Ejection: One of the significant benefits of a 3 plate mold is its efficient part ejection process. The presence of a dedicated C plate for ejector components allows for faster and smoother part removal. This reduces the risk of part damage during ejection, improving overall production efficiency.
- Design Flexibility: The three-plate design enhances design flexibility for complex parts. It enables the creation of intricate shapes, undercuts, and features that might be challenging with other mold types. This versatility is crucial for industries where unique and intricate designs are required.
- Reduced Gate Marks: A 3 plate mold often allows for strategically placed gates, minimizing visible gate marks on the final part. This improves the aesthetic quality of the molded components, reducing the need for post-processing or finishing steps.
Cons
- Higher Cost: The complexity of a 3 plate mold’s design results in higher manufacturing and maintenance costs. The additional components and intricate construction require specialized machining and assembly, increasing upfront expenses.
- Setup Time: Achieving precise alignment between the A, B, and C plates is crucial for proper mold operation. This demand for precise alignment can extend the initial setup time, potentially affecting production efficiency, especially for short runs.
- Maintenance Complexity: While the three-plate design provides advantages during ejection, it also introduces additional components that require maintenance. The ejector system, guide pins, and alignment features need regular inspection and servicing to ensure optimal mold performance.
- Limited Part Size: The complexity of the mold’s design can sometimes limit the maximum size of the molded part. Larger parts might require more intricate gating and ejector systems, increasing the risk of potential design constraints.
- Expertise Requirement: Operating and maintaining a 3 plate mold demands a higher level of expertise compared to simpler mold designs. Skilled operators and technicians are necessary to ensure proper alignment, setup, and troubleshooting.
Conclusion
In the evolution of injection molding, 3-plate mold systems stand as a testament to human ingenuity and innovation. By introducing an additional moving plate into the mold design, these systems have opened new avenues for producing complex parts with precision and efficiency. As industries continue to push the boundaries of design complexity, versatility, and automation, the role of 3 plate molds will continue to grow, ushering in a new era of manufacturing excellence.
Through meticulous design, thoughtful implementation, and continuous improvement, 3 plate molds have transformed injection molding, enabling the production of intricate and sophisticated components that were once considered challenging. As technology evolves, these systems will undoubtedly play a pivotal role in shaping the future of manufacturing across various sectors.
FAQ’s
What is the difference between 2 Plate and 3 Plate Mold?
A 2-plate mold and a 3 plate mold are two common types of molds used in injection molding, differing in their design and functionality.
A 2-plate mold consists of two main plates that enclose the mold cavity and core. The mold opens along a single parting line to eject the molded part. Sprue, runners, and gates are part of the stationary half of the mold. While simple, 2-plate molds might require additional ejection mechanisms, potentially affecting part aesthetics.
A 3-plate mold adds an extra plate, the runner plate, between the cavity and core plates. This plate contains the runners and gates, allowing them to be separated from the part during ejection. This design reduces the need for complex ejection systems and gate vestiges on the final part. It’s advantageous for intricate parts and when aesthetics are important, but it can be more complex to design and manufacture.
In summary, a 2-plate mold is simpler but might have ejection challenges, while a 3-plate mold separates runners and gates for improved part quality but is more intricate in design.
What is the mold opening sequence of 3 Plate Mold?
In a 3-plate mold, the mold opening sequence involves the following steps –
Primary Opening: The first step involves separating the cavity plate and the runner plate. This action detaches the runners and gates from the molded parts, preventing gate marks on the parts’ surfaces.
Secondary Opening: After the primary opening, the core plate and cavity plate separate. This allows the molded parts to be ejected from the mold cavities.
Ejection: Once the core plate and cavity plate are fully open, the molded parts are pushed out of the mold cavities by ejector pins or other ejection mechanisms.
The 3-plate mold design facilitates cleaner part ejection and reduces the risk of visible gate marks, contributing to improved part quality and appearance.
Name the 3 main parts of 3 Plate Mold?
1. Stationary or Runner Plate or Clamping Plate.
2. Centre or Floating Plate.
3. Moving or Front Cavity Plate.
Define 3 Plate Mold Design.
A 3-plate mold design is a type of injection molding mold configuration consisting of three main plates: the cavity plate, the core plate, and the runner plate. The runner plate is an additional component placed between the cavity and core plates. It contains the runners and gates that feed molten material into the mold cavity.
The key advantage of a 3-plate mold is that it allows the runners and gates to be completely separated from the molded part during ejection. This results in cleaner part surfaces with minimal gate vestiges or marks, enhancing the part’s aesthetics and quality. Additionally, the 3-plate design can simplify the ejection process, as the runners and gates are not attached to either the part or the core, reducing the need for complex ejection mechanisms.
However, 3-plate molds can be more complex to design, manufacture, and assemble due to the added runner plate. Despite the complexity, the benefits in terms of part appearance and quality often make 3-plate mold designs a preferred choice for parts that require a high-quality finish.
What are the advantages of 3 Plate Mold?
A 3-plate mold offers several advantages in injection molding. Firstly, it allows for the complete separation of runners and gates from the molded parts during ejection. This prevents gate marks on the part’s surface, enhancing its aesthetics and quality. Secondly, the design simplifies the ejection process, as the runners and gates are isolated on the runner plate.
This reduces the need for complex ejection mechanisms, minimizing maintenance and potential defects. Additionally, the 3-plate mold design provides more flexibility in terms of gate placement, allowing for optimal material flow and filling. This flexibility is especially valuable for parts with intricate geometries.
Although 3-plate molds are more complex to design and manufacture, their benefits in terms of improved part appearance, reduced defects, and simplified ejection make them a preferred choice for applications where aesthetics and quality are paramount.
What are the different types of 3 plate molds?
Three-plate molds are a type of injection molding tool that facilitates efficients ejection of molded parts. There are several variations of three-plate molds designed to suit different part geometries, production requirements, and molding processes. Here are some different types of three-plate molds –
Conventional Three-Plate Mold: This is the standard design of a three-plate mold, consisting of three main plates – A, B, and C. The A plate contains the cavities, the B plate houses the runner system, and the C plate holds the ejector components. This design is used for a wide range of part geometries and materials.
Hot Runner Three-Plate Mold: In a hot runner three-plate mold, the B plate incorporates a hot runner system. The hot runner eliminates the need for runners to solidify and be removed, thus reducing material waste and post-processing. This design is commonly used for high-volume production of small to medium-sized parts.
Insert Molding Three-Plate Mold: In an insert molding three-plate mold, the A plate contains not only the cavities but also inserts such as metal components, fasteners, or pre-molded parts. This design is ideal for creating composite parts or for over-molding onto existing components.
Rotary Three-Plate Mold: A rotary three-plate mold is designed for parts that have undercut features. The B and C plates are mounted on a rotary mechanism that allows for the ejection of parts with complex geometries. This design is often used for products like closures, caps, and containers.
Side Gating Three-Plate Mold: In this type of mold, the gates are located on the sides of the part, rather than directly on the parting line. This helps in reducing gate marks and improving the aesthetics of the molded part.
Valve-Gated Three-Plate Mold: Valve gating is used to control the flow of molten plastic into the cavities, resulting in more precise filling and reduced gate marks. This type of mold is suitable for parts with strict cosmetic requirements.
Multi-Cavity Three-Plate Mold: A multi-cavity three-plate mold contains multiple sets of cavities and runner systems on the A and B plates. This design allows for simultaneous molding of multiple parts in each cycle, increasing production efficiency.